Introduction: Truck Bed Lights From LED TV Backlight
I wanted to have lights under my tonneau cover and be able to turn lights on from the bed, without the truck having to be running. I also had a couple broken LED TV's that I took apart and salvaged the backlight LED's and Light Diffuser. I discovered if I split the lights in half they would be able to run on the 12V battery, and if I added a resistor they would also work when the truck was running 13.7-14.7V without burning out.
Supplies
Consumables
- LED Backlights from TV (Strip of 6 makes 2 lights)
- 3D Printing filament (I used Gray PLA+)
- Small Magnets (5x3mm)
- Resistors (22 Ohm)
- Wire (I used 18 and 22 Gauge) (~1 Amp of power draw for 6 lights)
- Zip Ties (for cable management)
- Bus Bar terminals (Optional: if you want to supply power easier for additional projects)
- Electrical insulated terminals (Optional: depending on how you do your connections)
- Solder
- Alligator clips (Optional: If you want quick attach to use under the hood)
- Adhesive (I used Silicone)
Tools
- TinkerCAD and internet connection (Optional: If you want to create a new or modify my models)
- DC Power Supply Variable (Optional but helpful, can use car battery)
- Multimeter (Optional)
- Hammer and Punch
- Soldering Iron
- 3d Printer (I have a Creality CR-6 MAX)
- Dremel
- Scissors (cutting tool for diffuser, a straight edge cutting tool would work better)
Step 1: Test Voltage Needed for Backlights
Verify your TV's backlights run on the same voltage as mine did. Analyze the lights and follow the lines on the board. Mine went from bottom through the LED as drawn in one of the pictures. Grind off the coating from a point that needs a positive Voltage and a point that needs a negative Voltage, to test. Then connect with an appropriate voltage, at the base ~12V of my vehicle they did not burn out. When I had the vehicle running a blue hue appeared in the lights and then one of them burned out quickly after that. To determine the appropriate resistor to use either use the DC Power Supply and increase the Voltage, or use a higher than estimated resistor and step down until appropriate. I used the formula Resistance needed = ((Voltage Future Use - Voltage measured)/Amperage measured). Before I bought the DC power supply I used AA Batteries in series, and I used the multimeter measured voltage of 10.92V and measured amperage of 0.15V with no resistor, wanting to keep the same amperage at estimated max of 15V. (15-10.92)/0.15=27.2 Ohms. I went with the closest resistor I had the 22 Ohms.
The DC power supply I used shows the current draw. The 12.25V image is meant to show battery when car is off, so it draws 0.824A. The 13.91V estimated when the car is running is at 1.182A.
Step 2: Design in TinkerCAD
Either use my models, modify them, create new
- TV LED LIGHT STRIP BASE - https://www.tinkercad.com/things/dv6WA6BwgBs
- Started with a box then added the 7 magnet holes on the bottom, 5x3mm. Then added the channel shown for wires to be hidden and come out of the box 3mm in diameter, and a slot 1mm tall for the diffuser panel just under the top with a taper so it would print better
- TV LED LIGHT STRIP TEMPLATE - https://www.tinkercad.com/things/16qwC8cATto
- Just a quick print to get the correct size of diffuser panel when cutting out
- Toggle-Switch-Black - https://www.tinkercad.com/things/7oJS4tDq32Y
- Just a basic box with magnet holes on the bottom and slots so it clips in place with wire holes at the bottom (I don't know where these came from I just had them around)
- Bus Bar 8 Hole - https://www.tinkercad.com/things/kOHH6C9wEHS
- Used the nominal measurements from the 8 terminal grounding bar and everything fit tight when I pounded it in
Step 3: 3D Print
3d Print your files, I didn't have to do anything special for these as they are pretty simple squares, the TV LED LIGHT STRIP BASE did have a couple lines around the lip that I had to pull off, I tried to make it tapered to get rid of this issue. But it doesn't affect the final product much so I left it as it is
Step 4: Prepare Lights
- Cut in half
- Sand off a negative and positive part of the board, note Positive side with a + (I used a dremel, but a razor blade will work too)
Step 5: Solder Together
Measure out desired length of wire on vehicle. I used extra wire running from the main wire to the lights so I could detach from inside and point outside of the bed. Then solder resistor to wire (I did positive side) and then resistor to board, along with the negative wire. Be sure to have wire through holes in the base and not to touch the print with soldering iron. Optional, have the last one in the line detachable with alligator clips as the ends so it can be detached and used under the hood.
Step 6: Secure With Adhesive
Secure the light strips to the base. I put some silicone on the base of it and moved it around a bit
Step 7: Diffuser Panel Cut Secure and Install
Use template print to cut to size diffuser panel then slide into slot with the rougher side facing inward. Add adhesive to secure.
Step 8: Press Fit Magnets and Bus Bar
Use hammer and punch to pound in magnets. The bus bar I also pounded in.
Step 9: Place on Vehicle
Roughly layout wire assembly on your vehicle to your preference. Then solder the switch together and for the ends going into the bus bar add solder to the ends and secure with the screws.
Step 10: Connect Wiring From Battery
This has worked for me, but might not be the best to do, do at your own risk. I use an empty fuse spot by finding the positive side and then in the empty side put the wire along side of the fuse, I chose 2A.
Step 11: Wait Until Dark and Enjoy
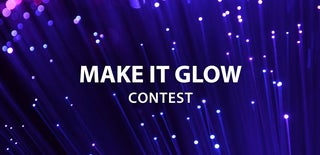
Runner Up in the
Make it Glow Contest