Introduction: Tube Audio Amplifier
I built this "tubes only" amplifier from scratch. It's a quite long project of mine and it required a lot of time and patience to make and in this summary I'll show you how i made it. If you are interested in building one of these than make sure that you take your time and get ready to face a few difficulties.
IMPORTANT! This device has lethal voltages all over inside. If you are unaware of high voltages and electronics, I do NOT recommend this project for you. If you are following along, you do so at your own risk! Definitely do not poke around electron tube devices while they are turned on!
Let's get on with it!
Step 1: The Idea.
I've found some old tubes in a drawer at my grandparents house and I was wondering what I could make out of them. After some thinking I decided to make an amplifier. I also wanted to make it special so i decided to NOT USE ANY semiconductors. I had to do some research to find out how these tube amps work and I'd like to mention here the Aiken Amps website. I've learned lots of things there about this topic.
Step 2: The Schematic & Components
This was probably the hardest part: designing a schematic. First I wrote a list of tubes that I had laying around and then I sat down to draw. What I imagined was a push-pull type stereo amplifier with tone controls, a phono and aux input, and some VU meters. The driver tubes had to be EL84 s and for the other stages i decided to use simple double triodes. I quickly ran out of tubes and had to order new ones. Which means new old stock. If you want to order tubes as well then I recommend Tubes-Store. I got mines from there and I'm very pleased. Then comes the difficult part: the output transformer. It isn't easy to find one for cheap. But after searching a bit I eventually found some on eBay. You may ask why I wrote NASS II-12 on the schematic. Well NASS stands for Not A Single Semiconductor, II means push-pull and it has 12 tubes in total. ;)
Step 3: The First Test
The rat's nest you see above is the assembly of the components in mid-air. I used two regular power transformers in series as an output transformer just to test if everything worked. Everything seemed to be all right so now was the time to find a power transformer. I had an old one laying around so I taught: Why not wind one myself? After disassembling, rewinding and testing it I quickly dropped the idea... I forgot to center tap it, which is essential for the rectifier tube. So I just took one from an old radio, thinking that this will be all right. But it wasn't. But more about that later.
Step 4: The Enclosure
For this I wanted something simple yet good looking. I thought about a brushed aluminium front, top and back plate. The sides would be made from some kind of hardwood. Sadly I had to abandon the aluminium top cover because my resources were limited. The front and back were made from a three layer material (two sheets of aluminium and a plastic one between). I don't know what it's called. For the top cover I still needed a strong and durable material, because it had to stand the heat generated by the tubes and had to hold the weight of the main transformer. So I decided to use textolite. This material has a brownish color and it's relatively strong and easy to work with. Important is to electrically shield the whole enclosure and connect it to ground at only one point to avoid ground loops. I used spray glue and thin aluminium baking sheet in this case.
I first designed the front and back panels in SolidWorks just to see how it was going to turn out. After that I used a drill press and a file to make the necessary holes for the connectors, fuses, switches, potentiometers and VU meters. For the nice surface finish I used a fine grit sandpaper and brushed it in only one direction (from left to right and vice versa) till I achieved the required look. After that I used transfer foil to print the labels and I finished it with a layer of shiny clear coat to prevent the letters from being wiped off with time.
I installed the top panel for a test fit and then I drilled out the necessary holes.
Step 5: The Wiring
After installing a sheet metal reinforcement on the top panel to help it sustain the transformers, I started the wiring. This was probably the most time consuming procedure. I first bolted on the transformers and tube sockets and then soldered the necessary components. The tone control module needed extra shielding because it really wanted to pick up noises from the environment. So I installed it into a metal box.
Step 6: The Final Assembly, Issues & Specs
So I got the whole thing assembled and after a test it turned out that the main power transformer had issues with the very high heater current, thus after around 30 minutes it got to a temperature of over 90 C (194 F). That was way over its optimal operating temperature and even after installing a small fan inside the enclosure, I couldn't keep the temps down. So I had to install another 6.3V transformer inside the enclosure. This solved the high temperature problem.
The other problem was the very high noise level. This is probably due to the ground loops that I accidentally left in the circuit. But with a rebuild this can be solved without too much effort.
In the end, despite of the small imperfections that this amp has, it sounds excellent! And by excellent I mean phenomenal. And definitely looks awesome...
This amp can output 15W RMS per channel without any noticeable distortion. It draws around 10-15W from mains when idling, and around 100W when heaters are on. You should be aware of the fact that the tubes generate a lot of heat, in winter it's great for heating up the room (not so much in summertime). ;)
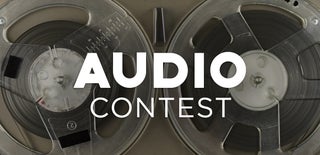
Participated in the
Audio Contest 2018