Introduction: Turned Wood Peppermill
A hand turned Peppermill can be a nice decorative and functional addition to your kitchen. Having a beautiful piece of nature on your table makes for a great conversation piece. The Peppermill project is a relatively easy project that does require some purchased parts to finish. For about $15 to $20 dollars, you can have a functional piece of art that generally costs three times as much at the specialty kitchen stores.
Peppermills can be made in a variety of shapes and sizes depending upon your tastes. The internal parts are sold in sizes ranging from about 4” to 18”. So, the size will be limited to your lathe requirements and your blank selection. Wood choice is key since there are a few factors that should be considered. First, the peppercorns will be in contact with the wood, so you don’t want an “oily” species. Second, we will be drilling out the bulk of the interior of the peppermill body. This requires a heavy load on the lathe and extremely dense woods are a challenge in this respect. Otherwise, choose an appealing variety of wood or create some eye candy with a mixture of wood that are glued together in a laminated blank.
Step 1: Project Materials:
The peppermill will require a kit for the grinding process. The inserts are sold at a number of online and local woodworking shops.
Tools:
Roughing Gouge
Spindle gouge
Skew
Parting Tool
Wood blank (3”x [1 ½” longer than the kit; for a 10” kit, we want a 11 ½” blank])
Forstner bits (1 5/8”, 1 1/16”)
9/3” Drill bit
Jacobs Chuck (holds the drill bits)
Four Jaw chuck
Step 2: Safety
Step 3: Project Setup
Mount the blank for spindle turning by removing any chucks and faceplates. Mark the center on both ends of the blank. Make an indentation at these center marks using a punch. Using the spindle roughing gouge, turn away the edges to make the blank a uniform diameter.
At this point, we will need to decide how to layout the design of the peppermill for maximum visual effect. The mill will be divided in a 70% / 30% manner, where the body will be ~70% of the blank and the head will be ~30%. If you want a particular feature (curl, bark inclusion, eyes, etc.) at one end or another, orient the placement accordingly.
Step 4: Turn the Peppermill
Using the parting tool, we will part the blank in a number
of places. First, part the first ¼” on either end of the blank to create tenons for chucking the blank. Second, create a part that starts at ~3 ¼” from the chosen head of the mill blank. This part will need to be 1 1/16” in diameter and ½” long. Directly below this part, create a 1/8” wide part that will be used to separate the head from the bottom. Carefully part the blank at this point. Make sure to support the blank as the part separates. One way to make the part is to cut it almost all the way through with the lathe. Stop the lathe and finish the cut with a small saw.
Drill the Top
Remove the blank and the centers from the lathe. Install the four jaw chuck and the Jacobs Chuck in the tail stock. Mount the head using the 1/4” tenon created in the previous step. Clean up the ends of the spigot and the bottom edge of the head. Now, install the 9/32” drill bit in the Jacobs Chuck and drill a hole through the center of the head. Careful to stop drilling as soon as the hole is through the center. For all drilling operations, reduce the lathe speed below 300 rpms.
Drill the Body
Remove the head and replace with the body with the bottom end exposed to the tail stock. Clean up the exposed end of the blank while removing a minimal amount of stock. Mount the 1-5/8” Forstner bit in the Jacobs Chuck and drill to ½” depth.
Now, replace that bit with the 1-1/16” Forstner and begin drilling through the blank. This drilling operation should be conducted very methodically and slowly. Drill 1”, then retract the drill bit and clean out the shavings. Repeat this operation until the hole is roughly half way through the blank.
Remove the body and turn it around to mount from the other tenon. Continue the drilling operation until you drill through the center. Turn off the tenon from the end. Remove the body in preparation for the next operation.
Shaping the Peppermill
Replace the body with the rear tenon in the chuck. Insert the head spigot into the body and close the tail stock with the bull nose center in the drilled hole. Shape the peppermill as you like. Be sure to remember, the wall thickness as you create your shape. As you shape the mill’s head, remove the tenon as much as possible. When you have the shape you desire, remove the mill. Re-chuck the body by opening the chuck jaws inside the body. Turn away the exposed tenon.
Create a waste block that will accept the mill head spigot. The waste block will have a hole that is tight enough to accept the spigot without turning and yet loose enough to press the spigot into the block. Mount the head and turn the exposed end to its final shape and length.
Step 5: Finish the Peppermill
Sand the blank thoroughly to 600 grit. Take care to sand with the grain to ensure that no sanding marks will show through the finish. Apply finish as desired. The finish should be a able to stand up to frequent handling. Once the finish has been applied to your liking, you can use a small amount of beeswax on the spigot the insure smooth operation.
You are now ready to assemble the peppermill using the kit instructions. Follow the instructions closely as the spring can be incorrectly installed and will limit the function of the mill.
Fill with your favorite peppercorns and enjoy your new Peppermill!
Sources:
The sources named here are available in any internet search for woodturning supplies and are not provided as recommendations.
Craft Supplies: http://www.woodturnerscatalog.com/
Chef Specialties: https://www.chefspecialties.com/catalog/index.php/...
I made it at TechShop on the Powermatic 4424 Lathe
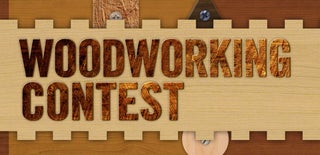
Participated in the
Woodworking Contest