Introduction: Two Stools
These are two stools that I made inspired by nature such as roots, branches , a trunk, and treetop, one with and the other without automated workshop machines and fine finishing such as sanding and glueing.
Hexagon stool (left) was made of birch plywood (6mm), sushi roller stool(right) of willow branches and skin.
Step 1: Design Plan and Prototype (Hexagonal Stool)
I wanted to make a transformable furniture so that I came up with an idea of making a rollable stool with a hexagonal cross section reminding of annual rings of tree.
First of all, I made a prototype with cardboard but it turned out possibly too heavy with real wood because of double layers so that I gave up the transformable part.
Step 2: Design With Rhino
Design the top of the stool with Rhino. There are three different sizes of board that are needed as can be seen in the file. The height of the stool is 45 cm.
Step 3: Arranging & Cutting
Arrange pieces to fit the board of which size is 1220*2440, trying not to waste the wood.
(Arrange the shorter side along the direction of grain! otherwise, the edge gets weak!)
To cut the boards, you need three shop machines as follows:
- Table saw: cut every piece that has the same length!!
- Milling machine: make 60 degree angle at one longer side of each piece. (There must be about 1mm straight part to make it less sharp at the edge, otherwise it could break easily)
- Pin router: make grooves with an appropriate drill bit. This is for the joints where boards meet.
Step 4: Glueing
- Make a zig with the exact 120 degrees and clamp it with pieces. (Put masking tape inside for each piece not to be glued on the zig!)
- Continue glueing one after another, always referring to the original blueprint. (It'd be good if you work on top of the blueprint. Because in this design, there are many parts interconnected to each other so that a small error could cause a bigger problem later! The glue goes to the groove and it takes about 15~20 mins to dry.)
- When you put the final layer, there are two ways to do this: to glue them by binding all the pieces together with masking tape first and glueing later at one time, or to glue them one by one. I did it with the second method, trying to fit it to the blueprint because it takes time to glue all 6 grooves at a time, while glue might dry. But if you have helping hands, try the first method.
Step 5: Finishing
Finish it with a sanding machine. Take care not to break edges when you sand the top surface.
You can see some gaps at joints, it might due to the the way I glued the final layer. But it's in no way ugly and turned out to be sturdy enough.
However, plywood is the material that is bent quite easily so that from time to time precise measurement is difficult to get. Try another way and share your tip with me!
I'll soon update the remaining part of making the Sushi roller stool.
You can also find the description of the project here.
Step 6: Ideation for the Second Stool
The second stool is based on the same idea, but this time without fine sanding and automated workshop machines. I wanted to make it nicely paired with the first stool showing a cross section reminding of year rings of tree. Still, sticking to the 'rollable' characteristic, my idea was to weave branches and roll these up to make a stool.
Step 7: Getting Material (willow) and Cutting
- Gathering material: I had to gather material for myself (That was a rule for this workshop). What I found appropriate for my stool were hazelnut and willow. Both of them are thin, quite flexible, easy to handle, and have nice skin. While willow is thinner and more flexible, hazelnut is firmer and better for bending. I went for willow cause there are bunch of well-dried willows in the workshop master's warehouse though we already had cut bunch of fresh willows.
- Cutting: Because I couldn't use an automated machine, I cut branches with an ad hoc table the master made for me. It was really nice table with a zig on it so that I could cut many branches with the same length. Hand sawing was not that difficult as I imagined once I had got the hang of it.
Step 8: Weaving and Making Prototype
- Weaving: is in order to make the stool more stable and for each stick not to be pulled out. But to make it look nicer, I didn't weave the outer layer. For weaving, we made once again an ad hoc weaving loom with nylon string. It is made by hammering normal nails on one side and hooked nails on the other side with heavy weight hung at the end of strings. I used 3 double lines of strings.
- Binding: I tried binding to see if it's stable enough and to check out the cross section.
Step 9: Peeling Willow Skin and Binding
There was still a problem with stability so that we first clamped them around with a ring clamp and bound them with willow skin.
- Peeling: To do that I peeled the willow skin as wide as possible by scoring a straight line all through a fresh willow branch and opening it carefully little by little. (Old willow cannot be peeled off to make a long string! and the peeled skin should be stored in a vinyl bag not to dry)
- Binding: I made a tight knot with the sailor’s way though I'm not sure which type it was. It is [1] to put an additional slippery string folded in half, [2] to wrap branches around tightly with some extra length set perpendicular to the direction of wrapping (but I couldn't make it perpendicular because the willow skin was too wide to do that), [3] and finally to pull the additional string to the other side to make a knot . It turned out to be quite tight to make the stool stable enough without glueing!
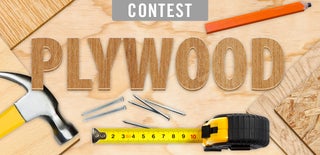
Participated in the
Plywood Contest