Introduction: Two-Tier Custom Cherry Side Table
I needed a side table to fit between two mid-century designed chairs. After waiting over 12 weeks for the chairs to be delivered, I decided to build the table myself.
Step 1: Design
First, I measured the space where the table was needed, then I made several thumbnail sketches exploring different ideas. I chose a rounded, right-angled triangle as the key shape in my design. I constructed the shape in Adobe Illustrator, a vector graphics program that allows you to scale your design anyway you like. Then, I duplicated the shape, shrunk it down, and flipped it over to make the second tier of the table. I positioned the second tier to fit along the backside of the table.
Next, I printed the two shapes at 100% by tiling several 8.5" x 11" sheets of paper, and taping them together with packing tape. The taped printouts served as templates for cutting the wooden table tops. As you'll see in the next step, I also experimented making a template with foam core. Paper works fine, don't bother with foam core.
Step 2: Hairpin Legs
The easiest part of making this table was purchasing the powder-coated, hairpin legs through this vendor via Amazon. It fits the aesthetic I'm looking for, and wasn't that expensive. I ordered three 16" teal-colored legs for around $75.
Step 3: Wood
You simply can't find beautiful wood at your big box hardware store. So, I went to one of the last remaining millworks and lumberyards near me. My chairs were made out of cherry wood, and I wanted the table to match. And, since I don't have the tools or the ability to plane my own lumber, the millworks shop would be able to do it for me. For around $90, they glued-up, and planed a 2'x3'x1" grouping of nice cherry wood planks. Great quality, as well as a time, and energy saver. The size was large enough to give me creative wiggle room when placing my templates, and thick enough to look significant as a small table.
Step 4: Grain
I found the best grain for the surfaces of my table. I decided to have the grain run diagonally across both tiers of the table, so they would complement each other and matchup visually.
Next, I held down my templates and traced the shapes.
Step 5: Shape
I used a jigsaw to cut out my shapes. If you have a bandsaw, it will be more uniform, but I like the imperfect look of a jigsaw. Don't forget to use a scrap piece of wood under the clamp, so you don't indent your table top's surface. Or, you can just clamp it outside of your shapes, like I did.
Step 6: Rasp
Yep, a jigsaw isn't perfect, which is just perfect. I rounded the corners, and smoothed the rough edges with a rasp.
Step 7: Columns
You might be wondering what to use for columns to support the second tier. Well, I realized that my kids haven't played with wooden blocks in years, so, I used three cylinder columns from their set. Not sure what kind of wood it is, maybe oak, definitely a hardwood, but the color matches pretty well. I was happy to repurpose something ready-made. Measuring at 1.25" cir. x 2.625" h, they are uniform, and wide enough and tall enough to work perfectly.
Step 8: Router Time
I clamped both table tops down and rounded all the edges with a router. Don't forget to use a scrap piece of wood under the clamp, so you don't indent your table top's surface. The router has a guide under the blade profile, that rolls against the side of your shape, while it removes the top edge. Remember to wear a mask and eye protection, and work counter-clockwise, against the rotation of tool, to avoid a 'climbing cut' where the rotation of the tool pulls it along.
Step 9: Sand, Mark, & Drill
I sanded all surfaces of both table tops with a disc sander using 150 grit paper.
Next, I placed the second tier on top of the columns and marked their position on the underside of the top tier, as well as the top of the main deck.
After marking their placement, I clamped the columns down, and drilled into the center of both sides, as straight as I could. I used a .25" bit with a drill stop in place to make my holes the right depth, fitting a .25" x 1.13" fluted dowel pin.
Next, I drilled into both decks at the center of each mark, using the same drill setup, so the pins fit evenly and snug on both top and bottom.
I checked the fit, and made a few minor depth adjustments, before gluing the table.
Step 10: Glue & Screw
I glued the table together and used sawdust to rub away any visible wood glue at the seams. I let the table dry overnight, with a stack of books on top.
The next day I attached the hairpin legs with #8 x .75" wood screws.
Originally, I wanted the right angles of the legs to maintain their rectangular visual alignment (see earlier picture of legs on black foam core), however, after screwing it in, I realized it was a little tippy. Clearly, I'm a visual artist and not an engineer. So, I repositioned one leg to be more aligned with the acute angle, which made the table nice and sturdy.
Step 11: Protective Finish
The next step is to protect the wood.
Hand-sand both decks with 220 grit paper, to smooth it out, and get rid of any oils from handling.
I chose not to stain my table, because I like the natural look of cherry wood, and I want it to match my chairs.
For a protective finish, I used this stuff, because it has awesome reviews, doesn't yellow over time, cleans up with soap and water, and doesn't bubble up much when using a sponge brush. I followed the instructions on the can and sanded between coats with 320/400 grit paper and applied three coats over all surfaces of wood. Finally, I let it cure in a temperature controlled room for a week.
Step 12: Viola
This project took me a few weeks and cost a little over $200. Now that the table is finished, these are the best seats in the house.
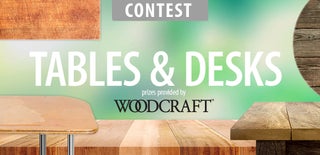
Participated in the
Tables and Desks Contest 2016