Introduction: (UNS)TABLE Wooden Coffee Table
Welcome to my second instructable!
Let's be honest: this table concept is not an original idea, it was inspired by a wonderful table from a famous brand. Yes, wonderful but also very expensive...
That's why we (my father, my brother and I) thought to build it by ourselves. We put a lot of effort in making it and I think it deserves to be shared with you all.
A small but important clarification: despite the name, wich is only a pun, this (UNS)TABLE table is not really unstable but indeed very stable!
Consider that, when we built this object, an instructable was not in my plans so, unfortunately, I have not taken photos of the construction but I will try to replace them worthily with some representative drawings of the various phases.
Consider that this concept could be adaptable to different objects:
- a coffee table
- a dining table
- a counter
- a stool
- ...
It is all up to your imagination!
Step 1: Materials and Tools
Materials:
- Wood panel 3100x1850mm about
- Wood glue
- Wood putty
- Wood screws 35/40mm
- 2mm bicycle spoke (or bar/rod)
Tools:
- A0 Plotter
- Bandsaw or jigsaw
- Hand or circular saw
- Drill
- Electric screwdriver (not essential but a great help)
- Mouse sander (not essential but a great help)
- Sandpaper in varoius grits
- Vernish
- Paint (if you want a painted top surface)
Step 2: Design Your Table
We have to design our object.
The fun part of this project is that it is meant to be a very sinous element with some curves recalling, in my opinion, the contour maps. No schemes, no geometric shapes..so you can give vent to your creativity!
- Choose the broad measures of your tabletop
- Conceive more or less the shape of the tabletop in a plan view
- Design the lower layers shrinking and slightly translating the prevoius one as you go dow
- Choose the height of the table and the number of layers you want in order to determine the thickness of the single layer
Keep in mind that, to avoid stability problems:
- The base (the lower layer) should not be too small.
- The vertical projection of the center of gravity of the whole object should fall more or less in the center of the base.
Ok, now you have got all the essential elements for your project. Usually, I sketch it on paper at first and produce a CAD model then.
We decided for a 375mm table height, divided in n°15-25mm layers. Broad measures of about 970x560mm for the top and 300x270mm for the base.
You will find attached my CAD files in .dwg format (2D) and .3dm/.obj format (3D)
Step 3: Choose Wood Type and Species
Although I present this step as a follow-up, it should actually go hand in hand with the first one.
You should choose the wood paying attention to:
- The look you want to give to your object
- The size and thickness of the panels you can find
- The ease of carving
At first, we thought that plywood would have been a good choice but the final look would have been too stratified, something like a layer with layers..we didn't like it very much but I think it is a matter of taste.
So, after some research, we decided for a 3100x1850mm beech wood blockboard panel (thickness 25cm, as said before).
Consider that also this type of panel has its faults, such as the slits between a strip and another in the core that will have to be finished later.
Step 4: Print Your Silhouettes
Now, you have to print each layer silhouette in a 1:1 scale, we will use them later to cut our shapes on the panel.
To prepare this drawing, I suggest you to:
- Give a progressive number to each shape
- Mark the projection of center of gravity of the whole object on each silhouette
- Draw, departing from the center, two lines to mark two "sides", e.g. "down" and "left"
These easy operations will help us to recognize and align correctly our layers.
Now we have to arrange our silhouettes in some A0 sheets, print and cut them all.
You will find attached my CAD file in .dwg format (6 A0 format sheets).
Attachments
Step 5: Pre-cut Your Panel
In order to have more manageable surfaces, we will prepare a scheme to cut our panel into smaller rectangles (named with a letter: A,B,C, etc.) that will contain one or more shapes. As always, try to reduce waste material.
Mark the dimentions of each rectangle so that they can be brought back to the panel and cut with your hand/circular/ or whatever-saw.
You will find attached my CAD file in .dwg format.
Attachments
Step 6: Cut Your Shapes
Place each paper silhouette on the respective wood rectangle, mark the center and trace the shape with a pencil.
Cut it following the lines with a bandsaw or a jigsaw (photo above) and drill a 2mm hole in the center. This hole's aim is to help with alignment of the layers in combination with the 2mm bicycle spoke.
After that, place again the paper silhouette on it, align it and mark the two guidelines ("down" and "left") on the sides of the shape.
IMPORTANT: when you drill the center hole on top layer, be careful not to go complitely through it because the upper face of it must be perfect!
Step 7: Finish and Paint/vernish
This step could be done also as the last one but I think it would be far easier to prepare all your layers before assembling them together.
So, fill with a proper putty (should be about the same colour of your wood) the slits on the side of each panel. You can clearly see the slits filled in the photos above (already assembled).
Then, smooth the top and the sides with a mouse sander, sandpaper and a lot of..elbow grease.
Lastly vernish the parts that will be visible in in the finished table:
- The upper face of the top layer
- The sides of all layers
- The area close to the edge in the lower face of each layer (except the bottom one)
The number of coats needed depends on the quality of the wood and many other factors but I suggest at least three, sanding a bit the surface between one coat and another.
If you want, paint the top with the colour you prefer.
Step 8: Assemble the Table
Turn the top layer (n°15) upside down, with the center hole (non-through!) facing up.
Remember that, from now on, your "left" mark will become a "right" mark.
- Put some glue on the wood layer
- Place your 2mm spoke in the center hole
- Position the lower one, upside down again (n° 14, will be "lower" on the finished table) on it sliding its center hole on the guide spoke
- Align it using the guidelines
- With the electric screwdriver, place 3 or 4 screws to tighten the two layers and let the glue work. Pay attention to sink also the head of the screw in wood because we don't want any extra thickness.
You can clearly see the center hole and the screws in the photos above (already assembled).
IMPORTANT: use shorter screws when you assemble layer 15 and 14 because we don't want to pass through and come out from the top layer.
Go on with the remaining layers using this technique.
Note that, during the assembly, considering the height of the sofa to which the table would have been coupled, we decided not to install the lowest level, ie we stopped at number 2.
Step 9: Adjust the Last Details
As the title says, give a last check at the table to see if further refinement is necessary and...you are done!
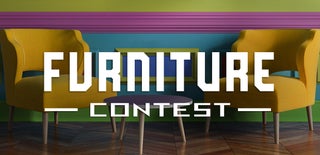
Runner Up in the
Furniture Contest 2018