Introduction: USB-PD Bench Power Supply
Portable and simple USB-PD digital control power supply
Some time ago, I came across a cost-effective DC-DC buck module equipped with digital voltage control (Constant Voltage) and a display. I'm a fan of digital control power supplies as the analog control knobs wear out after prolonged usage.
So thought of creating a compact and portable enclosure for the module, using a USB-PD decoy module. This modification would enable its compatibility with various USB-PD Smartphone and Laptop chargers or power banks.
USB-PD chargers can provide up to 20V, 5A. These voltage and power range could be useful for most of the DIY applications.
While these DC-DC power supply modules may lack precision and accuracy, they prove beneficial handy DIY solution for testing purposes when we are away from the main bench power supply. Additionally, they serve as a portable backup as a secondary power source for devices such as motors, LED strips, buzzers, repair works and more.
Supplies
Bill of Materials (BOM)
- HW-212 DC-DC Buck power supply module - 1 link
- USB-PD decoy module - 1 link
- 3D printed parts
- Acrylic parts
- 30-AWG wires (15 cm) - 3
- 22-AWG wires (15cm) - 2
- M3 Threaded Spacer (M2F) 5mm - 6
- M3x15mm Bolt - 8
- M3x5mm Bolt -2
- M3 Brass Inserts - 8
- M3 Nut - 2
- Banana Socket - 2
- 3mm THT LEDs - Red and Green - 1 each
- 220 ohm THT resistor - 1
- 470 ohm THT resistor - 1
- Aluminum tape - 1
- Banana Jack to Alligator clips - 1 set
3D printed Parts
- Primary body - 1x
- Secondary body - 1x
- Primary plate - 1x
- Secondary plate- 1x
- Holding strip- 1x
- Push Buttons - 4x
Acrylic Parts
- Display Slide
- Main Indicator Slide
- Sub Indicator Slide
Tools
- 3D Printer - FDM
- Screw driver set
- Soldering Iron, flux, solder wire
- Knife
- Wire Stripper
- Tweezers, Pliers
- Sand paper (optional)
Step 1: 3D Printed Parts
- Primary body - 1x
- Secondary body - 1x
- Primary plate - 1x
- Secondary plate- 1x
- Holding strip- 1x
- Push Buttons - 4x
Print settings: 0.2mm, Infill 80%
Print Material: PLA
Print color: White
Post Processing: Grey Paint in sides (Optional)
Step 2: Acrylic Parts
- Main Indicator Slide x1
- Display Slide x1
- Sub Indicator Slide x1
Step 3: Design
Inspiration for this idea was from lots of open source USB-PD based power supply enclosures online thingiverse, special mention to Miniware MDP-XP.
Thanks to all for keeping me inspired
Step 4: Let's Get Started
- Install M3 Brass inserts to the 3D printed parts with soldering iron
Step 5: Prepare - Main Indicator Slide (Acrylic)
- Acrylic part is covered with aluminum tape on both the faces, leaving open the 4 sides
- Aluminum tape helps in better internal reflection of light and distributes light on all open sides aiding better illumination
Step 6: Enclosure Assembly
- Primary body and Secondary body is assembled by sandwiching the Acrylic Main Indicator slide
- Pair of M3 x 15 mm bolt and Nut is used to secure position of the assembly
Step 7: Electronics Preparation
- USB-PD decoy module is configured for 20V USB-PD setting as per the image
- Solder 22AWG wires,
- power IN from USB-PD module
- power OUT to Banana socket crimp circular terminals
- Remove LED from front side of the PCB - OUT using soldering iron
- Red and Green LEDs are connected through series current limiting resistors (refer wiring diagram)
- Three terminals of the Red-Green combination is connected to certain points in the DC-DC Buck module ((refer wiring diagram)
- VCC
- SIG
- GND
- These taps are from output enable feature of the DC-DC buck module
Step 8: Electronics Assembly
- Four 3D printed push button are inserted into the primary body
- Complete wired setup is assembled by first taking the power out ring terminal wires through the cutouts from primary body to the secondary body
- DC-DC module is fastened to the primary body with 5mm-Spacers
- Banana sockets are installed to the secondary body with soldered ring terminal and fastened
- LEDs are placed into the cut out and positioned at middle of the acrylic indicator
- On the other side of the cut out at secondary body - aluminum tape is applied to close and limit light leakage
Step 9: Final Assembly
- Back plates are installed for both primary and secondary body
- Adhesive rubber bumper is applied to the bolt heads (To avoid slippery on the surface of placement)
- On the top side - Acrylic Display slide and Indicator slide is inserted in to the cut outs of the primary body
Step 10: Power Up
- Connect USB-PD power brick to the power supply
- Set the Input voltage and output voltage with push button navigation
- Tune the output current limit potentiometer with screw driver
- Connect the load through banana jack to alligator clips wiring
- Press enable button to power ON the supply
- output power is ON - lights up red
- output power is OFF/IDLE - lights up green
Step 11: P.S
HW 212 module has only constant voltage control digitally but not constant current control. There is a current limit potentiometer on the module but still lacks the constant current control feature which is very useful for many applications
Came across another module with this feature, but both CC & CV is through analog multi turn potentiometers, will try to make a mod with it if possible
Step 12: Update
v2.0
Similar enclosure for DP50V5A
Coming soon...
Wrapping it up!
Hope you enjoyed the project ,
Thank you and happy making! 🚀
Instagram: @ideazero_
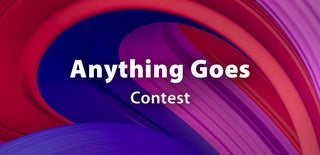
Runner Up in the
Anything Goes Contest