Introduction: Ultimate Animatronic Portal 2 Personality Core: the Design Process
WARNING: this project is NOT for the faint of heart. Depending on your printer size and print quality, you may have to do a lot of model splitting. Scaling these models up or down is not recommended if you plan to put any electronics inside later (i.e. servos, motors, Arduino, battery pack,) unless you want to model spacers for every individual mount. The outer diameter of the shell is 270mm. It's not full scale, but it's pretty large.
A little background info: This project traces its origins all the way back to 2017. I had just saved up enough money for my first 3D printer. At the same time, I had finally beat Portal 2. Of course, my favorite character was the Space Core, so I decided that I would model an entire Personality Core on my own on Tinkercad. It was ambitious, especially for a twelve year old who had never attempted anything close to the complexity and the scale of something like this. When I finished, I thought it looked amazing.
Key words here: I thought.
I rediscovered the project a half year ago, and decided to redesign the whole thing. I decided to once again go with Tinkercad (I had not yet discovered Fusion 360) and began the tedious remodeling. I have to admit, this go around was pretty impressive for a build on Tinkercad, aside from the complete lack of model resolution. I left it sit for a few months, and was about ready to continue it when I ran into the 3D printing contest. I quickly decided to switch the project over to Fusion 360. The only problem?
I only had six days to model the most accurate animatronic Core ever conceived.
Supplies
Here is what you will need for the BARE MINIMUM assembly. Electronics will be covered at a later date.
- Software that allows you to prep the model for whatever printer you plan on using, like Ultimaker Cura.
- A mesh-splitting software, like Meshmixer.
- A 3D printer.
- A lot of filament, possibly upwards of 2 kilograms.
- Some sort of high-grade glue. I will be using contact cement, although it would be possible to use epoxy, or if you're really strained for a budget, superglue.
- M3 screws of varying lengths (or any screw with a 3mm diameter).
- A screw or rod with a diameter of 5.5mm.
- A small amount of EVA foam or some other fabric- this will be used for the handles.
- Patience
Step 1: The Process
First I started by modeling the middle exterior shell, which is what attaches the gyro, the faceplate, the electronics bucket, and everything in between. It is what allows the middle of the Core to move independently of the outer shell.
Then, I modeled the exterior shells. These were simpler than the interior, just cutting up a sphere and adding a few rings where my reference images called for them.
Then I began work on the faceplate. This was also made by cutting up a sphere. All details from the reference images were included, save for the Aperture Science logo which I assumed to be a decal.
After this I created the interior faceplate that would attach the faceplate to the mechanisms which would later be attached to the bucket. This also houses the gyro that will contain the eye. THE EYE WILL BE 65mm IN DIAMETER! I did not model the eye, as I wanted to leave it to interpretation for anyone who wanted to create their own.
Next I made the eyelids. This for me was the most difficult part; I had no idea how I was going to attach them to the servos. In this instructable by RobotsWithRyan, you can see that he uses a gear system not unlike the one I would later use on the exterior shell. I, unfortunately, did not leave room for such a mechanism. Ultimately I resolved to attach them directly to the servos via a small, three-piece mechanism that would rotate and extend as the eyelids would rotate around the center of the Core.
After the eyelids I made the gyro that would mount to the middle exterior shell. It would house the bucket, and swivel around the exterior shell where it was mounted by a ring. This was an annoying process at best.
Next I designed the bucket. There was a lot of detail that went into this process, despite what you might think. In the renders I used much too dark of a material, so the details don't really show up much. The rear of the gyro and bucket are identical to those in the game. The bucket houses the Arduino Uno, the 18650 batteries and their corresponding charger. It may also house a speaker and a sound driver; I have yet to decide, although it is very possible. It will also mount the faceplate mechanism.
Next, I created the fabled faceplate mechanism. This was an intricate process; I had to create six connector pieces that would fit in the indentations on the bucket and interior faceplate. These are made to fit another connector piece that would swivel side to side but would allow the main mechanism to rotate up and down. I saw in RobotsWithRyan's instructable that the model he used was connected with ball joint sockets. I decided not to use this concept, as it was out of my realm of experience to design ball-joint sockets, and with my design the joints were less likely to wear out quickly and pop out. The inspiration for this design was derived from my Traxxas Rustler's suspension system.
The next part of the faceplate mechanism was in fact largely derived from RobotsWithRyan's project, as there is really no other reasonable way to make the mechanism you see in-game. I modeled the hexagonal shape and left a small indentation in the top where the geared section of the secondary piece would fit. I then modeled that secondary piece and the gear that would allow it to slide in and out of the primary piece. I then designed the servo mount.
I then designed the gear ring (which is attached to the exterior shells) that would allow the interior assembly to rotate as it did within the game. Of course, the range of motion is limited due to the geometry of the Core itself, but it's still the closest anyone to my knowledge has gotten. I then designed the corresponding gears, which I designed to fit on a hobby gearbox motor, such as this one. I then designed the mount on the middle exterior shells where these would fit.
Last came the handles. These I designed not entirely game accurately, but here's my reasoning: a, it would have been a lot more difficult for me to add in the sections in the center of the handle due to my lack of experience and b, I wanted to do those pieces with foam anyways. There's not much more to say in terms of the handles; other than that center piece it was a relatively simple process.
Step 2: Files
You can find the files right here. There are 83 parts you will have to print; the STLs are arranged into folders marking how many times they will be printed for your viewing convenience. Reminder that this is pre-mesh slicing, unless your printer is huge you will certainly have more than 83 pieces. A lot of the smaller pieces can be grouped together to save time; for instance, all 12 of the Faceplate Mechanism Connectors could probably get done in one or two prints. I've also included all the renders for reference. When I myself construct this, I'll make a more detailed video and post it on a seperate instructable. That may be awhile, though.
Don't be deceived by the appearance of the faceplate mechanism: each separate branch DOES in fact connect to the corresponding base on the bucket. You may have to look up some reference images of your own. The diameter of the holes designed to connect the Bucket and the Main Gyro at the sides is 5.5mm. Most pieces WILL NEED SANDING! This project will involve a lot of post processing.
Step 3: Conclusion
This project is, as far as I've seen, the most ambitious Personality Core project to date. It took me 24 hours over the course of 4 days to model, render, animate, and make this instructable to print (I found this contest when there were only 6 days left to enter, so I kinda freaked out and may have went a little overboard {you can see the hours in the last photo, I thought it'd be fun to record those}).
Thank you for considering my entry for the 2020 3D printing contest. A lot of detail was lost in the rendering (looking back I probably could have used a lighter color than the black oxide material!) so make sure to look over a few of the models, especially those for the bucket and gyro.
And for those who are thinking to create this monstrosity, godspeed! Make sure to post your makes down below.
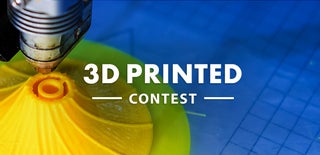
Participated in the
3D Printed Contest