Introduction: Ultimate CNC Router Enclosure
CNC routers are amazing tools with a lot of capability. However, anyone who has had to sit and watch a CNC router do its thing knows how loud and dusty things can get. While a good quality dust shoe can suck up most of the dust, the sound can still be irritating especially if there are multiple people in the workspace. An enclosure can practically eliminate dust in the surrounding area and decrease sound from the CNC router.
The easy lift gas sprung door provides 180 degree access to the interior when open and decreases dust and noise when closed. The best part about this design is that you only need a jigsaw and drill to make the entire thing (a miter saw and table saw will make your life easier though). It can comfortably fit large hobby CNC routers such as the Shapeoko XXL, X-Carve, and Workbee 1010. If you spend a lot of time near your CNC router while it's running, this is the perfect project. Let's get started!
If you would rather follow along with a cad model, you can download a step file from this link: Grabcad Link
Enclosure Dimensions
- Internal Dimensions 46" by 46" by 21" (116cm by 116cm by 54cm)
- Footprint 52" by 49" (132cm by 125cm)
- Door down total height 28" (72cm)
- Door up total height 58" (148cm)
Materials
- x1 4ft x 4ft x ¾” plywood or mdf sheet
- x1 8ft x 4ft x ½” plywood or mdf sheet
- x1 4ft x 2ft x ¼” plywood or mdf sheet
- x2 4ft x 2ft x ⅛” polycarbonate sheet
- x4 2x4 8ft long common board
- x1 1x4 8ft long common board
- x1 1x5 4ft long common board
- x5 1x2 8ft long common board
- x1 Box of 1-¼” long wood screws
- x20 3” long wood screws
- x2 18” long drawer slides
- x1 drawer handle
- x1 42” long 1.5” diameter pvc pipe
- x2 300N/67lb 15” gas spring link
- x1 4ft (48”) continuous hinge
- Paint or wood finish (optional)
- 10ft of door insulation (optional)
- Sound dampening material (optional)
- Led strip (optional)
Tools
- Circular saw (and straight edge)
- Jig saw
- Drill
- 1.5” diameter forstner bit
- Sand paper
- 3d printer (optional)
Step 1: Cut Plywood Sheets Into Pieces
The single 8ft by 4ft by 1/2" sheet will be cut up into parts of the walls and lift door. Check the pictures for dimensions. The 4ft by 4ft by 3/4" sheet must be trimmed down on one side to 47.5" long. The 1/4" thick sheet will serve as the bottom board of the drawer. Tolerances can be fairly lenient, but try to keep it within 1/4".I would recommend making all of these cuts with a circular saw with a straight edge, but a jigsaw can also be used. Note going forward that each image has annotations for extra information.
Step 2: Cut the Polycarbonate Sheets Down to Size
Two polycarbonate sheets are needed for a window on the front and top of the lift door. These can be machined from a single 4ft by 4ft sheet or two 4ft by 2ft sheets. Check the image for cutting dimensions.
Step 3: Cut the Supports to Length
All of the support pieces are cut from 1x2 and 2x4 lumber that you can find at your local hardware store. Just as a refresher 1x2 lumber usually has nominal dimensions of 3/4" by 1.5" and 2x4 lumber has nominal dimensions of 1.5" by 3.5". Four of the pieces require a 60 degree miter cut. If you need more details for the miter cuts, you can find drawings in the images above. Here is the list of lengths that need to be cut:
- x2 1x2 20.5” long with two 60 degree miter cuts (see image)
- x6 1x2 21.25” long
- x2 1x2 43.25” long
- x2 1x2 43.75” long
- x2 1x2 46.5” long
- x2 1x2 47.5” long
- x2 2x4 25” long with 60 degree miter cuts (see image)
- x1 2x4 43” long
- x1 2x4 43.25” long
- x1 2x4 44.75” long
- x3 2x4 45” long
- x1 2x4 46” long
I would recommend writing down the lengths on the wood, so that they are easier to find later.
Step 4: Assemble the Base
This base is designed to resist warping over time with 2x4 and 1x2 supports. Check the images for more information on which length 2x4 goes where.
- First bolt together the 2x4 frame with 3" long wood screws
- If you plan on making this enclosure a stand alone system without a separate table, now is the time to attach legs.
- Attach the 48”x47.5”x¾” plywood sheet to the 2x4 frame with 1.25" long wood screws
- Screw down 1x2 supports onto the plywood sheet from the bottom with 1.25" long wood screws
Step 5: Machine, Assemble, and Attach the Drawer
The sides of the drawer can be made from 1x4 boards trimmed down to 3.25" width for clearance along with a 1x5 board for the front panel. 6 right angle triangle brackets can be cut from 2x4 off cuts. Dimensions for these boards are shown below:
- x2 3.25” by 0.75” by 22” long common board
- x1 3.25” by 0.75” by 40.5” long common board (the length of this board may have to be modified if your drawer slides are anything other than 1/2" thick)
- x1 4.5” by 0.75” by 46.5” long common board
- x6 3.5" leg right angle triangles
You will also need the 40.5" by 21.25" by 1/4" sheet from before.
- Attach the triangle brackets at each corner and on the long side center of the 1/4" thick sheet.
- Screw on the drawer side panels.
- Attach drawer handle with its included screws.
- Install the drawer into the frame built in the previous step with drawer slides. (note that the last image is a bottom view)
Step 6: Attach the Enclosure Walls and Supports
With the base and drawer installed, its time to attach the walls and supports.
- Screw on the two walls to either side of the base. The bottom edge of these walls should be flush with the bottom of the 3/4" thick sheet.
- Add the internal supports onto the side walls.
- Attach the rear upper 45" long 2x4 support and rear wall. Don't forget the 4 3" long wood screws holding the 45" long support.
Now, the main enclosure frame and structure are complete. Next is the lift door assembly.
Step 7: Assemble the Enclosure Lift Door
The lift door can be assembled now and attached to the rest of the enclosure after everything has been painted and finished.
- Start with assembling the door frame.
- Then attach the panels and polycarbonate sheets.
- The door handle is made out of a long pvc pipe held in place with 3 wooden pieces with holes drilled in them.
Step 8: Cut Out Holes for Cables and Vacuum Hose
Holes in the side walls can be made by drilling holes with a forstner bit or hole saw then enlarged with a jigsaw. An optional 3d printed grommet can also clean up the rough woodcut holes.
Step 9: (Optional) Paint And/or Finish All Surfaces
Painting and finishing the bare wood will add protection and bring your cnc router enclosure to the next level. Of course it is also an optional step depending on your preferences.
Step 10: (Optional) Attach Led Strip And/or Sound Dampening Material
Another optional step if you want to increase visibility inside of the enclosure with led strips or decrease sound with sound dampening material. I've found that the sound dampening material doesn't really decrease sound as most of the sound escapes through the polycarbonate sheets, but it does change the cutting sound profile to be less harsh.
Step 11: Attach the Door and Gas Springs
I would recommend attaching the door and gas springs after all paint has dried to avoid getting paint on the gas springs. To attach the lift door, first attach the 48" long continuous hinge to the back of the frame with the included screws. Then make sure to align and center the lift door with the frame. There should be a 1/8" gap between either side of the lift door frame and top enclosure frame when the door is closed. Screw in a couple screws attaching the hinge to the door and do a test open before inserting all of the screws. Adjust if needed to get a smooth open without any rubbing. After the door is securely attached to the hinge, open the door and install the gas spring. You may need to readjust the gas spring mounting positions a couple times to get a weightless feeling on the door. Also make sure that the door in in fact resting on the enclosure frame and not bottoming out the gas springs. Bottoming out the gas springs will decrease its lifespan. After 2 tries, my door was able to stop at any angle between fully closed and open.
Step 12: Modifications and Final Thoughts
The dimensions of this enclosure should be fairly simple to modify if you have a smaller cnc router with less space to work with. Door open and close sensors could also be added for extra safety. There is enough space in the top back corner to mount a small air compressor to further reduce unwanted sound and keep the system together. Another benefit of this design is that if the work piece you are cutting is longer than the cnc router, the door can be slightly opened and the drawer can be used as a support. I've found that the drawer occasionally gets stuck when opening and closing, because it is much wider than it is long. To fix that, I would split the single wide drawer into two drawers with an extra 2x4 beam in the center.
Conclusion
Overall, this is a simple but robust enclosure design that can be built in a single afternoon with minimal tools. Although it's designed to be placed on an existing table or workbench, legs can be easily integrated into the base frame. I hope this Instructable will be helpful to those of you planning on upgrading your hobby cnc router setup.
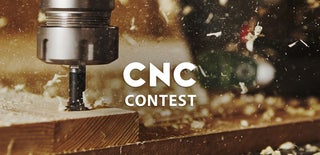
Participated in the
CNC Contest 2020