Introduction: Ultimate TS-100 Travel Case
The most important tool in my workspace would have to be my TS-100 soldering iron. Because of this, I find myself taking it with me everywhere. After a few accidental drops, I decided to print a quick case (0.7 layer height) for it so that I could take my iron in my tool bag knowing it was protected. This was never intended to be a longterm solution however as it wasn't exactly good looking and it wasn't a good example of the work that I do. Originally I was going to make the ever so popular PVC case for my iron but I felt that I could do better. I spent some time designing and came up with this. This case utilizes a carbon fiber rod usually used for large drones as a protective shell for the iron (there's only 0.2mm of clearance for the iron in the tube). For the ends, I figured the best material was 3D-printed wood stained to look like mahogany. I went all out, making sure to felt the inside of the cap and everything. Another feature that I added was a TPU sleeve around the tip of the iron to keep it from rattling inside of my toolbag. This case may be more art than anything else but it certainly does its job well.
Step 1: Gathering the Parts.
I need to start by saying that his project isn't exactly cheap. The largest reason for the cost is that the parts come in larger quantities than you'll ever need. This being said, if you want one of these cases but don't need extra carbon fiber, wood filament, TPU filament, and epoxy laying around you can always purchase a pre-made case from my online store (It's cheaper than building one yourself): https://goo.gl/su8ntD
Parts: (these are not affiliate links)
- $22.98 - 20mm ext, 18mm int carbon fiber tube - https://goo.gl/gw4MCg
- $32.66 - Hatchbox wood filament - https://goo.gl/JfdXAN
- $45.99 - SainSmart TPU filament - https://goo.gl/2m8JGL
- $7.87 - JB Weld clear epoxy - https://goo.gl/DWUVuS
- $9.38 - crafting felt - https://goo.gl/BM9swF
- $4.34 - MinWax Red Mahogany wood stain - https://goo.gl/2L8hmc
- $15.83 - Rust-oleum Ultimate Polyurethane Spray (Gloss) - https://goo.gl/URtSug
- $13.28 - Painter's Tape - https://goo.gl/dweF4H
Total: ~$152.33 (or buy the finished product from me for $20-$35 here)
Tools:
- Dremel or other rotary tool with a cutoff wheel (toothed blades will destroy the fibers).
- Ultra-fine point Sharpie (in the video I used a pencil but off camera, I traced it in Sharpie)
- 3D printer that can print flexibles (for obvious reasons).
- Various grits of sandpaper
- small paintbrush
- scissors (for cutting felt)
- Dust mask, gloves, and safety glasses (not really tools but PPE is important)
Step 2: Cutting the Carbon Fiber.
One of the fastest steps but also the most costly if you have a slipup is cutting the carbon fiber. In order to get a nice fit for your iron, you are going to want to cut your tube to exactly 170mm. This may seem a tad bit long but it will give you just enough room for any of the common heater cartridges (some are a couple of mm longer than others). To prep the carbon for cutting you are going to want to wrap the tube in painter's tape to avoid splitting the fibers apart. The tape also reduces the carbon dust produced from cutting as well as gives you a nice surface to draw your cutting line on.
Once you have the mark at 170mm, it's time to grab your PPE and get ready to do some dremeling. Technically carbon fiber should be cut with a diamond wheel but regular cutoff wheels are cheaper and do just as good of a job.
Some tips for cutting are:
- Take your time and make a nice, straight cut.
- Carbon fibers can irritate your lungs if inhaled so make sure to wear a particulate mask.
- The carbon dust can also irritate your skin so disposable gloves are a good idea if you have some handy.
- Try and stay about 1mm past your line so you can wet sand to the desired 170mm.
After cutting the tube, you are going to want to brush some clear JB Weld on the ends of the carbon tube to protect it and keep any fibers from fraying off. It is important to use the type of epoxy listed on the parts list. This video from a fellow YouTuber explains why: https://goo.gl/8j1wTR Using a Q-Tip or even just a toothpick should be sufficient to get the epoxy on the ends. After the JB Weld cures feel free to do some more light sanding to get it nice and smooth, just don't sand the whole way back to the raw carbon. (I used 600 grit)
Step 3: Make Some Caps!
Now that you have the basis for your case it's time to adorn it with some beautiful wooden accents. I decided to not include the .stl files in this instructable since you are going to want a perfect fit and every printer is different. When designing your caps you can pretty much make them however you want.
Some tips:
- Make the caps look different so you can tell which is the cap and which is the base (the one that will get glued to the carbon).
- The inside diameter of the cap should be exactly 20mm when printed.
- Keep the wall diameter pretty thin so it can flex and hold onto the carbon tube.
- A small chamfer on the inside of the cap can make it easier to put on when closing your case.
After you have the caps printed it's time to sand! Start with some 120-200g sandpaper to knock down any zits or other imperfections. After it is looking good, switch to some 400g to get a satin-feel to your caps. This will help hold the stain. When sanding I stopped before all of the layer lines were gone to give the look of woodgrain when stained.
Step 4: Be Careful With Stain.
This goes without saying but stain will stain just about anything. Afterall it's in the name. With that said, it's time to grab some old newspaper and get to work. Staining 3D printed wood is very different from staining actual wood. This is because while common wood like pine is porous and will soak up and absorb the stain, wood filament has a harder time retaining the color. Because of this when staining your caps you'll want to refrain from wiping off the stain like you usually would and instead leave it to dry for a day or two. When I did this step I brushed the stain on thick and then after a few minutes used the same brush to try and brush off the majority of the stain. This left patches slightly lighter and darker than others which mimics the grain of natural wood. Also, as I stated in the previous step, I didn't sand the part perfectly smooth which ended up leaving tiny super dark lines like what you'd see in mahogany grain.
Step 5: Humans Like Shiny Things.
Polyurethane not only makes your hard work look that much nicer but it also protects your work from meeting an untimely demise. This poly that I used is specifically designed for finishing stained wood. That being said, even though it is designed for use with stain it is assuming that the stain is all soaked in by this point and not slowly drying on the surface. Because of this, it is imperative that you make sure your stain is dry before you use the polyurethane. When I sprayed my caps they were sitting for about two days in a 70F degree room and they still felt a tiny bit waxy. They still came out absolutely beautiful after three coats. When you spray the caps I suggest doing two fairly generous layers, sanding the surface smooth with some 600g sandpaper, and finishing with one more light layer of poly. (with this polyurethane leave 2 hours between coats.)
Step 6: Bringing It All Together.
Now you should have a precision-cut carbon fiber tube as well as some shiny mahogany-looking caps. All that is left is to glue some felt into the top cap, glue the bottom cap to the carbon, and slide a TPU sleeve into the bottom of the tube. This is all pretty much self-explanatory but let's run through it quickly to make sure you have everything.
Cut a 20mm diameter felt circle out of your felt sheet and slide it into the top cap. Use some of your JB Weld to secure it. (I used superglue.)
Print a TPU tube with a printed external diameter of 18mm and an internal of 10mm. This tube should be 50mm long and it wouldn't be a bad idea to chamfer the end. Slide the TPU tube chamfer side first into the bottom of the carbon tube. After you have the TPU tube pressed in flush with the carbon tube, apply some JB Weld around the inside of the bottom plug. Make sure you apply enough glue that both the TPU and carbon are bonded to the wooden plug.
Now go out and share your soldering skills with the world! If you have any questions or comments make sure to leave them below. Thank you for making it to the end of my instructable and I will see you guys next time!
(PS: If you are interested in powering your Iron with a DeWalt drill battery check out my other Instructable here! )
Etsy Store: https://goo.gl/su8ntD
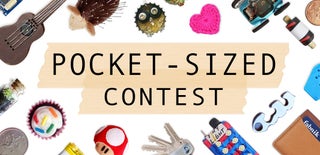
Participated in the
Pocket-Sized Contest