Introduction: Unique Wind Turbine. Very Adaptable Design, Vawt
This is my home made wind turbine. What makes this one special is that the
foils self adjust to maximize power.
It rotates vertically instead of horizontally. (also known as a VAWT) . There are many different designs on the INTERNET where the foils adjust, but this is my own unique design. What makes this design nice is that it is easily scaled up or down in size, and there is no welding required.
Most of the parts can come off with a screw driver so you could really play with the sizes.
Most of the tools used are standard tools.
There are two videos that I have made in association to this instructable, one shows the mechanics of how it works, the other is a short video of the working prototype.
Working prototype: http://youtu.be/9-jXDERwk3U
Mechanics of how it self-adjust: http://youtu.be/X4YFPb60euE
( In this video I used gears instead of pulleys, but the mechanics are the same, and the blades/foils adjust the same)
foils self adjust to maximize power.
It rotates vertically instead of horizontally. (also known as a VAWT) . There are many different designs on the INTERNET where the foils adjust, but this is my own unique design. What makes this design nice is that it is easily scaled up or down in size, and there is no welding required.
Most of the parts can come off with a screw driver so you could really play with the sizes.
Most of the tools used are standard tools.
There are two videos that I have made in association to this instructable, one shows the mechanics of how it works, the other is a short video of the working prototype.
Working prototype: http://youtu.be/9-jXDERwk3U
Mechanics of how it self-adjust: http://youtu.be/X4YFPb60euE
( In this video I used gears instead of pulleys, but the mechanics are the same, and the blades/foils adjust the same)
Step 1: Tools and Materials
Tools:
Metal Grinder ( with cutting blade)
Drill press
Drill bits
Rivet gun
optional Tap die set, ( Screw and bolts will work also)
Materials:
3 timing pulley. I used two 60 tooth pulley and 1 x 30 tooth pulley
2 timing belts ( Pulleys and belts purchased through "spd-si", Sprocket and chain would work as well)
multiple bearings . ( purchased online at "VXB")
Aluminum sheet metal ( any big box store)
Aluminum 1/2" inch tube, and 1 1/4" round tube ( Big box store)
1/4inch and 3/8 inch metal rods ( big box store)
JB weld ( epoxy)
Polymer spacers (easy to drill and cheap, purchased at big box store)
Flat aluminum bar 1/8" thick, 1 1/2 " wide
2 x 1/4 inch polymer thrust bearing
1 x 1/2 inch thrust bearing
Metal Grinder ( with cutting blade)
Drill press
Drill bits
Rivet gun
optional Tap die set, ( Screw and bolts will work also)
Materials:
3 timing pulley. I used two 60 tooth pulley and 1 x 30 tooth pulley
2 timing belts ( Pulleys and belts purchased through "spd-si", Sprocket and chain would work as well)
multiple bearings . ( purchased online at "VXB")
Aluminum sheet metal ( any big box store)
Aluminum 1/2" inch tube, and 1 1/4" round tube ( Big box store)
1/4inch and 3/8 inch metal rods ( big box store)
JB weld ( epoxy)
Polymer spacers (easy to drill and cheap, purchased at big box store)
Flat aluminum bar 1/8" thick, 1 1/2 " wide
2 x 1/4 inch polymer thrust bearing
1 x 1/2 inch thrust bearing
Step 2: Main Support
main support Material:
1 1/2" flat aluminum aprox 12 inch long.
4 bearings, 3/8" inner diameter , 4 mm thick, and 7/8" outer diamter
2 pieces of scrap metal to keep the top and bottom piece separated and aligned ( to keep 1 1/2 " sheet metal seperated). my spacers are 1 inch thick
2 polymer spacers , 1/2' inch inner diameter
Getting started:
I chose a distance of 5 inches from the center hole.
Mark the center and outside holes. ( I like to use a punch or utility knife for my markings on metal)
Drill 1/2 inch center hole
Drill outside holes ( 5 inches from center) , ( outside holes should be size of your outer bearings ( mine were 5/8")
Glue your outer bearing in flat stock metal. ( I used JB weld glue , i should have purchase *flanged bearings instead)
Glue the 1/2 inch spacers to the center hole ( these help keep everything steady)
Glue 1 inch metal spacers between center and outer holes
1 1/2" flat aluminum aprox 12 inch long.
4 bearings, 3/8" inner diameter , 4 mm thick, and 7/8" outer diamter
2 pieces of scrap metal to keep the top and bottom piece separated and aligned ( to keep 1 1/2 " sheet metal seperated). my spacers are 1 inch thick
2 polymer spacers , 1/2' inch inner diameter
Getting started:
I chose a distance of 5 inches from the center hole.
Mark the center and outside holes. ( I like to use a punch or utility knife for my markings on metal)
Drill 1/2 inch center hole
Drill outside holes ( 5 inches from center) , ( outside holes should be size of your outer bearings ( mine were 5/8")
Glue your outer bearing in flat stock metal. ( I used JB weld glue , i should have purchase *flanged bearings instead)
Glue the 1/2 inch spacers to the center hole ( these help keep everything steady)
Glue 1 inch metal spacers between center and outer holes
Step 3:
Center tube:
Center tube is 12 inches long, 1/2 inch outer diameter.
Place 3 bearings on this tube.
1/2 inch Inner diameter bearing at the bottom. ( This one I glued in place)
1/2 inch inner diameter bearing, at the top, Used a white polymer spacer to keep the 2 nd bearing in place on the 1/2 inch tube
At the top of the tube I placed the 1/2 inch inner diameter THRUST bearing. Ensure this bearing has an outer diameter larger then your largest tube. ( in my case the thrust bearing has an outer diameter slightly greater then 1 1/4 inch.) The entire weight of the rotating mass will be supported by the thrust bearing.
Top part:
I used 2 bolts to keep the top parts together
note: My thrust bearing was not sealed, so I wrapped the top support of the thrust bearing with a thin sheet of metal to create a dust shield.
Center tube is 12 inches long, 1/2 inch outer diameter.
Place 3 bearings on this tube.
1/2 inch Inner diameter bearing at the bottom. ( This one I glued in place)
1/2 inch inner diameter bearing, at the top, Used a white polymer spacer to keep the 2 nd bearing in place on the 1/2 inch tube
At the top of the tube I placed the 1/2 inch inner diameter THRUST bearing. Ensure this bearing has an outer diameter larger then your largest tube. ( in my case the thrust bearing has an outer diameter slightly greater then 1 1/4 inch.) The entire weight of the rotating mass will be supported by the thrust bearing.
Top part:
I used 2 bolts to keep the top parts together
note: My thrust bearing was not sealed, so I wrapped the top support of the thrust bearing with a thin sheet of metal to create a dust shield.
Step 4: Stand
My stand is 36 inches high
Main support tube is aluminum, and 1 1/4" outer diameter, inner diameter 1 1/8"
The base I made with a piece of wood with a bore hole 1 1/4".
Then I screwed 3 pieces of metal to create the base
Important:
The wind Vane needs to turn freely.
I placed a skateboard bearing (1/4" inner diameter) inside the 1 1/4" tube, The wind vane is supported by this bearing with the use of the 1/4" rod.
I placed the bearing on a round piece of wood and screwed the piece of wood in place ( see picture)
The base can really be made of anything solid
I used adjustable bolt screws ( or tensioner) so that the center pole can stay level on any type of ground.
Main support tube is aluminum, and 1 1/4" outer diameter, inner diameter 1 1/8"
The base I made with a piece of wood with a bore hole 1 1/4".
Then I screwed 3 pieces of metal to create the base
Important:
The wind Vane needs to turn freely.
I placed a skateboard bearing (1/4" inner diameter) inside the 1 1/4" tube, The wind vane is supported by this bearing with the use of the 1/4" rod.
I placed the bearing on a round piece of wood and screwed the piece of wood in place ( see picture)
The base can really be made of anything solid
I used adjustable bolt screws ( or tensioner) so that the center pole can stay level on any type of ground.
Step 5: Assembly
Assembly of center tube and rod
Vane rod:
inner 1/4" vane rod . ( 1/4 inch round, steel, 28 inches long)
Place polymer spacer on bottom of 1/4" rod, I drilled the spacer and placed a set screw in it.
The spacer will rest on the inner skateboard bearing
Your 1/4 inch rod is complete once you've placed the bottom spacer on it, You can place it inside the 1 1/4" tube and it should be resting on the skateboard bearing that is set in the 1 1/4 tube.
Half inch tube:
On the top part of the 1/2 " tube glue a small 1/4 inch bearing ( Mine is 1/4"x 3/8"x1/8")Take your inner hollow center tube ( Mine 1/2 inch OD, 12 inch long)
Install other bearings:
2 half inch bearing should be installed on shaft, or use a shaft support to keep the bearings in place
Place thrust bearing on top of 1/2 tube.
Your 1/2 inch tube should now have 4 bearings: 2 x 1/2 "bearings, 1 x 1/2" thrust bearing , and a glued 1/4"bearing at the top.
You can now place your 1/2 " tube in the 1 1/4" tube
Vane rod:
inner 1/4" vane rod . ( 1/4 inch round, steel, 28 inches long)
Place polymer spacer on bottom of 1/4" rod, I drilled the spacer and placed a set screw in it.
The spacer will rest on the inner skateboard bearing
Your 1/4 inch rod is complete once you've placed the bottom spacer on it, You can place it inside the 1 1/4" tube and it should be resting on the skateboard bearing that is set in the 1 1/4 tube.
Half inch tube:
On the top part of the 1/2 " tube glue a small 1/4 inch bearing ( Mine is 1/4"x 3/8"x1/8")Take your inner hollow center tube ( Mine 1/2 inch OD, 12 inch long)
Install other bearings:
2 half inch bearing should be installed on shaft, or use a shaft support to keep the bearings in place
Place thrust bearing on top of 1/2 tube.
Your 1/2 inch tube should now have 4 bearings: 2 x 1/2 "bearings, 1 x 1/2" thrust bearing , and a glued 1/4"bearing at the top.
You can now place your 1/2 " tube in the 1 1/4" tube
Step 6: More Assembly
Assembly:
Outer timing Pulley assembly:
Pulley has a 3/8" hole and two set screws
Pulley is set to a 3/8" rod aprox 8 inch long
3/8" rod ( mine is aluminum) needs two holes to screw or bolt foils to. (make sure the two holes are lined up
Foil:
Is made with 1/2" tubing , 10 inch long
and 1/16" aluminum sheet metal.( 4"x10")
Take a grinder or hack saw and cut the 1/2 inch tube in half, for the top 5 inches, now slide the sheet of aluminum in the cut and glue it in place.
Drill a small hole an inch from the bottom of the 1/2 tube ( to enter a screw into the timing pulley assembly)
Pulley assembly with 3/8" rod will fit on metal support
Place thrust washer under Pulley assembly
Connect 10 inch timing belt
Place top metal support
On one side place another timing pulley
Slide small timing pulley on 1/4 inch van rod
Connect 5 inch timing pulley
Aligning foils:
Foils should be perpendicular to each other, Use set screw to adjust
Aligning Wind vane:
Wind vane should slide on to 1/4 inch rod,
Use the set screw or bolt to set the VANE parallel to 1 side ( In the picture the Vane is set Parallel to the foil on the right) in this case the wind turbine will alway turn clockwise
Outer timing Pulley assembly:
Pulley has a 3/8" hole and two set screws
Pulley is set to a 3/8" rod aprox 8 inch long
3/8" rod ( mine is aluminum) needs two holes to screw or bolt foils to. (make sure the two holes are lined up
Foil:
Is made with 1/2" tubing , 10 inch long
and 1/16" aluminum sheet metal.( 4"x10")
Take a grinder or hack saw and cut the 1/2 inch tube in half, for the top 5 inches, now slide the sheet of aluminum in the cut and glue it in place.
Drill a small hole an inch from the bottom of the 1/2 tube ( to enter a screw into the timing pulley assembly)
Pulley assembly with 3/8" rod will fit on metal support
Place thrust washer under Pulley assembly
Connect 10 inch timing belt
Place top metal support
On one side place another timing pulley
Slide small timing pulley on 1/4 inch van rod
Connect 5 inch timing pulley
Aligning foils:
Foils should be perpendicular to each other, Use set screw to adjust
Aligning Wind vane:
Wind vane should slide on to 1/4 inch rod,
Use the set screw or bolt to set the VANE parallel to 1 side ( In the picture the Vane is set Parallel to the foil on the right) in this case the wind turbine will alway turn clockwise
Step 7: Detail View of Wind Vane
Wind Vane Assembly
Main tube:
1/2 inch tube, 15 inches long
Drill small hole in tube to place set screw or bolt
Horizontal rod:
1/4" rod, 20 inches long
2 holes for rivets
Vane:
1/16" aluminium sheet metal, 8 inches square piece that was later cut into a triangle
2 holes for rivets
Assembly:
Drill two holes in your 1/4 tube and in vane."
Rivets VANE and 1/4 tube
On top of the 1/2" tube drill 1/4" hole and insert 1/4 inch rod
I used metal putty to glue 1/4" rod and 1/2" tube in place.
Your wind vane assembly is now ready to slide onto the 1/4 inch center rod.
If you have any questions send me a msg on my youtube account.
Thanks
Main tube:
1/2 inch tube, 15 inches long
Drill small hole in tube to place set screw or bolt
Horizontal rod:
1/4" rod, 20 inches long
2 holes for rivets
Vane:
1/16" aluminium sheet metal, 8 inches square piece that was later cut into a triangle
2 holes for rivets
Assembly:
Drill two holes in your 1/4 tube and in vane."
Rivets VANE and 1/4 tube
On top of the 1/2" tube drill 1/4" hole and insert 1/4 inch rod
I used metal putty to glue 1/4" rod and 1/2" tube in place.
Your wind vane assembly is now ready to slide onto the 1/4 inch center rod.
If you have any questions send me a msg on my youtube account.
Thanks
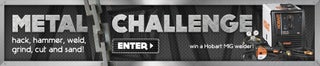
Participated in the
Metal Challenge