Introduction: Velomobile Three Seat Electric Car
Environmentalist? Give this a try!
The problem: Need exercise and local transportation
The first solution: Electric bike kit! (excellent parts from ebikes.ca)
The new problem: It rains here. A lot.
The second solution: A zero emission vehicle with a roof.
The plan is to make a car that is light weight and pedal powered with electric and solar assist.
For now this is a build log and collection of messy notes. I'll add more over the next few days until school starts again. Feel free to subscribe and check back in the spring (of 2013) when I hope to have the front wheels on.
Minirant: I was trying to sell my neighbour on electric bikes and she said "It rains a lot here". Which is true and it got me thinking; is it crazy that in our culture we use two tons of steel as an umbrella and call it normal? A tonbrella as it were. This vehicle is my first attempt at a more practical solution to the rain issue.
The problem: Need exercise and local transportation
The first solution: Electric bike kit! (excellent parts from ebikes.ca)
The new problem: It rains here. A lot.
The second solution: A zero emission vehicle with a roof.
The plan is to make a car that is light weight and pedal powered with electric and solar assist.
For now this is a build log and collection of messy notes. I'll add more over the next few days until school starts again. Feel free to subscribe and check back in the spring (of 2013) when I hope to have the front wheels on.
Minirant: I was trying to sell my neighbour on electric bikes and she said "It rains a lot here". Which is true and it got me thinking; is it crazy that in our culture we use two tons of steel as an umbrella and call it normal? A tonbrella as it were. This vehicle is my first attempt at a more practical solution to the rain issue.
Step 1: Prior Art
At Maker Faire 2012 in Vancouver I saw a couple electric cars. One was a Porsche (converted by my childhood friend it turns out). The other was made of door skin and a lot cheaper to make; plus it can go 60km/h 37mph.
This plywood car was called the Fauchet = faux + Mochet
Georges Mochet made pedal powered micro cars in the 1940~50s.
Mr. 1JohnFoster (from http://endless-sphere.com/forums/viewtopic.php?f=2&t=25315&start=30) made his Fauchet electric car out of 1/8" plywood using a stitch and glue boat building technique. http://fauchet.tripod.com/
Stitch-and-glue seems like a construction method that is quite useful: it requires no specialized tools, no mold (unlike fiberglass), little skill/experience, cheap materials. We'll find out shortly.
(Will add image credits once the notation system is fixed)
This plywood car was called the Fauchet = faux + Mochet
Georges Mochet made pedal powered micro cars in the 1940~50s.
Mr. 1JohnFoster (from http://endless-sphere.com/forums/viewtopic.php?f=2&t=25315&start=30) made his Fauchet electric car out of 1/8" plywood using a stitch and glue boat building technique. http://fauchet.tripod.com/
Stitch-and-glue seems like a construction method that is quite useful: it requires no specialized tools, no mold (unlike fiberglass), little skill/experience, cheap materials. We'll find out shortly.
(Will add image credits once the notation system is fixed)
Step 2: Measure Driver
Custom made for a person like this:
inseam: 70cm = 27 1/2"
thigh ground to crotch barefoot 34 = 13.4"
shin ground to knee bump 43 = 17"
torso sitting ground to shoulder bone 56 = 22"
arm shoulder bone to palm fingers up, palm forward 56 = 22"
hips 41 = 16"
inseam: 70cm = 27 1/2"
thigh ground to crotch barefoot 34 = 13.4"
shin ground to knee bump 43 = 17"
torso sitting ground to shoulder bone 56 = 22"
arm shoulder bone to palm fingers up, palm forward 56 = 22"
hips 41 = 16"
Step 3: Make Seat Mockup With Pedals and Measure It
Seat to floor: 12.25" plus padding
Seat flat length (short so can extend later) 9"
Lumbar angle rise 22.5 run 13.75: arctan (22.5/13.75)= 58.5704deg
Thoracic angle: (from lumbar angle +10.305) = 68.9
Seat / back junction to BB center (critical!) 33 1/8"
BB center to floor: 10 3/4"
Seat junction to thoracic 11.5" along lumbar board (note thoracic board is 1.5" thick)
My leg clearances:
32 from floor knee height max (no clearance)
24 from floor max toe height (heel on pedal)
22 forward from seat junction much less knee clearance needed.
Seat flat length (short so can extend later) 9"
Lumbar angle rise 22.5 run 13.75: arctan (22.5/13.75)= 58.5704deg
Thoracic angle: (from lumbar angle +10.305) = 68.9
Seat / back junction to BB center (critical!) 33 1/8"
BB center to floor: 10 3/4"
Seat junction to thoracic 11.5" along lumbar board (note thoracic board is 1.5" thick)
My leg clearances:
32 from floor knee height max (no clearance)
24 from floor max toe height (heel on pedal)
22 forward from seat junction much less knee clearance needed.
Step 4: Suspension and Steering Research Notes
Research different kinds of front suspension and steering systems.
J-arm seems to be intrinsically anti-roll bar like. Very simple. Maybe affects caster? Used in 1980s Odyssey buggies.
Double wishbone: heavy complex, takes up space, high performance.
Dunebuggy style: long straight lever with shock: very simple! Could be Mcpherson variant?
http://www.tmanskarts.com
http://www.youtube.com/watch?v=1SD3jRdFolI
Macpherson suspension is most common in cars. Few parts, easier to work on, cheaper.
Ackerman steering
caster
camber: negative camber is bottoms out
toe: front wheel drive toe out, rear wheel drive toe in.
body roll: run the shock from the outside of the arm to the CENTER of the car to eliminate body roll (according to SoCal dune buggies).
J-arm seems to be intrinsically anti-roll bar like. Very simple. Maybe affects caster? Used in 1980s Odyssey buggies.
Double wishbone: heavy complex, takes up space, high performance.
Dunebuggy style: long straight lever with shock: very simple! Could be Mcpherson variant?
http://www.tmanskarts.com
http://www.youtube.com/watch?v=1SD3jRdFolI
Macpherson suspension is most common in cars. Few parts, easier to work on, cheaper.
Ackerman steering
caster
camber: negative camber is bottoms out
toe: front wheel drive toe out, rear wheel drive toe in.
body roll: run the shock from the outside of the arm to the CENTER of the car to eliminate body roll (according to SoCal dune buggies).
Step 5: Sketchup CAD
Draw it up and check for places where heels, knees etc. would hit the body. Revise to fit on plywood sheets.
Check for possible center of gravity problems. Put weight well inboard of a line draw between front and rear wheels.
Check for possible center of gravity problems. Put weight well inboard of a line draw between front and rear wheels.
Step 6: Flat Layout
Flattery is a Sketchup program that unwraps curved shapes but it didn't want to work on my ancient laptop so I unwrapped manually.
Step 7: Draw on Wood
After some trial and error I figured out it's best to plot points from a single corner. Eg. 35" down the sheet of plywood and 24 1/3" over from the edge.
I used a tape measure, a long T square and a long L square.
I used a tape measure, a long T square and a long L square.
Step 8: Cut Out Shapes
Jiga jiga jiga.
Funfact: you don't need to drill a hole or start on an edge to start a cut with a jigsaw; just tip the saw way forward and eat into the wood like with a sawzall. This is sort of like a plunge cut.
Funfact: you don't need to drill a hole or start on an edge to start a cut with a jigsaw; just tip the saw way forward and eat into the wood like with a sawzall. This is sort of like a plunge cut.
Step 9: Drill Drill Drill
Drill holes along one edge to prepare for copper wire stitching.
Clamping identical pieces together and drill both at the same time to speed up the work.
The slightly harder part is drilling matching holes on the other piece of the seam.
Clamping identical pieces together and drill both at the same time to speed up the work.
The slightly harder part is drilling matching holes on the other piece of the seam.
Step 10: Wash Hemp
This might be unnecessary.
Most fabric comes new with starch sizing. This might interfere with the glue.
So I washed the canvas with a bit of laundry detergent. I hand washed because the edges were unhemmed.
The trick I learned from hand washing down sleeping bags is repeated rinses. Rinse until you're prepared to drink the rinse water.
Most fabric comes new with starch sizing. This might interfere with the glue.
So I washed the canvas with a bit of laundry detergent. I hand washed because the edges were unhemmed.
The trick I learned from hand washing down sleeping bags is repeated rinses. Rinse until you're prepared to drink the rinse water.
Step 11: Stitch
Snip bits of copper wire and stitch up some seams. I started with the wheel well to make my mistakes since it's fairly hidden.
Step 12: Glue!
Prepare a rounded squeegee. I found a bit of 2" scrap wood, rounded it out and sanded it smooth.
Mix wood glue with thickener until peanut butter texture. I got a garbage bag full of semi-fine sawdust. Proper fine wood dust might have been better; my thickened glue rolled up and stuck to the squeegee a lot. I massaged the glue back down with my finger and it seems OK.
Moosh glue into seams covering the copper stitches. Smooth down with rounded squeegee (may need to give it the finger too).
Mix wood glue with thickener until peanut butter texture. I got a garbage bag full of semi-fine sawdust. Proper fine wood dust might have been better; my thickened glue rolled up and stuck to the squeegee a lot. I massaged the glue back down with my finger and it seems OK.
Moosh glue into seams covering the copper stitches. Smooth down with rounded squeegee (may need to give it the finger too).
Step 13: Trouble With a Thick Floor?
I'm using 1/2" plywood for the floor but it's way thicker than the doorskin I'm using elsewhere. I'm concerned that when I bend the floor and stitch it to the walls, the stitches will tear right out of the walls as the floor tries to spring back straight. Maybe I'll cut an arc in some lumber and screw the floor to that to hold it's shape at least until the seams are stitched, glued and taped...
Step 14: Bending Thick(ish) Plywood
Success! The back was less curved and bent easily with the aid of some curved ribs. The front not so much. I tried screwing some ribs on but they started to punch through the plywood. Blasting the plywood with a heatgun did nothing. Cutting 1/3 into the plywood made it a lot bendier. I did a bunch of cuts 1" and 1/2" apart. I used two main ribs and a few more mini ribs to keep the very end of the plywood flipped up.
Step 15: Stitch and Glue Some More!
Here's where the thing starts to take shape. I tried abandoning the copper wire method and had pretty good success with hemp string. Instead of doing surgery style stitches with individual copper wires I drilled my holes in an alternating pattern and whip stitched the pieces together.
This innovation using string opens up a lot of possibilities with different stitch patterns. It would be possible to lock the panels together in perfect alignment using a stitch where the string passes in between the panels.
To thread the string, I used a needle of sorts made of some thinner steel wire (the wire used to tie rebar together in foundations) bent in half. This pinched onto the string and held it nicely.
This innovation using string opens up a lot of possibilities with different stitch patterns. It would be possible to lock the panels together in perfect alignment using a stitch where the string passes in between the panels.
To thread the string, I used a needle of sorts made of some thinner steel wire (the wire used to tie rebar together in foundations) bent in half. This pinched onto the string and held it nicely.
Step 16: Reshaping the Nose (Rhinoplasty)
Yeah, this is my first nose job. I didn't like the curve of the hood or I cut the sidewalls wrong. But I think I can fix it. I let the hood panel curve naturally and stitched it in place. This left a substantial gap that the fillet glue would have squished out of. So I used a plastic bag as an anti-stick layer and put on temporary panels to block the filler glue from pushing out.
Step 17: Glue AND Tape at the Same Time!
Yes, I'd forgotten some sage advice from Mr. 1JohnFoster: Lay your fiberglass on BEFORE the fillet filler is hardened. This lets you squish out air pockets more easily since they fillet won't have cruddy divots solidified in place yet.
This is especially important since I can't see any air pockets because I'm not using fiberglass tape. I'm using strips of hemp canvas instead. This canvas is not transparent when wet. Also I'm not sure how well it wets out with the goopy glue I'm using so I mooshed lots of glue on both sides.
I used 10 oz hemp canvas.
I cut the canvas into 3 1/2" wide strips.
Hemp sack material might have wetted out better.
This is especially important since I can't see any air pockets because I'm not using fiberglass tape. I'm using strips of hemp canvas instead. This canvas is not transparent when wet. Also I'm not sure how well it wets out with the goopy glue I'm using so I mooshed lots of glue on both sides.
I used 10 oz hemp canvas.
I cut the canvas into 3 1/2" wide strips.
Hemp sack material might have wetted out better.
Step 18: Glue Heater Cocoon
I'm using Tightbond 3. It's cheap, sort of waterproof, easy to work with and stench free, plus it's non-toxic. Way nicer than epoxy.
The only drawback is it needs temperatures above 8 deg. Celsius to cure properly. So I put a heater in the car and covered the whole thing with three layers of plastic. I made sure the plastic would be a safe distance from the heater. This should hopefully ward off any frosty temperatures at the glue cures overnight.
The only drawback is it needs temperatures above 8 deg. Celsius to cure properly. So I put a heater in the car and covered the whole thing with three layers of plastic. I made sure the plastic would be a safe distance from the heater. This should hopefully ward off any frosty temperatures at the glue cures overnight.
Step 19: Wheelwell Redesign
I wanted a stronger wheel well. The one I'd made had all straight pieces so it lacked rigidity and probably couldn't be sat upon. So I've designed one with each piece curved to give it stiffness. The trouble now is that it has so many dimensions, it's bogging me down... first world problems.
Yeah this wheel well's a bit gross. Oh well.
Yeah this wheel well's a bit gross. Oh well.
Step 20: Aligning Pedals?
Aligning pedals is tricky. I've set up two bikes side by side and I'm trying to get the two bottom brackets lined up but it's hard to get everything in position.
Step 21: Pedals Aligned?
I think I've done it.
Step 22: Chop Off the Slack!
Flight of the Conchords had an episode about someone dissing rappers who then cut his whole body off... I did something similar here.
With the bottom brackets as aligned as they're going to get. I locked everything in place and chopped off the rest of the bike frames.
Step 23: Practice Welding
Because I'm not a very good at it yet.
Step 24: Weld on Crossbrace
Now the pedals can go 'round and round.
Step 25: Gear Up
There was a gearing problem. It was too slow so I'm adding yet another stage to the transmission.
And I've busted out an early-release second generation Stokemonkey motor. I should install that before I put the wheel well in...
And I've busted out an early-release second generation Stokemonkey motor. I should install that before I put the wheel well in...
Step 26: Front Wheels and Suspension Materials
24 inch wheels with disk mounts and 20mm axles. Also some tubing for the front suspension arms. Aw yiss.
It was hard to find the parts to make a 20" wheel with a disk mount. I wanted smaller wheels to withstand lateral loads. 1JohnFoster used 26" wheels without incident but I wanted to err on the side of caution. He also kindly gave me some parts including hefty hubs that will probably make their way onto a recumbent trike at some point.
It was hard to find the parts to make a 20" wheel with a disk mount. I wanted smaller wheels to withstand lateral loads. 1JohnFoster used 26" wheels without incident but I wanted to err on the side of caution. He also kindly gave me some parts including hefty hubs that will probably make their way onto a recumbent trike at some point.
Step 27: Front Struts
I'm making these from $#!++y shocks from a mountain bike but they're going to be too wimpy. It would be better to use proper struts or at least motorcycle front shocks.
I had to shim the shocks with a bit of flattened mild steel wire so they'd fit tightly.
There are two sizes of 1/4 inch taps. Use the correct one.
I had to shim the shocks with a bit of flattened mild steel wire so they'd fit tightly.
There are two sizes of 1/4 inch taps. Use the correct one.
Step 28: Disk Brakes
Breaks on a bus, brakes on a car
Breaks to make you a superstar
Cause I'm Kurtis Blow and I want you to know
That these are the breaks...
Breaks to make you a superstar
Cause I'm Kurtis Blow and I want you to know
That these are the breaks...
Step 29: Motor (Start Small)
I'm starting with a ~400 watt motor geared down for cranking up hill. It's cheaper/less risky to start small.
Step 30: Reglue Redo
The rear right side panel somehow beveled itself the wrong way. I was in denial but it had to be reset before I put on the wheelwell and seat. Sooo, chop cut slice, brace, fill glue tape. I put three vertical boards on the inside and screwed them to matching boards on the outside. The outer boards are longer and wedged so as to force the correct bevel shape.
Also the problem probably originated from a slight alignment or tension issue which I think I also corrected by chopping and resetting the upper seam just behind the seat... hopefully.
Success!
Also the problem probably originated from a slight alignment or tension issue which I think I also corrected by chopping and resetting the upper seam just behind the seat... hopefully.
Success!
Step 31: Beef Up Strut Connection Area (and Clamping Using Magnets)
I should have done this before I put the side panels on. It would have been easier to clamp simply by laying them on the floor with weights on top. Oh well, now I'll have to get inventive. My first thought was to make a big clamp to squeeze everything in place but I ended up using psychotically powerful magnets instead.
I got the magnets to make a Hugh Piggott style wind turbine generator but I haven't built that yet...
I got the magnets to make a Hugh Piggott style wind turbine generator but I haven't built that yet...
Step 32: Redo Wheelwell (again)
The back wheel well was beveled in the wrong way on one side. This made it tricky to install without cracking the side panel. Sooo I'll try cutting the seam and redoing it with braces to maintain the correct orientation. The door skin I'm using has a natural curve to it which prefers not to be ignored.
This time I braced it in place for a few days whilst the glue set deep inside the fillet. It worked
Putting the wheel well in also required some butchery.
Success!
This time I braced it in place for a few days whilst the glue set deep inside the fillet. It worked
Putting the wheel well in also required some butchery.
Success!
Step 33: Shock Tower Side Panel Bracket
These are plates where the top of the strut will connect to the body of the car near the lower corners of the windshield. Smooth curves and a tad of flexibility to reduce stress concentration points... That's the theory at least. The jigsaw wouldn't go around the tight inner corners. Also I made one of these mostly with an angle grinder and that was much easier. Then I got hives all over my body. I must be allergic to the paint or something.
Enter the $5 sheet metal from the scrap yard.
I made a little tap jig to hold the tap perpendicular(ish).
Before painting, wash metal with dish soap and water before painting in order to remove oil etc.
Enter the $5 sheet metal from the scrap yard.
I made a little tap jig to hold the tap perpendicular(ish).
Before painting, wash metal with dish soap and water before painting in order to remove oil etc.
Attachments
Step 34: Seat
It might have been easier to put this in before the wheelwell. That way I would have been able to glue in the seat back by reaching through the rear wheel hole from underneath the car. Now I have to cut out the trunk first so I can access behind the seat.
Step 35: Trunk
Now this took some doing. The challenges are:
-Maintain the curved shape of the rear panel after having chopped out the trunk hole. I
-Reinforce the trunk hood and coping.
-Easy placement of stops for the trunk to close against.
-Proper clearance for the bottom to swing inward.
-Comfortable sitting position for passenger in rumble seat.
I think I've done it. I took some measurements (see video) and laminated two oversize pieces on the inside with my fancy magnet clamp method. I also put some screws through the cut line to act as clamps.
I also used the excellent nail-in-a-drill method. I did this to make little guide posts to line up the panels as I glued them in place inside.
It worked out pretty nicely. I cut the trunk hole with a snap blade knife since it's really thin. This gave a pretty clean cut. There were a couple of unglued spots in the upper corners that I'll have to fix somehow.
I beveled the cut on an angle to make a natural stopper.
-Maintain the curved shape of the rear panel after having chopped out the trunk hole. I
-Reinforce the trunk hood and coping.
-Easy placement of stops for the trunk to close against.
-Proper clearance for the bottom to swing inward.
-Comfortable sitting position for passenger in rumble seat.
I think I've done it. I took some measurements (see video) and laminated two oversize pieces on the inside with my fancy magnet clamp method. I also put some screws through the cut line to act as clamps.
I also used the excellent nail-in-a-drill method. I did this to make little guide posts to line up the panels as I glued them in place inside.
It worked out pretty nicely. I cut the trunk hole with a snap blade knife since it's really thin. This gave a pretty clean cut. There were a couple of unglued spots in the upper corners that I'll have to fix somehow.
I beveled the cut on an angle to make a natural stopper.
Step 36: Wishbone Front Bracket
A little trigonometry never hurt anyone. Well sort of... Anyway, I trigonometrified the placement of the front wishbone brackets. The challenge here was to make them pivot on the 11 degree forward rake that I'd designed the struts for. The result was a choice; do I have a thing sticking way down to get smashed when I roll over a protruding rock or do I have a thing that sticks way up and is harder to mount?
I chose to have a bracket that cantilevers up from under the car.
I chose to have a bracket that cantilevers up from under the car.
Step 37: Wishbone Connection Bolt at Bottom of Strut
I needed a 12mm bolt to stick out of the bottom of the strut. It needs to be coaxial with the strut so it will rotate as the wheel steers rather than force the wishbone in weird ways.
I thought of using an aluminum plug to fit up in the bottom of the strut which I could then thread to accept a bolt but I worried that such a bolt might wiggle out since it is rather hidden. Instead I made and attached a U shaped bracket and threaded this so I could screw in a bolt from the inside such that it could never fall out.
I thought of using an aluminum plug to fit up in the bottom of the strut which I could then thread to accept a bolt but I worried that such a bolt might wiggle out since it is rather hidden. Instead I made and attached a U shaped bracket and threaded this so I could screw in a bolt from the inside such that it could never fall out.
Step 38: Front Swing Arm / Wishbone
Here it is. I used bicycle inner tube as a rubber bushing.
And here's a neat way to extrapolate holes from an underlying piece:
And here's a neat way to extrapolate holes from an underlying piece:
Step 39: Door
The door and surrounding frame need reinforcement so I layered up more pieces.
Funfact: materials stressed by flexing have most of their load concentrated on their surfaces. The concave side is under compression and the convex side is under tension. Any discontinuities on the surface can concentrate stress at this discontinuity. For example, this is why takeout sushi soysauce packs have a little nick in the side so you can tear 'em apart easily at this discontinuous place. Also, polishing the surface of a material significantly strengthens it probably due to less microscopic nicks.
In light of the above fact I put a continuous horizontal strip of doorskin on the top and bottom of the door and frame.
Also the driver's side has no door but still needed to be beefed up in case someone silly leaned on the window sill.
I ran out of clamps and magnets so I used this awesome pipe clamp trick from Tim Anderson.
Funfact: materials stressed by flexing have most of their load concentrated on their surfaces. The concave side is under compression and the convex side is under tension. Any discontinuities on the surface can concentrate stress at this discontinuity. For example, this is why takeout sushi soysauce packs have a little nick in the side so you can tear 'em apart easily at this discontinuous place. Also, polishing the surface of a material significantly strengthens it probably due to less microscopic nicks.
In light of the above fact I put a continuous horizontal strip of doorskin on the top and bottom of the door and frame.
Also the driver's side has no door but still needed to be beefed up in case someone silly leaned on the window sill.
I ran out of clamps and magnets so I used this awesome pipe clamp trick from Tim Anderson.
Step 40: Steering (temporary)
A short push-pull cable steering system may work nicely. I got a 10 foot cable since that's all they had in stock. A 7 footer might have been better. Bear in mind this steering system will probably have little or no self centering steering.
Step 41: Test Ride
Step 42: Belt Drive CVT
I've had a lot of trouble with my chain drive falling off; I knew I would but I had to start somewhere right. Enter the belt.
Yes, belt drives have ~95% efficiency according to the internerd. They are also cheap, quiet and tolerate misalignment; ie. they're ideal for someone of my purposes. Also they are handily conducive to a nice continuously variable transmission. I thought I had one from my buddy's dead scooter (that cost a bottle of wine and a few bucks)... a look inside revealed that this was a single speed belt drive. That's fine, I'll just have to get creative.
Listen to me get confused in the video above when I still thought this was CVT and not single speed.
Step 43: Shorten Front Swing Arms, Bigger Shocks
Needed to shorten the swing arms in order to bring the axles 5.5 inches inboard. Pythagorean theorem to the rescue.
Also needed beefier shocks shoehorned in which is kind of an involved process.
Two videos:
http://youtu.be/qHrB2bYJkSw
http://youtu.be/IaqJyWmoY10
Also needed beefier shocks shoehorned in which is kind of an involved process.
Two videos:
http://youtu.be/qHrB2bYJkSw
http://youtu.be/IaqJyWmoY10
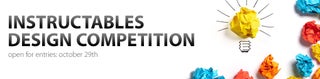
Participated in the
Instructables Design Competition