Introduction: Veneer Repair: Vintage Sewing Table
It's rare to find a vintage sewing table that is complete, unless it's been passed down to a family member that has taken care of it. We always seem to find the metal stands but bases with the original wooden top are harder to come by. I’ll bet that’s because people mistakenly think only the metal is salvageable; a table top with veneer in the condition we found this one usually ends up in the garbage.
Although the sewing machine was long gone, I could only imagine the wondrous things that were stitched together at this very table! Despite the water damage and missing/cracked veneer, it deserves a second chance to have purpose again. I can’t wait to show you in this Instructable that there’s still plenty of life left in this ol’ gal – and the table too!
Step 1: Condition Issues
We found our sewing table at a local thrift shop. You really can’t go wrong for only $14.99, however we had a lot of veneer repair ahead of us and I’ve never personally tackled a project like this. Luckily I have an experienced teacher in Hubs!
The table was missing veneer in some places. The centre of the top had a large split in the veneer that was bubbled (see the close-up in the 3rd picture). There was over water damage, scratches and alligatoring of the finish. On the outside, the finish was practically non existent, but when I opened the lid it revealed a darker stain (4th picture). The last picture shows the extent of the water damage on the drawers. On a positive note, it was structurally sound, all the drawers worked and there was no rust on the base.
With all the condition issues and variety of veneer repair scenarios, it was not the best candidate for stain so we moved forward with the intention of painting it.
Step 2: Use Air Gun to Clean
As I was exploring how everything opens, Hubs was preparing to blow off years of dust with an air gun and compressor.
He worked on the top first, then taped it up so he could turn it upside down without pieces flying open.
Hubs removed the base and blew each piece with the airgun. You could vacuum instead (or in addition to) but the blown air gets into all the nooks and crannies to release years of accumulated dust that a vacuum could never reach. Needless to say, do this outside or in a garage!
Step 3: Disassemble
We carried the legs and table down to my craft studio in the basement as-is so I could methodically take the rest of the table apart and document it with pictures. As you'll see in the next step, pictures are an important part of the process so you now how it goes back together again.
The metal base didn’t stay in my studio for long; once I decided on the paint colour, it was back outside to be painted with a metal paint. We didn’t tape off the Singer name on the base; in the finished product you can still see it, but it’s very subtle. If contrast is important to you and you want the original finish on the name to show through, take the time to tape it off before you paint it! Alternatively, you can always highlight the name in a different colour paint if you want to see it more.
As I was taking the green tape off the table that Hubs used earlier, I noticed that some of the remaining finish came with it. In the third picture, I lifted the finish off with a wider piece of clear packing tape. Although the alligatoring looks bad and the finish is in rough shape, sanding will take care of it.
We disassembled the table into manageable pieces so we could work on repairing each one individually.
Murphy's Law of Furniture Dissassemly
Here is my own personal Murphy’s Law of furniture disassembly: whenever I get down to the last piece, there’s always ONE screw that I absolutely can’t budge on my own. It’s like furniture builders of yore turn that one screw extra tight so they can look down and laugh at me contorting myself to will it out of the hole. Around here, I always have to call Hubs to use this brute strength to remove the last stubborn screw!
Step 4: Document With Pictures
I took a lot of pictures so we could reverse engineer the pieces back together again once it was painted. An iPad is ideal for this step because the pictures are larger than those on a phone or camera and you'll be able to scroll through the pictures in the reverse order when it comes time to reassemble.
When there’s two similar pieces, mark each with a piece of green tape and mark them left (L) and right (R) respectively. The 4th picture shows the drawer surrounds separated from the table and marked accordingly.
Here's a good tip. You'll notice in this step and the next one that we used a variety of different screwdrivers to get everything apart. However, they actually all have something in common: a ratcheting feature and magnetic end. These features are great for preventing wrist fatigue and holding onto the screws so they can't accidentally fall and roll away. Keep this in mind next time you need to buy a screwdriver.
Step 5: Bag It!
As I disassembled the table down to the sum of its parts, I placed all the hardware into ziplock bags so we wouldn’t lose any pieces. It's helpful to label the bags with green tape and a letter or number that matches the hardware to where it came from on the actual table; document it with another picture. Figuring out how to put the table back together is so much easier when you keep it all organized and have pictures to look back on!
Step 6: You Will Need...
- All purpose white glue (not school glue)
- Glue injectors
- Frog tape / green painters tape
- Poly-coated paper
- Famowood wood filler
- Weights
- Clamps
- Wood blocks
- Putty knife
- Paper (preferably waxed or poly-coated paper)
- Cling wrap (not necessary if using preferred paper)
- Hemp Oil (if you want to keep and refurbish some of the raw wood)
Don’t waste your money on a glue syringe for veneer work unless it has a good selection of thin blunt needles to get into tight spots (refer to step 11 to see what a good set looks like). I tried the syringe shown in the picture above, since I had it in my craft stash, but quickly discovered that it was useless for veneer repair!
Step 7: Gluing Veneer Without a Syringe
The first thing I tackled was the big split with the bubble. Since I didn't have the proper syringe to start, the next best thing is to pour some glue into a plastic lid. Use a thin piece of stiff material, such as the laminate edging shown in the 3rd picture, to scoop some glue. Push it under the veneer as far as you can and move it around. Apply glue as many times as needed to get a good thin coat under the wood.
Wipe away any glue that oozes out with a damp cloth.
Step 8: Apply Weight
The best thing to put right on top of the repair is waxed paper or poly-coated paper before it’s clamped. We didn’t have either at the time so instead use regular bond paper and a piece of plastic wrap on top of that to prevent sticking to the weight (the glue will seep through). We didn’t have a long enough clamp to reach the middle, so used an antique iron as a weight instead. Sometimes you just have to improvise.
On the edges, we used blocks of wood under both sides of the clamps to prevent marks and distribute the weight. If you don't use blocks of wood, you could end up with noticeable indentations from the clamps that will show once the wood is painted. You'll just trade one imperfection for another.
Once dry, under adequate clamping and weight, the veneer will be nice and flat again. The paper seen in the last picture that is stuck to the surface will be sanded right off.
Step 9: Fill Missing Veneer With Wood Filler - Prep
If you have missing veneer, you still must go through the process of gluing down the edges and clamping first as I did in the previous steps. After following those instructions, first tape along the edge with green painters tape. Apply more green tape around the entire patch so it’s surrounded. Now it’s time for the wood filler. Famowood is Hubs’ favourite brand because it won’t crack or shrink; it also cleans up easily!
For larger pieces of missing veneer, Hubs scores the field of the repair to provide some tooth for the wood filler to stick to. Use a utility knife to cross hatch as shown (see the last picture).
Step 10: Wood Filler Application
With a putty knife that’s as wide as the repair, scoop some filler out of the container and close the lid (which we forgot to do and will lead to it drying out!). Start at one end and make a first pass with the putty knife. Make as many passes as necessary to smooth it out to the same thickness.
Hubs likes to feather the edges of the filler into the tape. Don’t worry if it’s a little high on the actual edge because it will be sanded. Remove the tape. Famowood dries in 15 only minutes! Once dry, it acts just like real wood and is ready to sand. Apparently, Famowood is available in many different wood colours and you can stain it too. I’d be curious to see how it takes stain – another time :) For small chips on the edge, apply one piece of tape and use wood filler to fill in the missing veneer.
When done, put a piece of plastic over the container of the wood filler before closing the lid – or store it upside down – to help prevent the filler from drying out in storage.
Step 11: Glue Veneer With a Syringe
There's nothing wrong with improvising, but the proper tool just makes things so much easier. These glue syringes would have been ideal to fill the bubble we fixed earlier.
An injector set like this is great because it comes with several barrels and blunt-end needles in a variety of gauges. Nothing is better than a needle-tipped syringe for applying glue in awkward spots or deep into cracks.
Just fill the barrel with glue. Squeeze the glue under the veneer, wipe the excess off with a damp cloth and clamp as explained earlier.
When done all your veneer repairs, remove the excess glue from the syringe. If you clean and rinse thoroughly right away, these syringes should last a lifetime. Unless you're like us and completely forgot to wash the syringe before the glue dried! Don't be like us :)
Step 12: Sand
Sanding is best done outside where you don’t have to be concerned about kicking up dust. We arranged all our pieces like an assembly line and set up our workbench in the driveway.
For larger pieces like the lid (this is the one that had the ‘bubbled’ veneer), we used an electric sander to smooth it. Don’t go to town and sand too deep or you’ll go right through the veneer and have to patch again! Use a light touch to get things relatively smooth.
We use old socks to get off the initial sanding dust. Then we lightly mist a clean cotton cloth with water to remove the rest.
The drawers were in good shape, save for some water marks. Because the knob was in the way (it’s glued in so can’t be removed), we hand sanded with a fine sanding sponge.
The goal is just to give enough tooth for the primer to stick to the surface. You don’t have to sand the finish back to bare wood.
Step 13: Glue or Fill?
As we were sanding the drawer surround, a piece of veneer chipped right off the edge. If you happen to have the chipped piece, it’s really up to you whether you want to glue it back or replace it with wood filler. If you’re already at the sanding stage by this point and don't want to wait, opt for wood filler. After 15 minutes of dry time you’ll be caught up again.
Since we already had other things drying that we used the syringe on, we glued and clamped. In this case, Hubs just smeared the glue on with his finger; you don’t always need fancy tools. You'll see the repair of this piece live in the video at the beginning of this Instructable.
Step 14: Primer Choice - They're Not All Created Equal
The final prep before paint is to prime the wood. With the intention of painting the table, after sanding we tested two different primers. We placed our primer samples on the back of one of the pieces.
The primer shown on the left is Fresh Start from Benjamin Moore (K046). On the right is a product called INSL-X Stix. Both primers have excellent adhesion. I don’t honestly recall which one Hubs ended up spraying the pieces with, but for some reason we got a lot a weird colour bleed right through the primer (sorry there’s no pictures). Hubs changed gears and went out to purchase a different product – still in the INSL-X family called Seal Lock Plus. Seal Lock Plus is an alchohol based product that is phenomenal at blocking stains. It’s an alternative to shellac and dries in 15 minutes.
The lesson here is that how well a primer sticks isn't the only test of a good primer when it comes to furniture. Be on the look-out for bleed through - which can ruin your paint finish - and be prepared to buy a primer product that not only sticks but blocks stains too.
Hubs sprayed everything with the new stain-blocking primer (except for a few pieces we kept natural wood). To our relief, it did the trick.
Step 15: Paint Prep - Wrap Drawers
For the drawers, apply FrogTape to the inside where you don’t want paint to bleed and burnish it down well. Here, we’re demonstrating on the swing out drawer, but did this to all the drawers. FrogTape is edge-treated with a patented adhesive and it’s our preferred tape because it provides a crisp line (as long as you remember to put it back in container it comes with).
Once the FrogTape is applied, you can use cheap masking tape along the edge. This will give you a surface to attach the poly-coated paper. The poly-coated paper is essentially like a freezer paper and is impervious to the moisture in the paint. Together, they protect the interior of the drawer.
Use another piece of masking tape on the edge of the poly-coated paper and wrap it around the inside of the entire drawer to protect it from overspray.
The drawers are all wrapped and ready for paint!
Once the primer was dry and a few light coats of paint was sprayed on, the finish was perfect. When choosing paint, get one specifically formulated for furniture; it will be more durable. The one we chose for this project was PPG BreakThrough in a light blue colour.
Step 16: Clean Hardware
As Hubs was taking care of painting, I cleaned up the hardware. I didn’t want to affect the patina at all – just clean off years of grime.
I used Method All Purpose Cleaner; it didn’t even require rinsing. The bottom hinge of the first picture is cleaned; it’s just enough of a difference to shine it up a bit. If you have a tried and true method of cleaning metal, let me know in the comments!
Step 17: Seal Raw Wood With Hemp Oil and Paint
I don’t know the proper name of the piece shown above so I’ll call it the under belly. I wanted to keep some of the natural wood; the wood on the underbelly did not have any previous finish and was raw so I applied Hemp Oil to protect it.
You can use a bristle brush or wipe it on with a cotton rag as shown. Apply hemp oil generously. Let the wood tell you if it needs more. If it soaks in and still looks dry, apply more. You can't really over apply it; just make sure to wipe away the excess within 12 hours. I wiped off the excess oil with a clean, dry cloth. Although hemp oil was used on the outside, we painted the inside blue to match the rest of the table (you'll see that later).
Although I'm not covering the painting process, you can read more about it here.
Step 18: Get Organized
If possible, work close to the area where you plan on putting your finished piece. We worked on the floor on top of a piece of cardboard to re-assemble the piece.
I transferred all our pictures onto an iPad so we could see exactly how everything should go back together. This is where you’ll be happy you took lots of pictures and marked the hardware! Without this pictures to guide us, we would have been stumped about which hardware goes where!
As you can see, the hardware doesn’t look shiny and new. It’s clean but maintains the original patina. Just the way we like it!
Step 19: Reassemble
The escutcheons were a bit difficult to put back because of the paint overspray in the holes. Hubs solution was to press it in as far as possible, then use a clamp to drive it in the rest of the way. Just by tightening the clamp, he was able to get them snuggly back in place. You can protect the metal if you like, but we didn't bother.
We didn't paint the end caps on either side of the swing drawer. I'd like to say we did that on purpose, but honestly they went into a Ziploc with the rest of the hardware and we forgot to paint them. It's one of those 'happy accidents' that worked out better than planned! I like that there's still a few areas that are unpainted.
One side goes on first before the drawer and then the other side gets screwed in place to secure the swing mechanism.
After that, the underbelly went back on. Look how drab it used to look originally before the hemp oil and paint (2nd last picture). Doesn't the wood look so rich and lustrous now (last picture)? It slips in place via dowel and should sit underneath a metal catch (which we put on prematurely and had to undo to get it properly back in place later).
Step 20: Finish
L-brackets attach the middle section onto the table top. Then we were able to screw the metal stand back on.
Before screwing the drawers down, double check to make sure the pieces are facing the right direction. In the second picture above, you can see the drawer surround is facing backward! Hubs only realized his mistake as we were starting to screw on the second one. He unscrewed them and turned them around.
The last piece on the underside to attach were the brackets to hold the metal legs in pace.
We stood the table up and fixed the metal tab holding the underbelly (4th picture).
We unwrapped the paper on the drawers. As you saw earlier, Hubs’ secret trick to preventing paint seepage into the drawers is to use FrogTape to seal around the inside perimeter before applying a poly-coated paper. Peel the frog tape back on a 45 degree angle to reveal a crisp paint-free edge.
Remove any green tape from pieces that still have the R & L tags.
Step 21: I'm Ready for My Closeup, Mr. DeMille
I think the touches of wood we left are a nice contrast with the paint colour. It's nice to have a few small references to remember how this vintage table used to look! The end caps were the one thing on the table still in perfect condition; we didn’t have to refurbish them at all.
I haven’t sealed the inside of the drawers yet but I’ll probably use hemp oil again.
Step 22: A Second Life!
I’m sure that many a person passed up this old table at the thrift store because of the condition of the veneer. They might do a double take if they could see it now! It’s come a long way, baby (baby blue, to be exact)!
You don’t necessarily have to replace the double lids again. If you prefer, one lid is perfectly fine to cover up the gap where the sewing machine used to be. The first picture shows both lids with a grouping of succulents on top. The second configuration would be well suited for a laptop station.
Step 23: BREAKING NEWS - Voting Is Now CLOSED
Birdz of a Feather is excited to share that we've been nominated for an Amara Award in the Best Creative Blog category. Voting goes until September 11th, 2019.
Show us some ❤ by casting a vote!
Step 24: Vote for Us and Subscribe
Seeing the before (first pic) with the extent of veneer repair, did you ever think it would look this good again? If you enjoyed this Instructable, don't forget to vote for us in the Epilog Contest!
Get your DIY mojo on and subscribe to us here on Birdz of a Feather. You can also follow us on Pinterest, Facebook, YouTube and Instagram.
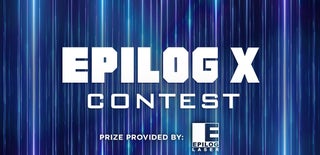
Participated in the
Epilog X Contest