Introduction: Vintage Dim Bulb Tester
For those of you who restore vintage electronics, like radios or tvs, you know the importance of powering up an untested device slowly (for those of you who are new to the hobby see this article from antiqueradio.org). You also know the high cost associated with buying a decent variac. For me, this conflict lead me to building my own dim bulb tester (DBT, also known as a poor man's variac) as a substitute. However, I didn't want to build a utilitarian collection of home depot parts and wires like most other DBTs. I wanted something that I wouldn't be embarrassed to sit next to the beautiful vintage radios I was working on. Thus I created this vintage, antique looking DBT.
However, just as my lack of money forced me to build a DBT instead of buying a proper variac, I was forced to use scraps and repurpose parts wherever I could. Here's how I did it for less than $30, in case you'd like to build one too.
Step 1: Parts, Tools, & Skills
Before we begin, please note that most of these materials (wood, wire, caps, etc) were scraps I had laying around my shop. In some cases you wont have access to the exact same items I used: don't worry! This device is fairly simple and substitutions can be easily made to fit your budget, supplies, or taste.
Here's what you'll need:
PARTS
- 3 Clear, incandescent light bulbs. One 25, 40, and 60 watt (Note: They don't have to be clear but I think they look better and it's easier to see them when they run dim. Also, the wattages can vary some and some equipment will need a higher wattage bulb. DONT use CFLs)
- 3/4" thick scrap wood: (I used dark walnut but any wood you like will work. See the cut diagram in the next step for amounts)
- 4 weatherproof bulb sockets.
- 2 midsize wire caps
- Finish coat (Polyurethane or lacquer of either the spray on or paint on kind will work fine)
- Wood glue
- Light bulb to plug adapter
- 8 1/2" screws
- 13 1" drywall screws
- 1 small machine screw (see step 7 for details)
- 1 small wire bracket or staple
- Plug
- Wire
- Cloth wire* (I had some extra from a pendant, any power cord can be used as a substitute)
- 4 way rotary selector switch.
- Mid size finish nails (not pictured)
- Duct tape* (not pictured)
- Small piece of 1/4" or 3/16" thick plywood
TOOLS
- Drill (bench or handheld is fine) & small wood bits
- Hammer
- Miter saw
- Table saw*
- Router & 1/2" round-over bit*
- Pencil
- Flathead screwdriver
- T-square*
- Wire cutters
- 1 1/2" hole auger (This is for the 4 bulb sockets. Make sure you check their diameter and use an auger that will allow for a snug fit)
- Sandpaper
- Rag
SKILLS
This project assumes at least:
- A basic understanding of woodworking
- A basic understanding of electrical wiring
- A knowledge of how to safely use all tools mentioned above (work at your own risk!)
(*optional)
Step 2: Make Cuts & Drill Holes
- Using a miter saw cut your stock wood as shown in the attached cut pattern. (A table saw will make things much easier but you can get away with just a miter saw. Also, I used 3/4" material but you could use thicker material if you like. Make sure to adjust the measurements accordingly.)
- Optional: Using a router fitted with a 1/2" roundover bit, round off the outside top edge of each side piece as shown in the diagram.
- Mark the center points for the four 1 1/2" holes on the top and front pieces. Then, using a 1 1/2" auger and a drill, drill the holes from the outside in to avoid blowout. (A drill press will make things easier but is optional)
- Mark then center point for the rotary switch, then, using a 3/8" or 1/4" drill bit, drill the hole.
- Countersink the holes on the underside of the bottom piece as shown in the cut diagram.
Step 3: Assemble the Cabinet
Now you're ready to put the cabinet together. First a couple of notes:
- Make sure you put a small amount of glue wherever two pieces of wood are connected.
- Drill pilot holes wherever finish nails or screws are used to avoid the wood splitting.
Alright, let's get started:
- Screw the back stops to the inside of each side piece using the 1" screws. They should be flush with the bottom of each side and a half inch from the edge as shown in the picture. (Note that each back stop will be attached to the side of each piece without the predrilled pilot holes)
- At this point the top needs to be attached to the sides. There are several ways to do this:
- Use a Kregg jig to do pocket joints
- Use a biscuit joiner to join them together - my suggestion
- Use finish nails from the outside - difficult because of the rounded edges on the sides.
- Clamp and glue them
- Nail the front to the top and sides. The face should be flush with the outside edge of the sides and top. The large hole should be on the right and the small hole on the left.
- Attach the assembly to the base using the 1" screws. (Note the base should extend beyond the cabinet assembly 1/4" on all sides except the back, where it should be flush)
Step 4: Sand & Finish the Cabinet
- Sand all the outside surfaces of the cabinet. A medium grit sandpaper will do fine, like 60 or 80. (For a better finish start with a coarse grit like 30, then sand with a medium grit, and finally a fine grit like 150 or 220)
- Give the back panel a light sanding as well.
- Wipe all the surfaces of the cabinet with a damp, not wet, rag.
At this point you should stop to clean up your work area. Trust me, it helps.
- Finish the cabinet and the back panel using whatever product you prefer. (I used a spray on polyurethane, for a better finish sand with a fine grit sand paper and wipe down after the first coat dries)
- Apply a second coat after the first dries.
Step 5: Prep the Wiring
- Begin by cutting the power cord to length, it should be at least three feet long. (Longer is better)
- At either end, cut away 1" of the exterior sheathing then strip and expose a 1/2" of each of the wires.
- Remove the shell of the plug and feed the stripped end of the cord through it.
- Connect the wires to the plug leads.
- Optional: Some plugs will have a built in mechanism for holding the wire inside the plug. Mine did not so I did the following: Wrap a small amount of duct tape or electrical tape around the point where the individual wires come together. This will create a stop which will prevent the wire from pulling out. You'll need to do some trial and error to find the right amount.
- Repeat step 2 on the opposite end of the power cord, only this time cut away 6" of sheathing instead of 1".
- Using a wire bracket, or a heavy duty staple, secure the other end of the power cord inside the box. (Make sure to align the wire with the hole in the back cover and to place the bracket inside the box so it wont interfere with the installation of the back)
- Coat the inside surface of each of the 1 1/2" holes with a small amount of glue.
- Place one bulb socket in each of the four holes. Make sure they are pressed all the way down.
- Wipe away any excess glue with a damp rag.
- Using a flathead screwdriver, remove the knob from the rotary switch by unscrewing the small silver screw on the front. Set the knob and screw aside.
- The rotary switch will have four small nuts embedded into each corner of the switch body. Pry these out with the screwdriver, but don't break the plastic housing.
Step 6: Finish the Wiring
Use the attached wiring diagram as a guide for the following steps. (Note that I substituted red for white in the diagram so it would show up)
- Using a wire cap, connect the white wire from the power cord to the black wire from the bulb socket attached to the face.
- Using another wire cap, twist the white wires from all four bulb sockets together.
- Create two jumper wires using two 6" pieces of wire with 1/2" exposed at either end.
- Connect the black wire from the power cord and one of the jumper wires to pin #1 on the rotary switch.
- Connect the other end of the jumper wire from pin #1 and the other jumper wire to pin #3.
- Connect the free end of the jumper wire from pin #3 to pin #5.
- Connect the black wire from bulb socket #1 to pin #2.
- Connect the black wire from bulb socket #2 to pin #4.
- Connect the black wire from bulb socket #3 to pin #6.
Step 7: Final Assembly
- Position the rotary switch on the inside surface of the front panel so that the knob shaft goes through the predrilled hole.
- Screw a 1/2" screw through each of the holes at the four corners to attach the switch to the cabinet. (Note, make sure that the switch is positioned so that when the knob is in the off position it points up)
- Turn the cabinet over and place a small washer around the knob shaft as pictured.
- Reattach the knob. (Because of the thickness of the wood, the screw that came with the switch will no longer be long enough to connect the knob to the shaft. I couldn't find a machine screw in my shop that fit so I just found a flathead screw that was the right diameter and long enough then forced it into the threaded hole on the shaft. It worked for me but I DONT recommend this. Try and find the right screw if you can.)
- Screw the bulb plug adapter into the empty bulb socket on the front of the cabinet.
- Turn the cabinet back over and attach the back cover using the remaining four 1/2" screws
- Stand the cabinet up and screw in the three light bulbs with low to high wattage going left to right.
Step 8: Test & Enjoy
Congratulations! You're done. You can now test out your cabinet. (Note, you may want to do a test run before screwing in the back panel to save you some time if you have any trouble)
- Plug it in, make sure the switch is in the off (up) position.
- Plug in a lamp to the outlet on the front of the cabinet. Make sure the lamp is on.
- Turn the knob clockwise. Each bulb, from left to right, should light up in succession with the 1st one being brightest and the last one being dimmest.
If everything looks good you can being using your DBT.
Additional note:
You'll notice there aren't any labels or stickers on the cabinet to indicate the knob positions. I am still working on a solution for this. I tried several things but didn't like the results. I'll post my solution when I have it! Feel free to comment with suggestions.
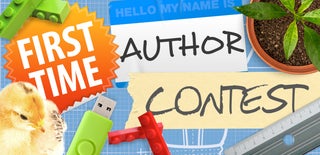
Participated in the
First Time Author Contest