Introduction: LDO Voltage Regulator, 1 MOSFET, 2 BJTs, and a Zener, <= 40V Supply Voltage
I searched the web to find out if the standard L78XX voltage regulators could be run in parallel in order to supply more amps than a single L78XX IC alone. I found no references to a successful implementation. However,I came across this Low Dropout Voltage Regulator circuit on homemade-circuits.com suggesting this circuit was good alternative.
The author used a high-current PNP BJT in his sample builds. I wanted more current than a single BJT could supply. Since running IGBTs in parallel is more complicated than running MOSFETs in parallel, I needed to modify the circuit to make it work with parallel MOSFETs. I also wanted to use N-Channel MOSFETs because they are less expensive than, and carry more current than, their comparable P-Channel MOSFET counterparts. I did build a P-Channel MOSFET version, and that circuit will be disclosed in another post here in instructables.com.
The input voltage in this circuit is limited to 40VDC due to the choice of BJT controller transistors. In the P-Channel MOSFET version, I used IGBTs as the controller transistors and that circuit can handle input voltages higher than 40V.
Supplies
- (1 to 8) N-Channel MOSFETs - I have used IRFP250N and IRFP460, up to 8 in parallel; substitute your favorite as desired.
- (1) NPN BJT - I used 2N4401; others such as 2N3904 should work equally well.
- (1) PNP BJT - I used 2N4403; others such as 2N3906 should work equally well.
- (1) Zener Diode - I used 1N4742, a 1W, 12V Zener diode; I have also used other Zener diodes, 4.7V-18V with good results.
- (2) 4.7 kΩ, ½W resistors.
- (1) 100 kΩ, ½W resistor; may need to lowered to 10 kΩ, ½W resistor, as your number of parallel MOSFETs increases. This is a MOSFET Gate pull-up resistor that switches the MOSFET on.
- (1) 100 µF, 50V electrolytic capacitor. This is a smoothing capacitor that smooths our ripple and slows the oscillation of the circuit
Step 1: Build the Controller Circuit on a Breadboard
The controller components handle very little current, so a standard breadboard works well. The MOSFETs are placed on a separate circuit board that can handle higher currents. There are three connections between the two boards, one for the MOSFET Gate voltage, one for the Drain voltage, and one for the Source voltage.
When the voltage is high on the Drain side of the MOSFET, the voltage at the base of Q2, the PNP BJT. is high, and the PNP BJT is passing no current. This allows the voltage on the Drain side of the MOSFET to open the MOSFET Gate, passing voltage and current to the Source side of the MOSFET.
When the voltage on the Source side of the MOSFET reaches the breakdown voltage of the Zener diode, voltage on the base of Q1, the NPN BJT, is made high, turning on the NPN BJT, which drops the base voltage of the PNP BJT to ground allowing current and voltage to pass through Q2. This, in turn, brings the Gate of the MOSFET to ground, switching off the MOSFET.
And so it cycles. I have measured the oscillation frequency to range between 6.7 kHz and 130 kHz.
I have used the device with a few different loads and it performed well. The voltage remained steady. With this setup using an N-Channel MOSFET as the workhorse and the PNP transistor performing the P-Channel function, that the output voltage of the device is 0.6-0.7 Volts above the rating of the Zener diode. I believe that has to do with the forward bias voltage drop across silicon Zener diodes being ~0.7 V. So when I use a 5.6 V Zener, the output voltage is 6.25 V. In the last photo, I built the voltage controller right into the circuit board where the voltage was needed to run an SN74HCT74N Flip-Flop, which can operate at a maximum of 7.0 V, and the voltage supply rail is at 12.1 V.
Let me know your experience with the device if you build one.
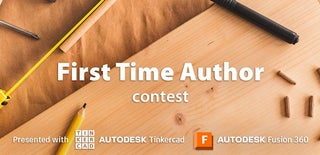
Participated in the
First Time Author