Introduction: WORKBENCH WOODWORKING
Massive solid top,
endless bench dog holes,
6 full depth draws,
2 full depth cupboards,
1 end vice,
1 normal vice.
THIS IS THE 7th THING IVE EVER MADE.
originally i purchased a plan from RON PAULK, a portable work bench. but changed the design so much i looked for something else. i did however love the endless bench dog holes. which i incorporated into my top.
I settled on a Bench build to last published May/June 2001 in fine woodworking by Dick McDonough.
Again i started to change this and that so i kept the draws n cupboards and tossed the rest.
what I made was without physical drawn plans and changes were implemented along the way due to one of the many mistakes or oversights.
the final product is still a finish
I hope you enjoy this project and PLEASE FEEL FREE TO VOICE ANY ADVICE.
endless bench dog holes,
6 full depth draws,
2 full depth cupboards,
1 end vice,
1 normal vice.
THIS IS THE 7th THING IVE EVER MADE.
originally i purchased a plan from RON PAULK, a portable work bench. but changed the design so much i looked for something else. i did however love the endless bench dog holes. which i incorporated into my top.
I settled on a Bench build to last published May/June 2001 in fine woodworking by Dick McDonough.
Again i started to change this and that so i kept the draws n cupboards and tossed the rest.
what I made was without physical drawn plans and changes were implemented along the way due to one of the many mistakes or oversights.
the final product is still a finish
I hope you enjoy this project and PLEASE FEEL FREE TO VOICE ANY ADVICE.
Step 1: Tools
endless clamps
wooden mallet
hack saw
jack and smoothing plane
wood glue
biscuits no 10, 3 large packs
biscuit machine
drill press
screwdriver
door handles x 11
tail vice mechanic's
wood vice
glue gun
electric planer machine
router
router sled
sand paper 80,120,180 220 grits
belt sander
orbital sander
chisel
hammer
steel rule
square
rasp
level
nuts n bolts :
ratchet and sockets
threaded rod x 2
18mm spade bit
aluminum tubing
wooden mallet
hack saw
jack and smoothing plane
wood glue
biscuits no 10, 3 large packs
biscuit machine
drill press
screwdriver
door handles x 11
tail vice mechanic's
wood vice
glue gun
electric planer machine
router
router sled
sand paper 80,120,180 220 grits
belt sander
orbital sander
chisel
hammer
steel rule
square
rasp
level
nuts n bolts :
ratchet and sockets
threaded rod x 2
18mm spade bit
aluminum tubing
Step 2: MATERIALS
recycled red gum fence posts
standard Australian hard wood from Bunning's.
11 door handles
vice
end vice
recycled hardwood floor boards
standard Australian hard wood from Bunning's.
11 door handles
vice
end vice
recycled hardwood floor boards
Step 3: Timber Length: Joint Lengths Not Included
cut timber to length. measurements do not include joints ie, tennon which are at 70 mm each.
Vice jaw block 530 x 40 red gum finished
top = 12 x 90 x 45 x 2270 finished
legs rails if hardwood top
3 x 90 x 90 x 1205
3 x 90 x 90 x 924
top 13 x 90 x 45 x 2270
legs rails if mdf and hard wood top
6 x 90 x 90 x 1205
top 7 x 90 x 45 x 2270
3 x 600 x 2400 MDF sheeting. @ 19 mm
legs regardless of top
6 x 90 x 45 x 590 finished.
dual boxs top and bottom
2x MDF sheeting @ 19mm
box walls
@ 19 mm mdf
4 x 548 x ??????width
under top supports 532
3 x 90 x 45 x 532 mm
clamp tail
1 x 90 x 45 x ?????????
cupbard door frames
sides 4 x 118 x 19 mm x 632
top and bottom 4 x 118 mm x 19 mm x 433 mm
back board
19mm 3/4 ply wood,
size 590 x 1880
Vice jaw block 530 x 40 red gum finished
top = 12 x 90 x 45 x 2270 finished
legs rails if hardwood top
3 x 90 x 90 x 1205
3 x 90 x 90 x 924
top 13 x 90 x 45 x 2270
legs rails if mdf and hard wood top
6 x 90 x 90 x 1205
top 7 x 90 x 45 x 2270
3 x 600 x 2400 MDF sheeting. @ 19 mm
legs regardless of top
6 x 90 x 45 x 590 finished.
dual boxs top and bottom
2x MDF sheeting @ 19mm
box walls
@ 19 mm mdf
4 x 548 x ??????width
under top supports 532
3 x 90 x 45 x 532 mm
clamp tail
1 x 90 x 45 x ?????????
cupbard door frames
sides 4 x 118 x 19 mm x 632
top and bottom 4 x 118 mm x 19 mm x 433 mm
back board
19mm 3/4 ply wood,
size 590 x 1880
Step 4: Tennons for Legs
making tennons for 6 legs
measure and mark your desired depth on all 12 ends of you legs.
using a square trace the line around each end
with a tennon saw cutting to a depth of 10 mm
make several extra saw cuts as it will help to chip away the extra waist.
Using a 1" chisel, work your way around each leg
Note:
HERE WE ARE REMOVING THE EXCESS WAIST, STOP 2-3 MM SHORT OF YOUR NEEDED LINE
(unless your skill with a chisel is better than mine)
THE ROUTER WILL CLEAN UP THE REMAINDER TO MAKE THE PERFECT TENON.
measure and mark your desired depth on all 12 ends of you legs.
using a square trace the line around each end
with a tennon saw cutting to a depth of 10 mm
make several extra saw cuts as it will help to chip away the extra waist.
Using a 1" chisel, work your way around each leg
Note:
HERE WE ARE REMOVING THE EXCESS WAIST, STOP 2-3 MM SHORT OF YOUR NEEDED LINE
(unless your skill with a chisel is better than mine)
THE ROUTER WILL CLEAN UP THE REMAINDER TO MAKE THE PERFECT TENON.
Step 5: Tennon @ the Router Table
Adjust your router bit to cut only down to a depth of 10mm
pass the tennon over the router bit, each pass move the back board back a 6 mm until you are at the shoulder of your tennon.
repeat on all ends of your 6 legs/
pass the tennon over the router bit, each pass move the back board back a 6 mm until you are at the shoulder of your tennon.
repeat on all ends of your 6 legs/
Step 6: Tenon Error
one of the edges cracked away from the sides while on the router.
I used off cuts to place around the job to glue it back in place.
when dry sand excess dried glue and your done,
I used off cuts to place around the job to glue it back in place.
when dry sand excess dried glue and your done,
Step 7: Making the Legs
if you have not already cut your timber to length now is the time to cut the length of your legs
if you are making a dual top then cut :
12 x 90 x 45 x 1205 mm
using a biscuit machine make your slots at each line. i have used no.10 biscuits.
coat each slotted surface with glue, and clamp together,
you should have just made 6 bottom legs and 6 top legs
if your making a dual top ( hardwood and mdf )
12 x 90 x 45 x 1205 mm
if you are making a solid hard wood top.
the top of each leg was shortened to accommodate the sold top.
6 x 90 x 45 x 1205 mm
6 x 90 x 45 x 924 mm
across the flat face of each board. measure and mark every 5 " for the full length of the board. ensuring your first and last are 5" from each end.
glue and clamp together and leave for the night.
if you are making a dual top then cut :
12 x 90 x 45 x 1205 mm
using a biscuit machine make your slots at each line. i have used no.10 biscuits.
coat each slotted surface with glue, and clamp together,
you should have just made 6 bottom legs and 6 top legs
if your making a dual top ( hardwood and mdf )
12 x 90 x 45 x 1205 mm
if you are making a solid hard wood top.
the top of each leg was shortened to accommodate the sold top.
6 x 90 x 45 x 1205 mm
6 x 90 x 45 x 924 mm
across the flat face of each board. measure and mark every 5 " for the full length of the board. ensuring your first and last are 5" from each end.
glue and clamp together and leave for the night.
Step 8: Mortising for Your Legs
drill out as much of the mortise as possible using a spade bit.
depth required is a personal choice. i choose 70 mm.
Using a hammer and chisel clean out the remainder of the waist.
I clamped 3 off cuts around the holes, lining them parallel to the lines.
Using them as a guide to keep my chisel straight.
depth required is a personal choice. i choose 70 mm.
Using a hammer and chisel clean out the remainder of the waist.
I clamped 3 off cuts around the holes, lining them parallel to the lines.
Using them as a guide to keep my chisel straight.
Step 9: Test Fitting Tenons
do a dry test fit to ensure the joint is accurate.
fix any indiscretions with very light sand paper.
Note:
failure to make light adjustments will result in sloppy joints.
first hand experience.
fix any indiscretions with very light sand paper.
Note:
failure to make light adjustments will result in sloppy joints.
first hand experience.
Step 10: Doweling the Joints Jig
bottom and top rails and jig
using a 90 x 45 off cut approx. 200 mm long ( mark this as dowel jig)
measure and mark in from an end, 45mm ( half the width) draw your line down the face.
measure and mark in from the side 45mm again half the width.
where these lines intersect is your drilling point.
using a 12 mm spade bit drill all the way through.
Attach 2 thin scrap pieces of timber to the sides. screw and or glue them in place.
slide the joint together, ensuring your mortise and tennon joint is flush and square to the leg.
place a scrap 90 x 45 on top the leg you just inserted, sliding hard up against the rail and inline with the leg.
slide your jig across the rail cupping the 2nd off cut.
using double sided tape to keep the drilling JIG IN PLACE.
remove the leg so u don't drill through the tennon, the long bit ?
using the jig at the drill ,drill your hole all the way through.
here is the tricky part. A third hand is handy here.
insert tennon back into slot , keeping it square and tightly butted against the shoulder.
with the drill press off, lower the spade bit back down the hole u just drilled until the tip touches the newly inserted tennon.
apply just enough pressure to leave the tiniest indent.
remove joint, remove leg from drill press.
align tip of spade bit 2/32 off center towards the shoulder of the joint and drill through. using a spare scrap board under the tennon so not to blow out the bottom.
REPEAT FOR ALL 12 ENDS
note:
I'm sure there is a easier way to do this, I just don't know it.
using a 90 x 45 off cut approx. 200 mm long ( mark this as dowel jig)
measure and mark in from an end, 45mm ( half the width) draw your line down the face.
measure and mark in from the side 45mm again half the width.
where these lines intersect is your drilling point.
using a 12 mm spade bit drill all the way through.
Attach 2 thin scrap pieces of timber to the sides. screw and or glue them in place.
slide the joint together, ensuring your mortise and tennon joint is flush and square to the leg.
place a scrap 90 x 45 on top the leg you just inserted, sliding hard up against the rail and inline with the leg.
slide your jig across the rail cupping the 2nd off cut.
using double sided tape to keep the drilling JIG IN PLACE.
remove the leg so u don't drill through the tennon, the long bit ?
using the jig at the drill ,drill your hole all the way through.
here is the tricky part. A third hand is handy here.
insert tennon back into slot , keeping it square and tightly butted against the shoulder.
with the drill press off, lower the spade bit back down the hole u just drilled until the tip touches the newly inserted tennon.
apply just enough pressure to leave the tiniest indent.
remove joint, remove leg from drill press.
align tip of spade bit 2/32 off center towards the shoulder of the joint and drill through. using a spare scrap board under the tennon so not to blow out the bottom.
REPEAT FOR ALL 12 ENDS
note:
I'm sure there is a easier way to do this, I just don't know it.
Step 11: Recycled Dowels
using fence post off cuts.
make a 12mm dowel to match dowel holes on the wood lathe.
alternatively buy dowel and match holes to fit.
make a 12mm dowel to match dowel holes on the wood lathe.
alternatively buy dowel and match holes to fit.
Step 12: Leg Assembly
using a large square ensure all corners are square.
lace holes and joints with glue and clamp together.
check square by measuring diagonals.
tap the longest edge to reduce to equal measurements.
WHEN SQUARE AND CLAMPED TOGETHER DRIVE YOUR DOWELS THROUGH BUT NOT ALL THE WAY. LEAVE ENOUGH TO CUT OFF AND SAND .
to keep the bottom of the legs from moving I placed a thin scrap length of timber diagonal across all 4 legs and drove a small nail in then.
lace holes and joints with glue and clamp together.
check square by measuring diagonals.
tap the longest edge to reduce to equal measurements.
WHEN SQUARE AND CLAMPED TOGETHER DRIVE YOUR DOWELS THROUGH BUT NOT ALL THE WAY. LEAVE ENOUGH TO CUT OFF AND SAND .
to keep the bottom of the legs from moving I placed a thin scrap length of timber diagonal across all 4 legs and drove a small nail in then.
Step 13: Under Table Boxes. Top and Bottom
cut 2 sheets of19 mm 3/4" 2400 x 1200 mdf down to :
855 X x 1780
cut leg slots out on both pieces so the slot starts at 867 from one end. each slot 46 mm wide and 69 mm deep
allowing 19 mm (3/4")
the ends of the mdf are glued and screwed to the lip on the top and bottom of each end leg.
for added strength.
glue and screw a 90 x 45 x 800 long to the inside of the outer legs. they call this a cleat
once the mdf board is glued to the leg i glued and screwed to the mdf to the cleat
855 X x 1780
cut leg slots out on both pieces so the slot starts at 867 from one end. each slot 46 mm wide and 69 mm deep
allowing 19 mm (3/4")
the ends of the mdf are glued and screwed to the lip on the top and bottom of each end leg.
for added strength.
glue and screw a 90 x 45 x 800 long to the inside of the outer legs. they call this a cleat
once the mdf board is glued to the leg i glued and screwed to the mdf to the cleat
Step 14: Under Table Boxes. Sides
using 3/4 " mdf make 4 sides to fit internally between both top and bottom mdf sheets.
cut 4 boards to 550 x 855 mm
cut 4 boards to 550 x 855 mm
Step 15: Leg Rail Height Adjustment.
cut 12, 90 x 45 x 350 mm
glue to the ends of bottom rails
glue together to make 6 blocks 90 x 90 x 350.
glue to under side of the bottom rail.
dry over night
round the bottom corner to your desired shape, start to work with a chisel.
when you are close to the shape u like smooth off with a belt sander finish with a orbital sander/
repeat with 6 legs.
glue to the ends of bottom rails
glue together to make 6 blocks 90 x 90 x 350.
glue to under side of the bottom rail.
dry over night
round the bottom corner to your desired shape, start to work with a chisel.
when you are close to the shape u like smooth off with a belt sander finish with a orbital sander/
repeat with 6 legs.
Step 16: Box Sides Test Fitting
insert box ends to test fitting.
do not glue or screw at this stage.
draw runners need to be cut.
do not glue or screw at this stage.
draw runners need to be cut.
Step 17: Draw Runners
measure and mark the appropriate depths for your draws using your own personal selection of tools u will be storing in the draws
the sliding rails I have chosen to put on my draws not the walls.
last minute adjustment.
I made my top 2 draws in to 3 .
2 1/2 draw and 1 deep draw to hold all my rags in a convenient location.
to do this i needed a divider to support my runners.
I glued, screwed and doweled a center support to the top of the box, then places a runner on either side of the base of that runner, off setting the dowels on the other side.
the sliding rails I have chosen to put on my draws not the walls.
last minute adjustment.
I made my top 2 draws in to 3 .
2 1/2 draw and 1 deep draw to hold all my rags in a convenient location.
to do this i needed a divider to support my runners.
I glued, screwed and doweled a center support to the top of the box, then places a runner on either side of the base of that runner, off setting the dowels on the other side.
Step 18: Recycled Timber for Draw Fronts.
large red wood gate posts installed in mid 1950, up rooted Jan 2013
cutting the post down to usable lengths of 1000 mm lengths then down to 23 mm widths and finally down to 19 mm as finished .
true the boards, glue them together, making a large rectangle.
with short testing strokes find the grain direction of each board and align accordingly.
align all grain in one direction before gluing up.
remove any obvious high spots with your hand plane.
sand until happy with your final product.
cut ends flush ready to divide into draw widths.
cutting the post down to usable lengths of 1000 mm lengths then down to 23 mm widths and finally down to 19 mm as finished .
true the boards, glue them together, making a large rectangle.
with short testing strokes find the grain direction of each board and align accordingly.
align all grain in one direction before gluing up.
remove any obvious high spots with your hand plane.
sand until happy with your final product.
cut ends flush ready to divide into draw widths.
Step 19: Under Table Box, Back
using 3/4 ply wood, glue and screw your board to your legs
size is 590 x 1880
measure your diagonal to ensure you have everything square.
size is 590 x 1880
measure your diagonal to ensure you have everything square.
Step 20: Table Top, Outer Edges.
here we will make 3 groups of laminated boards for the
top:
1x 4 90 x 45 clamped along the 90 mm edge @ 2300 mm long
1 x 3 90 x 45 clamped along the 90 mm edge @ 2300 mm long
1 x 5 90 x 45 clamped along the 45 MM EDGE @ 23000 mm cut
measure and mark 2" from each end, that your start point for your biscuits joints at 10 " apart where possible
.
Clamping the group of 4 together, number them 1,2,3,4 cut one end square and level.
Repeat same with the remainder 2 groups.
Mark the outer edge of plank 1 and plank 4, front and back respectively
from the straight edge, measure in 300 and mark the area for the wood vice.
EACH VICE IS DIFFERENT SO PLEASE USE CAUTION WHEN LAYING OUT YOUR MARKINGS.
On the opposite end you cut straight, label your planks again 1,2,3,4
remove plank no 2. lean over to read the inside of plank 1,
on the inside of plank 1 mark as 1b
on the opposite board to 1b, ( board 3) mark as 3b
both 1a and 3b will now be given a 19 mm 3/4" channel 450 long at a depth of 16 mm. cut your channels on the router.
This will be used as the end vice. cut it down to suite your individual needs.
Lay the 4 boards back down with the straight edge back in place. Slide board 2, 450 mm towards the straight cut end, opening up a gap so you can now see the 2 channels in plank 1 and 3.
Clamp back together and cut off the 450 over hang on board 2. this will be used as the sliding section of the end vice.
clamp the other 2 sections of board without any adjustments or alterations.
top:
1x 4 90 x 45 clamped along the 90 mm edge @ 2300 mm long
1 x 3 90 x 45 clamped along the 90 mm edge @ 2300 mm long
1 x 5 90 x 45 clamped along the 45 MM EDGE @ 23000 mm cut
measure and mark 2" from each end, that your start point for your biscuits joints at 10 " apart where possible
.
Clamping the group of 4 together, number them 1,2,3,4 cut one end square and level.
Repeat same with the remainder 2 groups.
Mark the outer edge of plank 1 and plank 4, front and back respectively
from the straight edge, measure in 300 and mark the area for the wood vice.
EACH VICE IS DIFFERENT SO PLEASE USE CAUTION WHEN LAYING OUT YOUR MARKINGS.
On the opposite end you cut straight, label your planks again 1,2,3,4
remove plank no 2. lean over to read the inside of plank 1,
on the inside of plank 1 mark as 1b
on the opposite board to 1b, ( board 3) mark as 3b
both 1a and 3b will now be given a 19 mm 3/4" channel 450 long at a depth of 16 mm. cut your channels on the router.
This will be used as the end vice. cut it down to suite your individual needs.
Lay the 4 boards back down with the straight edge back in place. Slide board 2, 450 mm towards the straight cut end, opening up a gap so you can now see the 2 channels in plank 1 and 3.
Clamp back together and cut off the 450 over hang on board 2. this will be used as the sliding section of the end vice.
clamp the other 2 sections of board without any adjustments or alterations.
Step 21: Bench Dog Holes.
CLAMP the 3 sets of boards back together.
measure along the length of board 1 and mark at 4 " intervals, with a square mark across the 4 boards. repeat for all groups.
find the center of each board and draw a continuous line from one end to the other.
where lines intersect and with (personnel choice ) drill a 19 mm 3/4 " hole at the drill press.
repeat this on the 2nd and third group of boards.
Note
you can have as many or as little hole as you like. make them suite your needs.
measure along the length of board 1 and mark at 4 " intervals, with a square mark across the 4 boards. repeat for all groups.
find the center of each board and draw a continuous line from one end to the other.
where lines intersect and with (personnel choice ) drill a 19 mm 3/4 " hole at the drill press.
repeat this on the 2nd and third group of boards.
Note
you can have as many or as little hole as you like. make them suite your needs.
Step 22: Top Outer Edges Gluing / Vice Check Out
Measure and mark out your vice.
Please remember that every vice is different so these measurements will be useless to anyone.
I wanted to keep the open area directly underneath the table where the vice will sit open and free from too much obstruction, otherwise I could have removed the back plate and lowered the entire vice and avoid the large cut out. NOW AFTER MONTHS OF USE, A WAIST OF SPACE.
locate your boards marked 1-4 to be glued on the 90mm side
place biscuit slots and evenly cover with glue
repeat the process to the remanding top sections
ensure when gluing the end with a sliding vice you insert a 90 mm x 45 mm scrap to prevent the boards from bending
ENSURE WHEN CLAMPING YOU ALSO CLAMP THE TOPS FLAT, WILL SAVE YOU HEAPS OF TIME LATER.
Please remember that every vice is different so these measurements will be useless to anyone.
I wanted to keep the open area directly underneath the table where the vice will sit open and free from too much obstruction, otherwise I could have removed the back plate and lowered the entire vice and avoid the large cut out. NOW AFTER MONTHS OF USE, A WAIST OF SPACE.
locate your boards marked 1-4 to be glued on the 90mm side
place biscuit slots and evenly cover with glue
repeat the process to the remanding top sections
ensure when gluing the end with a sliding vice you insert a 90 mm x 45 mm scrap to prevent the boards from bending
ENSURE WHEN CLAMPING YOU ALSO CLAMP THE TOPS FLAT, WILL SAVE YOU HEAPS OF TIME LATER.
Step 23: Top Option Choice Time.
Here you have the choice of making a MDF top with hard wood sides
or
a solid hard wood top.
or
a solid hard wood top.
Step 24: MDF Top
2400 x 900 x 3 MDF sheets @ 19mm 3/4" each
evenly coat the entire surface with glue
lay the second sheet on top and cover with glue again.
place the top sheet on
carefully align all edges of the 3 boards, failure to do so will create enormous work later.
using as many clamps as possible clamp the 3 boards together adjusting each clamp slowly avoiding the sheets from sliding around while clamping them tight.
NOTE:
UNFORTUNATELY, I CAN NOT TELL YOU WHY MY BOARDS DRIED WITH A HUGE BOW IN THEM.
HOPE YOU HAVE BETTER LUCK THAN I DID.
evenly coat the entire surface with glue
lay the second sheet on top and cover with glue again.
place the top sheet on
carefully align all edges of the 3 boards, failure to do so will create enormous work later.
using as many clamps as possible clamp the 3 boards together adjusting each clamp slowly avoiding the sheets from sliding around while clamping them tight.
NOTE:
UNFORTUNATELY, I CAN NOT TELL YOU WHY MY BOARDS DRIED WITH A HUGE BOW IN THEM.
HOPE YOU HAVE BETTER LUCK THAN I DID.
Step 25: Solid Hard Wood Top
clamping the 3 table top sections together.
1x 4 90 x 45 clamped along the 90 mm edge @ 2300 mm long
1 x 5 90 x 45 clamped along the 45 MM EDGE @ 23000 mm long
1 x 3 90 x 45 clamped along the 90 mm edge @ 2300 mm long
clamped in that order.
the boards glued along the 45mm edge are the center bards of the table
to glue the 3 sections together is no different than gluing the individual sections together with one exception.
pay close attention to your clamps and ensure the overall table top is as close to flat as you can make them before the final turns of the clamps are made.
1x 4 90 x 45 clamped along the 90 mm edge @ 2300 mm long
1 x 5 90 x 45 clamped along the 45 MM EDGE @ 23000 mm long
1 x 3 90 x 45 clamped along the 90 mm edge @ 2300 mm long
clamped in that order.
the boards glued along the 45mm edge are the center bards of the table
to glue the 3 sections together is no different than gluing the individual sections together with one exception.
pay close attention to your clamps and ensure the overall table top is as close to flat as you can make them before the final turns of the clamps are made.
Step 26: Draws and Draw Runners
select the desired thickness for your draws and calculate how many you will make.
cut 12 draw runners from hard wood, pine, plywood or mdf, @ 35 mm wide x 850 mm long
glue and screw into box side slots.
I APPOLIGISE FOR THE LACK OF PHOTOS ON MAKING THE DRAWS.
we had a hard drive die and lost all pics of the draws.
draw 1,2 and 3
measure and mark the half way point of the overall width of the top draw and insert a 300 mm x 850 mm mdf board, glue, screw and dowel it to the top of the box.
this is the divider board and board to hold the runners for the first and second draws.
thickness of the draws is decided by your own personal needs.
make your draws using finger joints or dowel joints ensuring with this extra deep draws they have a thick bottom.
These have 19 mm / 3/4" MDF bases glued, screwed and biscuit-ed to the sides, back and front of the draws.
the draw sides sit on top of the base. secure the sides to the base. glue together and slide on top of draw runners.
once all the draws are made and sitting on their runners its time too measure from the width and height of each draw.
ensure you cut each draw face one at a time to allow for the thickness of the saw blade.
attach the face after all draws have been made and are sitting institute.
use playing 2 cards for even spacers between draws.
use double sided tape to hold the faces in place while you screw from the inside of the draw, 2 securing screws.
no glue used here so draw faces can be replaced or removed if needed at any time.
handles are again a personal choice, choose your handles and your preferred handle location
measure down to your chosen height and mark your first point to drill.
measure the distance between the threads on your handles
transcribe that measurement to your draw and drill your second hole.
I had to move the location of all my handles as the reclaimed timber imperfections restricted my handle locations.
cut 12 draw runners from hard wood, pine, plywood or mdf, @ 35 mm wide x 850 mm long
glue and screw into box side slots.
I APPOLIGISE FOR THE LACK OF PHOTOS ON MAKING THE DRAWS.
we had a hard drive die and lost all pics of the draws.
draw 1,2 and 3
measure and mark the half way point of the overall width of the top draw and insert a 300 mm x 850 mm mdf board, glue, screw and dowel it to the top of the box.
this is the divider board and board to hold the runners for the first and second draws.
thickness of the draws is decided by your own personal needs.
make your draws using finger joints or dowel joints ensuring with this extra deep draws they have a thick bottom.
These have 19 mm / 3/4" MDF bases glued, screwed and biscuit-ed to the sides, back and front of the draws.
the draw sides sit on top of the base. secure the sides to the base. glue together and slide on top of draw runners.
once all the draws are made and sitting on their runners its time too measure from the width and height of each draw.
ensure you cut each draw face one at a time to allow for the thickness of the saw blade.
attach the face after all draws have been made and are sitting institute.
use playing 2 cards for even spacers between draws.
use double sided tape to hold the faces in place while you screw from the inside of the draw, 2 securing screws.
no glue used here so draw faces can be replaced or removed if needed at any time.
handles are again a personal choice, choose your handles and your preferred handle location
measure down to your chosen height and mark your first point to drill.
measure the distance between the threads on your handles
transcribe that measurement to your draw and drill your second hole.
I had to move the location of all my handles as the reclaimed timber imperfections restricted my handle locations.
Step 27: Solid Top End Caps.
on both ends of your table top will have end caps to protect the ends from damage.
i you have not already done so, then now is a perfect time to square off your ends
measure and mark 1/2 " in from each end of your table top along the end grain.
place a piece of tape along the line to ensure the router stops at this line.
this rebate will be 19 mm 3/4" wide and 15 mm deep and 10 mm down from the top of the work bench.
use a router with a straight bit for this job.
As per the photo the end cap was going to be 180 mm wide but due to aesthetic purposes I reduced the width to 90 mm .
cut the rebate, stopping 1/2" from each end, 19 mm wide and 15 mm deep and 10 mm from the top edge.
cut 1 mdf strip, 19 mm thick x 29 mm wide and 847 long
the strip sits in the channel without glue or screws. keeps everything aligned and allows for seasonal movement .
instead it is held in place by one nut and bolt on each end of the cap.
the end caps are attached to the top via 2 bolts, one on each end of the end cap, secured via a nut inside an aluminum tubing which is drilled into the outer board on both front and back edges, 70 mm in from the end grain on the bench top and 20 mm in from the ends of the end caps.
i you have not already done so, then now is a perfect time to square off your ends
measure and mark 1/2 " in from each end of your table top along the end grain.
place a piece of tape along the line to ensure the router stops at this line.
this rebate will be 19 mm 3/4" wide and 15 mm deep and 10 mm down from the top of the work bench.
use a router with a straight bit for this job.
As per the photo the end cap was going to be 180 mm wide but due to aesthetic purposes I reduced the width to 90 mm .
cut the rebate, stopping 1/2" from each end, 19 mm wide and 15 mm deep and 10 mm from the top edge.
cut 1 mdf strip, 19 mm thick x 29 mm wide and 847 long
the strip sits in the channel without glue or screws. keeps everything aligned and allows for seasonal movement .
instead it is held in place by one nut and bolt on each end of the cap.
the end caps are attached to the top via 2 bolts, one on each end of the end cap, secured via a nut inside an aluminum tubing which is drilled into the outer board on both front and back edges, 70 mm in from the end grain on the bench top and 20 mm in from the ends of the end caps.
Step 28: Reclaimed Red Gum Vice Backing.
rough cut the red gum to roughly the thickness you wish and allow extra for smoothing and sanding.
cut my 4" slab into 2 x 2" then preceded to clean up one until it resembled the thickness required
reduce the thickness even more to accommodate the minimum 110 mm thickness I wanted for my vice.
I used the left overs to make more dowels and bench dogs.
cut my 4" slab into 2 x 2" then preceded to clean up one until it resembled the thickness required
reduce the thickness even more to accommodate the minimum 110 mm thickness I wanted for my vice.
I used the left overs to make more dowels and bench dogs.
Step 29: Solid Top Flattening.
after gluing my 4 top sections together I was really daunted at how much work was required to level this top.
after several phone calls i found a furniture factory who would put the top through their dual barrel sander.
$110 dollars and 14 days later the top arrived cleanly sanded.
at first glance, I was ecstatic with the outcome. days later when i had the time i noticed by feel, 1 large hill and 2 gully's running down the center of the table.
Time to router the top flat.
after several phone calls i found a furniture factory who would put the top through their dual barrel sander.
$110 dollars and 14 days later the top arrived cleanly sanded.
at first glance, I was ecstatic with the outcome. days later when i had the time i noticed by feel, 1 large hill and 2 gully's running down the center of the table.
Time to router the top flat.
Step 30: Top Routeing Preparation!
require 2 long straight edges, both 6 inches longer than the bench top on each end. I used 19mm 3/4" MDF sheeting
one for each side of the table. 2420 being the full length of a 1200 x 2400 mdf sheet.
clamp them to the workbench so both ends are parallel to each other and also the same height from the top
this process can be found by a quick google search.
to continue you will need the following:
4 short screws with washers
2 lengths of light rope / string
place one screw several inches below the top of the straight edge and as close to each corner as you can. attach cord or string diagonally from the outer vertical face across the table pulling the string so tight it makes a twang when u flick it
now I you have a large X across the table made of string.
take 2 small pieces of the rope and sit them under the rope, just as it turns the corner of the straight edge. the objective is to raise the top string up the thickness of the string it self.
I know the back edge is perfectly straight so I can adjust the bottom string up until both strings touch each other.
the perfect location is when you push the bottom string down without moving the top one and vice versa.
lift the line up with off cut strings, 2 lines touching means, if the line was not lifted up, both lines would intersect at the same point..
now all 4 corners are level with each other.
NOT VERY CLEAR SO I WOULD SUGGEST WATCHING THE YOU TOUBE VIDEO ON THE PROCESS.
Step 31: Sled for Routing and Setting Router Depth.
a sled for guiding the router across the table top.
needs to be solid enough not to bow when the entire weight of the router is in the center.
19mm 3/4" plywood base and sides. EACH router will need a different set up to allow for the different styles of routers.
route slot with large straight bit
glue and screw the box together making sure to test your router in the box before you glue it together, my router has strange knobs sticking out preventing me from having 2 high sides so i made the front edge double thick.
lower the router bit until it couches the table .
slide the router sled around on the table looking for hollows,
lower the bit each time u find a lower hollow.
once you have ensured you have found the lowest point, lower the router bit 2mm further.
start on one end and make 1 full pass at a time, do the whole table.
I FOUND IT MUCH FASTER AND CLEANER TO MOVE THE SLED 1/2 THE THICKNESS OF THE BIT FORWARD EACH PASS.
When finished run your sander lightly over the top removing any fine lines left behind, but not too smooth as you need some roughness for gripping your wood or so the utube video says.
once sides strings were set level and the sled was made. the routing process took approx. 25 minutes.
needs to be solid enough not to bow when the entire weight of the router is in the center.
19mm 3/4" plywood base and sides. EACH router will need a different set up to allow for the different styles of routers.
route slot with large straight bit
glue and screw the box together making sure to test your router in the box before you glue it together, my router has strange knobs sticking out preventing me from having 2 high sides so i made the front edge double thick.
lower the router bit until it couches the table .
slide the router sled around on the table looking for hollows,
lower the bit each time u find a lower hollow.
once you have ensured you have found the lowest point, lower the router bit 2mm further.
start on one end and make 1 full pass at a time, do the whole table.
I FOUND IT MUCH FASTER AND CLEANER TO MOVE THE SLED 1/2 THE THICKNESS OF THE BIT FORWARD EACH PASS.
When finished run your sander lightly over the top removing any fine lines left behind, but not too smooth as you need some roughness for gripping your wood or so the utube video says.
once sides strings were set level and the sled was made. the routing process took approx. 25 minutes.
Step 32: Flat Top
results of routing your top.
very satisfied.
as you can see in the photo this end has not yet got a end cap.
very satisfied.
as you can see in the photo this end has not yet got a end cap.
Step 33: Dog Holes
using the router put a sham-fer around each hole.
nothing more than protecting the edges from wear and tear.
nothing more than protecting the edges from wear and tear.
Step 34: Underneeth Top Support Boards
3 support boards
90 x 45 mm x 540 mm
glue and screw into top so they align with the legs on the table when flipped back over.
plane and sand until the supports are level with the base of the top.
STEEL LOCATOR HOLES AND PINS.
300 in from the end of each of the support board and 22 .5 mm in from the edges is your pin drilling location.
I CANT STRESS THE NEED FOR ACCURACY HERE. IF YOUR MEASUREMENTS ARE OUT YOU WILL MISS ALIGN YOUR HOLES FOR YOUR BOX BASE.
Step 35: Box Cupboard Doors
cupboard doors with raised panels
measure the total width of the opening and subtract 2mm for the closing of both doors.
divide the cupboard size in half and u have your door size
same process with the height of your doors.
again personal choice will determine how thick you make your door frame and how wide or high to have your raised panel.
once you have settled on your design make a tongue and grove joint around the frame.
mark the inside edge of the door where the raised paneling will sit.
cut a grove around this entire edges.
raised paneling.
again reclaimed red gum gate posts are used.
follow the earlier process to making reclaimed timber usable
once glued up and cleaned up: cut the angle in the edges
the angle will depend on how thick your timber is and how much you want the raised panel to protrude.
what we need to be left with is a section for mortising around the outer edges of the raised panel and a slope from that point out towards the surface of the raised panel.
all raised paneling was done on the table saw.
slot the raised panel into the 4 edges of the door frame.
glue the frame to its self but DO NOT GLUE the raised panel to the door frame. seasonal movement.
check into the Centre and outer leg 2mm for the hinge.
securing the hinge to the door is straight forward, 2 playing cards under the door for height and lean in to the cupboard and screw the hinge to the inside of the door.
repeat for both doors ensuring your doors align at the top where is it most visible.
mine required 4 playing cards on the right hand side. errrr.
measure the total width of the opening and subtract 2mm for the closing of both doors.
divide the cupboard size in half and u have your door size
same process with the height of your doors.
again personal choice will determine how thick you make your door frame and how wide or high to have your raised panel.
once you have settled on your design make a tongue and grove joint around the frame.
mark the inside edge of the door where the raised paneling will sit.
cut a grove around this entire edges.
raised paneling.
again reclaimed red gum gate posts are used.
follow the earlier process to making reclaimed timber usable
once glued up and cleaned up: cut the angle in the edges
the angle will depend on how thick your timber is and how much you want the raised panel to protrude.
what we need to be left with is a section for mortising around the outer edges of the raised panel and a slope from that point out towards the surface of the raised panel.
all raised paneling was done on the table saw.
slot the raised panel into the 4 edges of the door frame.
glue the frame to its self but DO NOT GLUE the raised panel to the door frame. seasonal movement.
check into the Centre and outer leg 2mm for the hinge.
securing the hinge to the door is straight forward, 2 playing cards under the door for height and lean in to the cupboard and screw the hinge to the inside of the door.
repeat for both doors ensuring your doors align at the top where is it most visible.
mine required 4 playing cards on the right hand side. errrr.
Step 36: Finishing
unknown
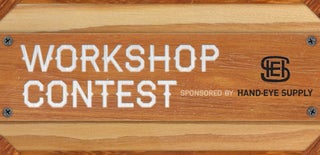
Participated in the
Workshop Contest