Introduction: Wallace the Animatronic Alien Creature
Welcome!
Today I will be showing you how to build Wallace, an animatronic alien creature.
To get started, you will need:
x 1 Fur Real Friends dog (like this: https://www.ebay.com/p/1903566719)
x 5 MG996R Servos
x 1 Pololu Maestro 6-Channel Servo Controller
x 1 20mm Half round realistic eye
x 2 Big Boxes (the total height, length, & width of the 2 combined boxes should be greater than 12"/1 ft.
x 1 Small Box for the creature to sit on and store the electrical components in.
A Hot Glue Gun
A Strong Cardboard Corner/Cardboard Edge Protector
A 6V Power Supply (preferably high in amperage, at least 20A)
Some Springs(I used 2 long springs from an assorted pack which I acquired from Princess Auto)
Some Air Craft/Steel Cable (You could use fishing line or thin rope, but I prefer Steel Cable as it is stronger and more reliable).
Some Aluminium Swag Sleeves for the Steel Cable.
Some 3D Printed Parts from my Thingiverse Page
Some Bolts and Screws
Step 1: Getting Started
First you will need the fur from the toy dog. Carefully remove the fur from the animal, starting from the underside/belly. You should notice Velcro holding it together. Open the Velcro and fell for little plastic hooks that hold the fur to the body. Carefully remove the plastic hooks off (these hooks are located all over the body but mostly in the joints. Be sure not to rip the fur). and then remove the fur from the body (The fur is securly attached to the eyes, so you may have to rip that part off and you will be left with 2 eye holes in the fur (Don't worry as you can glue the holes/gaps shut, stick the ears inside them, or cover them with the ears).
Once you have successfully extract the fur from the toy dog, you can either keep its body or throw it out.
Now take the 3D printed eyeball and cut a portion of it off such that the 20mm half round eye can fit inside it. Then glue the 20mm eye to the 3D printed eyeball, and insert the eye into the mouth of the creature's fur. Once you have the eye at the position you desire glue the fur to the 3D printed portion of the eye, leaving the 20mm eye exposed (Refer to the image above).
Step 2: Creating the Joints/Arms
Take your 3D printed parts (these 3D printed parts were form a movable hand, but the finger parts worked really well as joints for this animatronic) and search for the long Finger set piece and the Knuckle (I refer to it as an L-bracket).
Now, take the 2 pieces and add a 12-24 bolt through them and weld them together.
(Refer to the images above)
Step 3: Creating the Joints/Arms Part 2
Now, attach another L-bracket on top of the current mechanism to act as a guide for the cable.
Once you have done that, I highly recommend you add a spring across the mechanism so it can easily return to its home position, and help you avoid further complications. I used 2 servo screws to hold my spring in place.
Now, take a long cable (It's better to have it too long than too short. We can always cut off the extra length afterwards, but it's a lot harder to add extra length afterwards) and feed it through the joint mechanism, add your stopper to the end of the cable, and crimp it. If you look closely at the images you should be able to see my aluminium swag sleeve (my cable stopper) crimped, and hiding inside the long 3D printed finger part. You should also notice that my servo screw is also holding it in place.
(Refer to the images above)
Step 4: Creating the Joints/Arms Part 3
Attach another L-bracket to the L-bracket on the joint mechanism, to allow for a bigger surface area to bolt the servo horn to.
Repeat the previous steps to create the other arm. But this time, attach you servo horn vertically (facing up) so the joint can move left and right, not up and down like the previous servo. You will have to add another L-bracket to the mechanism so you can bolt the servo horn to the joint. (refer to the image that says: "set this servo to 0 degrees")
Now, we have a servo that moves one arm up and down, and another servo that moves another arm left and right. Also when we pull the cables, the joint should move from 90 degrees to 180/0 degrees. This will be our bicep, and the 2 servos we just added will be our shoulders/arms.
For the right arm (the servo that moves left and right) set that it to 0 degrees.
For the left arm (the servo that moves up and down) set it to 180 degrees.
Step 5: Creating the Joints/Arms Part 4
Now, take your cardboard corner, and attach the servos to it, in a 90 degree fashion with the joints facing down.
For the servo that moves left to right, cut a slot in the cardboard so there are no restrictions.
Now, I cut the cardboard corner to a short length (up to the slot that I made) so it could fit inside the body/fur.
(In the images on the next step you will get a better idea of how short my cardboard corner is)
(Refer to the images above)
Step 6: Creating the Head Joint
Now, take a long finger part and bolt your servo horn to it. Before attaching you servo horn to the servo set your servo to 90 degrees.
Then, glue the head servo on top of the 2 arm servos at a 45 degree angle.
After that, insert the cardboard bracket with all the servos inside the body/fur and place the arm joints in the fur's arms slot, and the head joint in the head area of the fur.
Now, glue the 3D printed head joint/piece to the back of the head (I used the eye holes to get my hot glue gun in there and help me attach the piece to the back of the head).
(Refer to the images above)
Step 7: Moving the Cables
Take, your small box and cut out 2 slots for 2 servos to fit in. Insert the servos into the slots and hot glue them in place.
If you're referring to the images above, you'll see an image that says "Set both servos to 0 degrees" This may work if you don't have your cables criss crossed (this may take some trail and error for you to get it just right). In my case, I decided to criss cross my cables (left arm cable went to right servo, & right arm cable went to left servo) because they worked better for me, movement wise. If you decide to criss cross your cables because they work better or you then you will have to set one servo to 0 degrees and one servo to 180 degrees) For me L-bicep (Right cable servo) was set to 180 degrees and R-bicep (Left cable servo) was set to 0 degrees (You can refer to my Pololu setting in the image above).
Now, take some 3D printed L-brackets and attach them to the servo horn. If you refer to the images above, you will notice only one servo screw is used to bolt the L-bracket to the servo horn. This allows the L-bracket to pivot and helps with the pull down and the pull up of the cable. You'll also notice a 12-24 bolt joining 2 L-brackets. those L-brackets are welded in place so they do not pivot at the bolt. The bolt is there to act as an aligner and as a backup in case the weld of the 2 brackets broke. The nut is also glued to the bolt so it doesn't come lose.
Lastly, feed your cable through the small hole in the L-bracket and crimp an aluminium swag sleeve to the end of the cable so it doesn't slide out.
Do some testing to ensure the cables get pulled and released properly. When the cable is pulled the bicep should extend to 180/0 degrees, and when it is released the bicep should return back to 90 degrees.
Step 8: Finishing It Up
Now, hot glue the base/butt of the creature to the lid of the small box and take a small metal L-bracket and bolt the cardboard corner to the box lid. This will ensure your creature sits up and doesn't fly backwards when the cables get pulled.
Remember to have the servos in the box facing the back and your creature facing the front (the audience)
Now you can create a routine for your creature using the Pololu Maestro control board.
I decided to created a containment unit for my creature, Wallace. To do this take 2 big boxes and put them on top of each other. To secure the boxes together I used some small 6-32 wood screws to bolt the boxes together. To create a cover so no one sees the base or what's under your creature, you must cut the big box's lid to create a U-shape that fits around your creature's small box/base. Put you creature inside the big box and put the U-shaped lid inside the big box as well. This creates a platform and prevents anyone from seeing what's underneath the platform (which would be you're creature's base and any other electronic comments you decide to add). I painted my platform green to resemble grass and I bolted my platform to the small box/base to ensure that it doesn't move.
I painted the backside, left side, right side, and the top (well it's actually the bottom of the box but it's the top of the enclosure) of the boxes a silver color, leaving the front exposed/clear so we can see him.
(Refer to the images above)
Enjoy your new animatronic creature and be sure to stay tuned for more projects.
Step 9: The Code
Here is my code that I have used for the routine in this video.
I have included my Arduino code and my MP3 sound file for this specific routine. I have also added the code and complied code (Copy and paste the Maestro code into your empty script on the Pololu controller and use my complied code to check to make sure that your complied code is the same as my complied code) from my routine created on the Pololu Maestro.
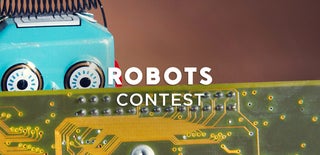
Runner Up in the
Robots Contest