Introduction: Walnut Box With Aluminum Splines
https://www.youtube.com/watch?v=98m3kiga3Aw
This project started out as a passing thought... "I wonder if I could get some nice hardwood scraps on Craigslist?"
I had never done any work with Walnut or Maple hardwoods, and wanted to try them out. After a quick search I found a local guy who makes custom wood frames who was selling off some of his scraps. For $5 I got a bucket of scrap walnut and maple, and got to thinking.
I really like small box projects, as they can employ a wide variety of techniques and skills, and have lots of potential for a creative and interesting piece. I had also been working with aluminum lately, and thought that it could make a nice accent to a wood box. Why not aluminum splines? Since I had never seen it before, I set out to do it myself.
Watch the video, and/or read on to see how it was done!
Step 1: Making the Side Material
For the sides of my box, I wanted a mostly-walnut piece, with a white maple stripe through it. This actually served double-duty for a different fridge-magnet project here: https://www.instructables.com/id/Custom-Wood-Aluminum-Magnets-From-a-Hard-Drive/
I took three strips of wood (two walnut and one maple), and glued-up the flat sides together in the striped pattern I wanted.
Once dry, I clamped the strip into an edge-jointing table saw sled and cut the faces down smooth, the turned the panel down flat on the table saw and cut the edges straight.
The blank was about 1/2" thick, and I wanted something thinner for my box. The panel was re-sawed into two thinner panels, and then sanded down smooth on my belt sander. A planer would certainly have done a better job than my sander, but I like the challenge (and the cost savings) of using what I have.
Step 2: Cutting the Side Pieces
Using my table saw cross-cut sled, I cut the long striped blanks down into shorter pieces which will become the sides of the box.
The sides will be joined together with 45-degree miter cuts. Originally I tried running them through my table saw, but I had trouble keeping them square without a 45-degree sled. So instead I moved to my miter saw and cut the 45's on each piece, using a stop-block setup to keep the size of the sides consistent. However, somehow my box ended up a little rectangular... but it still looks cool.
Step 3: Gluing the Sides Together
Having watched enough box-making on YouTube, I've learned that a good way to get your miter cuts glued up is to use blue painters tape on the outside of the joints to keep them together.
I laid out the sides on the workbench, added tape to the outside of each joint, added some wood glue, and folded up (and taped) the box. It was then clamped and set aside to dry.
Step 4: Adding the Top and Bottom
Once the sides are dry, sand down the top and bottom to ensure a nice smooth surface for gluing. Placing the sandpaper down on a flat surface is the best way to get a smooth surface on your work piece.
The top and bottom pieces were also sanded flat, glued on the top and bottom, and clamped to dry.
Step 5: Trimming Top & Bottom
Using a flush-trim bit on the router, cut off the edges of the top and bottom pieces to make them flush with the sides.
Step 6: Cutting Splines
For this step you'll need a spline-cutting jig. There are many different kinds that you can buy or build. In my case I made one that rides on top of my edge-jointing sled. It holds the box at a 45-degree angle so you can cut slots through the corners for splines. The splines add strength to the corner joints. Just don't cut the slots all the way through to the inside of the box; they should only be visible on the outside.
Step 7: Making Aluminum Splines
After cutting slots for the splines, I measured the width of the slots cut by my table saw. They were about 0.100" wide.
Using some 1/8" aluminum bar I had on-hand, I took it to the belt sander to make it thinner. This takes a while, and the aluminum can get quite hot. For this reason I used a piece of scrap wood to hold the aluminum down on the sander to keep my hands from getting burned.
Once you have the aluminum down to the proper thickness, cut it into small triangles that will be used for the splines.
Once I had my triangle spline pieces, I drilled a small hole in each one where they would be inserted into the box. I wasn't sure if the dissimilar materials would have problems bonding, so I did this as a way to add some extra strength to the joint, by adding some more space for the epoxy.
Step 8: Inserting the Aluminum Splines
Using a basic 5-minute epoxy, glue the splines into each slot. Don;t worry about any squeeze-out on the box, this will get sanded off later.
Once dry, the excess aluminum can be cut off with the band saw. The remaining aluminum was then sanded down rough with the belt sander, and then smoother with 220 grit on the palm sander.
Step 9: Cutting Off the Lid
Up until this point, we had one solid sealed box. This way, we can ensure the lid and the box are a perfect match.
I placed the box in my table saw cross-cut sled, and used a stop block to locate the box. I then cut each side to remove the lid from the box. The box and lid were then sanded flat to remove any saw marks.
Step 10: Making the Inside Liner
To add another interesting element to the box, I added a small inside liner to help align the lid.
The liner is made up of four thin pieces of maple. For accuracy, I measured each side of the box (they were a bit different), and then cut my liner pieces to length. Each liner piece is the width of the inside of the box, minus the thickness of the liner material. This will be more obvious in the photos coming up, where the pieces are glued in place.
Step 11: Adding the Liner Bottom and Sides
For an added visual accent, I placed a small sheet of aluminum in the bottom of the box, and glued it down with super glue (also known as cyanoacrylate or "CA" glue). Besides looking good, this bottom piece also hides my glue squeeze-out in the bottom of the box from when I glued on the bottom panel. The edges of the aluminum will be hidden by the sides of the liner.
The side pieces were glued in with CA glue as well (a thicker viscosity of glue), and the gaps between the side pieces were reinforced by adding some thinner CA glue, which gets "wicked" into the small gaps.
Once dry, the exposed part of the liner is too big to allow the lid to fit on the box. This was sanded down with a sanding block until it was small enough to allow the lid to fit.
Step 12: Finishing
I finished my box with a few coats of spray lacquer. It's easy to apply and really makes the colors stand out.
Follow the directions on the can and use in a well-ventilated area.
Step 13: Done!
See the video here:
This was a really fun project... I got to try a lot of new things, and the end result came out great. Thanks for reading (and watching).
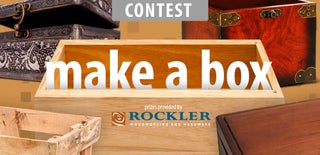
Second Prize in the
Make a Box Contest
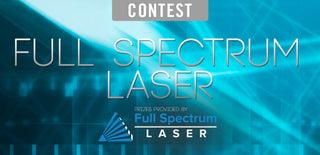
Participated in the
Full Spectrum Laser Contest 2016