Introduction: Micarta Like You've Never Seen Before, in a Rainbow Themed Cheese Board.
Ok, here we go! This is my chance to show an idea that I have had for a while now. To my knowledge, this has never been done before. I have used this method before in much smaller scale but I wanted to do something larger to really show off the technique. It is a messy process but the outcome is so worth it. Micarta is actually a brand name for the prosses of layering paper or fabrics with resin, then pressure and heat are added to create a number of different things. Its main use is in high strength electrical insulations, but it is mostly known today for being used as knife scales. The prosses I and all other DIY makers, does not involve the extreme pressure or heat that is used in true Micarta, but it is widely known as micarta. What I do differently is instead of layering the paper or fabric into a rectangle mold I am using the wood as a mold to shape it. The inspiration for this project is my twin brother. He has been after me for a while to make him a cheese board and recently he got a tattoo of a purple ribbon to signify his battle and beating testicular cancer. I had been thinking of what I was going to do for the contest and when I saw his tattoo, it hit me. I thought of all the colored ribbons that represent the many battles with cancer. So, this is for you Trevor, I love you.
Supplies
Wood, of your choice -I chose walnut
Quality Paper and color of your choice- I chose the base colors of the rainbow that also represent colors of cancer ribbons. The color for testicular cancer is orchid.
Wood glue
Resin, preferably slow curing- I used East Coast slow curing resin.
Colorant for resin- I used Apple Barrel acrylic paint
cups for mixing the resin
A mixing utensil - I used a popsicle stick
Food grade mineral oil with beeswax.
Double Sided Tape,
Tools
Tape measure
Ruler
Resin resistant mat
Gloves
Safety goggles
Respirator
Bandsaw/Jigsaw
CNC machine with a 1/8 shank, 2mm ball nose 2 flute bit- I used an X-carve
Belt Sander/Palm sander or a Benchtop Planer
Tablesaw
Router or a Router table with a small chamfer bit
Step 1: Be Creative.
My first step was to rough cut the shape that I wanted and sketch up a design. I used a 1-inch thick 13in piece of Walnut. I love the richness of the wood. I got it from a local mill where I live. You could find a piece at a Woodcrafters if it is available. You can use any wood and any thickness. I sketched up a design just for placement.
Step 2: Creating and Cutting the Ribbon
For this project, I wanted to use resin to make the ribbon for testicular cancer. To do this I drew the ribbon I wanted and took a picture with my phone so I could load it into Easel to cut it with my X-carve CNC.
I drew a ribbon by hand and took a picture of it with my phone, I was then able to load it into Easel, I used a 1/8 shank, 2mm ball nose 2 flute bit to cut it.
Step 3: Cutting the Paper for the Rainbow
I used a small paper cutter, which was a huge time saver.
The width of the paper depends on the thickness of the board. I always cut the paper a little thicker, it is more work but it turns out better.
The length depends on the length of the board and the shape of the cut you make in the board. The sharper or wavier the curve, the longer the paper needs to be.
- Measure the curve first to get an idea of the length you need for your paper. Nothing worse than cutting all of that paper and finding it was never long enough, to begin with
- .For my rainbow, I was able to use 11" long paper that I cut into just over 1" wide strips. The excess paper left sticking out will be sanded off later. Better to have extra to sand than gaps when it is finished.
Step 4: Cutting the Board for the Micarta Rainbow
This step is cutting the gap for the micarta.
Before you cut the board you must determine the thickness you want the gap for micarta., Once you decide the thickness of the micarta you want, stack the paper and measure it. The measurement you get is the width the gap needs to be.
- In picture 1 I am cutting the first line, It is marked in red.
- .In picture 1 The black line just under the red line is the second line that needs to be cut.
- If you do not cut a strip out of the board the paper will shift the two pieces of wood apart from each other, this is seen in the 3rd picture.
Step 5: Glue the First Two Down
I made this a step by itself because it is important. Before you start the micarta step, you need to glue the first two strips of paper down to the wood.
The strip you start with and the last one. This can be seen in the two pictures The bottom board will get the red strip of paper and the light purple on the top.
This will ensure that the micarta will stick to the wood properly.
Wait for the recommended drying time before moving on to the next step.
Step 6: Making Micarta
Make sure everything is ready to go before starting.
- Wear gloves.
- use a resin resistant mat. I use scrap pieces of a plastic sign board.
Stage your paper in a way that you can pick up one at a time. It will help when both of your gloves are covered in resin.
If possible, use a resin that has a slow curing time. Mine has a pot life of 30 minutes and I was able to do 70 strips of paper with time left on the clock.
Layering your micarta:
- Begin by evenly spreading resin on your first strip. This is the strip that you glued down on the bottom piece of wood. As seen in picture number 2
- Add the next strip of paper down onto the resin-covered strip. Cover this strip with resin evenly from end to end as you did the first strip. Repeat this for each strip of paper. As seen in pictures 3 and 4.
- As the resin builds up, it will begin to run onto your work surface. Once this happens, I found it easier to dip my strips of paper into the excess resin to coat them before placing them down. I still coat each paper strip with resin as I did with the first strips.
- Continue these steps for each piece of paper. MAKE SURE to coat each piece thoroughly with resin.
As you stack paper layers, you will notice your paper will start slipping out of place. Simply place your fingers on either side of the stack and gently push inward. This will force the strips to slide back into place.
Clamping the workpiece:
Once all of your paper and resin has been placed lay the stack down to meet up with the top portion of your workpiece (pic #5).
- Press the outer edges of your micarta strips inward while simultaneously pushing up into your top portion.
- Place your clamps loosely around your workpiece.
- Slowly apply pressure with clamps rotating back and forth between each clamp to apply even pressure. Note: As you apply pressure, resin coated paper will begin to slide outward. Simply push it gently back down in line with the workpiece. You may have to hold the paper in line with one hand while tightening your clamps with the other.
Once it is clamped, you may see the paper still trying to push out. If this happens, apply pressure to hold it in until you feel the resin start to hold. Allow to completely set and cure before moving on.
Step 7: Shape It Up!
Your workpiece is completely set and cured by this step.
You will find the paper is sticking up proud from the board. This will need to be removed. This can be completed by using a few different tools. Here are a couple of examples that can be used:
- A thickness planer or hand plane
- A bench sander, belt sander, or palm sander
- A wood chisel
I used a bench top belt sander to remove the excess paper and resin from the workpiece. The purpose of this step is not to make smooth, but to make even.
Once this has been completed, it is time to square up and finish the overall shape of the workpiece.
Using a square, mark the piece in order to cut into shape. This step will also take care of any off-shape pieces that misaligned due to the insertion of the paper. Use this step to also adjust the shape in relation to your handle if it is off-centered.
Step 8: Filling the Ribbon
Before you begin filling the ribbon, make sure to test colors to match the paper used in the rainbow. I was able to purchase a paint color to match the orchid ribbon for testicular cancer. If you cannot find a color close enough, you may have to mix up a color of your own. Besides paint, there is a number of dyes and powders that can be used as well.
Mix a batch of resin to the manufacturer's directions. Once mixed, mix in your color.
Note: . I used 2 ounces for the rainbow and about 1 1/2 for the ribbon. Each project will be different and you will have to adjust to your own needs.
Slowly pour the resin into the cutout. Make sure to fill it high enough so it is proud of the board. This will save you in sanding later and will ensure that there is an even level of resin throughout the cutout.
Step 9: Embellishments (optional)
Once the resin in the ribbon is set and cured, it is time to consider embellishments. These steps are not necessary, but make your piece look more professional and finished.
Drilling the handle:
- Measure the width of the handle and find the center from both sides and from the top. Mark the center. The size of the hole is up to you. Just make sure to not go too big as to compromise the strength of the handle end.
- Clamp your workpiece down to the work surface. Make sure to use a sacrificial board under your handle to prevent tear out.
- Using a drill or drill press line the center of your bit to the center mark on the handle. Drill your hole.
Routing the edge:
After clamping your workpiece down rout the edge on the front and back as well as the hole in the handle using a handheld router to get your desired finish. You could also use a router table as well.
I used a hand router with a slight chamfer bit for a minimalist look.
Step 10: Finish Sanding
Using a palm sander, I moved through multiple grits of paper from 80-220 grit to achieve the desired smoothness of the piece. Take your time. The effort is worth the result.
Make sure to sand in the hole on the handle and around the chamfered edge. Using hand sanding instead of the palm sander around the chamfered edge will reduce the possibility of over sanding the edge.
Step 11: Applying Food Safe Finish
Prepare your workspace with a towel or paper.
Using a clean, lint-free rag and a food-safe finish, cover the entire workpiece front and back. Make sure not to miss the edges and the hole in the handle. Work the finish into the grain of the wood. Follow the manufacturer's directions for applying the finish.
I used "Howard Butcher Block Conditioner", which is a food-grade mineral oil and wax all in one.
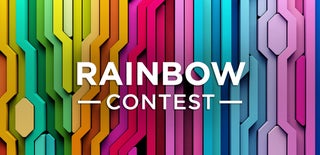
Participated in the
Colors of the Rainbow Contest