Introduction: ☠WEEDINATOR☠ Part 3: Chassis Build
Winter is the perfect time to be building machinery, particularly when welding and plasma cutting is involved as both provide a fair amount of warmth. If you're wondering what a plasma cutter is, then read on for in depth procedures.
If you've been following the progress of the Weedinator, stage one showed the drive / steering / suspension mechanism and since then I've dumped the suspension system for a more simple version found on my International 454 tractor. In this system, the back wheels remain fixed to the chassis whilst the front wheels swivel on one single axle. This system lends itself to having the steering linked with a tie rod which can be used to remove backlash in the gearbox and balance out forces created by acceleration, friction or braking on the wheels themselves.
Will the steering system work with the wheels being driven / braked? I think it will come down to the torque ratio of the respective systems in that the steering has to be sufficiently forceful to cope with transmission forces. Sounds complicated? Results will be obtained when the Weedinator is rolled out of the workshop door and tested in early 2018.
Step 1: Tools and Components
- Levelling table / surface plate
- MIG welder
- Plasma cutter
- Clamps
- Half round coarse 12" file
- 100 x 100 x 4mm box section
- 200 x 100 x 5mm box section
- Magnetic Broaching drilling machine
- 40mm broach drill
- 60mm broach drill
- 6 x 617082RS Thin Section Deep Groove Ball Bearing 40x50x6mm (61708-2RS-EU)
- Stub axles for 4" 12mm wheel PCD .... 2 of
- Spirit level
Step 2: Using the Surface Plate
The central part of the chassis, which is also going to be the CNC machine, is laid out on an extremely flat surface plate so that the pieces of box section can be positioned as accurately as possible, enabling the CNC components to run nice and smoothly. The pieces are welded up on the table taking great care not to get hot splatter on the table itself, which would ruin it.
The box section itself needs to be cut with an accuracy of about 0.2 mm and I chose the best steel supplier in my location with a saw that used automated feed to get an accuracy to 0.1 mm. Other steel suppliers cut to +- 5mm which is useless!
The sections are checked for squareness to each other and carefully tacked together in diagonal sequences to avoid distortion.
At this stage the construction seems to be wildly heavy and very much over engineered, but in the later stages the plasma cutter is going to be used to remove as much mass from the structure as possible.
Step 3: Buidling the Swivelling Front Axle
The front drive units are positioned relative to the main chassis and wooden blocks are used to level it up. This enables the front axle to be measured. It is then drilled each side with a diameter 60mm hole in it's centre using a broaching drill. The 600 mm long box is drilled diameter 40mm.
The small 100 x 100 box sub frame is welded onto the main chassis, getting it as level and square as possible and the suspension tube is inserted and welded into the 60 mm holes.
The low profile 50 mm bearings are inserted into the tube and the shaft is carefully positioned and welded in.
The 970mm axle box section is then welded to each of the drive units in turn.
Step 4: Building the Back Axle Assembly
The back axle is a temporary fixture to enable testing of the main front drive units. The dimensions of the 100 x 100 mm box sections used are given by setting the rest of the chassis level and making measurements.
Step 5: Making Oval Slots in 100 X 100 Box
The box sections used in the chassis are far too heavy and so weight needs to be removed using the plasma cutter.
A template is made in 2mm steel and clamped to the box section wherever a hole is required. Before cutting begins, a small hole is drilled into the bit of steel to be removed which allows the cutting 'flame' to be initiated without having to blast through solid steel, which will very quickly destroy the nozzle. The plasma flame works much better by cutting sideways into steel.
A lot of practice is needed to get a clean cut, which starts at the drilled hole. The torch is held very firmly and is slowly dragged backwards against the side of the template. Never push the torch forwards or sideways! Sometimes the template has to be repaired with a file to ensure a smooth surface.
If done well, with a nozzle in good condition, the metal to be removed should just fall out and all the lines should be nice and clean, otherwise there will be a lot of very tedious work required to clean it all up. The slag created is simply knocked off with a hammer and the final surface filed with a coarse half round file. No grinding should be necessary!
Step 6: Slotting Out the 200 X 100 Box
The 200 x 100 box is incredibly heavy, but is needed for ease of fabrication on the surface plate. It's much easier to remove the unnecessary material with the plasma cutter than try and build up complicated structures. Eventually we end up with a frame that has an attractive 'aerospace' design.
Rather than create a template I used some large washers that were about the right size. It's very satisfying to remove the large 'tongue' of steel with nice clean cuts although by this time the plasma nozzle was beginning to deteriate.
By the time I had finished that day I'd managed to remove 17 kg of material.
Step 7: Finished Chassis
The chassis is finished and the drive / steering mechanism can be tested - just waiting for another pair of wheels to arrive.
Step 8: Next Stages
After thoroughly testing the drive units / steering modules, the CNC components can then be attached to the main central frame. The first video shows the maiden voyage of the Weedinator and the second a 3 point turn.
☠
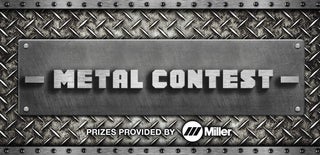
Runner Up in the
Metal Contest 2017
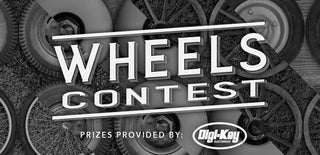
Participated in the
Wheels Contest 2017
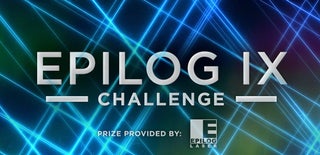
Participated in the
Epilog Challenge 9