Introduction: Weekend Handmade Puzzle Box
I am going to open my first instructable, with a spoiler. Who wants to read through a whole puzzle box build, only to find out that the actual puzzle is boring. So I am going to show you the steps to opening the box. Then if you are interested in building this pretty box with or without power tools, please read on!
I built this with hand tools for fun and also for a little challenge. It also hopefully illustrates, that you can build without a huge investment in tools. Most of the woods that I used are scrap, odd size pieces I bought from lumber yard discount bins to use as inlays and such. The top is Leopard wood, the sides are Tigerwood, the ends are Ambrosia Maple, the knob and dowel pins are Ipe. (None of these woods are listed on the CITES Appendices. )
Step 1: Lock Number One
Step 2: Lock Number Two
The front side of the pin can be seen but not pulled out of the box...with your finger. It requires a key.
Step 3: Lock Number Two: the Key
Both pins are removed and the knob (key) is returned to the top of the box.
Step 4: The Last Lock
Yeah it looks easy, but would you figure it out? So far best time I have seen so far is well over an hour.
Step 5: Sketching Out a Rough Plan
Step 6: Hand Built
You don't need the most expensive planes to do this, especially something this small. What you need is to make sure they are TUNED and SHARP. (Two things that can be done cheaply even with some wet dry sand paper taped/glued to a piece of glass.) The other trick is to take your time.
Step 7: Join the Gang
Remember just plane your end grain first. As you plane the end grain you will most likely experience chip-out, on your side grain. Fix this by planning the side grain last.
Step 8: Dowels and Pins
I used a simple and cheap plug cutter to make the dowels out of the Ipe. Then I drilled the larger holes for the locking pins and installed the false permanent pin and magnet on the inside. Glue up with a good quality wood glue, let dry and using a simple flush cut saw to level the dowels. DO NOT GLUE IN THE BOTTOM YET!
Step 9: Lid and Bottom
I then epoxied the nut into the hole I had created in the underside of the lid. This allows a more secure seating for the knob to be constantly screwed in and removed rather than just threading the wood. The bottom I don't want flush to the sides of the box, because I want to facilitate the spinning of the box to enable the nails to unlock. So I began planning and sanding the bottom piece so I had a very gentle curve. I didn't want the box to rock like a boat but I did want to reduce the friction for spinning the box by reducing the area of the bottom.
Step 10: Making the Knob...
Step 11: The Locking Pins
The second pin was easy to build, while shaping the first pin, I just made it a little longer than necessary and cut off a piece before finishing the ends. This is what shows on the outside of the box, the remaining shaft of the pin is made out of the remainder of the maple from the ends of the box. I did this because Ipe is tough and hard but is prone to cracking and splitting when it gets thin.
I drilled a hole through the Ipe end piece for the machine screw to fit through and reach the machine nut glued into the maple. On the back side of the pin, to make it stick to the magnet (duh, I know) I just drilled a hole and interested a cut off nail head with epoxy. The important thing is that you have a magnet strong enough that the pin can't be shaken out of the box and the pin is too short to be gripped and pulled out of the box without using the key. (knob)
Step 12: Centrifugal Nail Lock (Not a Bad Band Name)
The easiest way to lineup and glue the nail holders is to put the lid in place, flip the box over and work from the bottom. This way you know everything is flush with the lid. One important thing to note is the length of the nails. Depending on what dimension you would like to make the box the nails need to be short enough that when in the locked position, will not hit the pin on the far side. Also, the nails need to be long enough that when the box is spun they will stop before falling out of the piece that holds them in the box. Otherwise you will not be able to reset the lock without doing some type of ship in a bottle building magic. (Or don't glue in the bottom.)
Test it a few times and you should be able to safely glue in the bottom.
Step 13: Finish and Notes
Thanks everybody. I hope you found this interesting and understandable.
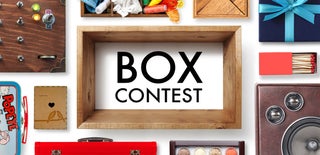
Participated in the
Box Contest 2017
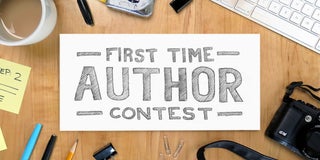
Participated in the
First Time Author Contest