Introduction: When Words Fail--3d Print 'em
8 Nov 2016 has been a pretty memorable day. It's not often that 58 million of your fellow citizens can disappoint you all at once. Having shared my astonishment on Twitter, I felt like I needed to sum up my feelings in a fashion that I could avoid having to rehash details, but really got to the core of how I was feeling.
A plaque seemed like a great idea. At the office tomorrow, when a co-worker might approach me with a 'hot take' on the previous results or even a measure of gloating from a sub-set of my colleagues (to protect their identity, I will just call them "D'Plorable"), I could wordlessly shake my head and point to my new sign.
Hence, the WTF plaque was conceived. Let's just agree that WTF stands for What The Fromage.
Even if you aren't experiencing an existential crisis, I'm showing you a way to use Fusion360 to create a 3D printed sign. Now my printer has a pretty small print bed and a few letters work just fine within the space that I had available. Conceivably, you could reduce the size of the letters and get a bit more chatty, but I should think that less is more.
Step 1: Starts With a Sketch
Having just participated in an Instructable course/webcast on 3D printing, I started a new design in Fusion 360. Autodesk allows students, hobbyists, and SMBs to use the program for free as long as you make less than $100k a year (http://www.autodesk.com/products/fusion-360/try-bu...
That is a great deal. I had been using 123D Design, another Autodesk product, so many of the concepts transfer over.
At this point I need to confess that while I was trying to figure out a portion of the build that just wasn't working, I deleted my original sketches. I've tried to recreate them as much as possible, but there may be some minor differences.
I created an ellipse in a sketch. I chose dimensions based on my print bed, so your setup may need to be adjusted to reflect your printer.
I didn't want to make the sign very thick, but I added a raised edge to the oval to give the model more stability and reduce the likelihood of the print warping away from the print bed. I used the offset tool to create a border of couple millimeters.
Step 2: Create the Base
I extruded the thin border that I just created 2mm and that created a raised ring.
That completed, I selected the center portion of the oval and extruded it just 1.5mm. This completed the base.
Step 3: W Then F Then T(ish)
From the sketch options, I selected 'text' and positioned a 'W' on the face of the plaque. To fit into the oval of the plaque, I set the char height to about 50 and found a font that seemed like it would make an interesting statement (the font is called chalkbuster).
The next pictures document generating the letters. If you are wondering why I did the letters one at a time, apparently the 'T' causes Fusion to throw a 'tool error'. Something like that at least. Not very helpful. After I had tried to do 'WTF' several different ways, I finally figured out that it was the 'T' that was causing the error.
Perhaps the sketch for the 'T' doesn't create a closed loop? Someone will probably clear it up in the comments.
Anyways, I made my own 'T' from the '|' and '_' symbols. I had to scale them a bit so the kerning worked out.
I extruded the letters 3mm. I wanted them to stand out, but I could have probably saved time in the print cycle if I had chosen something smaller
Step 4: Use Cura to Generate the G-code
With my model complete, I used Fusion 360 to export the plaque as an STL and then imported that into Cura.
Cura is the official slicer for the Lulzbot Mini that I'm using. There is no good reason why I have the layer height set to .15 mm. It is the setting that I have been using for my other project (planetary gear using herringbone gear profile) but I would have carved an hour off the print time if I had gone with .4 mm.
Cura does a fine job of generating g-code for the 3d printer. I have experimented with Slic3r because it gives more control over perimeter overlap, voids and infill, but I haven't got the recipe right to equal what can get from Cura.
Step 5: Printing With Octoprint
With the g-code compiled, I only had to upload the completed file to the Octoprint server and wait twice as long as necessary for the job to print. I'm using ABS here because that is what I had on the roll.
I wanted to get the text to stand out, but I rushed the finish a bit and just grabbed a Sharpie to color in a background. You don't get the chalkboard feeling from the font but I might have been able to do a better job with something with a more precise tip than a permanent marker to get in around some of those details.
Attachments
Step 6: Epilogue
I'm happy to report that the WTF sign functioned as desired.
My boss walked by my door, saw the sign, pointed and raised an eyebrow. All I had to do was nod and grimace. He gave me the 'whatcha goin to do' shrug and our conversation was complete without having to say a word.
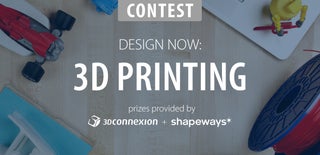
Participated in the
Design Now: 3D Design Contest 2016