Introduction: Wide Angle Reflex Finder for Amateur Astronomers
Amateur astronomers have widely adopted the use of a 1X magnification optical reflex device, known as a Telrad, to help locate deep sky objects. The Telrad projects a calibrated target reticle, focused at optical infinity onto the night sky. The Telrad is aligned with the axis of the telescope tube, and thus the center of the reticle indicates exactly where the scope is pointed. The Telrad is very useful for "star hopping", a technique used to help locate deep sky objects too dim to see with the naked eye relative to bright known stars. The Telrad's calibrated projected circles help to estimate angular distanced between known objects (i.e. stars) and the dim objects you're looking for (galaxies, nebula, globular clusters, planets, etc.). The projected circle diameters in a Telrad are 0.5 degrees, 2.0 degrees, and 4 degrees. I own two Telrads and have been using them for years.
A drawback of the Telrad is that the projected circle reticle provides a limited field of view target ring (4 degrees max), and although the projected reticle brightness is adjustable, it is sometimes hard to "look through" the reticle to see the reference object you're looking for. It can be either too bright, and obscure the objects you are using to find a very dim object, or the reticle is too dim and hard to use. Furthermore, the projected circles provide no angular reference relative to the sky.
The Wide Angle Reflex Finder (WARF-1X) includes some key improvements and updates compared with the venerable Telrad:
1. The angular field of regard of the projected reticle is increased from 4 degrees to 16 degrees enabling additional projected reference circles.
2. The projected reticle orientation can be adjusted to help navigate from reference stars to the final object along a diagonal. For example, one reticle axis can be aligned to the desired direction to aid in the manual slewing of the telescope;
3. The brightness of the projected reticle can not only be varied directly, but the improved design also enables an adjustable on-off-on duty cycle. Thus, combination of adjustable brightness and duty cycle improves the overall "transparency" of the projected targeting reticle.
4. The larger collimator lens is used in the WARF-1X enabling more of the reticle larger field of view to be seen without head movement.
A photograph of the as built 1X Wide Angle Reflex Finder ("WARF-1X) is shown, along with the 3D model of the unit (Fusion360).
Step 1: Wide Angle Reflex Finder Project Overview
This project combines optics, mechanical packaging and electronics:
1. Optics - The 1X Wide Angle Reflex Finder (WARF-1X) uses a 40 mm diameter collimating achromatic lens which provides more physical aperture compared with a standard Telrad (40 mm vs. 25 mm). A larger exit aperture enables the viewer more eye movement to view the projected reticle, and more of the field of view to be visible at one time.
2. The WARF-1X provides a 16-degree diameter projected reticle circle, up from the Telrad's 4 degrees. Thus, precise star-hopping over larger angular distances is possible.
3. A rotationally adjustable reticle assembly that enables the viewer to align the reticle axis with the movement axis of the telescope, thus enabling more accurate telescope slewing when star hopping.
4. An electronic circuit that enables the reticle brightness to be varied, but also enables the reticle image on-time duty cycle to be varied from about 2 seconds (on-off-on) to continuously on.
5. A compact 3D printed housing assembly.
Overview of Building the WARF-1X:
The following is an outline of the steps to build the reflex sight.;
1. 3D print all mechanical components. All files are downloadable.
2. Purchase optical, electrical, and mechanical components.
3. Assemble the major subassemblies.
4. Final assembly
5. Calibration
The images show the various components.
Step 2: 3D Print All Mechanical Parts
The WARF-1X was designed using Fusion 360 software. All non-purchased internal and housing components are 3D printed in PLA or other suitable materials. There are a total of 12 files representing 15 printed components, as follows:
1. Collimating lens housing (2 parts) - Black filament, no supports, 0.2 mm slice
2. Reticle housing (2 parts) - Black filament, no supports, 0.2 mm slice
3. Reticle - Black filament followed by white diffusion layer. Print the reticle detailed side down (on the build plate) per the orientation of the .stl file. Slice at 0.15 mm. At 0.65 mm, switch to white filament for the final layers. (Other semi-transparent materials could be used in place of the white filament.) The purpose of the white backing is to hold the reticle components together and to diffuse the LED illumination.
4. LED illuminator holder - White filament, no supports (grouped with item 5)
5. LED illuminator diffuser / reflector - White filament, no supports (grouped with item 4), 0.2 mm slice. The diffuser / reflector acts to improve the uniformity of reticle illumination from a single LED.
6. Fold mirror support bracket - Black filament, no supports, 0.2 mm slice.
7. Front Panel Fold Mirror Interface - Black filament, no supports, 0.2 mm slice.
8. Chassis - Left Side - Black filament, supports, 0.2 mm slice. Supports are minimal.
9. Chassis - Right Side - Black filament, supports, 0.2 mm slice. Supports are minimal.
10. Left side cover - Black filament, no supports, 0.2 mm slice.
11. Right side cover with nomenclature - No supports, 0.2 mm slice. (Optional) Print the cover with black filament for the first 2.6 mm thickness. Print the next two layers, starting at 2.8 mm, with white filament. Finally, finish the part with glow-in-the dark filament starting at layer 3.2. This combination enables the text to be clearly visible in the daylight and at night.
12. Two control knobs - Glow-in-the dark filament, no supports, 0.15 mm slice.
All of these components are available for download as .stl files.
The key components are #8 and #9 above. The housing was designed as a single unit, but was split along the center line with the slicer software. Three internal #4 screws are used to hold the two halves together. All components, except for #8 and #9 can be printed without supports with a nozzle diameter of 0.4 mm. If possible, the reticle should be printed with a 0.25 mm nozzle to improve the line definition. (The prototype reticle was printed with a 0.4 mm nozzle with acceptable results.) The .stl files indicates when to switch filaments. The right-side panel (with nomenclature) is printed with Black material, with two color changes (to white for the raised characters with a glow-in-the dark finish). Note that some supports (from build plate only) are needed only for the two chassis halves.
NOTE: 12/4/18 - I have uploaded modifications to the Left and Right Chassis stl files. I have changed the position of the mounting features to match up to the standard Telrad base.
Pictures of all the parts are shown in the figures.
Attachments
Step 3: Purchase Optical, Mechanical and Electrical Parts
Optical Parts
The WARF-1X uses 40 mm diameter collimating lens achromat (better quality, color corrected lens) with a 125 mm focal length from www.surplusshed.com . The cost is $8.00. (The surplusshed.com part number is C11832.) The collimating lens housing is printed in two halves (3D printed item #1). The surface of the lens with the more steeply curved radius should be placed away from the combiner and towards the fold mirror. (This alignment reduces the overall optical errors.)
The fold mirror between the achromatic collimator and the reticle can be a shaped front surface glass mirror (may be expensive), or as an alternative you can modify a standard plastic mirror. (Tap Plastic at www.tapplastics.com has plastic mirrors). Use the 3D printed fold mirror profiling template to transfer the shape and size onto the plastic mirror. (I cut an oversize mirror out with a band saw and finished it off with a disc sander.) Once the mirror is shaped, the painted protective coating must be removed. I soaked the plastic mirror in lacquer thinner, which is effective at dissolved away the painted backing coating but does not attack the acrylic substrate. After several soaking cycles and careful wiping, a usable front surface mirror. Note that if a front surface mirror is not used, a double image of the reticle will be seen.
Bond the mirror to the 3D printed mirror holder using a household kitchen caulk.
The "combiner" is profiled 1/8" thick acrylic using the 3D printed template. You might make several, and select the one with the lowest optical distortions.
Electrical Components
A schematic of the LED drive circuit is provided. The design uses a simple 555 timer to enable a variable frequency pulsed LED illuminator. As the LED draws very little current (low brightness), the 555 timer can drive the LED directly. All parts were purchased from Jameco Electronics (jameco.com). The parts list is attached.
Mechanical Parts
Several screws, nuts and springs are needed, as shown in the Parts List. These were purchased from McMaster-Carr (https://www.mcmaster.com).
Note that the compression springs enabling the angular adjustment of the fold mirror are made by cutting in half the spring in the Parts List. The 4-40 screws are threaded through the fold mirror support from the inside. Although the 3D model of the fold mirror support includes the 4-40 threaded holes, use a 4-40 tap to clear out the holes.
Step 4: Assemble Electronics
A schematic of the LED drive circuit is provided.
Note that most parts can be positioned on an 80 X 15 mm PCB Prototype Board. A standard 20 mm wide PCB is reduced to 15 mm in width to fit within the chassis next to the battery. A PCB prototype board set with an 80 X 20 mm prototype board is available from Amazon.
A socket is recommended for the 555 timer part, but is not necessary. The circuit components can be laid out like the schematic layout. The wire interfaces to the two potentiometers, LED, and battery can be pins or tie points. Making each solder point accessible will make the final wiring simpler and more reliable.
The brightness control potentiometer with push-pull on/off switch will be mounted to the side panel on the collimator end of the unit. The pulse-width control potentiometer is similarly mounted to the back end of the housing side panel in a later step.
The LED is pushed through the 5 mm hole in Item 4 in Step 1, the LED Illuminator Holder.
The 3 volt battery holder is mounted under the flanges on the main housing as shown in the picture.
The circuit board slides into two flanges on the right side of the chassis, as shown in the figures.
Note that the schematic has an error. The electrolytic capacitor should be 100 uf as shown in the parts list.
Update 9/2022 - I have developed a small printed circuit board for this project. This small board enables all the electronics (power switch / brightness pot, pulse width pot, battery holder, and circuit board) to be mounted to the side cover, except for the LED reticle illuminator. If you are interested in getting the Gerber files for the board, please let me know. You can purchase 5 boards on line for about $6.
Step 5: Final Assembly
The following is an outline of the final assembly process:
1. Screw the two main chassis halves together using the #4 thread cutting screws. There are three chassis attach locations.
2. Install the collimating lens mounted in its cell into the chassis from the front. It is a tight fit, but the cell should fit snugly into the chassis. Not glue is required. Note that the more highly curved surface should face downwards towards the fold mirror.
3. Install 3 4-40 screws into the Fold Mirror Support (3D printed item 6) from the inside. Slide springs over each of the screws, and thread them through the front panel fold mirror interface (3D printed item 7) and thread on the 4-40 knurled thumb screws. Install the assembly onto the main chassis using 4 #4 thread cutting screws.
4. Insert the LED into the hole in item 4, and slide the assembly into the chassis as shown in the figure. Make sure the LED is near the center of the chassis.
5. Insert the LED Diffuser / Reflector (3D printed item 5) into its slot. Use a small amount of glue to permanently attach the diffuser to the chassis. Glue on one side only so the chassis can be disassembled if needed.
6. Insert the reticle into the reticle holder. The reticle disc should turn easily in the housing. The housing could be glued, but it is not required.
7. Slide the reticle assembly into the chassis. Loosen the 3 screws holding the chassis together to make the reticle assembly insertion easier. The reticle surface should be towards the fold mirror.
8. Wire the circuit board to the pulse width control potentiometer. There is a gap in the chassis for wire routing.
9. Wire the circuit board to the brightness control potentiometer and on/off switch.
10. Wire the LED to the circuit board.
11. Wire the battery assembly to the circuit board. Install the battery holder into the chassis. Slots are provided.
12. At this point, turn power on and verify the LED brightness control potentiometer and pulse width control are working. This is the time to trouble-shoot the electronics. It is easier to bring up the circuit outside of the chassis. Once everything works, install into the chassis.
13. Attach the left-side cover to the chassis with 6 self-tapping #4 screws.
14. Install the two controls through the respective holes in the right-side cover. They should fit tightly. Use some super glue if needed.
15. Attach the right-side cover to the chassis with 6 self-tapping #4 screws.
At this point everything should be fully functional. Note that the WARF-1X is designed for use at night looking at a dark sky. The projected reticle will not be visible in bright environments.
Step 6: Test and Calibration
At this point, the WARF-1X should be functional within the chassis with the sides on.
Install the WARF-1X onto your telescope using the interface bracket. The installation should result in the device close to being aligned with the telescope axis.
Screw the elevation and two azimuth adjustment screws all the way in (clockwise) as a starting point for alignment. Adjust the projected reticle position relative to the telescope boresight using a bright target (moon, bright star) by releasing tension on the springs holding the fold mirror as needed until the reticle is centered on the same object being viewed by the telescope.
Note: do not expect to see the projected reticle during daylight. The finder is designed to use low light levels, moonlight to total darkness.
I hope the WARF-1X helps to improve the speed and accuracy in hunting down dim deep sky objects.
Robert Wood
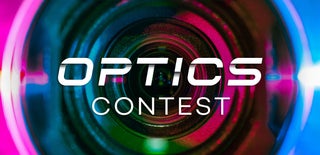
Runner Up in the
Optics Contest