Introduction: Window Bird Feeder
Nature at Your Fingertips!
Hey there, fellow bird enthusiasts! This window-mounted bird feeder has taken my bird-watching experience to a whole new level with its broad visibility and vast customizability through numerous angles of brackets and lengths of wood, and I hope you can adapt it to your needs. I started with a sketch before moving to Fusion 360 for the final design.
This feeder is all about making it your own. You can customize the panel-based designed to fit your style by changing the lengths of the panels and the angles of the corner brackets. Feeling like a bigger feeding area or wanting something unique and funky? No problem! This bird feeder lets you express yourself and create the perfect design.
This feeder attaches with suction cups onto any window. Mounting it on glass allows for an unobstructed view, bringing all the bird action right into your living space. A WiFi camera can be installed on the inside of the window, facilitating wiring, waterproofing, and thermal conditions.
See the attached supporting files for a multitude of sizes for angled brackets, editable STEP and F3D files that you can use to make it your own. Of course, this project does not need to be 3D printed as any off-the-shelf metal bracket can be substituted.
Supplies
For a brief summary, see below.
Materials
- angled brackets: 3D printed or purchased; any angle works - make it your own!
- plywood: 5.2 mm for the attached STLs; any suitable alternative may be paired with customized STEP files
- m4x14+ mm screws, nuts, and washers
- 3x suction cups: m5 screw attachment <amazon.com>[https://www.amazon.com/BlingKingdom-Suction-Plastic-Without-Adhesive/dp/B09BTW2148/]
Tools
- circular saw, clamps, construction square: cutting wood
- drill: approximately 4 and 5 mm Ø
- 3D printer (opt.): if not purchasing brackets
Step 1: Design
Start with a sketch of your build. See the attached renders of models for inspiration!
Afterwards, start with determining the angles of your brackets. As I opted for a hexagon, I needed to first determine the total internal angle measure of the polygon. For any regular polygon with n sides, that can be done by the following formula (remember Geometry?): (n-2)*180. Dividing this by the number of sides n yields the internal angle measure of each vertice as follows: (6-2)*180/6 = 120 deg. Each of my angle brackets fit this measurement. If you would like to purchase your brackets, opting for 90 deg angles is the most accessible way to create a rectangular feeder.
The panels can be sized however you see fit. As I made a regular polygon, I cut six identical panels of 136 x 160 mm. Consider the size of the birds that you hope to visit as you plan your feeder.
Step 2: Angle Brackets
For those of you following along with the CAD process, what follows is an outline of the process. Fusion 360 is used, but concepts can be carried over to your preferred software package. If you are purchasing brackets, skip ahead!
Fusion 360's parametric modeling software makes it easy to customize the angle of your brackets later. Start with setting a parameter for the angle measure. Feel free to create one for each angle measure you anticipate using. This panel can be used as a formula in the sketch of the bracket component, and it will update automatically as you edit the parameter fields. Tip: if you need to search for a feature, hit the S key and search for it.
See the attached image in the carousel for the base sketch used for the angle bracket component.
For the sake of brevity, refer to the F3D files in the introduction for complete details. This guide serves as a point of reference for designing your own bracket of for modifying the included models. For every step, click on an image to view the carousel in the order that chronologically matches the writing. Several angle measures are included as STL files, however the F3D and STEP files are intended for further customization. The dot on these files should be aligned upwards when slicing to allow for the bridging design in the vertical hex slots to work properly. See the carousel for a visual on this. The suction cups have their own 90 deg brackets.
Step 3: Wood Panels
Sketch the shape of your feeder, and bring it into life with CAD as an intermediary. For my regular polygon, I opted for six identical wood panels of 136x160x5.2 mm panels, however the possibilities are endless! Check out the carousel for inspiration. Consider the anticipated weight of your feeder as well as the length of unsupported spans when choosing the thickness of your panels.
These were sketched in CAD and aligned using fixed joints to each bracket. Using Fusion 360's Drawing tools, each panel can be printed out in 1:1 scale by deriving features from the modeled part. This can be done by right clicking on a component and clicking "Create Drawing". Then, select a size of paper around what you can print, and import a 1:1 scale base view of the panel, making sure to select the appropriate view. Using the dimension tool D, draw dimensions for the sides of the panel. Then, export a PDF. When printing the PDF, use 100 % scale for a perfect outline to cut at. This was especially useful for the edge panels that seal the bird feed in the feeder as they had awkward dimensions to measure and cut at.
Step 4: Prepare Parts
Now that the design process is complete, it is time to fabricate the parts.
The wood panels can be cut however best suits you. A CNC, table saw, circular saw, or hand saw are all suitable. Print drawings at 100 % scale if if helps with oddly shaped panels.
I 3D printed my brackets with a 0.2 mm nozzle at 0.15 mm layer height due to a past project, however I recommend a 0.4 mm nozzle at 0.2 mm layer height. Consider outdoor temperatures when choosing a material: PETG or a flexible might be better suited than the PLA that I had on-hand. Use sufficient perimeters (3+) for strength, as increasing perimeters is a more efficient way to increase strength than infill density. Have any questions about printing? List them below!
Step 5: Assemble
With each part now created, it's time to put them together! All what remains is to post-process any 3D prints for a smooth fit with the hardware and to drill holes into the panels. The simplest way to position the panels for drilling is to put two against each other until the edges fit tightly together, clamp the bracket to a panel, and use the bracket as a guide for the drill bit. Once you have a good panel, it can be optionally used as a template for the rest if they are identical, however this sacrifices precision. Edges can be sealed with tape whenever necessary. Washers can be used for stripped hexes or soft wood.
Some components do not need to be screwed in a precise position, such as the suction cups. For these, the suction cup can be screwed in and the mount can be placed in any approximately sturdy location. One 5mm hole can be made in the food sealing panel for a suction cup, reducing the need for an additional suction cup bracket.
Step 6: That's It!
Hope that helps any of you out there make something new for your local birds. If anything seems incomplete, missing, or unclear, leave a comment down below! If you make the project, great! Post a pic!
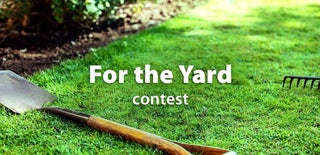
Participated in the
For the Yard