Introduction: Wood Burning Stove With Hotplate From Gas Bottle
What is more backyard ('garden' to us Brits) than cooking sausages? Nothing!
A few things came together for this project:
1) I had an old gas bottle to get rid of and the dump will not accept these.
2) I had a large pile of scrap wood to get rid of.
3) I wanted a hotplate so that I can make a cup of tea (I am English) and griddle sausages.
The solution to these 'problems' suggested itself.
First of all an apology for mixing metric and imperial measures. That's just the way I work...
Step 1: Materials and Tools
Materials:
Gas bottle (mine was 12kg)
Steel plate for hotplate. This needs to be quite thick. Mine was 6mm.
Pipe for chimney. Mine was about 4in diameter.
Short piece of 2 inch Square steel tube for air inlet
1 in square tube for legs
old paint roller for air inlet handle
old welding hammer for door handle
1 inch x 1/4 inch steel bar for door catch and hinge connectors
10mm diameter steel bar for pivot
thin piece of steel for air intake valve
thin steel strips for the door seal
Furnace sealant
Stove paint
BBQ thermometer (£3 from China)
Tools
Angle grinder
Adjustable spanner (wrench)
Welder
Tap and die set for the pivot (you could just use a large bolt)
Step 2: Careful Now...
Empty the gas bottle completely. Then remove the valve. Obviously go careful with this step!
Look online and on YouTube for how to do this safely. https://www.instructables.com/id/Purging-a-Gas-Cyl... is also useful.
Unfortunately I don't have photos of this step, but I put a large bar through the holes in the top of the bottle, then laid the bottle on its side. This stopped the bottle spinning as a lot of force is needed to undo the valve.
Then fill the bottle with water for a day or so before cutting it.
The bottle will smell of gas even when this is empty, but I BELIEVE this is the additive to make the gas smell, not the actual gas.
Please satisfy that you are happy it is purged before moving on to the cut.
Step 3: Making the Cut
Using an angle grinder cut the door and the top for the hotplate.
The hotplate hole needs to big enough for a hotplate, but not go so low that there is not enough room for a good fire. I made mine long enough to fit my large camping kettle.
The front door on mine is 7.5inch x 6 inch. This needs to be but carefully and in one go so that the door is still intact.
Step 4: John Wayne Is Big Leggy (showing My Age There)
Now to make the legs. I'm sure there are better ways, but this is how I did it:
The leg bottom piece needs to be the correct length for fitting. 13 inches outside in my case. The uprights were 14 inches. I wanted it short enough to fit in my shed, high enough not to burn the lawn. This was vital as one of my previous projects burned a large hole and Mrs Black wasn't impressed.
Cut 45 degree angles at both ends of the bottom and one end of the uprights. Weld them together as in the photos.
Hold them against the gas bottle and mark the placement. Now make cardboard templates. Cut the cardboard so that it fits the circle of the gas bottle perfectly. You need templates for the front and back. Use the template to mark the legs. Now cut and grind them until they fit.
Now weld the first leg unit to the gas bottle.
Now prop the gas bottle up and wedge it until the weld unit sits level on the ground with the door cuts horizontal. Once it all looks correct place the other leg unit in place and weld it on.
Step 5: Air Intake
Cut a hole in the door to fit the piece of square tube. I looked online and found some calculations for commercial wood stove air intakes. They more or less met my 2 inch square tube. Goal!
Using the tap and die, put a thread on the paint roller handle. Drill a hole in the tube and pass the roller through and put a nut on it.
Cut a square piece of steel for the flap so that it comfortably fits in the tube. Now weld the flap to the roller as in the photo.
Weld the tube to the door. Make sure it's airtight (this will be checked later).
Step 6: Unhinged
Cut a steel bar for the door pieces and hinge support as in the photo. Make a cardboard template as in the previous step so that the pieces meet flush against the gas bottle.
Drill 10mm holes in them.
Weld the pieces to the door first, making sure that they are level with each other and align horizontally with the door. Put the 10mm bar through the hole before welding to keep the alignment.
With the door in place (I used lots of magnets to hold it closed) put the rod through all the pieces and weld the supports to the body, making sure that everything is aligned and that both supports will make contact and carry the weight.
Use the tap and die set to cut a thread on the bottom end of the bar. Weld a flat piece or nut on the top end (this is just to stop it dropping through the hole).
Step 7: Door Liner
Cut some strips of metal, bend them to shape and weld them inside the door. I used a street sign that I found in the street (ahem). They were a bit tricky to weld in place, but I managed to get the welder head inside the door.
The strips are to hold the door in place and to create a bit of an air seal, so this step is important.
Step 8: Can You Handle It?
I used a welding hammer for this. I had an old one, but they are only about £4.
Cut off the hammer head. Heat and bend the shaft. Using the tap and die set put a thread on the end. Drill a hole in the door that JUST fits the handle. Put the handle through and put a nut and washer on the inside.
Now cut a piece of the steel bar to make a catch for the handle. Weld it in place so that it will hold the door tightly shut.
Step 9: Hotplate
This step is pretty obvious.
Cut your sheet steel to size, grind off the sharp edges and weld it into place. Use lots of weld to ensure that it's airtight.
Step 10: Chim Chim Cher-ee Chim Chim Cheroo
Time for the chimney. Cutting the the correct size hole had me stumped for a little while, but here's how I did it. I didn't use my high school geometry, I used an empty bean can.
The bean can was about the same diameter as my chimney pipe. So I repeatedly snipped away at the can until it was flush with where I wanted it on the gas bottle. I then drew around it and carefully cut the hole until the pipe just fit inside. With the pipe inside I reached in the gas bottle and drew around it. Then I cut the pipe.
With the pipe in place (projecting slightly into bottle) and properly upright, I welded it into place. I made it 30 inches high and it works well.
Step 11: Seal
Seal the chimney with fire cement or furnace sealant. This step is important as without a proper airtight seal the chimney won't function.
Step 12: Fire It Up!
Fire it up. Check that everything is airtight and correct any holes with welds and/or sealant as appropriate.
Step 13: I Want to See It Painted, Painted Black
Spray it with proper high temperature stove paint.
Add a BBQ thermometer. Go for one with high temps (I'll explain why later). You simply drill a hole, poke it through and screw the nut on.
Step 14: Sausage Time!
Now your stove is complete you can finally cook some sausages!
Light her up. Usual procedure; paper, cardboard, kindling, wood, close the door. Use the air flap (and door if necessary) to regulate temperature.
Cook your sausages directly on the hotplate. Eat your sausages.
Now for the importance of the high temp thermometer. We have a self cleaning oven that does that whole pyroclastic thing (ooooh!). Well I thought I'd see if I could get pyroclastic on the hotplate. Turns out I can. Once you have a roaring fire close the flap and use the thermometer to get it as hot as you can. Hot enough to burn away the fat and residue from the hotplate. Boom!
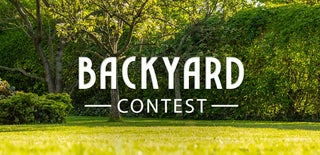
Runner Up in the
Backyard Contest