Introduction: Wood Cake Stand - Hand-cut Japanese Joinery
Excited for my first instructable and contest, here we go!
I love the Japanese style tables and their hand-cut joinery in particular from George Nakashima. So with my beginner's naivety I set off to build a coffee table in this style! Then I started looking into cost of the beautiful olive wood top and oak legs that I wanted... then thinking that I never actually tried to cut a joint like this... finally it seemed like it would be just another sketch up 3D model idea that would forever live in the virtual world...
Until on another hopeful search on e-bay for a piece of olive-wood I found this company selling these beautiful cutting boards for really cheap. They were the factory seconds but got a couple of them and I thought they looked really nice!
Then it dawned on me, what if I make a mini version of the table to use as a cake stand or serving board? It would be a great skill builder and give me confidence to tackle a bigger version later on!
Step 1: Materials and Tools
Wood:
- 1 olive-wood cutting board: 350x150mm
- 1 oak piece: 30x30x1000mm
Tools:
- layout tools: ruler, marking gouge, marking knife, pencil
- Japanese pull saw
- small set of chisels and mallet
- jeweller saw (optional)
- jack-plane
- mitre box (optional)
- flush cut saw (optional)
- mineral oil
- callipers and try square
Step 2: Cut the Vertical Post
The main joint in this project is called shiro/ castle joint. I found this tutorial by Katz-Moses that explains the process quite well although he did it using power-tools.
In my case I did the following:
- made sure my oak was flat, square and precisely dimensioned to 30x30mm. I did this with my jackplane and checking regularly with my calibers and square. Takes a bit of patience and elbow grease but it's well worth the effort so that the joint cutting goes smoother.
- cut a piece to 100mm.
- measure 30mm + the thickness of your top + 2mm (so you can later flush it with the top) and mark a knife line on all the faces.
- using the marking gauge accurately set to 10mm, scribe from all faces till the mark you did before. Mark the waste part which is the center cross.
- with the Japanese saw cut on the waste side of the line as close as you dare but knowing you can later chisel to the knife line.
- remove the bulk of the waste with the jewellers saw and then chisel slowly back to the knife line.
Once this is done do exactly the same on the other end of the post but this time just to the depth of 30mm +2mm
In the end the part should look like the last photo.
Step 3: Cut the 4 Mortices on the Top
Since I was a bit nervous about these 4 mortices I decided to do them before finishing the other joints.
My process was:
- mark the post cut on the previous step with letters in each tenon.
- find the center of the top on the narrow side and them mark a line 64.5mm from one of the ends.
- draw accurately a grid of 3x3 10mm squares to match the posts previously cut and scribble the letters matching the ones on the post.
- transfer these marks as accurately as possible to the other side of the top since to get a clean cut I'ld have to chisel from both sides.
- chisel slowly till the line but leaving it.
- test fit the post to the top and start tuning the joint. Be particularly careful on the top side of the top so you don't get a little chunk to fly off like I did! (3rd photo).
- be patient as this took me quite a bit of back and forth but its the most visible part.
Step 4: Cut the Base and Top Supports
If you made it here the hardest part is behind you, time to finish cutting the joint.
From the same oak post used before, cut:
- 2 pieces to 100mm
- 1 piece to 300mm
- 1 piece to 211mm
Cutting the base:
- mark a knife line 40mm from the top of the 300mm part. Then using the post cut on step 2, mark another knife line on the other side to mark the width
- with the same marking gauge set before to 10mm, mark the longitudinal lines as per the 3rd photo
- Cut on the waste side of the line with the pull saw then using the jewellers saw remove the bulk of the waste
- pair to the lines carefully with the chisel (picture 4 and 5)
- repeat this process to cut the 100mm part this time in the center of the part
- check the fit of the 2 parts inside the bottom of the post and tune as needed. Write letters matching the ones on the post to keep track of the orientation.
- finally mark for the half lap joints so you get the 2 parts as shown (picture 7 and 8). This can be a bit looser as the post will lock in the joint
Cutting top supports:
- As per the diagram, mark the 211mm part 28.3mm from the top.
- Then just follow the same procedures as for cutting the base
Step 5: Tapers
Time to beautify!
Pick the 2 longer pieces of the base and top support. On the end further away from the joint, mark a line half the thickness of the material (15mm). Then trace a line from the joint till this line at the end grain.
Tune the plane and make some pretty shavings until you hit the lines.
Step 6: Cutting the Ends to 60 Degrees
Using my mitre-box I cut all the ends of the base and top supports to 60 degrees trying my best not to change the total length of the part.
Use the picture 3 to check the orientations of the angles! It's very easy to mess up (actually if you pay close attention to my sketch up model and the finished project you'll see I did just that :P).
Step 7: Enjoy Your Beautiful Parts and Get Excited About the Assembly
If all the joints are tuned this is the most satisfying part! I think I assembled and disassembled it at least 10 times!
Check again the video at the top to see it all coming together.
Step 8: Flush Cut the Post and Plane
Because we left the tenons on the post a little proud it now time to cut them flush and them plane them both at the top and bottom.
I also had to do a couple passes with the plane to make sure the 2 bottom part was coplanar.
Step 9: Chamfer the Underside of the Top
At this point a power tool makes its appearance! I wanted to match the angle of the ends of the base and top supports and for that I tough that a 60 degree chamfer bit on a router would bring me the best results. I ordered one bit similar to the one on the photo and got to work.
Unfortunately no photos survived of this process but using this bearing guided bit made quick and easy work. I did a test cut on a piece of scrap aiming to get the chamfer up to 2/3 or 3/4 of the top thickness.
In the end the top was looking like the first picture.
Step 10: Glue Up and Sanding
For the glue up I used a waterproof glue and clamped it all together with my vice, a couple of clamps and a piece of scrap. It all locked together pretty tight so gluing wasn't really necessary but as I wanted to give it as a present though it best. Also helped hide some small gaps as the glue swells up the wood slightly.
Using a 120 and then a 240 grit sandpaper I sanded on all surfaces and knocked all the sharp edges by hand.
Step 11: Finishing
Using a food safe mineral oil and a foam-brush I saturated the wood a couple of times.
Then wiped off the excess with a paper towel.
Step 12: Enjoy Your Art Piece and Bake a Cake!
You can also bake 2 cakes :P
Enjoy!
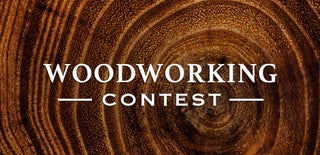
Participated in the
Woodworking Contest