Introduction: Wood Carving Knife Set
This Instructables is all about building a set of a carving knife. I wanted to be a person who is capable of doing all kinds of work and that's the reason why I stepped into this kind of work and if you do a wide variety of work you have plenty of things to learn. I kept watching a lot of wood carving channels from Vietnam, Indonesia, Thailand, USA and many other countries and the way they carved wood is really marvellous and that thing always forces me to give this at least a try. This Instructables is all about that. I am not good at carving wood but I think it's all came from practice and more practice. The more I do the better I get in this work. So I started this thing by making a set of knives and they turned out very nice. In the video, it might seem that they are very fragile and not able to cut any material but the material is high-speed steel and very robust and can withstand last long. If you have any suggestions feel free to post them in the comment section down below.
Supplies
For the material, I am using two different blades one is a circular saw blade and other is a hacksaw blade. It's not a hand hacksaw blade it's a machine hacksaw blade, I get it from a person from where I buy my material supplies. The blade laying in his shop and I asked him and get it for this build. The material of the hacksaw blade belongs to high-speed steel material. And the circular saw blade is from unknown tool steel but the company name is black and Decker. The thickness of both the blade is around 3 mm in thickness. The handle material is an ipe wood and its a 1" wide strip leftover from my coffee table projects in which I made 2" wide CNC inserts. The total width of ipe plank is 5" and I need around 2" wide strips for my inserts and 1" become useless but glad that today I utilize them.
Tools Required
For the tools, you really didn't much of the tools. If you didn't have a scroll saw then copping saw works well. If you didn't have coping saw then block plane can complete the job because there is not too much-cutting include and most of the work is just shape the handles and then hand sanding completes the job done. Here is the list of tools which I used in my build.
- Variable speed angle grinder
- Sanding disk pad
- Cut off wheel for angle grinder
- Flap disk
- Diamond Lapping disk (bench grinder also works well, but didn't have that)
- Speed regulator
- Diamond sharpening block
- Ruby stone for Honing the edge. (leather and buffing compound also works well)
- Two-part epoxy
- Drill machine and drill bits
Step 1: Material Cutting
The material has been cut according to the template. I made a set of the template and they are most likely those which are available in the market. For the cutting process, you can follow any method you want. Either stick them to the material you wanted to cut or just place and trace them. I like the tracing work because during the cutting the paper template usually burns out and you might lose the reference. I mostly use an angle grinder for this process. I didn't make any template for the hand saw design because the blade already has teeth and I used the same teeth because the blade when used in the machine only the middle part of the blade, gets mostly used so the sharpness of the adjacent teeth is fine. I focused onto the hacksaw blade because it's material is HSS and used for cutting metal items and the circular saw blade usually used for the cutting wood.
Step 2: Final Grinding and Deburring
After the cutting process, the blades have burrs because cutoff wheel usually makes burrs while cutting and since I cut them roughly so they need to be ground down to the final shape. It also debuts all those burrs which appear during the cutting process.
Step 3: Making the Handle
Handles part usually depend upon the palm-size but I provide a template. It's not really that complicated process to draw but if you want you can use the template. Since it's a repeated process so I decided to make a template from MDF which is laying around in my workshop. I stick the paper template and then cut it onto my scroll saw. Later on, I sanded down the edges of the MDF template to make it smooth to take reference. The wood for the handle is an ipe wood and I kept is for a very long time. A few years ago I made a coffee table and I made wooden inserts in that table which are of ipe wood. Since the wood is quite costly so I decided kept that 1" part in the hope that I might use it in future projects. The plank is 5" in width and the insets were made around 2" wide. So that's how they came from. After laying out the outer profile of the handle I cut them onto the scroll saw. IPE is a very dense wood and blade have to do a lot of struggle during the cutting process but all went OK and I get those shapes. In my design, I kept two different styles of handles. Usually, I used a bigger handle for the bigger blade. Once the basic shape is achieved I straighten the profile onto the angle grinder. From thereafter I started the contouring process of the handle and there a definitely a lot of different ways to do that. Being a knife maker it's an easy process for me. But the key to success is that once you straighten out the edges then marked a center line onto the handle and then start the contouring process by joining the side center line and the top center line in round shape. I use hand sanding and drum sander for this work. I sanded the handles up to 220 grit sandpaper.
Note:- If you are willing to watch ceramic coffee table check the instructable link down below.
https://www.instructables.com/id/DIY-Stainless-Steel-Coffee-Table-With-Ceramic-Top-/
Step 4: Drilling a Tang Hole
Once the basic shape is finished I start the drilling work so that I am able to fit the tang of the knife inside those handles. I roughly marked the hole location and then I start from 3mm drill and then made a final hole with a 6.35 mm drill bit.once the blades fit into the handles it's good to go with the next process.
Step 5: Quenching and Tempering
Before installing them into the wooden handles I did the quenching process by heating them up to red colour and then quench them in water. That will immediately harden the blade but to avoid the brittleness I again heat them with the torch to temper them so that they remain hard and flexible. Tempering is necessary for this and yellow straw colour of the metal is a stage when you have to stop providing the heat to the blades otherwise you overshoot the temperature and softens the blades again.
Step 6: Edge Bevelling Process
For the sharpening process, I am using a diamond lapping disk on the angle grinder. Now here one thing has to not down that this is a variable speed angle grinder and even then to reduce the speed too much slower I hooked this thing to a voltage regulator. By doing this the wheel is spinning at a very slow rate and the chance of an accident are also reduced. So for this, I am using different grit size of wheel one is 80 grit and the other is 180 grit. For the bevelling process, I am going to do a single side bevelling method because 3mm is not a too thick and ingle side bevelling works very well in this case as we saw in the Japanese chef's knife. To start the process make sure to know the rotation of the blade and while grinding the blades make sure not to insert the blade against the wheel rotation. Then I coloured the edge and start the bevelling work. To keep the wheel cool during the grinding I sprayed wd40 onto the wheel and just by eyeballing start the bevelling work. I kept water along with me to cool down the blade at regular intervals. The process is difficult for some of the curved blades but I manage to do them. Then I repeat this process with 180 diamond lap disk.
Step 7: Gluing With the Handles.
From thereafter, I mixed two-part epoxy resin and insert the tang into the handles and allow them to cure overnight.
Step 8: Polishing and Sharpening Process
Once the glue cures it's time to do the polishing process because now the blades have some base to hold down. To do this process I use a diamond plate and it has two different grit sizes 400 and 1000 grit. I first remove the scratches with 400 grit and then sharpen the edge with 1000 grit. Here one thing needs to know that to have a sharp edge you need to flatten the entire blade as the have a chisel edge. If it has a double side beveling then you have no need to do this straightening process. The sharpening process is similar to the chisel sharpening and for the curved blade, you need to divide it into different sections and then sharpening that perticular section of that blade. If there is a burr appears onto the backside then it means to stop the sharpening process and move to the next step. For the straight-edge blade, it's not difficult to get the sharp edge. Once the burrs appear onto the blades with the help of ruby stone I hone the edge for the final edge. Honing process is also important to get a good edge onto the blade.
Step 9: Finishing the Knives
The final finish is done with the help of linseed oil. I just rub it onto the wooden handle and wipe off the excess. This makes the handle colour pops up and make the set quite beautiful.
Step 10: Final Look
Although I am not good in wood carving and still in a learning stage. I tried to test the blade onto a piece of wood and the blade works very well. In the image, the blade might seem quite fragile but you have to remember that these blades are made up from a blade which is capable of cutting mild steel. If you have any suggestions to improve let me know in the comments section down below.
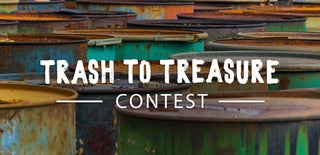
Second Prize in the
Trash to Treasure Contest