Introduction: Wood House Advent Calendar
A few years ago my cousin asked my father to make her a couple of wood advent calendars. Dad and I went through a few ideas on how to construct them. However, before he had a chance to build them he passed away. My family said it was now up to me to carry on the woodworking tradition of the family. So with this I decided to take the ideas we had started with to make these advent calendars. The first couple I made I had some serious issues with the doors. How to hinge them... After trying to make custom ones with thin metal, using ½” steel dowels and modifying regular hinges, I finally came up with an idea that would work. I use long pieces of 1/8” steel rod that run through the full height of the calendar going through holes in the doors. This may sound tricky, but it is actually quite simple.
The calendars are highlighted with a Christmas tree in the top gable area with a battery-operated tea light in behind to give a nice glow. My preference for wood is maple for the main case and Padauk for the doors and accent pieces. I like the Padauk for the main fact of having the red accent wood for Christmas. These house shaped advent calendars have now become quite a popular item on my online store. This is a project for intermediate to advanced woodworkers and requires patience and the proper tools. With the trial and error process that I worked through over the past year, I think I have worked out all the bugs to make these a sturdy and long lasting family heirloom.
I have included the drawing plans with material list and templates for easy reference. If you love the design but just want to buy the finished product, you purchase it on my Etsy store.
Attachments
Step 1: Materials & Equipment Needed:
6 ½” x 12 foot rough 4/4 Maple wood (or any type of light coloured wood)
6” x 4 foot rough 4/4 Padauk wood (or darker accent wood of your choice)
24” x 24” piece of 1/8” hardboard
5/8” pre-cut wood numbers for the doors (Stockade.ca)
25 – ¼” x 1” Wood Axel Pegs (Stockade.ca)
5 – 1/8” x 12 5/8” steel rod (Hinge Rods)
25 - #4 thin Washers
1 – Keyhole Slot Plug (Lee Valley #05H03.01)
1 – Battery Operated Tea Light
Maple Veneer (optional)
Gorilla Super Glue
Wood Glue
Hot Melt Glue Gun with clear glue
Clear Polyurethane Satin Finish
Drill Press with Fence and stop block
Table Saw
Miter Saw
Router
3/8” Dado blade or router bit
¼” Round-over Router Bit
5/8” Forstner bit
1 ½” Forstner bit
Lots of Clamps
Step 2: Prepare Material for the Case and Roof
Prepare your parts for the main case, dividers and roof from maple. The main case, roof and gable are constructed with 3/8" material. The dividers are 1/4". I plane my maple to just above my thickness required, cut them to length and width (as per attached drawings), then run them through my drum sander to get my final thickness. For the roof gable, prepare a rough piece 6 ½” x 13”. You will most likely need to glue up some wood to get a width of about 6 ½” unless you were lucky enough to get some wider wood. Finish sand all parts with 220 grit by hand.
TIP: Depending on the thickness of your rough maple you may be able to re-saw on the band saw. You will need to plane the wood to a minimum of 1" or just slightly over. You can save a lot of wood by cutting your parts to rough width and length and re-sawing those pieces in half. If you can get 7/16" pieces from re-sawing you will have enough board left to still run through the planer and/or drum sander for the case materials. If you go off a bit on the band saw, the narrower parts can be used for the dividers. I try to do this as often as possible as I hate to see all that wood go to waste as wood shavings from the planer.
Step 3: Pre-finish Case Parts
Before I start cutting my rabbits and dadoes I like to spray finish with a couple of coats polyurethane on the dividers and case frame pieces. Those little boxes are impossible to spray and sand properly after assembly. Only put one coat of finish the inside only of the gable board. One coat helps prevent the board from warping before getting to the cutting and assembly stage. For the two roof pieces, you will need to tape off the inside area where they will be glued to the gable later. Using painters tape apply a piece of tape on the inside back, ½” from the outside edge. I prefer to spray on my clear finish, but if you don't have access to an HVLP spray gun you can finish all parts by hand. I use a water based finish, but any clear finish of your choice is fine. While these parts are drying I start working on the other parts.
Step 4: Calendar Doors
For the doors, plane the Padauk to 3/8”. Cut two 2 3/16” x 36” strips. Rout a ¼” round-over down the one side of each strip. This will be the outside / hinge side of the doors. The round-over allows the doors to open properly without the edge rubbing against the frames. It is easier to rout this round-over on the long strips than trying to do each door individually.
Sand the strips before cutting into length for the doors. Sanding before cutting takes away a bit of the work load when finish sanding the doors. Cut the doors to 2 3/16” long on the miter saw. Make sure you put the square side of the doors to the miter saw fence and have a zero clearance backerboard against the fence to prevent any tearout on the doors. Alternatively, you can cut your long strips 2 ¼” wide then after the doors have all been cut you can trim each door down to the final width. This will skim off any tearout you may get. It is good practice to make several extra doors for test drilling the hinge holes later on. You should get 30 doors from the material.
Lay out doors and spray or hand finish all sides and edges of the doors with 2 coats of polyurethane, lightly sanding between coats. Pre-finishing at this stage, before attaching the numbers and knobs, makes the sanding much easier.
Step 5: Cutting Case Dadoes and Rabbits
Now lets prepare the pre-finished parts for the outside case. I tend to work back and forth now between spray-finishing the doors and making the final cuts and dadoes of the calendar case. Before I start cutting the dadoes and rabbits, I choose the best outside and front edges and mark the inside ends and inside back with pencil so I know which sides I want to cut. For the case sides, you need to cut a 3/16” x 3/8” rabbit on each inside end of the sides and a 3/16” x 3/16” rabbit along inside back of each side and case bottom. You can do this either on the table saw or router, whichever is your preference for tools. Just be sure to use backer-boards to prevent any tear-out on your finished pieces.
On the outside top edge of the case sides cut a 45 degree angle 3/16” deep. This gives a flat clean surface for gluing on the roof pieces. (see drawings)
To keep the dividers even during assembly, cut or rout 3/16” x 3/8” dadoes where each divider will sit. Please refer to my attached drawings for the exact location of each dado. These need to be cut on the inside of both the side and end pieces. I originally never did the dadoes for the dividers, but have found that assembly works much better to hold everything in place and ensuring squareness. Lightly sand the dadoes and edges slightly for a clean look.
Step 6: Cutting Divider Dadoes
For the dividers to fit into each other, a 1 5/32” x 3/8” dado will need to be cut on both vertical and horizontal dividers where they cross each other. It is handy to have some extra stock cut at the same width and thickness to use as test pieces. Each piece needs to nestle together snugly but not so tight that you can't get them apart. You may need to pull them apart after dry-fitting to make adjustments. The dadoes also need to be flush on the outer edges when put together. The drawings show the exact location of each dado.
Select the edges that you will want to have toward the front of the calendar. Flip over and mark the back sides. Since the dadoes are on reverse edges for the horizontal and vertical dividers, it will make it easier for cutting the proper side on the table saw. I prefer using my dado set on the table saw as each groove can be done in one pass. If you prefer to use your router, and have a long enough 1/4" straight router bit, you will need to cut in increments. Alternately, if you don't have a dado set for your table saw, you can use a full kerf TCG blade and make the dadoes in two passes, adjusting your fence for each pass.
Step 7: Hinge Rod Holes and Case Assembly
We now need to drill some 9/64" holes for the steel hinge rod. These will be done on the horizontal dividers only and the top and bottom pieces. Placement of these holes is key and must be accurate to ensure the rods go straight through the case. For the top and bottom pieces, the holes will be 3/16” deep. I go to my drill press for this job and utilize my fence and a stop block. The holes are 3/16” from the front edge of the dividers and top and bottom pieces. The left side holes are 3/8” from outside edge and the subsequent holes are 3/16” to the right of the divider dadoes. Set your fence so that the center of the bit is 3/16" from your fence. I designed a template from 1/8” hardboard for this but it can easily be done by marking the center of the holes on each piece. If you plan on making more than one you may want to make a template or a jig to speed up this process. I drill each divider individually so the bit doesn't move or bend making the lower board holes crooked. You can mark and drill one, then use that piece as the template for marking the other dividers and top and bottom pieces. You can mark with a pencil, but I like to use the same size brad point drill bit and tap it lightly with the hammer through my template holes to give an indentation for the center. Another method I have done is by using my stop block. I mark one divider only, set my stop for the first hole and drill all the dividers and top and bottom pieces individually, then set the stop block for the second hole and repeat until all holes are drilled. This ensures ever hole is identical.
For the five hinge rods, I purchase 1/8" steel rod in 48" lengths from one of the home improvement box stores and cut it to length with my hack saw. The steel rods are the same lengths as the dividers, 12 5/8".
Once the holes are drilled it would be a good time to do a dry fit. Assemble the dividers together. Just as a note, I don’t glue them together as I try to keep them as snug as possible, so once your done dry fitting you can leave the divider assembly together, depending on how tight your fit is. When assembling you will need to clamp the dividers within the side pieces and clamp the top case piece in place, leaving the bottom off. Push your 1/8” steel rod up from the bottom through each line of holes to see if they line up properly. You can use a small rasp or your 9/64” drill bit in your hand drill to make the holes a bit bigger in any direction to ensure everything is going in straight. If the holes are slightly bigger than the 9/64” it won’t affect how the doors open.
Once you are satisfied you can glue up the case. Remember, don’t glue on the bottom piece on yet. It needs to stay off to install the doors. Glue your dividers together first if required. Apply glue to the top edges of the divider assembly and clamp on the case top ensure front is flush. Let dry for about half an hour. Then repeat this process to attach both sides, applying glue to the dividers and end dadoes of the sides. Make sure front side is flush and the entire case is square. This is going to require a lot of clamps. When dry, remove from clamps and clean up any glue squeeze out. Sand joints and front of case with 220 grit paper as required. I usually sand the front of the case with my 1/3 sheet sander to ensure all pieces are flush.
Step 8: Roof Assembly
For the roof parts, cut a 45 degree angle on both inside ends of both roof pieces. At this point I like to glue my roof pieces together so they have ample time to dry before final assembly. I use a 45 degree angle clamp and glue the roof pieces together at one end before gluing in the gable. Remember to remove the painter's tape before this step. Set aside for attaching to gable and case later.
I wait until my back panel has been attached to the case to cut the gable, this ensures the gable is cut to the exact measurement.
Step 9: Door Hinge Rod Holes
This is the step where patience is a virtue. Holes need to be drilled through the entire height of the hinge side of each door. This must be done on a drill press. Insert a 9/64” drill bit into the drill press with about 1 ¼” of the bit sticking out. This will help keep the bit straight while drilling. Also ensure your drill press bed is square to your bit and fence. Set up your fence on your drill press so the bit is lined up in the exact center of the door thickness. Next set up a stop block so your bit center is 3/16” from the hinge side (rounded side) of the door. Make sure you have a few pieces cut the same size as your doors to run some test drilling. When you are perfectly lined up put your first door against the fence with the outside of the door facing out. You can only drill about halfway through the door at a time then you will need to flip it over and drill from the opposite end. If you try to go through the entire height of the door, the bit will usually go off on a bit of an angle. Drill the hole in increments. Only go in no more than ¼” at a time, pull the bit out, clean off any material stuck on the bit, then continue drilling gradually until you are just past halfway of the door height. Trying to do too much at once causes the bit to heat up too much and can crack the wood. I like to keep a stiff paint brush handy for cleaning the bit. Now you need to flip your door over ensuring you are keeping the bit on the hinge side of the door. The inside of the door should now be facing you. Repeat the process as you did on the other side only drilling small amounts at a time. Continue until all 25 doors are drilled. To ensure the holes are straight and cleaned out well, I like to put the drill bit into my 12v cordless hand drill and ream the holes running the bit through the entirety of the hole. If you are slightly off angle with the holes you can use the bit to lightly ream them. But if you did this process slowly and carefully everything should line up nicely.
Step 10: Preparing Door Handles
The door handles are made from the ¼” axel pegs. Since you can’t buy them ½” long, you will need to cut them down. This can be done on a band saw, miter saw or by hand. The easiest for me was on my band saw. I used a piece of ½” MDF about 3” x 12” and drilled 5 – ¼” holes in a row, about 2” from the bottom. Spacing isn’t important. I locked in my fence or you can clamp a straight edge to the bandsaw bed – ½” from the blade. Put 5 axel pegs through the holes with the button side away from the blade and the excess part of the peg sticking out. Slide the MDF board along the fence through the saw cutting off the excess. Your blade should lightly skim along the MDF board. This was just my quick easy way of doing this that was a lot safer than cutting on a miter saw.
Alternatively, you can purchase small brass or silver finish turned knobs from Lee Valley if you want something a bit fancier. However, since you need 25 of these, it can get a bit costly.
Step 11: Completing Doors
To insert the door knobs, mark and drill a ¼” x 3/16” deep hole in each door 3/8” from the bottom and outside edge. Using the drill press with the fence and stop makes this step simple and quick as you only have to mark one door for the setup.
For the door numbers, I purchase them online from Stockade.ca. They are Cooper Font 5/8” high. If you own a laser engraver cutter, you can make your own. The material list in the attached plans tells you how many you need of each number. You can either mark each door or make a jig to ensure the numbers are all centered at the same location on each door, about ¾” from bottom of door to bottom of the numbers. I made a simple jig using 1/8" hardboard on the top and bottom and some small 7/16" inner pieces for the left and bottom sides. Mark the center line for the center of the door measuring 1 3/32" over from the inside of the left support. This way you can always get the numbers in the center of the door. I also cut an area for the knob so I can do all the work on the doors at once.
Glue on the numbers and the door knobs with Gorilla Super Glue. You only need a small amount, too much and you will have squeeze out that is difficult to remove.
Finally, glue a #4 washer around the hole for the rod hinge on the bottom only. This will keep an even space underneath the door when it's upright. It's not necessary to put on on the top. I glue them in at this stage to make the door installation easier. Use the Gorilla glue for this step as well and have some of the cut of 1/8" steel rod handy to put into the hole to ensure the washer is in the correct location.
Step 12: Door Stoppers
The doors need stoppers so they don’t push inward. I find this easiest to do before installing the doors. I cut thin strips of maple that match the case wood. Each piece is 1/8” x 3/8” x 1 7/8” long. Place the case upside down with the back facing you. Glue each piece on the top side of each compartment opposite of the hole for the hinge rod with Gorilla Super Glue. Make sure each piece is flush with the back. This should leave 3/8” space from the front edge for the door to sit and rest against the stopper.
Step 13: Door Assembly
Assembly is always a bit of a trial process. I always lay out my doors on my bench in numerical order so it’s easier to find them. Remember they have to be installed in order. Lay your case on it’s back and starting from the left vertical compartments, feed one steel rod through the first divider hole slightly and push through your first door, then feed through the next divider, put on the next door, repeat this till you get to the top and push the rod into the hole in the top case piece. Test each door to ensure they open and close properly. Sometimes you may need to either do some fine sanding of the doors or ream the hinge rod hole slightly. Repeat this process for each column of doors. Once all the inner doors fit well, test for the bottom row of doors to ensure they will work will. You will want to do a dry fit of the bottom piece as well. You may need to slightly tap the steel rods to go into the holes of the top and bottom of the case.Glue and clamp the bottom piece in place.
One final touch still needs to be done. Once the case frame is dry, remove from clamps and scrape any excess glue. You may notice that the doors tend to flop open. The difficult time I have had was getting the doors to stay closed. I had one customer say that I should put in little magnets. However, this would be a tedious task as well it would increase the cost of the calendar quite a bit. As a solution, I put a dab of clear hot melt glue on bottom outside corner of each door. Let it cool slightly and push it down with your finger to flatten it out so that the door has just enough friction to keep it closed. Test your door, If you make a mistake just peel it off and try again.
Step 14: Back Panel
To make the back look clean and to give more stability to the entire advent calendar, I cut 1/8” hardboard in the shape of the house and glue on the back. See the drawings for the exact dimensions and verify with complete case assembly. The 45 degree angle for the roof gable can be cut on your miter saw or table saw using the miter gauge. Mark your cut line with an angle square on both sides of the board before cutting to ensure you get your cut accurate. I use my miter saw, I set my stop at the height of the back of the case area, then cut as far as I can at a 45 angle for one half of the roof. Then I flip it over and cut the other side. Lightly sand the cut edges for a clean edge. Apply glue to all rabbit areas and a thin bead on the backs of the dividers. I like to brush out the glue before applying back panel to ensure an even thin layer of glue and to prevent any major glue squeeze-out. Clamp and set aside. This step was one of my additions that I started doing after having some issues of the roof assembly coming off. This has proven to really assist in the stability of the calendar as well as giving a cleaner look on the back.
Step 15: Attaching Roof Assembly
I cut the roof gable on my miter saw or you can use your table saw with miter gauge set at a 45 degree angle. Verify the length required for the bottom side of the gable by measuring the top of the case between the inside edge of the 45 degree chamfer on the top of the case. The gable must sit in that area evenly so the roof parts don't have any gaps. It should work out at 12 5/8", however, even a 1/32" difference can make attaching the roof difficult. An easy way, now that you have your back panel glued in place, is to trace the back panel onto your gable piece. The back panel and gable must be flush on the outer angled edges. Dry fit the pre-glued roof section, gable and case and sand as required to give a tight fit.
Before attaching the gable to the back panel, you will need to sand off the finish on the back side of the gable. Since only one coat was put on, roughing up the back with 120 grit paper will remove the finish to allow the glue to adhere properly. To attach the gable to the back panel and case, spread a thin layer of wood glue on the back and bottom edge of the gable and clamp. I usually leave this clamped for about half an hour. Remove from the clamps and scrape out any glue squeeze-out before it dries too hard. You may need to do a light sand of the case 45 angles at the top, and the outer gable edges and back panel to ensure they are smooth.
Now you can glue on the roof assembly. Make sure the front of the roof is flush with the case front the the area that was taped during spray finishing is at the back. Apply glue along the angled edges of the gable and the angled corners on the top outside edges of the case. Clamp together making sure the entire assembly stays flat. Because the roof gable wants to pull up, make sure you clamp the gable and calendar case to your work bench to hold it down and keep it flat. Put a 1/16" piece of scrap wood under the gable area before clamping to your bench as the back panel is recessed 1/6".
Step 16: Roof Facia
While the case is drying you can cut the roof facia scallop pieces for the front of the roof edges. Cut 2 pieces from Padauk, ¼” x 1” x 11 7/8” long. Cut 45 degree angles on one end of each piece. Print 2 copies of the attached drawing plans for a scaled template for the facia pieces. You can either use spray adhesive to attach the template to the wood or trace it out. The paper can easily be removed after cutting and a light sand removes any gum residue from the glue. Cut your scallops on the band saw or scroll saw and finish sand with 220 grit paper. An oscillating sander with a 1 1/2" spindle makes sanding quite simple. Glue and clamp to front edges of roof ensuring pieces are even and line up straight at top. Leave an overhang on the flat side about 1/16” past the roof. Make sure the facia doesn't block the top corner doors from opening properly.
TIP: Depending on my material, I often cut the facia from a wider piece of stock, cut the scallops and sand the entire piece. Then I rip my 1/4" pieces on the table saw. When cutting this way, it is safer to leave the one end square and cut the 45 degree angle after the individual pieces are cut. This makes it safer to rip giving you a square end to use a push block on the table saw.
Step 17: Christmas Tree Candle Holder
To cut the Christmas tree for the top you will need some of the accent Padauk wood with maple accents. Or you can do in reverse with a maple tree with Padauk accents. Prepare your piece for the tree to around 3/16” thick. You will use the attached plans again for the scaled template for the tree. Cut out the tree on a scroll saw (my preference) or band saw with a fine blade and sand to smooth all edges. Now you will cut some 1/8” thick, or less, pieces of maple for the garland using the template to mark them on the maple. Cut with scroll or band saw. If you don’t want them too thick you can use 1/16” maple veneer and cut with a utility knife or scissors. If you pick up some pre-glued veneer edging you can attach by ironing on. Glue the garland to the tree with Gorilla Super Glue. This part doesn’t have to be exact to the plans. Feel free to be inventive. Drill a number of 1/8” holes through the tree between the garland. This allows a bit of the light from the tea candle to glow through giving the appearance of ornaments on the tree. Making the tree is definitely a bit tedious, another step that would be easily done on a laser engraver cutter. That is the one tool that is on my wish list as I make numerous projects with small cutouts.
There are other options for the decorative accent for the candle holder. Ready made wood cutouts can be purchased through various online stores like Stockade.ca. They have numerous Christmas options, i.e. Christmas trees, Reindeer, Wreaths… Remember these will be done in a white wood, so if you want the Padauk wood you will have to cut them yourself.
To hold the candle, cut a piece of maple to the size specified in the cut list. Using a 1 ½” forstner bit, drill a hole in the center of the piece. This can go all the way through or not, depending on the depth of your tea light. Ensure the tea light you purchase will fit in the hole. I have had issues with them being a bit too large. Glue the candle base to the bottom back of the tree ensuring bottoms are flush.
Once your tree/candle holder is dry, scrape out any glue squeeze-out, lightly sand and apply 2-3 coats of polyurethane. Finish sand the tree/candle holder prior to attachment. Attach with the Gorilla Super Glue in the center of the roof gable area. Since you have applied finish already to the entire calendar, standard wood glue won’t adhere properly.
Step 18: Install Keyhole Plug for Hanging
Once the assembly is dry, you will need to install the keyhole slot plug for hanging the calendar on the wall. I like the brass Keyhole Slot Plug from Lee Valley. Mark your drilling spot, 2” down from the top roof peak, centered on the back. With a 5/8” forstner bit, drill a hole 5/16” deep. Make sure you don’t push too hard and go through the roof gable. Glue the keyhole plug in place with Gorilla Super Glue ensuring correct orientation.
Step 19: Final Spray Finishing Entire Calendar
Now it’s time to do the final spray finish of the entire calendar with another one or two coats of the polyurethane. Since the inside of each compartment was finished prior to cutting and assembly, you only have to worry about the outside and roof assembly. Two coats on the inside of the compartments is more than satisfactory. The number of extra coats you do in this step is completely up to you. As mentioned earlier, this can be done by spraying or by hand. If you still have any imperfections you can finish rubbing out with 0000 steel wool. I don't spray the back since the hardboard is pre-finished when you purchase from your local store.
Step 20: Relax & Enjoy
Stand back and admire your finished product. Remember, if you don't want to make this yourself, you can buy the finished product on my Etsy store.
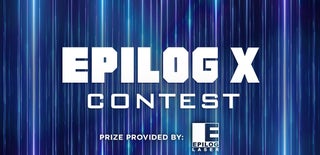
Participated in the
Epilog X Contest