Introduction: Xylophone
I have two beautiful nieces that I love very much. At the moment they are 1 and 3 years old. That is such a fun time for Christmas presents. For the three year old, she is crazy excited to open all of her gifts no matter what they are. She is at that age where she gets super excited about everything. Also, she is still young enough to enjoy homemade presents so I am going to take advantage of that.
Unfortunately there will come a time when homemade toys will become less desirable then the cheap plastic ones. I get it, these are not as flashy or loud and as you get older, the stimulation you get from these kinds of toys is somewhat important.
But luckily for me they are still young enough where any toy is fun. So I wanted to make something that they could use their imagination to play with. Something that would out last those cheap plastic toys. The younger of my nieces loves to bang on whatever she can get her hand on. So I thought a xylophone would be perfect.
Although I know there will be a time when this will go into the toy box or attic and not be seen for years, when it comes out again hopefully it will look the same, work the same and be more loved than it was in the beginning.
So here it is, my wood xylophone. I hope you enjoy this instructable and give it a try. After all, the very best gifts come from the shop... I mean heart... Same thing.
Unfortunately there will come a time when homemade toys will become less desirable then the cheap plastic ones. I get it, these are not as flashy or loud and as you get older, the stimulation you get from these kinds of toys is somewhat important.
But luckily for me they are still young enough where any toy is fun. So I wanted to make something that they could use their imagination to play with. Something that would out last those cheap plastic toys. The younger of my nieces loves to bang on whatever she can get her hand on. So I thought a xylophone would be perfect.
Although I know there will be a time when this will go into the toy box or attic and not be seen for years, when it comes out again hopefully it will look the same, work the same and be more loved than it was in the beginning.
So here it is, my wood xylophone. I hope you enjoy this instructable and give it a try. After all, the very best gifts come from the shop... I mean heart... Same thing.
Step 1: What You Need
Some thin wood scraps
I used oak cherry and walnut
Miter saw
Bench sander
Spindle sander
Drill press
Felt
Small pegs
Wood Glue
I used oak cherry and walnut
Miter saw
Bench sander
Spindle sander
Drill press
Felt
Small pegs
Wood Glue
Step 2: Cut Some Wood
I had a bunch of extra wood left over from my wood rug project. I had to cut a lot of long skinny pieces for that and they worked perfect for the xylophone. I Used cherry walnut and oak because I wanted the contrast in the wood to look really cool. In the end, I did look great but the different woods makes tuning the blocks difficult.
I started by cutting my longest piece at 9 inches. I cut a total of seven pieces and I cut each one 1/2 inch shorter than the last. When I was done the longest was 9 and the shortest was 6 inches. I played around with different cut lengths but his one looked best in the end.
After I had them all cut, I rounded the blocks with the bench sander to make sure that getting a silver would be impossible.
I started by cutting my longest piece at 9 inches. I cut a total of seven pieces and I cut each one 1/2 inch shorter than the last. When I was done the longest was 9 and the shortest was 6 inches. I played around with different cut lengths but his one looked best in the end.
After I had them all cut, I rounded the blocks with the bench sander to make sure that getting a silver would be impossible.
Step 3: Tune the Blocks
I was unaware of this before but it turns out that correctly tuning the blocks is essential in making a working xylophone. I am by no means an expert but I will explain how I did it as well as I can.
Like I said before, each block was cut a half inch shorter than the one before. I thought that the length of the block would have the greatest effect on the tone that it makes but I was mistaken.
Turns out that is it the groove in the bottom of the block that determines the tone. I used my spindle sander to make the grooves in the blocks. I started out sanding everything but the outside inch and a half. This gave each one different tones but not enough to sound pretty.
The more you take off the bottom, the lower the tone will be. I made a small stand to check the tone. It was just some scrap wood sticking up with rubber bands stretched across. I would lay the blocks across the rubber bands and see how it sounded. If it sounded a little high, I would take more off the grove. If it sounded too low, I wound take a little off the end of the block with my bench sander. Some people really go all out and use a tuner to get it perfect but I did not. Maybe for my next one. Once you have everything in a descending tone, you can attach them.
Like I said before, each block was cut a half inch shorter than the one before. I thought that the length of the block would have the greatest effect on the tone that it makes but I was mistaken.
Turns out that is it the groove in the bottom of the block that determines the tone. I used my spindle sander to make the grooves in the blocks. I started out sanding everything but the outside inch and a half. This gave each one different tones but not enough to sound pretty.
The more you take off the bottom, the lower the tone will be. I made a small stand to check the tone. It was just some scrap wood sticking up with rubber bands stretched across. I would lay the blocks across the rubber bands and see how it sounded. If it sounded a little high, I would take more off the grove. If it sounded too low, I wound take a little off the end of the block with my bench sander. Some people really go all out and use a tuner to get it perfect but I did not. Maybe for my next one. Once you have everything in a descending tone, you can attach them.
Step 4: Set the Blocks
This process is really pretty simple. The main goal here is to not let the blocks come into direct contact with the rail. This will ensure that you get the best sound out of your blocks. Also, I have been using the word "block" to explain this throughout this ible but I'm not sure if that is actually want there are called. Hope you still understand what I mean.
First I drilled 7 holes into the rail the same size as the pegs that I planned on using. I made sure that I didn't drill the holes too deep. I wanted the blocks to be loose even when the pegs are glued into place. Then I drilled holes in each side of the blocks. That hole was one size larger than the pegs that I picked up at menards.
I used some adhesive backed felt to make sure that the blocks were not in contact with the rails. I punched a hole in them and stuck them to the rail. I slid the pegs through the blocks and glued them into the rails.
First I drilled 7 holes into the rail the same size as the pegs that I planned on using. I made sure that I didn't drill the holes too deep. I wanted the blocks to be loose even when the pegs are glued into place. Then I drilled holes in each side of the blocks. That hole was one size larger than the pegs that I picked up at menards.
I used some adhesive backed felt to make sure that the blocks were not in contact with the rails. I punched a hole in them and stuck them to the rail. I slid the pegs through the blocks and glued them into the rails.
Step 5: The Mallet
For the mallet I didn't want just a plain old boring one. I glued two pieces of cherry together and let it sit overnight. I drilled a hole for the dowel and then I took it to my bench sander and gave it all sorts of weird angles. There was really no rhyme or reason to this. I kept sanding until I saw something that I liked.
I glued the dowel in and that was it. A custom mallet that works well and looks really cool.
I glued the dowel in and that was it. A custom mallet that works well and looks really cool.
Step 6: Conclusion
My one year old niece opened this Christmas afternoon and it was a big hit. She loved banging and the blocks and hearing the sounds that she was making. The adults seemed to have a good time with it as well.
If I were to do anything different, I would take more time tuning the blocks. I was in a bit of a hurry with Christmas right around the corner and a few gifts left to make so I hurried that step and i regret it. With a small amount of work, you can tune the blocks to sound close to perfect... Next time.
Thanks you so much for reading about my xylophone. I hope you give this project a try. It wasn't a difficult project and turned out great. I would encourage everyone to give a homemade gift a try at least once. It is definitely more difficult than picking something up at the store, but it's also much more rewarding. Thanks again
Andy
If I were to do anything different, I would take more time tuning the blocks. I was in a bit of a hurry with Christmas right around the corner and a few gifts left to make so I hurried that step and i regret it. With a small amount of work, you can tune the blocks to sound close to perfect... Next time.
Thanks you so much for reading about my xylophone. I hope you give this project a try. It wasn't a difficult project and turned out great. I would encourage everyone to give a homemade gift a try at least once. It is definitely more difficult than picking something up at the store, but it's also much more rewarding. Thanks again
Andy
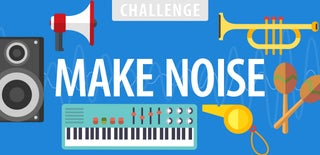
Grand Prize in the
Make Noise Challenge