Introduction: Wood and Resin Light
When you build strong relationships with the local community around you, that is when you get given hidden gems like I did with the completely ant riddled and obliviated piece of hard maple. One of my local sources for wood stumbled across a piece of maple found while slabbing out a full maple tree and knew it would be something that I not only would appreciate, but that I would put to use, and he was right. I had been keeping an eye out for a piece that I could use to make my first wood and resin LED Light, and this was the piece!
Step 1: Design
Besides knowing that I wanted to fill the wood with resin and put an LED light in it, I had no idea what to do as far as design right away. I took some time, did some research on Pinterest and YouTube just looking at other wood and resin LED lights to see what kind of style I liked. Then I did some free hand sketching on my computer just to get a general idea of what I was going for. I was going to have the maple and resin light sit on end, with an LED strip going up into the piece. To help dissipate heat from the LED and have it give off more light I would cut slots into the finished piece.
Step 2: Wood Prep
The piece of maple did not sit flat on either end, so the first step of prep work was to cut one end flat with my bandsaw. Next, I drilled a hole for the LED strip lights. I used a 5/8ths inch drill bit to make a large enough hole to place a tube and the light strip in. Because I wanted the tube and lights to go throughout the majority of the piece, I used a long drill bit that did not fit into my cordless or corded drill, so I had to use my manual drill to get the job done. Once the hole was drilled, I used my handheld Dremel tool to remove any of the totally decayed and loose pieces within the maple piece before pouring the resin.
Step 3: Resin Pour Prep
I wanted to leave the piece intentionally not square, it seemed more organic and natural that way. Because of this design choice though, building a mold with melamine was really out of the question. I decided to try using carpet protection film that they sell in big rolls. I reinforced it with blue painters’ tape to try to keep the sides from bowing out when it was filled with resin.
Step 4: Resin Pour
So, looking at the piece of maple I totally got an ocean waves vibe from it and wanted to carry that vide through stronger with the resin. I went with a mostly blue tinted resin with a little bit of blue/green glow in the dark resin. Now, in my head, I wanted the glow in the dark resin to be in different spots throughout all of the blue, that’s why I poured some blue, then glow in the dark, then more blue and so on and so forth. Unfortunately, in the end, all of the glow in the dark resin sank to the bottom and concentrated in just one place. Also, as I was pouring, it became clear that the painters’ tape was not going to be strong enough to hold the resin in without bowing. So, I quickly grabbed some scrap wood and clamps and placed them along the middle section which was the place with the least amount of support.
Step 5: Fixing the Bubble Explosion
The type of resin that I used for this project was not meant to be poured at the thickness it was poured at. I originally thought it would still be okay to pour it because there were so many various cavities being filled that I thought the wood that would be internal provided enough of a break up that it would be okay. Boy, was I wrong! Since it was so thick, it overheated and created a huge bubble explosion along with several internal cracks. Consider this a major lesson learned.
So, the idea of sanding through all of the bubble seemed a bit less then appealing. After a bit of thought, I decided to shave off the layer of bubbles with my bandsaw. Using the bandsaw instead of sanding definitely saved a great deal of time.
Step 6: Final Shaping, Sanding, and Resin Fix
Once the bubbles were taken care of, I used my angle grinder with the turbo plane attachment and the belt sander to create more of a natural edge and surface. Using the bandsaw had left the piece square and flat on all four sides and I wanted the piece to have a more organic look to it. After the final shape was reached, I sanded to 180 grit. At this point the cracks in the resin, from it overheating during the cure time, became very evident.
Though I could not totally erase the cracks, I could make sure they were stabilized so no further cracking could happen and so the resin would not loosen and fall out. I used just a two-part quick set epoxy that I picked up at Lowes. The epoxy I used had a 5 minute set time, and 24 hour full cure time.
Step 7: Set the Light Free
I decided to put the strip LED light in to see how well it came through the tinted resin and found that it didn’t shine through as much as I had hoped for. To address this issue, and to also help with some possible heat dissipation issues, I decided to cut some slots in the light piece. I used my miter saw to cut the slots, which would just be the width of the saw blade. I made sure to go deep enough to go through the channel that was there for the LED light strip.
Step 8: Finish and Lighting
After the slots were cut, I sanded inside the slots and the rest of the light up to 600 grit. Then I went with a brush on lacquer finish. I used a disposable foam brush to apply the finish.
Once the finish was cured, I inserted the LED strip light. To keep the strip light inside the channel I just applied a bit of hot glue. This allows for fairly easy change out of the lights when they do burn out.
Step 9: Conclusion
This was my first wood, resin, and LED light. My only so far. Even though I learned some hard resin lessons, I am still very happy with how this light turned out and I am looking forward to the opportunity to make another one. I just need to find that perfect piece of wood for it!
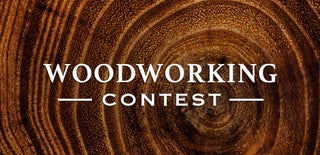
Participated in the
Woodworking Contest