Introduction: Wooden AT-AT Walker
This is a scale Wooden AT-AT Walker from Star Wars that I made as a gift for my kids.
It is made almost entirely from scraps of Baltic birch plywood, and is 20 inches tall (about 51 cm).
Here are some of the features:
- fully poseable
- pivoting "gull-wing" main doors, just like in the movie (wait, that's Back to the Future)
- removable magnetic wall panels
- articulating neck/cockpit tunnel
- cockpit hatch
- LEGO panels in the body and cockpit
- weighted feet
This was made completely by hand with common woodworking tools (no laser cutters, etc.)!
I designed, scaled-up and hand-drew all of the individual pattern pieces as well. I thoroughly enjoy the non-computer, pencil and paper process . . . what can I say.
If you're feeling ambitious and have access to some woodworking tools, hopefully this will help you build a wooden AT-AT Walker for yourself. I've shared my hand-drawn templates in Step 3 as a PDF.
Enjoy!
Step 1: Possible Poses
The Walker is unwieldy when the joint bolts are loose, but the whole thing is quite sturdy once they are tightened.
Step 2: Breakdown
The completed AT-AT Walker can be broken down into 29 separate parts (cockpit and body were permanently joined after the 2nd photo was taken).
The walker consists of 274 individual wooden pieces, 12 movable joints made with 1/4" bolts, and 20 pin hinges made from bits of metal rod. I used almost every tool in my little garage shop for this, as well as almost every kind of adhesive I had.
Here are the tools you will need to complete a project like this:
- band saw
- scroll saw
- drill press
- oscillating sander
- lathe (optional)
- power carving tools or other means to shape some oddball pieces
- rotary tool
- clamps (lots of small spring clamps, and a few bar clamps)
- miscellaneous hand tools
- optional: table saw, jointer, planer (I used mine for a couple things, but you could do without)
I've shared a lot of little tips and tricks in the photo notes, so be sure to look at all the photos.
Step 3: Planning and Templates
I began this project by gathering up all of my scrap Baltic birch plywood to see what I had to work with.
The sizes I used are 9mm and 15mm. I also used two full sheets of 12" by 24" 3mm craft plywood, which appeared to also be birch.
After getting some AT-AT Walker images online (thanks wookieepedia), I set about designing how everything would function and scaling up the various pieces with paper, pencil, rulers, compass, and calculator.
All of my templates are metric, but any hardware I used was standard, so you'll see a mix of both in the templates. If anyone needs proof that the metric system is superior to standard, just try building any scale model with inches. It would be ludicrous!
I find working out the details on paper and hand-drawing plans for things like this incredibly enjoyable for some reason. Craziness, maybe?
The completed templates were then scanned and printed onto 110 lb. cardstock. The individual pattern pieces were cut out with an x-acto knife to use as stencils (since there are many duplicate pieces made from the same pattern pieces).
Linked below are scans of all of my templates, other guides, and miscellaneous bits that I made along the way. They are not perfect and you will still have to do a fair amount of improvising, but these templates will at least get you going in the right direction.
They are shared for non-commercial use only.
Attachments
Step 4: Scroll Saw and Band Saw Time
I began by tracing the stencils for the various leg pieces, and started cutting out all the pieces. I used my band saw for most of the 15mm parts, and the scroll saw for the 9mm and 3mm parts.
It is essential that these saws are dialed in fairly well and the tables level, with the blades making perfect 90 degree cuts.
Step 5: Drilling Perfectly Centered, Clean Holes
Anywhere I needed holes drilled, I used a nail punch to put a little dimple in the correct location.
With my drill press I pre-drilled every hole with a 1/16" bit precisely in the dimple all the way through the piece, which provides a guide hole to help center the forstner bits I used to bore the completed holes. Regular twist bits are not good for making this kind of clean, precise holes.
With a forstner bit, bore the hole halfway down, then flip over the work piece. Then with the help of the 1/16" guide hole, finish drilling the hole. This results in perfectly clean holes with no blowout.
For all of the joint bolts, I used 1/4" bolts that were threaded into toothed t-nuts that were Gorilla-glued in place in the receiving ends of things. (Photos along the way will show this in more detail.)
Like the band saw and scroll saw, it is essential that your drill press table be perfectly level for work like this. If needed, be sure to fine tune it before you get started.
Step 6: Power Carving the Feet
This step could be simplified with a lathe. But I don't have a lathe, so the pieces had to be carved instead.
The layers of the feet were cut out and glued together. A bolt was used to center all the pieces and apply clamping pressure.
They were then carved down with a power carver and sanded smooth with a drum sander on my rotary tool.
Step 7: Add Weight to Feet
I wanted the feet to be as heavy as possible. I went to a local tire store and asked for some used lead tire weights. They led me to a bucket and said "help yourself."
Rather than try to melt the lead down, I just broke off the leady chunks from the steel clippy parts, and filled up the feet with these bits. Then I filled all the cavities around the lead with hot glue, and glued & screwed the bottom pieces of the feet in place. Each completed foot weighed about 13 ounces.
Step 8: Leg and Feet Pieces
Here are all the leg and feet pieces up to this point. I thought I was making progress, but I had no idea how much work lay ahead . . .
Step 9: Glue Up Leg Parts
The various leg parts were glued together with wood glue, and clamps.
T-nuts where fastened into the correct pieces. The ones I used were the kind with spiky teeth, but I added Gorilla glue to reinforce the bond. Drilling out the holes for the t-nuts was done very carefully at the drill press to ensure precise holes as needed.
Step 10: Carve Leg Bottoms
The leg bottoms were carved to match the shape of the AT-AT Walkers in the movie.
Carving plywood allows you to cheat because you can gauge depth and shape based on how the plies look.
The plywood creates a neat effect, but I think using hardwoods would provide a better look, ultimately. Live and learn.
Step 11: Greebles, Greebles!
"Greebles" are the surface details that provide visual interest.
For these knobby leg discs, I used a paint stir stick and cut out nickel-sized circles. These were glued in place.
Glue Tip! For gluing little bits like this where clamping isn't ideal, I put a very thin film of wood glue on both surfaces to be joined. ("Thin film" means a fully covered surface, but not enough to allow any noticeable squeeze out when the parts are put together.) Then I wait about 30 seconds for the glue to get tacky. When you stick the pieces together and hold for another 30 seconds or so, they stick with no need for clamps.
Step 12: Joint Knobs/bolts
For all of the joints, I made fancy knobs to match the Walker's joints, with 1/4" bolts and thin plywood. The bolt heads were carefully epoxied into bored-out areas.
All of these pieces were cut out very carefully using a scroll saw.
Step 13: Epoxy Bolt Heads
To make this job cleaner, I first applied masking tape over top of the knobs and the hole where the bolt heads would sit. I trimmed away the tape over the hole with a hobby knife.
The bolts were slid into the holes so the heads sat just about 1/4" above the head-holes. 2-part epoxy was added just under the heads, and they were pulled down into place. Then the tape was removed.
The trick here is to make sure the threaded section of the bolts are perpendicular to the round wooden knob parts. If they are not, they will have to be remade. I had to remake a couple of these, as I wasn't paying close enough attention until after the epoxy had set. Wobbly knobs are no good!
Step 14: Undercarriage
I'll call this the undercarriage of the body. This part holds the hip pieces, which hold the legs, and connects them to the main body of the Walker.
There weren't a lot of reference photos or images for this area of the AT-AT Walkers, so I improvised based on what I needed. This part has four embedded bolts which the hip pieces are fastened to.
Simple knobs were made with plywood and t-nuts to tighten against these bolts. See fourth photo for how those were made.
Step 15: Undercarriage, Cont.
The undercarriage got some fancy bits to make it look more engine-y. This was all improvised, but I like the way it turned out.
Step 16: Leg Details
Various bits were added to the upper legs.
The side details needed to be flush with the back, so to add these I had to route out a good-sized glue area to hold them.
Step 17: Body Base
The base plate for the body was cut from 15mm plywood.
Note the specific bevel angles as mentioned in the photo notes.
Step 18: Compound Angles
This is where my brain started to get a real workout.
Side angles plus all kinds of bevels going this way and that. Yikes.
After some sketching and head scratching, I had a plan that worked out pretty well. The angles were close to what was needed coming off the band saw, but there was quite a bit of fine-tuning required using my oscillating belt sander. This is the one I have, and from what I've seen, most other home woodworkers do as well. It's the only thing of it's kind, and an incredibly useful tool to have.
A bevel gauge will be very handy at this point, as you can just match the angles from the plans and transfer them to the wood pieces. Then set your saw tables to match, and you can avoid having to fuss over numerical angles like I did.
Step 19: Undercarriage to Base Plate
The undercarriage was glued to the base plate, and a few screws were added through the base plate from the topside to reinforce the connection. This was very carefully and precisely located. It would be very bad to put this on all skee-wompus.
Step 20: Support Stand
At this point I needed to make a little stand to hold the base and undercarriage while I worked on it. This was made from cheap 3/4" pine plywood.
Step 21: Glue Up Body Frame
The body frame was glued up a this point. Screws were also added from the underside.
Front and back roof pieces were added, with skylights built in. These were improvised features on my part, but the holes double as nice little handles for carrying the Walker.
Step 22: Gull-wing Doors
I wanted this AT-AT Walker to be cool. So, inspired by Doc Brown's Delorean, I decided to make two main access doors at the center of the body that raised up like the gull-wing doors.
I wasn't sure how I was going to attach them at this point, but was vaguely planning on using a piano hinge. In the end that didn't work, and I had to make built-in wooden hinges. These were a better option, and look so cool. More on those later.
Step 23: Wood Burning, Lacquer, and Hinge Pins
I used a wood burner to add lots of little surface details.
It's a unique look, and I was a little hesitant to commit to it. I had never done any wood burning before, so I made a lot of mistakes. But the mistakes blend in pretty well and just look like intentional blemishes!
I used various tips from a basic wood burning kit to try out different effects, and also a propane torch to darken the edges and create some shaded corners and such.
All the pieces were then coated with several layers of semi-gloss spray lacquer, with a light 220 grit hand sanding in between coats.
Various bits of metal rod were used to create hinge pins for the feet and ankle pieces. To install these, I used tape and shims support the pieces that were to be joined very securely, and then drill out the holes where the pins would go. See notes in photo two for more details.
Step 24: Gluing in LEGO Plates
I swiped a few tan colored ground LEGO plates from my kids' stash of LEGO and glued sections of these down to the base of the body.
To do this, I used contact cement AND spray adhesive. The contact cement is brushed on in areas where spraying isn't an option. I waited about 15 minutes, and then sprayed the spray adhesive on the bottoms of the plastic parts. I waited about 30 seconds and joined the pieces to the wooden base.
They stuck like . . . glue.
I picked up this gluing technique from Drunken Woodworker. It's a fantastic trick.
Step 25: Attach Access Doors
To attach the main access doors, I had to modify them and create some built-in wooden hinges. These were glued and screwed in place, and then finished to match the rest of the pieces.
The doors were positioned and fastened temporarily with masking tape where they needed to be. Then I carefully drilled out holes and installed little hinge pins made from short pieces of metal rod. A bit of super glue was added to the pins just to the outside flush parts to hold them in place.
Step 26: Removable Magnetic Wall Plates
I made the remaining four walls of the body from 3mm plywood. Small neodymium magnets were epoxied into bored-out holes, which will line up with screws placed into the body frame.
Step 27: Wall Plate Details
The details of the wall plates were added with the wood burner and propane torch, and then the pieces were lacquered.
Step 28: Tail Section
I couldn't find many photos or images that detailed the rear section very well, so I just kind of made it up. Even watching and pausing the AT-AT scenes in Empire Strikes Back didn't offer much help.
It seems logical that this is an exhaust-type area on the vehicle, so I went heavy handed on it with the blow torch. Additional notes in photos.
Step 29: Cockpit
The cockpit was built in a similar fashion as the body.
A pattern was made, and pieces were cut out and glued up. A top hatch was created with hinges similar to what was done on the body.
I learned a lot when doing the body section, so this cockpit was noticeably easier as I knew what to expect, and what dumb things to not repeat!
Step 30: Red Bull Windshield
Is it a windshield? Polarized Empire-approved visor?
Nobody knows. I made it out of a piece of shiny red soda can. This little piece was glued in place with contact cement. The piece it was glued to was made from a small bit of maple.
It has a shiny, metallic red color which wouldn't have been possible with paint. It really pops!
Step 31: Cockpit Details
This was a fun part for me. I was in the groove now, and familiar with some techniques that worked well for the body.
For the cockpit details, various bits of wood were cut, glued up, sanded and glued in place.
Never underestimate the effectiveness of a stencil. They take time to make, but speed up the process immensely overall.
Step 32: Thoughts?
What do you think?
Better with the burned weathering/wear and tear, or better without? Let me know in the comments!
Step 33: Articulating Neck
I really stewed over how to do the neck the whole time I was working on all the other parts. I just couldn't figure out how I would make it. I considered many approaches, but none of them seemed likely to work or look the way I wanted.
In the end I finally decided to layer up rings of plywood, with a beveled piece in the middle attached with hinges. This allows about 40 degrees of movement side to side.
On the body-end of the neck I made the juncture able to swivel. I like the way it looks and works!
See photo notes for details.
Step 34: Neck to Cockpit
The neck was glued into the head/cockpit, making sure it was lined up vertically.
Step 35: Neck to Body
The neck was screwed to a retaining ring inside the body of the Walker.
I wanted the neck to still work like a tunnel, so my kids could slide LEGO men in and out of the cockpit.
Step 36: Assemble!
I found it most easy to assemble the AT-AT Walker upside down.
Without legs it looks like some kind of funky woodpunk bug. That'll be a future instructable. Maybe.
Step 37: All Done
This was a challenging project that really stretched me. I'm going to try to avoid overly complex projects like this for a while . . .
If you make one, let me know!
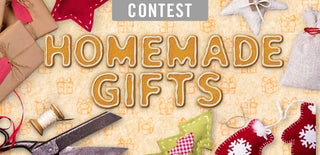
Participated in the
Homemade Gifts Contest 2015
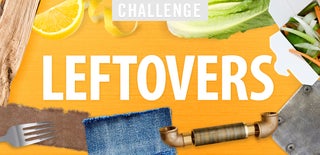
Participated in the
Leftovers Challenge
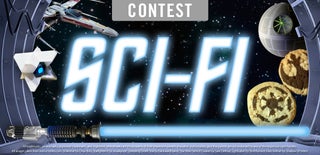
Participated in the
Sci-Fi Contest