Introduction: Wooden Computer Keyboard by Steve M. Potter
I decided that I deserve a keyboard that I really adore, since I spend most of my workday at the computer. You can buy gorgeous office desks, chairs, wooden pens and beautiful stationery. Why is it that keyboards are all plastic and ugly? I always liked the feel and sound of the old IBM-AT clicky keyboards. These have the "buckling spring" mechanism that is very strong and never wears out. But aesthetically, beige plastic – Yuck! So I decided to take the mechanical and electronic guts of a clicky keyboard and install them into a home-made wood version. This turned out to be a long and tedious art+engineering project, and I will spare you some of the missteps I made, describing here what worked. In the end, I have a very solid, completely functional beautiful wood keyboard that I use every day at work. The keyboard even survived dozens of kids pounding on it at the Atlanta Maker Faire, where I had it hooked up to my laptop for people to try it out.
There are many artistic or aesthetic decisions I made that you may not have, and which involved a lot of extra work, such as dyeing the function keys according to the resistor color code, or using Scrabble tiles for the letter keys. But these were important for me to really love it, and to think of it as an art project, rather than just a tool I use to type at work. If you do decide to make your own wooden keyboard, I encourage you to add your own artistic touches and post them here! Also feel free to add your comments and ideas to this Instructable.
Step 1: Materials and Tools Needed:
Materials:
- A donor keyboard whose mechanical action you love. [Unicomp sells new ones, or you can find one surplus. This Instructable uses the “buckling spring” type keyboard that makes a tactile click each time a key is pressed. ]
- PS/2 to USB converter if you use an old keyboard as the donor
- A plank of nice wood to form the body of the keyboard
- Dye or stain appropriate for your keyboard body
- (1) 3/4" x 36" maple dowel
- (1) 3/4" x 36" square poplar rod
- (1) 5/8" x 36" square poplar rod
- 1mm thick wood veneer (around 1 sq. ft.)
- 6" of stainless steel tubing (~1cm, but diameter depends on your donor keyboard)
- Small sledge hammer
- Letter tiles from a game of Scrabble
- Clear label tape
- Thick CA glue
- Weldwood contact cement
- Envirotex Lite Pour-on Epoxy
- Stirrers and 30 mL mixing cups
- Modeling clay
- (3) Sugru rubber glue, any color
- LED
- Flexible wire from headphones
- A rainbow of wood dyes
- Disposable left-overs containers for mixing dyes
- ~1cm thick piece of lucite
- Scrap wood pieces
- Large pieces of paper or cardstock for templates
- Felt or fleece for the underside
- Scotch tape, normal and permanent double-sided
- Plastic wrap
Tools:
- Power hand planer
- Router or mill
- 1/2” Forstner bit, to cut flat-bottom holes
- Various drill bits
- Grinder or grindstone
- Bandsaw, reciprocating saw, jigsaw or coping saw
- Belt or disk sander
- Dremel and/or Foredom tool with sanding, cutting and carving fittings.
- Labeler
- Screwdrivers
- Heat gun
- Long-nose and rubber-jaw pliers
- End- or angle-cutter pliers
- Calipers and rulers
- Sandpaper and sanding block
- Drill press or lathe/mill combo
- Sponge
- Soldering iron and solder
- Hot knife
- Various clamps
- Razor or X-acto knife
- Tweezers
- Pencil
- Safety equipment: rubber gloves, leather gloves, earplugs, goggles or face shield, organics absorbing respirator.
Step 2: Get a Clicky Keyboard.
I got a brand new clicky or tactile (buckling spring mechanism) keyboard from Unicomp (http://pckeyboard.com/page/category/SpacesaverM) , model Spacesaver M, which works with Mac computers. I believe they bought the original molds from IBM for the base, and added updated electronics (for USB interface) and a pretty lame plastic shell (compared to the bomb-proof and heavy old IBM keyboards). As these clicky keyboards have become kind of trendy, these are not as cheap as a couple years ago when I bought mine. So to save money you may want to find an actual old keyboard from surplus or a garage sale, and use a PS/2 to USB converter instead.
Take photos of the keyboard before removing the keys, so you can remember which key goes where.
Remove the cover, and use the top to create a paper template by tracing it and cutting out the paper template with a razor or X-acto knife. This can be used to mark up the block of wood once it is planed down to the right thickness.
Pluck out all the keys carefully using long-nosed pliers, and save them all. Also make a note of and maybe photograph how the key stalk looks in relation to the key it is attached to. Memorize which side of the stalk points North, which points South. Don't allow any springs to get damaged or unhooked from the base. When inserting keys later, make sure the spring goes all the way up the inside of the stalk for proper Buckling Spring action. Store the base somewhere it will not get dust in it, and the circuit board will not be damaged by static electric discharge.
Step 3: Get a Large Plank of Nice Wood.
I am very lucky that one of the best woodworking shops in the US, Highland Woodworking (formerly, Highland Hardware), is just a mile away from our house in Atlanta. They do have an online store: http://www.highlandwoodworking.com/
But nothing beats actually seeing the material. I chose a very solid, dense plank of cherry wood for the body of the keyboard. It was dried and roughly planed, about 50mm thick. Probably any wood would do for the body, with softer woods (pine, cedar) being much easier to carve and sand than hardwoods like cherry. But be sure it is dried and acclimatized to your local humidity, so that it does not change shape later from drying or taking on moisture. Look carefully at the wood grain, and choose the section that appeals to you and hopefully does not have any knots. Knots are very hard to carve so avoid them if possible. Using the width of the keyboard guts you have acquired (next step) as a guide for length, cut the plank the the right length (and width, if it is too wide). Draw a curve on one end, trace that onto paper, cut the paper along the curve, and flip the paper over to trace a symmetrical curve on the other end. Cut along these curves with a reciprocating saw, bandsaw, jigsaw, or coping saw.
Step 4: Plane the Body Down to Form a Wedge.
Pay attention to ergonomics when shaping the body of the keyboard. You want your wrists to be straight when typing. As you can see in my end-view drawing, I decided that a 56mm hand rest was about right, with a gentle slope up to the full 47mm thickness of the plank. Use a powered hand planer to remove lots of wood to form this wedge shape. Only take a couple mm off per pass and keep measuring the thickness to make sure you are doing it evenly. To clean up and further shape the plank, I used a Foredom tool (like a Dremel, but with a pedal for speed control, and with a heavy-duty motor at the end of a flexible shaft) with a drum sanding wheel attachment.
Step 5: Route Out Holes for the Keys.
Mark the locations of the holes through which the keys will protrude, using the paper template you made earlier. Use a plunge router (carefully!) to remove wood where the holes are. If you have a mill, that would be even better. You could also use a drill press. Be sure to clamp the piece down firmly when doing routing, and wear a full face shield and earplugs. Use a smooth piece of wood or metal as a guide for the router to butt up against, that you can clamp at different locations for different edges to be routed.
Step 6: Carve Out the Underside.
Use the keyboard guts as a guide to know what shape needs to be cut out to accommodate them. Use different sized carbide cutting attachments and drum sanders on the Foredom tool to carve out the underside, and to shape the top to your liking. You will need about 3mm of clearance between the inside edges of the body and the plastic cylinders around which the keys will sit.
Step 7: Finish Shaping and Sanding the Body.
Use the drum sander attachments, sanding blocks made of dense felt, or sanding foam bars, and lots of hand sanding to shape the frame until it is the shape you want it, with no sharp edges. Practice using any new tools or attachments on scrap wood of the same type before you use them on your precious keyboard body. Hand sand the body with coarse sandpaper to get rid of any marks made by the shaping tools. Use progressively finer grits to get rid of scratches made by the coarse paper. There are no shortcuts here, just lots of manual labor. The more you put into this step, the nicer the finished product will look.
Sponge the body with water when you think you are done, to raise the grain (make little wood fibers stick out). When it dries, sand off the tiny hairs with fine sandpaper. You are done when it is extremely smooth and shows no scratches or marks when wet, and remains smooth after it dries.
Store the body in an environment with a similar humidity to where it will be used while you now go to work making the keys.
Step 8: Punch Out the Key Stalks.
Using a piece of stainless steel tubing of the right diameter (it should fit inside the plastic cylinder on the underside of each key), make a tool to punch out the key stalks from the plastic keys. Sharpen the end on a grinder, and use a thin cutting wheel on a Dremel or Foredom to cut two slots as shown.
Write down the widths of all the non-square keys (at their widest point) before you do the next step.
Punch out the key stalks OF ALL THE SINGLE-STALK KEYS ONLY against a hunk of lead or wood so as not to make the tool dull. Use a heavy hammer for this. Plastic may go flying, so wear goggles. Pop out the stalk by shoving a pen or dowel into the back end of the tool. This will be nearly impossible if you did not make the slots that allow the inside diameter to expand a tiny bit. Do not lose any key stalks. Treat each one like the precious piece of precision engineering that it is.
Do not punch out stalks from the special keys that have two stalks, like zero, Enter, Return, etc. Put them aside for later.
Step 9: Cut Tops Off the Key Stalks.
With good ventilation, use a hot knife (attachment for a wood burner tool) to slice off the tops of the keys from the stalks. In retrospect, it might have been better to do this by sanding off most of the top on a belt or disk sander, and leave some thin remains of the round key top on the stalk, for a firmer glue bond to the wood keys. But I cut them all off. Try to cut perpendicularly to the stalk, as close as possible to the top being removed. Some stalks I cut too much off the top, and these were useless. I had to mine another keyboard for additional keys. You will sand them a bit later so don't worry if you did not cut perfectly perpendicularly.
Step 10: Cut and Drill Key Blanks From Dowels.
I decided to make all printable character keys (letters, numbers, punctuation) round (or oval), and all functional keys rectangular. I decided the space bar is not a printable character; I realize that is debatable. Feel free to do what works for you aesthetically.
Cut a 3/4" (19mm diam.) maple dowel into 14mm length cylinders for the 26 letter keys, using a miter saw or other means to be sure the cuts are perpendicular. I used a bandsaw with the dowel held in a jig that slides on its table's rails.
The non-letter keys (numbers and punctuation) are comprised of veneer and maple dowel pieces that are longer than they are for the letter keys: 19mm (3/4") long.
For all these round keys, put them in a lathe chuck, with a 1/2" (12.8mm) Forstner bit in the tailstock, and advance the tailstock into the key blank to drill a flat-bottomed hole 9mm deep. Put a mark on the bit with a Sharpie or paint pen so you know how deep to drill. You could do this step with a drill press, but using a lathe ensures that the hole is centered on the key (and is perpendicular to the cut end).
For the F keys at the top of the keyboard, I cut a 3/4" poplar rod into nearly-cube shapes that were only 17mm wide, and 19mm = 3/4" tall and thick.
For the rectangular functional keys, I used a 5/8" square rod of poplar, though other types of wood would work. They will have maple veneer glued to the tops. Cut out pieces of this square rod with widths to match the list of key widths you wrote down earlier for the non-square keys. Also cut the appropriate number of square ones. Mark each key with its identity: Write on each key's underside near the edge that will be closest to the typist, which key it is. Don't put the ID mark where there will soon be a hole drilled. Some keys will be only slightly different sizes and you don't want to mix them up.
Mark where holes go on the underside of all the rectangular keys using the keyboard base, (and your photos of where the keys go) as a guide. As shown in the photo, draw a line to help ensure the hole is drilled equidistant from the edges. For the square keys, you can draw an X from the corners to center the hole.
Drill holes 9mm deep in all the square and rectangular key blanks with a 1/2" Forstner bit on a drill press or mill.
Step 11: Select & Prep the Letters.
Mine that old Scrabble game for the best looking letters. The 26 letter keys will be made from these glued to the maple dowel pieces. Trace a circle on the top of each one using a dowel piece, such that the number (point value) will be inside the circle. Sand off the corners, roughly, using a belt or disk sander. Mind your knuckles! The letters will be sanded more carefully once glued to the dowels.
Step 12: Glue Letters Onto Keys
Get a bunch of clamps ready of any sort you can find. Vises, vise grips, c-clamps, whatever. Prep keys in batches determined by how many vises you have. Paint the top of a 14mm dowel piece with Weldwood Contact Cement and also the underside of the letter tile. Let both dry until tacky. Carefully position the two and touch them together. This glue holds fast, so you only get one try here. Put the glued pair in one of your clamps to dry for several hours. Use some thin wood or rubber to protect the wood if the clamp has jaws that may mar it. Repeat X 25.
Step 13: Glue Veneer Onto Non-letter Keys.
Get some gorgeous veneer (unless you used a more interesting wood than poplar for the square and rectangular key blanks), 1mm thick (1/32"). I used bird's-eye maple veneer from Highland Woodworking. Trace each non-letter key onto the veneer and cut out the circles or rectangles with a sharp knife or scissors. You don't need to be very precise--aim for too big rather than too small; you will sand them after glueing to make them perfect. Glue these like you did for the letters, onto the corresponding key blank's top, except use thick cyanoacrylate glue. (I found that the yellow color of the contact cement came through the veneer.)
Step 14: Shape the Keys.
Sand off the letter or veneer overhang from each key with medium grit after they are good and dry. I put my belt sander in a vise to do this, but you can also use a disk sander or sand by hand with a sanding block. Wear leather gloves or hold the keys with rubber-jaw pliers to avoid skinned knuckles. Round the corners of all the keys, and you may want to make them more oval shaped than round, for most of the characters. Test fit them on the keyboard guts to see what size/shape will fit. Sand them all by hand with finer sandpaper to get rid of any scratches or plier marks that the shaping may have caused. This is a LOT of work. Think of each key as a sculpture, a work of art. Put on some good music. I listened to Flashback Alternatives on my internet radio---DJ Ed spinning my favorite New Wave hits from the 80s.
Step 15: Glue in the Key Stalks.
I tested a lot of glues, and concluded that syrupy thick cyanoacrylate glue is the best for glueing the plastic stalks to the wood keys. The "StickFast CA Thick" from Highland Hardware was marginally stronger than other thick CA glues. The keys will take a lot of pounding, so a really strong bond is important. That requires the plastic surface to be rough.
To roughen up the ends of the plastic key stalks you previously cut with a hot knife, sand them with coarse sandpaper attached to a sanding block while they are protruding slightly from a hole you drilled into a piece of wood that holds them firmly. Drill the hole on a drill press, or with a plunge router, to ensure the hole is perpendicular to the wood surface. Your goal here is more to roughen them than to level them completely, because you don't want to make them too short. A too-short stalk may not click sometimes, and the stalk will need to be replaced with a longer one from an additional keyboard.
Make a jig out of 1cm thick lucite, which will be used to glue stalks. I used a thick T-shaped ruler because that is what I had on hand. Drill one or more holes perpendicular to the surface and all the way through; use the appropriate diameter to hold a stalk snugly. Use a caliper to choose the correct drill bit for the stalks you have.
To glue the stalks, apply thick CA glue with a toothpick (or the sharp nozzle on the bottle) to the roughened end of the stalk, and a little bit (1mm) up the sides, too. Insert it into a hole in the lucite with long-nose pliers, carefully aligning it to be upright (North is pointing North), and protruding 1cm. Put a drop of thick CA glue in the bottom of the hole in next key to be glued, and spread it around with a toothpick. Put this key over the key stalk and push it down so you feel it pushing the stalk 1mm deeper into the lucite, and its base is up against the lucite jig. Now flip the jig over and use a long piece of scotch tape to hold the key in the right position. That is, the letter should be aligned vertically (North-South) in relation to the key stalk, and the stalk should be well centered in the hole, as seen by sighting through the lucite (see photo). Let them dry with the keys upside down, so glue will not run down the stalk, but pool in the hole you drilled in the key. If the lucite becomes clouded from glue fumes, be sure to sand it smooth with fine emery paper before gluing the next key, so you will be able to sight through it and check that the stalk is in the center of the hole. Probably a lot of improvements could be made to this process, but this worked for me.
Keys that are not glued properly will make your keyboard look all wonky, and may rub against the keyboard mechanism and get stuck, so center them and align them with the axes of the key stalk carefully and check alignment after taping and before walking away to let them dry. Be sure to let them dry AT LEAST 12 hours in the jig, then AT LEAST 12 hours removed from the jig for better airflow into the key, before plugging them into the base to test. Otherwise, the spring may get glued permanently to the key. [This was a costly and time-wasting error I made, ruining my first Unicomp keyboard.]
Step 16: Make Key Labels.
Use a labeler with clear label tape to generate all the labels for the non-letter keys. In the photo, that is white peel-off backing behind the clear tape. You could also use transfer lettering, or laser-print onto transparency sheets, or just draw symbols onto the keys if you are really good at that sort of thing. I tried using a wood burner, too, which was a bit too folksy for me. Cut as much of the clear tape away from the symbol as possible with fine scissors, peel off the backing, and stick them carefully to the keys with tweezers.
You might also wish to glue on some small bumps (I used tiny rhinestones) to the F and J keys so your fingers can find the home row without looking.
Step 17: Make the 2-stalk Keys.
I found after some trial and error that it was difficult to get the two-stalk keys to work properly if I had glued the stalks separately. The tolerances are really tight. So the solution I eventually hit on was this:
Shave down a lot of the original plastic key with a belt sander and Dremel, such that its two stalks are still attached to each other by some plastic bridges. Carve out the wood key blank so it is hollow enough to receive the plastic part inside it. When it fits well, glue it in place with CA glue.
The space bar has a stiff wire as part of its mechanism, and you will need to make little holes in the ends of the wood key to receive this wire, and shape it a bit until it works smoothly.
Step 18: Add LED to CAPS LOCK Key.
The control board of the keyboard has a CAPS LOCK light on it, but I decided the upper right corner of the keyboard is a dumb place for this, as the key is way on the left. So I moved the LED to the key itself. Actually, I used a very bright blue LED I got at Radio Shack, so I will never again fail to notice when CAPS is on. I also added foam bumpers (see photo) to the underside of the key to make it hard to press it accidentally.
Sand off any lip the LED may have, and roughen it up with sandpaper so that it diffuses the light better. Drill a hole through the key slightly larger than the LED, and poke it up through the bottom. Make a note of which wire is the anode (+) and which is the cathode (-) and glue the LED in place with CA glue. Cut or desolder the original LED from the controller board, and solder very flexible fine wire from an old pair of headphones to the board where the LED used to be. Later on you will cut this to the right length, solder this to the LED in the CAPS key and tape the wire down.
Step 19: Test Fit All the Keys.
Once all the stalks are glued and dried at least a day, plug them into the keyboard guts and make sure they don't bump into each other. If they do, more sanding is needed. Also make sure each key clicks properly and easily. If some stalk was not glued properly, break it out carefully with needle-nose pliers, carve out most of the glue with a Dremel, and glue it again.
Also test fit for clearance between the keys and the wood body. Sand either the body or the keys or both, as needed to be sure they won't rub after they get covered in epoxy finish.
Step 20: Dye the F Keys.
Instead of putting labels on the Function keys, I decided to color-code them according to the resistor color code. Use dye made for dyeing wood (I got mine at Highland Woodworking). If the dye comes as a powder, follow the instructions carefully for preparation and dyeing. Make sure the keys are as well sanded and shaped as needed. Keys may need multiple dips into the dye for the intensity you desire. Practice on some key blanks and veneer before dyeing the real keys. For the white key I used white paint.
Step 21: Apply Epoxy Finish to the Keys.
I originally applied many layers of water-based "hydrocote" finish to the keys, which looked great. But I found this to be less durable and MUCH more work to apply than just one thick coat of epoxy finish.
Use the 50/50 two-component epoxy that is used for restaurant tables, bars, and counters, such as "Ultra-Glo" or "Envirotex Lite® Pour-On High Gloss Finish" available at Michael's Arts & Crafts. Follow the instructions carefully, wear gloves and have good ventilation or an organics-filtering respirator; mix it VERY well using popsicle sticks, or it may not set properly.
Now would be a good time to get out the shop-vac and clean up as much dust from the work area as possible, so it does not end up becoming embedded in your finish.
Only mix a small amount (8+8mL) at a time; the epoxy has ~20 minutes working time, depending on its temperature. Use small (30mL) mixing cups with markings (see photo) to be sure you are adding 50% of each component. Hold the key stalks with long-nose pliers and dip each key into the well mixed epoxy, let it drip a second, then turn it upright and poke the stalk into a blob of modeling clay to hold it level while it sets (see photo). There should be a nice convex pool of epoxy covering the top of the key. Be very careful not to let any epoxy get on the key stalk. If that happens, wipe it off carefully immediately, and start over. To get rid of any bubbles, briefly wave a heat gun over the epoxy, as soon as they have risen to the top. Set up a tent made of plastic wrap on sticks (not shown), or a box of some sort to keep dust from landing on the keys while they are setting.
Step 22: Test Fit Finished Keys.
When the epoxy is completely hard, clip off the drips with end cutters. Plug the keys into the keyboard base, and ensure they all still work well and don't bump into each other. If they do rub or bump, more sanding is needed. Put the base into the wood body and check the clearance again. Sand the body more if needed, anticipating the thickness of the epoxy finish it will get.
Step 23: Finish the Body.
If the keys all fit, and work and look good, do a last check to make sure the body is well shaped, sanded and beautiful. Create a small groove with the Dremel through which the USB cable can exit the body at the back. The whole body should be finished with very fine sandpaper, and then slapped with a towel or blown with compressed air to get rid of any sawdust stuck in its grain.
Stain the wood if desired. I used wood dye Cherry #1832 from Highland Woodworking. Be sure to stain and finish a practice piece of wood (see photo) from the original plank before doing anything with the keyboard body you might regret. I did many practices with different stains and dyes before deciding on this one.
When the stain is dry, it is time for coating it with tough epoxy. Rig up some sort of clean cover to keep dust from landing on it while it is setting.
Prop it up on some pieces of scrap wood or something, not too close to its edges. If the stands are too close to any of the edges, they will become glued to the body. Prepare enough 50/50 pour-on epoxy to cover it, being sure to mix it very well. Follow the instructions supplied by the maker to the letter. Pour it on liberally, and let it drip all over the place.
Once it is hardened (about a day), clip off the drips from the underside with end cutters. If the finish is too high-gloss for you, you can now buff it with steel wool, or sand it with very fine emery cloth (e.g., 600 grit). A satin finish will show fingerprints less than the super shiny high-gloss finish.
Step 24: Assemble Your Keyboard.
Once again, plug in all the keys and see if they all fit and work with the now finished body over them. If not, do more sanding.
Solder the caps lock wire (whose other end you soldered onto the control board previously) onto the LED leads of the CAPS LOCK key, and tape or glue it down to the guts (see photo) so it won't get hung up on any other keys. Be sure to get the polarity right. Plug the USB cable into a computer and try it out to make sure it works.
If everything fits and works, make sure the guts are well seated in the body and with it upside down and resting on its body (not on the keys), apply a few dabs of Sugru to the corners of the bottom surface of the guts to glue it into the body (see photo). This will hold well, and is easily removed with a sharp knife if necessary. You might wish to use some screws if you anticipate taking the keyboard apart. Also use the Sugru (not hot glue, as I did) to hold the USB wire in place and route it out through the groove you made.
Finally, trace out the shape of the body onto a suitable piece of felt or fleece with chalk, and cut it to fit well. Attach it to the undersurface with Scotch double-sided tape. You're finished!
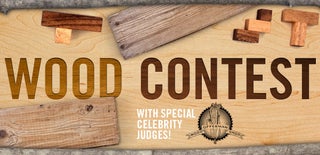
Participated in the
Wood Contest