Introduction: Wooden Mallet (AKA Thorin Oakenhammer)
I’ve wanted to start some chiseling work for a while; mortise and tenon joints, dovetails, etc. and a wooden mallet seemed like a good starter project. There are a lot of plans on how to build these online and each one has it’s own unique design aspects. This is my take on it.
Step 1: Design, Tools, and Materials
The mallet was built out of some scrap oak that I had lying around. I didn’t really put a lot of thought into the design. A quick idea in my head and some quick guesswork measurements on the scrap wood was all it took.
I have an old wooden handle claw hammer that I really love the feel of and decided to mimic the handle for this mallets design. After that some quick guesswork measurements on the scrap wood was all it took. I chose a 6” head length simply because I thought it looked about right when held next to the handle sized piece of wood. The head is approximately 6"x3-1/2”x2-1/2” and the handle is approximately 1-3/4”x1-1/4”x11”.
Tools:
Drill press
Forster bits
Table saw
Scroll saw
Roofers triangle
Ruler
Sureform
Sandpaper
Misc clamps, hammer, blocks, and scrap wood as needed
Materials:
Oak (or any scrap hardwood)
Wood glue
Oil finish (optional)
Step 2: Mallet Head
This project was my first attempt at a mortise and tenon joint. I took my time with the placement of the joint to make sure everything lined up as this is really the only part where something could go wrong on this build. I found the center of the head in both directions and measured out to the edge of the finished handle dimensions. In my case I ended up with an area approximately 1-3/4”x1-1/4” to match the dimensions of the handle. I measured this and re-measured about few times just to make sure it was accurate on both the top and bottom of the head. I shaded the area that would be carved out.
To cut the mortise out I broke out the old vintage drill press and the forster bits. The drill press was a little under powered for the job but it’s the only one I had access to. I used a 5/8” bit and drilled 6 holes on each side. The bit wasn't long enough to go any farther. It wasn’t perfectly in line from side to side, but it was pretty close and the chisel could take care of the rest. I then chiseled the hole square all the way through.
Side Note: This project was my first attempt at using chisels and I quickly stumbled onto a problem; how do you use chisels to make the hammer that you need to hit the chisels with? My solution was to hold a scrap wood block over the butt end of the chisel and hit the block gently with a regular old claw hammer. Definitely not ideal and probably not recommended, but it worked.
Step 3: Mallet Handle
To make the handle I measured the length, width, and height of an old claw hammer handle that I really like the feel of. I ripped some oak on the table saw down to this size; it was about 1-3/4” x 1-1/4" x 11” long. I then traced out the shape of the old hammer handle onto the oak. The oak was rough cut to match the handle contours on a scroll saw and I left one end of the handle rectangular. This rectangle end would become the tenon half of the joint.
I took the rough cut handle and clamped the rectangle end into the vice. Using a sureform I took down the corners into a mostly round/oval handle. Following the sureform I cleaned it up with some sand paper (60 through 320 grit) to smooth out the majority of the tool marks. Since this will be a tool for the shop and not a display piece or a piece meant to be sold, I didn’t spend too much time getting every tool mark off. It’s a hammer, it’s meant to take a beating.
Lastly I took the handle back to the jig saw and cut a relief throught the rectangle end to help with installation into the head.
Step 4: Assembly
I put the handle in the head and with the help of some glue, a big hammer, and a block so I didn’t screw up the handle I forced it into it’s final place. It took a LOT more force than it should have to join the pieces. Next time i'll make the relief cut larger or add a second cut. After a good strong beating, there was still about a 1/4" of gap where the handle wouldn’t move any farther. The relief cut I made closed up to the point where I couldn’t get a wedge in to hold it in place as originally planned but with the glue and the amount of force needed to get it in place I figured it would never move.
After some final sanding to knock of the sharp corners and a quick oil finish, it was done.
Step 5: Finished Mallet
I shall call it Thorin Oakenhammer.
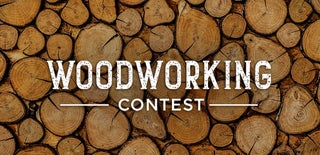
Participated in the
Woodworking Contest