Introduction: Wooden Mallet With Brass Inlay
I think it's a right of passage that all woodworkers make their own woodworking mallet at some point in time. So for mine I figured I would add a little something extra to it, some Brass Inlay! The mallet I made has dimensions of 7" wide x 3 3/8" tall x 2 1/2" thick for the head of the mallet. The over length of the handle from the top of the mallet head to the end of the handle is 12 1/2". The handle is 1 3/4" x 1 1/2" inside the mallet head and rounded off for the rest. It utilizes a mortise and tenon joint to adhere the mallet head to the handle. So if you are interested please check out how I made mine with a little something extra.
And if you can't see the link for my YouTube video on this build, here you go!
https://youtu.be/JwMiFw_85yA
Supplies
Includes affiliated links to products.
Wood of your choice
Another Wood Mallet
Table Saw (Optional) or Handsaw
Drill Press or Hand Drill
1/8" Drill Bit
Band Saw or Handsaw
Clamps
Belt Sander (Optional)
Sandpaper (80 to 220 Grit)
Wood Finish Of Your Choice
Step 1: Cut the Lumber Down to Rough Dimension.
For what ever type of wood that you use you will want to cut it down to rough dimensions. I personally used some walnut that had already been surfaced on both sides down to around a half inch. Surfaced meaning that it has been made flat on the wider edges. This was done by a powered planer in my case but can be done by a hand plane as well.
The center section of my mallet is made from what I believe is either Maple or Poplar wood. It was given to me by someone who was not sure what is was either. It was given to me already at a 1 1/2" x 3 1/2" dimension so I just had to cut in down to length.
Step 2: Cut Angles on Interior Faces
To accept the future wedges that will be hammered in I cut a 3 degree angle on the interior of the mallet head.
Step 3: Glue the Mallet Head Together
I liberally applied wood glue being careful to not get any glue in the area where the mallet handle will be. Using the mallet handle as a spacer I got everything clamped together. I then removed the handle after clamping to insure that it did not get glued in at this time. I then set everything aside to dry.
Step 4: Drill Holes and Cut Slots
In the mallet head I marked out and drilled two holes. These will provide relief for when the future wedges are hammered into the slots the wood will not split further down the grain.
After the holes are drilled I used my band saw to cut slots down to the previously drilled holes. An optional method would be to use a hand saw for this.
Step 5: Shape the Handle
At this time I spent some time shaping the handle till I was happy. I started off with a belt sander to remove the bulk of the material on the corners of the handle. I then switched over to my orbital sander with 80 grit sand paper to further refine the shape of the handle.
I then decided to go back to my band saw and cut off just a bit more to get to a handle length I liked better.
Step 6: Shape the Mallet Head
To start shaping the mallet head I cut a 3 degree angle on both sides.
Using my trim router I used a 3/8" round over bit a rounded off all edges of the mallet head.
The step is optional. Other options could be a chamfer bit with a trim router. Or a small hand plane can be used to chamfer the edges as well. It's all in what you want it to look like and what tools you want to use.
Step 7: Make the Wedges
To make the wedges I utilized a large chuck of walnut I had leftover from another project. I set my table saw up to cut 3 degree cuts and made two passes to get two wedges. These will need to go from about a 1/4" down to a point.
I then cut out the final width of the wedges.This dimension comes from the thickness of the mortise inside the mallet head which in my case was 1 1/2".
Step 8: Mark Out and Cut Grooves for the Brass Inlay
Using a pencil and a straight edge I marked out where I would put the inlay. For mine I chose 3 equally space lines on each side of the mallet.
At that point I used my plunge router with a 1/8" straight cut bit set to cut 1/16" deep to rout out the groves for the brass inlay.
To guide my router in a straight line I simply used two scraps of plywood clamped together. Set up in a way that the router would ride on top of the lower piece of plywood. This piece I could line up with the line on the mallet head.The second piece of plywood I clammed down at the right distance so the router bit skimmed the edge of the lower piece of plywood. Then everything was clamped down to the work bench during routing.
Step 9: Set the Brass Into the Wood
With the 1/8" brass rod I used some plyer cutters to cut the brass rod to rough length. From that point I used my bench grinder to gently round over the ends until I got the brass rod to the perfect length. Be careful of heat build up using this method. I dipped the brass in some water when it got too hot.
Once that was done it was time to glue the rods into place. Using some 5 minute epoxy I set the brass into place. I then used a scrap board covered in painters tape and clamps to clamp the brass down until dry.
Step 10: File the Brass
I mainly used a bastard file to file the round brass rods down flush with the walnut. I actually started out trying my orbital sander but this did not work well. So the bastard file worked best but beware as it does create a lot of heat in the brass. So take your time as you do not want to melt the epoxy which would make the brass come loose.
I then sanded everything down to 220 grit sand paper.
Step 11: Join the Mallet Head to the Handle
One of the best parts!
I liberally applied wood glue to all surfaces of the top of the handle as well as the inside of the mallet head. Then I slid the mallet head onto the handle. Utilizing a clamp to keep the mallet head from sliding further down the handle I then inserted the wedges and drove them down into place with another mallet.
Step 12: Remove Excess and Sand Smooth
After everything had time to dry I went over to my band saw and cut off the excess handle material. This could also be done with a hand saw just as easily.
From there I used my orbital sander with 80 grit sand paper to bring the handle down flush with the top of the mallet.
Step 13: THE BEST PART!
After sanding everything down again using 220 grit sand paper it was time to add the finish. I simply used some butcher block oil I had laying around. I wiped down all the surfaces until covered and then wiped off any excess.
And Done!
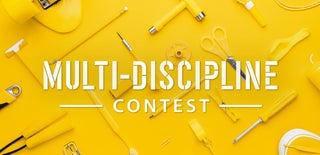
Participated in the
Multi-Discipline Contest