Introduction: Wooden Threads With Your Router Table
I haven’t had much luck with the commercial tap and die sets for making wooden threads. It seems like the cutting knife in the die is the weak spot, it just doesn’t last for me or leaves a rough thread. So I decided to make my own threading jig for my router table. This wooden thread-making jig uses 3d printed parts to reliably create threads on a wooden dowel to make wooden screws for toys or jigs. The included files are for a 3/4 inch screw with a 6 TPI thread. (TPI = threads per inch). You can easily adapt the idea for other size dowels and threads.
Equipment:
- 3D Printer
- Router Table
- V-Groove Router Bit, 60 degrees
- 3/4 inch Tap - 6 TPI
Supplies
- 3/4 inch hardwood dowels
- hardwood to make wooden hex nuts, mounting plates, etc
Step 1: 3d Printed Parts
3d print the four parts: the dowel guide, the thread box, the thread sleeve, and the set-up block. If you don't have a 3d printer use your local maker space or send the files off to a commercial 3d print shop. I designed the parts using Autodesk Fusion 360.
After printing the parts make sure the thread sleeve screws smoothly thru the thread box, and the dowel fits snug into the thread sleeve.
Use the set-up block to set the router bit height and distance from the fence.
The dowel guide clamps to the router table fence over the v-groove bit. The thread box clamps to the fence to the right of the bit (infeed).
Insert the dowel into the thread sleeve and then thread both into the thread box. When turning the dowel it will advance across the v-groove bit at the 6 TPI rate while the v-groove bit cuts the threads. If the dowel slips in the thread sleeve wrap the dowel with one or two layers of scotch tape to attach firmly.
Edit 7/3/2020:
Attached are new stl files for the 3d printed parts. They include all jig parts for 1/2”-8TPI screws and for 3/4”-6TPI screws, including setup blocks to get you started.
Attachments
Step 2: Set-Up
The tip of the v-groove bit should be at 16 mm above the table, and 22.5 mm from the fence for the 3/4"-6TPI screw. For the 1/2"-8TPI screw set the tip of the v-groove bit at 13 mm above the table and 17 mm from the fence. You will have to experiment a little for the best cutting height. Mount the dowel guide and thread box on the router table as shown in the previous step. The thread sleeve should be positioned and fixed on the dowel so that the front of the dowel is at the tip of the v-groove bit.
Use a hardwood dowel with a straight grain. I am showing an oak dowel bought at the hardware store for this Instructable. A long dowel that extends beyond the router table edge is easiest to handle when turning the dowel.
The pictures should explain the positioning to start the cut.
Step 3: Cutting the Thread
Now start the router and turn the dowel to slowly advance it to cut the thread. The first part of the thread could be a little off until the dowel enters the dowel guide hole to the left of the bit (It has not been a problem for me). Keep turning until you have your desired screw length but stop before the thread sleeve exits the thread box on the far side. With the setup as shown you’ll get a thread length of about 3 inches. For longer screws you’ll have to 3d print a longer thread box. Everything else will be the same.
Step 4: Clean-up and Fine-Tuning
After cutting the screw clean up with a light sanding of the threads. Try the screw with the 3d printed sample nut. Attached is the file. As mentioned before, setting the exact height of the v-groove router bit above the table is very critical! If the thread-fit on the nut is too tight you need to raise the v-groove router bit by a very small amount. For a fit that is too loose lower the router bit. Even with the set-up block from step 1 you may need to do a little fine-tuning. The pictures above show a dowel with a perfect thread and a dowel where the bit was set too low; it does not fit the threads in the nuts.
Once you find the 'perfect' setting you can use a piece of hardwood to cut a v-groove into a set-up block for future reference.
Maple dowels and cherry dowels cut beautiful threads. Oak dowels and poplar dowels from the hardware store cut well with little chip-out. Birch dowels and pine dowels do not work well. I haven't tried any other hardwood dowels, so let me know your results if you try walnut, hickory, mahagony, etc.
Attachments
Step 5: Wood Taps
To make a threaded wooden nut you need to get a tap like this and follow their instructions:
https://www.grizzly.com/products/Grizzly-Wood-Thre...
https://woodworker.com/12-diameter-taper-tap-mssu-...
Drill a 5/8 inch hole for a 3/4 inch tap, then use the tap to thread the hole as in the pictures. Use the 3d printed screw (file attached) and nut to mark the outline of the wooden nut. Then cut on a bandsaw and sand to the lines. Round all edges with a light touch.
To make a bolt head use a Forstner bit to drill half way into your wood block. Then mark the outline of the head as before , cut on the bandsaw, and sand. Finally glue the threaded bolt into the head.
Attachments
Step 6: Be Creative!
Now that you have a bunch of wooden screws and nuts you can make beautiful construction sets or other toys for children. Look at some of my ideas in the pictures. I am working on a larger wooden construction set using these screws and nuts, with wooden wrenches, screwdrivers, a workbench, etc.
All pieces are finished with food-grade mineral oil.
Use the same technique to make larger diameter screws for clamps or bench vises.
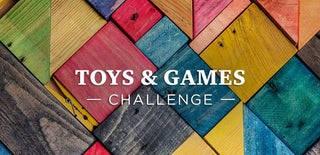
Second Prize in the
Toys and Games Challenge