Introduction: Woodworking Marking Knife
Hi! I'm The Redsmith, I'm a maker.
For two years now, I've been listening to the "Making it podcast"
hosted by Bob Clagett, David Piccuito and Jimmy DiResta. These three awesome makers have given me inspiration to make more and make better things.
December 3rd, 2016, they gathered a lot of Makers to celebrate the 100th episode of the podcast. I wasn't there, so, this build is a way for me to thank them. I made three marking knives : one for Bob, one for David and one for Jimmy using different hard woods for the scales.
A marking knife is a must have tool for any woodworker or carpenter.
You can buy a marking knife for cheap now, but why not try to make one ?
I made a full tutorial video that you can watch here :
Let's get started !
Step 1: Needed Materials and Preparation
For this build, you will need :
- High carbon steel : I used XC75 High carbon stee because that's what I can easily find in my country.
XC 75 contains 0.75% Carbon, 0.55% Manganese and 0.30% SIlicon. It is mainly used to make blades, chisels and cutting tools. It needs to be quenched in oil between 790 and 810ºC / 1454-1490ºF (the color of the steel would be between red and bright red) and tempered for one hour between 200 and 300ºC / 392-572ºF (the color would be from faint strow to blue).
Be sure to use the right material and refer to the factory specifications of the steel you use.
- Angle grinder with a cutting wheel or hand metal saw
- Metal files and/or a 2x72" belt grinder - a belt sander
- two 6 mm diameter brass pins
- one 10 mm diameter brass tube
- Two part epoxy
- Hard wood for the scales
- Clamps and a straight edge
- #600 and #1000 grid sand paper
- Boiled linseed oil
- A ruler and a black sharpie pen
- 20 cm (10 inches approx.) of flat leather lace
The first step is to measure the steel and cut it.
I decided I wanted to make a small marking knife, so I started by using my calipers to mark a 3 cm (1.2 inch) width. Don't mark your line to deep with your calipers or the line will be difficult to make disappear.
You can also use a ruler and a black sharpie pen. The most important thing is to get a straight line for you to cut.
Step 2: Cutting Steel
- Then, clamp a piece of wood to use as a straight edge (optional but helps a lot).
- Use a cutting wheel on your angle grinder to cut the steel to width.
- Make another cut to obtain the desired length (I cut a 15 cm / 6 inches long piece of steel).
You can also free hand your cuts using a angle grinder or a hand metal saw. Use the tools you have, you can refine the shape of your blade later.
Step 3: Straigthen the Edges
If you decide to make two or more knives at once, follow the next step.
If you're making just one, you can skip this one.
- Use double-sided tape to hold your pieces together. For more safety, I also used two F clamps.
- Use a file, a belt sander or a 2x72" belt grinder or even a hand file to straighten the edges and obtain perfectly identical pieces.
Step 4: Draw the Tip
- Draw a line in the middle of you blade.
- Then draw a triangle. The shape entirely depends on you and the angle you want for your blade.
Step 5: Make It Sharp, Make It Round
- Use 2x72", a belt sander, a grinder or a file to grind the end of the piece and give it a triangular shape.
- Draw a half circle on the onther of your blade and grind / file / sand it to shape.
Step 6: Center Punch
- Use a center punch to locate the holes you need to drill for the pins.
- Try to punch on the middle line of your blade for all your pins to get aligned.
Step 7: Drill, Drill, Drill
- Drill a pilot hole with a small drilling bit. Don't forget to lubricate the bit with oil or WD40 and go slow to not break it.
- Then, drill the holes to the final size.
- The ones near the tip of the blade are the smallest ones, for the pins. The last one will be used for the brass tube. Just take your time and lubricate the drill bit.
Step 8: Bevels
- Now, you will give your blade its final shape. You can use many tools (2x72", belt sander, grinder, etc...) but I recommand to use a simple file. Giving your blade the required bevel by hand allows you to go slow, don't make any mistake and get bevels with the same angle on each side of the blade.
- Just take your time, work on one side, then do the other one. Try to keep always the same angle. Don't worry, if you miss or make a mistake, you can always fix it (which isn't that easy with a 2x72" or a grinder).
Step 9: Perfect Bevels
- Once you're happy with the shape of your blade, use a finer file to clean the edges.
- When the two sides are perfectly identical and smooth, you can go to the next step.
- You can refine the shape of your blade until heat treating. So, take your time and work your shape till you're happy with it.
Step 10: Hardening...
Now, let's heat treat the blade.
As said previously, I used XC75 High carbon steel because that's what I can easily find in my country.
XC 75 contains 0.75% Carbon, 0.55% Manganese and 0.30% SIlicon. It is mainly used to make blades, chisels and cutting tools. So it's perfect for making marking knives. But your need to choose your steel carefully and check the factory specifications. If your heattreating fails, your steel / knife can become too brutal, break and hurt you or someone you care about or work with. So, be sure to know how the heat treating should be done before you do it.
- XC75 needs to be quenched in oil between 790-810ºC / 1454-1490ºF (the color of the blade should be between red and bright red). So I heated it with a torch untill I saw it turn red-bright red.If you do so, try to avoid the tip of your blade as much as possible. Let the heat travel to the tip and mainly heat the handle. As you have less material at the tip of your blade, it will heat faster than the handle and you may damage the steel, which means you will to grind it afterwards.
- Once you get the nice red color, quickly quench the tip of your blade in oil. (motor oil works just fine but be sure to wear safety gears and a respirator)
- To check it the hardening was a succes, use a file on the edges of the blade. If you can hear a clear sound and if the file doesn't scratch it, your hardening is a success and you can move on.
Step 11: ...and Tempering
- Clean the burnt oil from the blade with fine grid sandpaper (I used #600 grid). This will enable you to see the color of the blade after tempering and know if it was successful.
- Now you need to temper the blade otherwise it will be to hard and may break. Put it in your toaster or kitchen owen at 230ºC / 446ºF for one hour. The color of the blade should be now between light straw (light yellow) and blue.
- Let it cool overnight.
Step 12: Make It Shine
- Clean the blade using #600 grid and #1000 grid sandpaper glued on a flat surface.
- You can also wet the paper, it will make this step easier.
- Try to make a 8 pattern while sanding, it will prevent any visible scratch on the blade.
- If you have a buffing wheel, use it to make your blade shine a little bit more.
Step 13: Make the Scales
Now, it's time to make the scales of your blade. You have many options here but I recommand hard wood. You an easily find it, it's cheap and forgiving materials, specially if it's your first knife. But you can also use bone, horn, mikarta, stabilized wood, etc... For my three knives, I use three different woods : mahogany, wenge and buna (japanese beech).
- Cut two pieces of wood the same width of your blade.
- You will also need two 6mm pins and one 8mm brass tube to fix the scales to the blade. You can buy pins but, as I did myself, you can also make some using 6mm brass rod and 8mm brass tube.
Step 14: Drill, Drill, Drill
- Use double sided tape to attach your blade to one scale. This way, the holes of your blade and scales will be perfectly aligned.
- Drill the holes into your scale.
- Use double sided tape to attache the two scales together. Then, going through the holes you just drilled, drill the second scale. This way, all your holes will be aligned and your assembly will be very easy.
Step 15: Finish the Scales
- You can let on tip of the scales flat, but you can also shape them to match the shape of the blade.
- If you want to do so, use your blade's tip to draw the shape. Put the blade on your scales and draw a line with a sharpie.
- Use any saw or file you have to give the scales a triangular shape matching the shape of the blade.
- Once you're done, you can start beveling the scales to match the bevels of the blade.
Step 16: Assembly
- Mix the two part epoxy composant for at least one minute.
- Glue the scales to the blade using epoxy and the pins you made earlier. Don't hesitate to put a little bit to much expoxy than needed. As you will clamp your blade in few seconds, all the excess will squeeze out, so don't worry. Just clean the excess with a towel or a paper tissue (I also recommand to wear rubber gloves for this step).
- In order to not scratch your scales, use some scrap wood beforing clamping.
- The time needed for the epoxy to cure depends on the type of epoxy you use (I used 5 minute epoxy but had to let it cure overnight because it was to cold in my shop to fully cure in a few minutes).
Step 17: Final Shaping and Oil
- Once the epoxy is fully cured, cut any excess material (wood or brass pin) from the scales.
- Clean the scales belt sander and sand paper.
- When you're happy with your blade, you can apply oil on the wooden scales. I recommande boiled linseed oil, but once again, you have a lot of options here. You can also use beeswax or spray laquer.
Step 18: All Done !
And you are done !
A little leather ring will enables you to hang your knife to the wall and not scratch the blade or blunt the edges.
You can customize it the way you want: choose different shape, wood, leather, length and width.
Here is the full tutorial video :
I tried to make this Instructable as clear and easy as possible if
you have any questions or requests for clarification don't hesitate to comment.
I hope you liked it and if so please vote and like, share and watch the videos.
See you soon for my next Instructable!
The Redsmith.
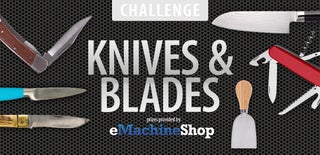
Grand Prize in the
Knives and Blades Challenge
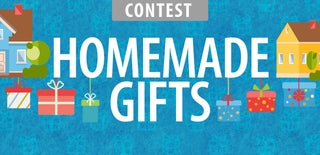
Participated in the
Homemade Gifts Contest 2016