Introduction: World's First Recycled Disc Golf Disc
Disc Golf is an outdoor sport that depends on plastic production, and it's currently growing at an unprecedented rate! The problem? None of the top manufacturers, who are making hundreds of discs per minute, have a disc made entirely out of post-industrial & post-consumer waste.
As someone who has been playing disc golf for 12 years and making things (thanks to my pops) my whole life, I realized one day: if I wanted to see this dream become a reality, I was going to have to make it! I had no experience welding, 3D modeling, or injection molding, but I knew I could learn.
Step 1: Recycle and Shred Plastic
Recycling plastics starts with four simple steps:
Collecting
Cleaning
Sorting
Shredding Plastic*
Once you finish the first three steps, simply throw them in the shredder. (My shredder is currently operated with a hand crank, but I added room on the base for a motor if desired.)
Precious Plastic, an awesome company based out of Europe, made open source plans for this shredder, which can easily be accessed on their website: www.PreciousPlastic.com - their plans include detailed drawings and laser files.
*Step One is optional as there are online retailers that sell regrind plastic. It limits what types and colors you have access to, but it comes with the pros of not needing to collect, clean, sort, and shred the plastic yourself!
Step 2: Design and Machine Mold
Designing the mold is quite simple and I used Fusion360!
First, design the disc. With a pair of calipers, just take a disc golf disc that you'd like to model yours after and measure away. Most discs are patented, so you can use this as a starting point, but do not make it exactly the same. Then, transfer your desired measurements into Fusion360!
Second, design the mold. The mold is basically just a negative of the disc, made out of two pieces of aluminum. I use four different 3/8" holes on each corner for alignment and to hold the mating pieces together. The injection point is a threaded 1/4" hole which allows for a 1/4" nipple (which also screws into the injection machine).
Lastly, machine the mold. Like most people, I don't have a metal CNC so I outsource this part to a friend who is a machinist. If you have one, you can do it yourself!
Step 3: Make Injection Machine
Precious Plastic, an awesome company creating an alternative recycling system and equipping anyone to recycle their own plastics, made videos and open source plans for this injection machine, which can easily be accessed on their website: www.PreciousPlastic.com . (I will keep my instructions here minimal, as their videos and plans are as detailed as one could desire, and there are many Instructables that can supplement as well).
Electronics: the electronics consist of a PID controller, solid state relay (SSR), band heaters, and a thermocouple. Once you learn about these components, wiring them up is easy. Here is the Instructable I used to learn about them: https://www.instructables.com/PID-Temperature-Controlled-Oven/)
Base: Welding the base and other components is quite simple. The videos and detailed drawings from Precious Plastic outline every cut necessary, and make the build easy! One feature you can adjust is making an entire base or making it wall mounted.
Plunger & Barrel: The plunger and barrel must be a perfect fit. The plunger mustbe a seamless/extruded pipe. Common pipe from big box stores (like Home Depot) have a weld bead running down the center and render them useless for Injection Machines. Sourcing this can be difficult depending on your country. In the US, I am able to get an 1.25" OD and 1.01" ID seamless pipe for the barrel, and match that with a 0.999" steel rod as the plunger.
Full Disclosure: I've built a handful of these machines. The first took me months as I learned how to weld, taught myself electronics, and sourced all of these specific materials. The second one I built took two days!
Step 4: Make Recycled Disc
Once you have all of the necessary components, making a recycled disc is quite easy!
Heat Barrel (250 degrees Celsius) and Preheat Mold (250 degrees Fahrenheit)
Fill Plastic in Barrel (180gram shot size)
Melt Plastic (about 20 minutes for HDPE)
Attach Mold and Inject
Detach Mold and Let Cool (about 10 minutes)
Remove Disc From Mold
I documented the entire process from learning to weld to making a fully recycled disc on YouTube, and you can check that out here!
Step 5: Conclusion
I'm still learning a ton and perfecting the disc itself, but it's officially the world's first disc made from 100% post-industrial and post-consumer plastics!
Maybe you want to make a disc or another recycled plastic product (coasters, planters, etc.). Regardless, I hope this Instructable helped you!
The steps may seem difficult (they were definitely daunting to me at the beginning), but rest assured you can learn! I was a beginner in every aspect I needed to make this thing: welding, electronics, plastic, CAD, etc.
If I can do it, so can you! Just learn something new everyday.
Cheers!
Jesse.
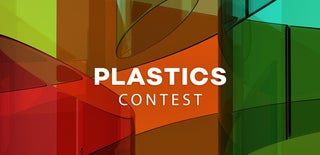
Participated in the
Plastic Contest