Introduction: Y220 - Mini Tricopter (Quadcopter Frame Transformed)
Recently, I have seen a review about a Mini Tricopter from RCExplorer and also HJ-Y3 as below links.
They are very inspiring me as they seem to be very interesting than those boring old Quadcopters I've made before. So I started to think how can I build one without buying a new complete kit since the price for these kits are not that cheap for me. Then I started from researching a lot on how TriCopter works especially on the rear motor and servo part.
About the servo moving part, I don't have much confidence to replicate the mechanism, therefore, my solution is just buying a replacement part for Servo mount of HJ-Y3 as you can see later in the next step for the Part lists detail.
About the whole frame, I've been searching so many different kinds of Quadcopter frame kits available in the internet those are feasible to be transformed into a Tricopter. Since the Quadcopter frame kit with the frame size 250 is very popular and the most important thing is that they are cheap enough to try one. Finally, I found Q250 from HMF Totem that should be the most convenient solution according to its PCB shape is quite "round" enough to transform from Quadcopter to Tricopter.
Step 1: Part Lists
Below are the complete part lists I've dedicated for this project.
Digital servo (1 EA) - TowerPro MG90D 13g Metal Gear ($5.19)
Servo mount (1 EA) - HJ-Y3 Three-axis Aircraft Brushless Motor Mount Holder ($5.27)
Motor protection (3 EA) - Universal Motor Cover Protection for 22 Series Motor ($1.70 / 4 ea)
Propellers 6045 (3 EA) - FCMODEL 6045 3-Blade Propeller CW CCW for QAV250 Multicopter ($1.97 / 4 ea)
Flight controller (1 EA) - CC3D Flight Controller 32 Bits Processor With Side Pin ($9.56)
TOTAL PRICE FOR ALL PART LISTS EXCLUDED TRANSMITTER AND LIPO BATTERY ARE BUDGETED < 80 USD.
Step 2: Motors and ESCs Preparation.
In my case, I need this step because I don't want to use the bullet connectors to connect motors and ESCs together except on the rear motor. So what I need to do is just removing the shrink tube on each ESC then removing the 3 controlled wires and directly solder those points to motor wires, finally just put back a new shrink tube on each ESC. Sorry that I didn't take any pictures at this step as I think it is not really necessary.
For the rear motor and ESC, I decided to apply 2 mm bullet connectors to connect them together because of 2 reasons: 1) I may need to change the 3 wire connection later according to the motor CW/CCW direction 2) I don't know exactly the appropriate length of the wire to be there when servo is moving from one side to another side.
Step 3: Tail Arm Preparation
At this step you need to prepare below components.
- One of a Q250 Arm that will be used as a tail arm
- Digital servo (MG90D)
- Servo mount kit from HJ-Y3
Started pre-assembly tail arm follows these instructions.
- Cutting the landing skid area underneath motor mount position (on the bottom side, at the end of the arm). According to my findings that the tail arm is better to be used as "upside-down" because it will be much easier to place and secure the servo moving parts together on the arm. Thus the landing skid area needs to be cut off in order to avoid obstruction while servo mount is moving from one end to another end.
- Assembly the Servo mount kit together, fully put the given rod through the hole of the 2 mounting parts.
- Put the metal gear of servo into another hole of the mounting parts. Align the servo center position with the mounting parts in upright direction.
- Place the pre-assembly mounting servo on the tail arm (hold an arm upside-down), fixed the mounting part by provided screws.
- Tighten the servo with cable ties firmly and reinforced by hotmelt glue.
- Assembly the rear motor on the servo mounting part, fix it with provided screws.
Step 4: Frame Preparation
For the frame preparation, the whole components required are as below.
- A Q250 Top PCB
- A Q250 Bottom PCB
- 3 pcs of Q250 arms (10.5 cm length)
- Assorted of fixing screws
- 4 pcs of Motor protection for motor 22 series
- ESCs pre-soldered with Motors
What you may need to prepare on the frame kits are as the following:-
- Pre-soldering on those PCB pads on the Bottom PCB part with the appropriated amount of solder lead.
- Soldering +, - pads on those PCB pads with the ESC power wires (Red, Black) regarding the polarity.
- Soldering the Battery connector terminal (XT60 male) to the bottom PCB.
- Assembly Motors with Arms, use motor protection for the front arms motors.
- Assembly the 2 front arms with the Bottom PCB by the provided screws (fixing it through the given holes on the PCB).
- Manage to organize the ESCs and Cable wires beneath the arms as good as possible. Cable ties can help a lot on this step.
- Assembly the Top PCB (without having the tail arm yet), fix it with the 2 front arms by provided screws.
- Inserted the pre-assembly tail arm between the Top PCB and Bottom PCB, you have to give the tail arm upside down so that the servo and servo mount set are positioning upright to the whole frame. At this step you may also need to align the position of the tail arm to be centered as much as possible because the Top PCB doesn't have holes to fix the tail arm unlike front arms (keep in mind that, we're transforming a Quadcopter frame to be a Tricopter). My solution is to take the use of the available slot on the Top PCB to fix this tail arm. You may need to apply washers if needed before apply the fixing screws.
- For fixing the Bottom PCB with a tail arm, since there's no hole or slot available to be fixing screws at all, yet, I don't want to drill any new holes on the Bottom PCB because it may damage the copper layer unintentionally. So what I did was just left it alone and putting a hotmelt glue around the tail arm area that contacts to a Bottom PCB. This may not be a perfect solution but it can help a lot to reinforce the tail arm with bottom PCB.
Step 5: Final Assembly
Almost there! The remaining parts are just to finish the connection with a Flight controller and Receiver then organize those messing cable wires.
Just another tip, for I already have the motor protection 2 pieces for spare. So I used them as the landing skids, this can help the Bottom PCB not to be touched directly on the ground while taking off and landing. Refer to pictures, for a better explanation.
Step 6: Criticism
On the first flight test, after a basic setup on CC3D Flight controller with OpenPilot GCS this Mini Tricopter performance is quite good. The rear motor on tail arm had no oscillation (no tail wagging), so I don't need any PID tuning at all. Just don't forget to select the Servo type as Digital servo during a setup.
My only apology on writing this topic is that this is my first Instructables published and I didn't take enough pictures along the construction as I didn't plan to write it at the beginning. Until this Mini Tricopter has been done and everything is working well so that I just decided later to share it here.
Any criticism, comments and suggestions are all welcome. Also please do not hesitate to ask in case that my instructions are not well explained or not cleared in any steps. Thanks for your attention so far.
Step 7: Further Improvements
I just added this step after the Instructable had been posted for a couple days. Because after a few test flights, I would like to add, remove and change somethings here and there. Below are lists of those changes:-
- Move the CC3D Flight controller and R6D Receiver to be placed between the Top and Bottom PCB.
- Added velcro tape on the Top PCB to secure battery placement in addition to a belt strap.
- Added an antenna tube to secure a receiver antenna wire and for decoration purpose.
- Added the Q250 original landing gears to protect Bottom PCB surface from touching the ground.
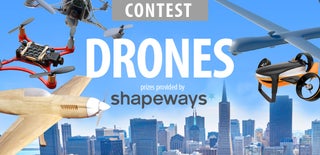
Participated in the
Drones Contest 2016