Introduction: Zebra Ply Lamp
In this Instructable I use some bits of walnut and scraps of ply wood to make a lamp for my little sister. She is a pretty cool kid so the contemporary design and stripes should be appreciated.
I have wanted to make a lamp for her for some time but the right peace of wood never came up. After looking back at some old sketchbooks (I tend to work out designs ahead of time in sketchbooks) I saw that I could modify an old design and make something nice out of the stuff I had in the bin.
So apart from the electronics and super glue this project is entirely free. :)
As well as scraps of wood from the sin bin if you want to follow the Instructable you will need...
Consumables...
Wood glue
A wood finish, (I used super glue and burnishing cream)
A plug
An inline dimmer
A lamp holder
A bulb (I used an Edison bulb because they are ace)
Some wire (I used braided wire again because its ace)
Tools
A lathe and cutting tools
A drill and drill bit
a few good clamps.
Wire stripper and screwdriver
Protective equipment
I always turn with a face mask and I would recommend a dust mask or respirator to avoid bereaving fine particles.
A dust extractor is a good thing to use if you have one.
By the way:
Here are a few reasons why wood turning is ace.
1 its a fun and organic way to make cool things. 2 you can use all the bits of wood left over at the end of a project or save wood from the fire and make something amazing / you can take other wise overlooked materials and make something really pop. 3 You can complete a whole project in less than a few hours.
Step 1: Get Your Wood Together
For this project I had an idea about the shape I wanted.
I cut different types of plywood to square and took two bits of walnut from the sin bin (the pile of wood left over from other projects which are likely to be only good as flue) and arranged them to make a small pile with the grain orientation crossing each other. (this helps make the ply stronger ... which isn't needed for this project but also helps make the project look more interesting which is needed for this project)
Once I was happy the height would be adequate to house the lamp fitting I glued together the stack and used clamps to ensure everything would set nicely.
I used different types of plywood to help the lamp look as interesting as possible, rather than having the same size stripes running throughout the different ply's create a variation.
Step 2: Round, Rough and Make a Tenon
Once the glue had cured.. (I glued up before work and when I got back home the glue had cured) I put the blank between centers trying to ensure the ply were as vertical as possible and turn a rough shape as well as turning a tenon where the lamp can be held in the chuck.
I checked the ply's were as vertical as possible by rotating the blank and observing where the last ply in the stack was in comparison to my static tool rest. I didn't end up with the ply's exactly right... I could have spent more time to get this but I got a reasonably correct orientation. I was happy knowing the walnut would hide alto of sins when it came to a very slight misalignment.
Step 3: Chuck, Shape and Hollow
Chuck the blank up using the tenon you recently cut.
I found it useful to cut a recess for the bulb holder into the lamp base which then acted as a guide for the rest of the lamp base shaping. Once I had finished cutting the outside shape I hollowed a space for the bulb holder to fit by drilling to the depth i wanted to go before using bowl gouges to remove the rest of the waste material.
At this point I sanded the outside faces of the lamp and showed off a little. (I might have showed off a lot I really like how this project turned out)
Step 4: Put a Hole in It and Make It Shine
I locked the lathe using its indexing system to hold the lamp in place and drilled towards center to give a place for the power cord to enter.
I gave the peace a final sand down before applying a few coats of cheep CA glue with a paper towel.
Once the CA had fully cured I lightly sanded this before buffing the surface to a high gloss.
Step 5: Turn Off the Tenon
I turned the lamp around and chucked up using the inside diameter as my chucking point.
Being very careful I turned off the tenon and was left with a nice flat bottom to the lamp.
Step 6: Wire It Up
Different countries will have different plugs and you will likely have a different inline dimmer switch and holder than the ones I chose. Please follow the instructions to your kit parts.
For me it was pretty much a simple case of stripping the wire where I wanted to include the components and screwing them into place.
Step 7: Enjoy the Lamp
I hope you have enjoyed this instructable and feel inspired to make something yourself.
If you do I would love to see what you come up with.
I know a lot of people will look at this and think they would like to take up wood turning but don't know where to start.
I would recommend looking to see if there is a wood turning club near you. In my experience the people you meet at clubs drawn together through a common interest there will be a lot of people who want to encourage you and share their passion and knowledge.. Much like instructables as a community but with people you can see and talk to without a computer.
If there isn't a club near you I would recommend looking for individual wood turners. Many of whom would be willing to put aside some time to introduce you to the craft/ hobby. (probably offer to pay, they might not take it but showing willing is always a good thing.. and shows you value their time)
Failing these two check out the internet.. your already there and looking at some wood turning. Just remember to be as safe as possible.. If something feels dangerous don't do it!
If your interested in more lamp designs I have another one here https://www.instructables.com/id/Edison-lamp-in-a-b...
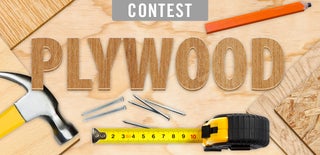
Participated in the
Plywood Contest
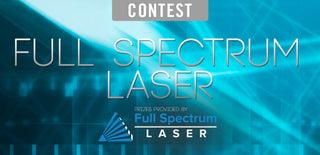
Participated in the
Full Spectrum Laser Contest 2016