Introduction: Deckchair With Baby Version
What does it have to do with epilog contest? Imagine to cut my blueprints on a 20mm acrylic plate (or two 10mm plates to glue together), or on some plywood boards. Your deckchair will be ready in an instant, and you can probably make something really unique.
Step 1: The Sample
Step 2: Project
Exact dimensions usually depends by profiles section, which is about 21x45mm in my case. In my blueprint you can see a view of the close frame and the exploded components aligned to the frame on the corresponding sides.
In pdf file you can find projects for all three versions described in this instructables.
Attachments
Step 3: Material
I chose antique wood boards coming from an old Italian roof, they probably are 80 years old. I sanded them and cut at the right length.
Step 4: The Grooves
Step 5: Some File Job
Begin with a rounded rasp, then refine with a file and smooth out with sandpaper.
Step 6: Dowel Holes
There is no need to be extremely precise, just don't drill too much near to the edge or the joint will be weak.
I used a pair of 8mm wood dowels to connect larger bars together, usually 6mm are too small and 10mm not so handy.
Step 7: Fastening Profiles
Step 8: Armrests
In the pictures you can see that I cut the armrests from some wood boards, I smoothed edges on top surface, I drilled holes for dowels in the supports, I painted everything with walnut mordent and glued supports and armrests together with vynilic glue.
Step 9: Colouring
I used walnut colored mordent, just dilute with water to set the darkness.
Step 10: Drilling Pairing Holes
Then set the column drill stopper so that holes will be deep as much as half dowel or a bit more.
If you look at the first picture you see that drill bit of on contact with wood surface and graded marker is locked on 16mm, when lever is at the lower position and hole is completely made the gauge show zero. That means the home is 16mm deep.
Step 11: Pivots
Use a special drill bit to make space for bolt heads and nuts inside the wood, especially where there are adjacent boards. I used a 22mm bit to guest self-locking nuts and 26mm bit to make space for bolts heads.
Step 12: Assemble Frames
Add glue and dowels in the holes and push parts one against other, sometimes you will need an hammer.
You can place clamps and belts, but wait to tight them.
Step 13: Checking Perpendicularity
Especially in this project where are moving parts and joints, perfect perpendicularity is essential. We already know that parallel sides have the same length, that's easy to do, but we also need to measure diagonals.
If diagonals are not equal use a cord to shorten the longer one, until it's needed. Then you can tight clamps and belts more. Wait enough time, usually some hours, before open them.
Step 14: Assembling
Some bolts need to be cut at a certain length, which is difficult to anticipate because some profiles differ a bit, especially if they come from an antique roof frame.
The best way is to assemble the frame with all washers in place and measure where the cut should be made. Mark the exact length or cut it in place.
At the end you can use a special product on the thread to avoid nuts to unscrew.
Step 15: Finishing Paint
But before painting the frames you can impregnate the thin parts where are footing of the diagonal support with a special soluble natural resin which will make them harder and tougher (second and third photos).
Step 16: Fabric
After sewing the hem I sewed a loop at one end of the fabric and used a clamp to the opposite edge to test different length and determine the best solution. In my opinion and with my geometry the fabric should stay stretched when the chair is closed.
Step 17: Fabric Locking Solution
Step 18: Make Someone Happy
Step 19: Lying Version
Step 20: Making Of
Step 21: Frame Comparison
Step 22: Fabric
Someone liked this chair so much and made me happy, try it and you will fall asleep at once.
Step 23:
Step 24: The Baby Version
Last made deckchair is the baby version. It's a special present for my little nephew. As always I chose old wood, but this time I paid more attention to remove any sliver of wood, sharp corner and anything which could hurt a child.
Step 25: Making Of
I sanded it and I cut the many pieces.
Step 26: Wedges
File the edge portions where wedges are. Try to not make wood too much thin or it will brake.
Step 27: Grooves
I made grooves as before, draw then on the board side, then cut and smooth.
Step 28: Armchairs
Armchairs boards were bed slats. I drilled holes for dowels and glued them to wood supports.
Step 29: Holes and Seats
Drill 8mm holes and also seats for nuts and bolt heads. Remember that self-locking nuts need a small seat so to be hammered in.
Step 30: Dowels
Use the method described before. Drill holes on the bars extremities, and with special metal cylinders mark the hole center on the opposite board.
Step 31: Glue
Drip glue in the holes, insert dowels, connect parts, tighten with clamps, and check perpendicularity.
Step 32: Verify and Paint
When everything is glued take off clamps and verify the assembling.
If everything is OK you can paint parts with mordent and shellac.
Step 33: Assembling
Metal joints are the same of the bigger brothers. If wood bars are enough straight a big washer between two adjacent bars designs be fine. But the space could be wider so you can choose to insert two washers instead.
Step 34: Fabric Fastening
Awesome, frame is ready to receive a cool fabric. This time the fabric fastening is different again. Loop is now on the bottom side of the frame, and the fabric doesn't make any revolution around the frame (solution A). This solution is not suggested if the frame is wider and the allowed guest weight higher.
Step 35: Testing Time
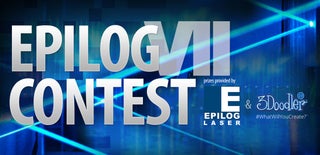
Participated in the
Epilog Contest VII