Introduction: 200 Watt Solar Day Lamp for Banks Offices Factories Etc
Introduction: Solar Day Lamp as the name suggests, works only in the day time, when the Sun is shining. Most Banks, Offices, some factories etc work in day time. Hence Solar Day Lamp can meet their lighting demands easily. The advantages of Solar Day Lamp in such applications are:
1) Very simple, cost effective and lasts more than 15 years.
2) No maintenance, fix and forget type design.
3) Battery-less operation, hence no battery maintenance/ replacement costs.
4) Off grid operation, provides light when grid supply is not available (only in day time).
5) No complex wiring required. Only two wires for connecting to solar panel.
6) Easily expandable by adding more lamps and more solar panels.
7) No transmission power loss, no battery charge/ discharge power loss.
8) No complex circuit, hence high reliability.
In this article, very simple 200 W Solar Day Lamp design is presented. It uses easily available raw materials in the market. It can be fabricated with minimum efforts.
Step 1: Material Required
1) Solar PV panel, 24 V 200 W (72 cells) - 1 pc
2) 5 W, metal clad, white LED pcbs (50 mm dia) - 40 pcs
3) Aluminium "U" channel (24 mm x 12 mm) with "T" slots - 12 ft long 2 pcs
4) Resistor 10 ohm 2W - 40 pcs
5) Two core hook up wire - 60 ft
6) Connector with 2 terminals - 5 pcs
7) Cotton / Fibre sleeve 6 mm dia - 10 ft
8) M4 X 25 mm screws, washers & nuts - 40 sets
9) Translucent plastic sheet - 6 ft X 2.5 ft
10) 5 Amp two core cable - Length as required (From PV panel to the lamp)
11) Plastic pipe 0.5 in dia - Length as required (for protection of cable from sunlight)
12) Heat sink compound or thermally conductive paste
13) Plywood sheet/ plastic sheet - 6 ft X 2.5 ft x 5 mm thick
14) Aluminium reflective foil - 6 ft X 2.5 ft x 0.5 mm thick
Step 2: Circuit Diagram
Circuit diagram of 200 Watt Solar Day Lamp is shown in Fig. 3.
The circuit consists of single solar PV panel of 24 V 200 W power rating. It comes with 72 cells connected in series and generates 36 V at maximum power point. Output of this panel is connected to 20 LED arrays A1 to A20. Each array consists of two round metal clad LED pcbs (PCB1 & PCB2) of 5 W each. These PCBs have five 1 W LEDs connected in series (each LED is actually two 0.5 W LEDs in parallel). These two PCBs are connected in series with two resistors R1 and R2 to limit LED current. The value of resistor is 10 ohm 2 W.
Step 3: Channel Assembly
Take the two Al channels which are 12 feet in length. Cut them in the middle to get four pieces of 6 feet each as shown in Fig. 4. Note that if you do not get channels with "T" slots, you can take standard channels. In this case, holes have to be drilled to mount the PCBs.
Take one channel and mount two pin connector inside the channel near one end as shown in Fig. 5. This connector is mounted slightly inside, leaving the hole at the extreme end free as shown in the figure.
On each 6 feet channel, we have to mount 10 LED PCBs. Two PCBs are mounted at extreme ends. Remaining 8 are mounted with even spacing between them. Before mounting the PCBs, a thin layer of heat sink compound is applied over the area where the PCB will touch the channel as shown in Fig. 6. Al channel acts as heat sink.
PCBs are numbered as PCB1 (near the connector) to PCB10 at other end of the channel.
Step 4: Interconnections
As per the circuit diagram, we need to connect PCB1 and PCB2 in series to form array A1. Similarly PCB3 and PCB4 in series to form array A2 and so on. Arrays A1 to A5 will be connected to two pin connector. For this purpose cut 5 pieces of two core hook up wire. Wire length required for A5 will be measured from PCB10 up to 2 pin connector. Similarly measure and cut wires for other arrays. In the present design, we need 70" for A5, 54" for A4, 38" for A3, 24" for A2 and 10" for A1.
Take one piece of wire and separate the red and black wires up to 10", at one end. Now cut 9" of separated black wire as shown in Fig. 7. Cut this black wire in two equal parts.
Take two 10 ohm resistors and solder them in series as shown in the figure. Solder the two black wire pieces to the resistor assembly. Cut the cotton sleeve to a length slightly longer than the resistor assembly. Insert the resistor assembly inside the sleeve. Tie knots at two ends such that the sleeve does not move. Make 5 such wire harnesses for the five arrays. Complete the five arrays A1 to A5, by soldering the five harnesses to the PCBs as shown in the Fig. 8. Connect the other end of wire harnesses together such that all five arrays are in parallel. Similarly, make the remaining 3 channel assemblies ready as shown in figures 9 and 10.
Step 5: Integration
The first step of integration starts with joining the plastic sheet with Al reflective foil. Place the Al foil on the plastic sheet and draw four lines length wise, for mounting four channels assemblies with uniform separation between them. Mark 10 points on each of the lines where the PCB mounting screws get aligned. Drill 5 mm holes, while ensuring that the two sheets are aligned properly as shown in Fig.11. Now mark and drill 4 sets of four holes pattern for each of the two pin connectors as shown in the figure. These connectors project out from the plastic sheet.
Take four small pieces of twin hook up wire. Connect these wires to the two pin connectors of channel assemblies. Connect other ends of the wires such that all the channel assemblies are in parallel. Connect these ends to the 5th two pin connector as shown in Fig. 12. Now mount all four channel assemblies on the reflecting sheet by inserting the screws in the holes drilled.
Connect 5 Amp cable to the 5th connector. The other end of the cable is to be connected to the PV panel. Ensure that the polarity is correct. Keep the PV panel in a place where there is sunlight through out the day. If sunlight falls on the 5 Amp cable, over a period of time the cable will become brittle. Hence, pass the cable through the plastic pipe, where ever cable is exposed to sunlight.
The LED needs protection from dust accumulation. For that purpose the translucent plastic sheet is mounted on the front side. Fig 13 shows the lamp without plastic sheet. Fig 14 shows the lamp with plastic sheet.
The big plastic sheet can be avoided by putting small round plastic caps on each of the PCBs. This is a much cheaper solution as compared to big plastic sheet.
Step 6: Automatic Backup
Major drawback of Solar Day Lamp is the change in intensity of light with changing sunlight conditions. Especially when the sky is overcast with clouds, the light intensity reaches low levels. In such situation, there is need to turn ON backup lamps to get sufficient light.
This can be done by mounting few lamps (operating on grid supply) on all four sides of the Solar Day Lamp. The solar PV panel voltage gives an indication of how much light is being produced by the Day Lamp. If the PV voltage drops below certain threshold, then the surrounding lamps could be turned ON. To implement this, a comparator circuit is designed as shown in Fig. 15.
This circuit uses comparator IC LM393. The supply voltage is derived from PV voltage using 5.1 V Zener. Reference voltage is given to Non-Inverting input, using potential divider R204 and R205. Inverting input is connected to PV voltage through potential divider R201 and R202. R206 is used to generate hysteresis. Hysteresis is needed to avoid nuisance switching of backup lamps. The comparator output drives and opto isolator IC2. When Day Lamp is having sufficient PV voltage, the output transistor of IC2 is ON. If the PV voltage falls below threshold of about 27 V, the comparator output goes high and turns OFF the output transistor of IC2. This signal can be used to operate backup lamps.
Step 7: Multiple Lamp Design
In larger locations such as Malls, parking lots etc, more than one lamp is required. It is possible to install multiple lamps without complex wiring. Figure 16 shows four lamps connected in series. In order to power these four lamps, we need to have four PV panels connected in series. Between two lamps a small 0.5 ohm resistor is added. This represents wiring resistance. The first lamp does not need this resistance as the cable offers this resistance.
Step 8: Conclusions
Solar Day Lamp offers cost effective solution for providing light in the day time. This will reduce the power bill while providing light throughout the day. It will act as emergency lamp in the day time, if the grid fails. Large scale usage of Day Lamps will reduce the overloading of the grid and also fight global warming.
References:
https://www.instructables.com/id/Simple-Solar-Day-Lamp-which-lasts-for-15-years
https://www.instructables.com/id/High-Power-Solar-Day-Lamp
https://www.instructables.com/id/Add-on-LEDs-for-Solar-Day-Lamp
http://www.electronicdesign.com/power/solar-day-lamp-also-powers-fm-receiver
Vijay Vasant Deshpande
Bangalore
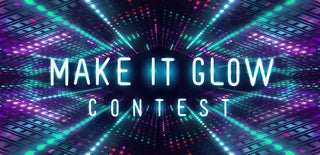
Participated in the
Make it Glow Contest 2018