Introduction: 3D Printed Ceramic Oil Lamp
I have an ancient lamp made of clay. There's no way I'm going to improve on the thousands of years of collective design embedded in it, but maybe I can make some new mistakes.
This Instructable is about what I learned while trying. It doesn't cover CAD technique or how to do 3D printing, and this project calls for some prior knowledge of those, but this was my first try with the ceramic material, and I see no reason it shouldn't be yours too. You'll need:
- CAD software and the will to use it
- Some money for the 3D print
- Oil, e.g. olive or peanut
- A wick, e.g. a piece of string
- A bit of hardware for a wick holder
Step 1: Design
What features does an oil lamp need? Well it has to hold some oil. It should be safe to handle while lit, and stable enough to not tip over. You need a big hole to fill it and a small hole for a wick. The oil reservoir wants to be wide rather than tall, because the wick wants to sit right on top of the oil, so you want the oil level to drop slowly. I'm appreciating this old lamp more and more.
What are the guidelines for designing 3DP ceramic? I'm getting this from Shapeways, so I punt to their page on how to use this material. One important rule is that when you have an enclosed space, you need at least a 10-15mm hole so the interior can be depowdered. Picture people reaching through the hole with dental picks, trying to touch every part of the interior: if they can't do this easily, your part fails.
I decided to make my lamp fairly simple. It's trilaterally symmetrical because I make everything like that. It has three fill holes, which should be plenty for easy depowdering. It has a central volume to hold the oil, and it thins out to solid edges which should be safe to handle and thick enough to print well. I put some decorative dots on the bottom lobes, I'm not sure how well those will come out.
It's shaped like an Enneper surface. I used Surface Evolver, which is freeware intended for mathematicians, to generate the main body. I modeled the holes, bullnose edges, decorations and interior fillets in Rhinoceros. Then I exported the whole thing to an STL file, and used Materialise Magics to clean up the mesh. My software toolbox looks like this for historical reasons (the last update to Evolver was in 2008) but there's no reason yours should look the same. De gustibus -- your lamp probably won't look like mine either!
To console myself while I wait for the print, I made a realistic image using Maxwell Render. Again, I use this software because I like it and I'm in the habit: not saying it's the best, it's a matter of taste. I got the candle-flame light effect from their material library.
Step 2: Fabrication & Findings
It cost $80 to print the lamp at Shapeways. Maybe I made it too big...anyway, three long weeks later the piece arrives. The material looks just like regular china: it's smooth and glossy and perfectly white and slightly translucent, with warm tones in the subsurface scattering. I'm a little disappointed with the size of the unglazed spots surrounding the "feet". My dots came out OK: not stellar, there are some glaze sag marks over one of them, but OK. Overall I think it's not bad.
To make a wick I used cotton string. I got "chalk line" because it's thicker than regular string, about 1/8" diameter. Oil lamp mavens online say you can use anything that's a natural fiber and and fairly smooth, or in a pinch rolled-up toilet paper. The classy solution would be to get actual oil lamp wick, but I couldn't think of a local source and didn't want to wait. Don't use flammable synthetics such as nylon or polypro! You don't want the wick to burn without fuel.
For oil I used some old evoo that had gone off. Again consulting the Intertubes, people say any kind of vegetable oil will work, or bacon grease, or if you want to be pedantic most hardware stores carry lamp oil.Don't use a fuel that can sustain fire on its surface, such as alcohol or kerosene. You don't want the oil reserve to catch fire, this will make the lamp too hot to handle, plus be an extreme hazard if it spills.
I'm afraid the heat will crack the ceramic, I'll be kicking myself if I light this thing and it breaks right away. While at the hardware store I got a stainless 6-32 T-nut with a round flange, without prongs. The ID is big enough for my string, and the OD is small enough to fit in the wick hole of my lamp. Anything of the same general shape would work, I found this by browsing the fasteners in an Ace hardware. I hope that it will a) hold the wick vertical, and b) diffuse the heat at the base of the flame. This may not work, or it may not be needed. My old lamp doesn't have one. Don't use galvanized metal near flame, hot galvie gives off toxic fumes. Look for steel, stainless, brass or bronze, they're nicer looking anyway.
My T-nut has 3 symmetrically placed holes, to match the symmetry of my lamp. If it had 4 holes, that wouldn't work.
Step 3: Preflight
I fill and assemble it. Drum roll please...
Step 4: Light It on Fire
Two oil lamps, 2000 years apart.
Have to keep the new one around for a while and see how it holds up, but so far so good. I'm really glad that worked. It'll be useful during power failures.
I hope someone is making lamps 2000 years from now.
I hope they look cool.
Step 5: Things I Learned
Problems
These fill holes suck. It's hard to pour oil into a hole that is close to vertical, and if you tip the thing over so one of the fill holes is more horizontal, you have to cover the other two with your (now oily) fingers. It would be better with only one fill hole that was more horizontal. Of course, it would be harder to depowder that way.
After filling, you have a round, slippery, expensive piece of oily porcelain in your oily hands. Eek. This would be better if it were easier to hang onto.
The upper lobes are near the hot part of the flame. If the lamp is set on a slant, or the wick goes sideways, the flame will brush into those lobes and I bet they'll crack. Too much design, not enough common sense.
The lower part of the oil reservoir isn't used because the wick can't pull oil up more than a half inch or so...which is why most antique oil lamps are flattish. Damn you, 3D brain.
This design doesn't say "I'm a container, don't spill me". When handed this object, if it is not lit, most people immediately turn it upside down with messy results. I'd like this to be a bug in my species rather than a bug in my design, but no.
If this were black ceramic instead of white, I would spend less time wiping soot stains off it. They come off easily, but I notice them. Shapeways has black ceramic, so this would be an easy fix.
Don't fill oil lamps near your photo setup. Do it somewhere else.
Things that went well:
My 3D print is on fire.
With olive oil it burns for about five hours.
Now that I've had it a few days, I think the print is nice. It was worth taking the trouble to understand the design constraints for this material, even though there are a lot of them.
Wick, holder and fuel were no problem: all that works perfectly. I successfully fought the urge to 3D print a custom wick-holder in steel, that's for the future when all of this is much cheaper. Meanwhile, hardware store ftw.
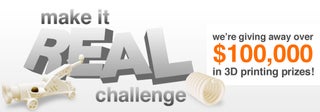
Participated in the
Make It Real Challenge