Introduction: 5 Watts LED Table Light
This one was made for my mom's sewing machine but can be adapted for any type of table. The measurements used in this was for the sewing machine table, thus you are required to adjust it according to your needs.
A little background on this project, feel free to skip it, if you are bored. I had a 1W LED light with flexible head that can be used as a table light or can be hung on the wall which I made it for my own use when I was in university hostel. I didn't want my roommate to be disturbed when I turn on the tube light. So I used this to read or to do some soldering and so on. I have finished studies and now I don't use it anymore. My mom recently learned sewing and started using the machine and had to turn on the tube light all the time just to have some light when she wanted to sew. I gave her the 1W LED which was focused on the needle area. While this was sufficient during day time when there is bright sunlight available. During the period when it is cloudy outside she has to use the tube light. As our Government has weird way of billing the electricity usage which costs more if you use more than 500 units/ 2months. If it is under it is cheaper. So to cut down on the consumption and to avoid using a big 26W tube light, we decided to buy a LED table light like this one but this was pricy at Rs.1,521 (approx $24, hey I know it is quite reasonable, but at 1k+ rupee is a big deal in India) which was the only one that looked nice and has the functionality we needed.
So not willing to shed that amount for a light my mom said NO. Therefore I decided to make a powerful LED Table Lamp that doesn't take the useful space on the table for her so that there is enough light available for her to work with and doesn't have to turn on the tube light.
Step 1: Stuffs You Require
I decided to make the circuit and the fixture myself, but found out that there is cheap LED light bulb with B22 base.
Therefore decided to use the internals of that light bulb and make the fixture myself.
All the parts where bought locally, hence the cost of the project may vary depending upon your location, for example a similar looking 5W LED light bulb in ebay.com cost about $1.95.
Most parts could be in your parts bin too...
Materials List:
- 5W LED light bulb with B22 base 5,000K - 6,500K (base type is not important) - ₹60 - ($ 0.97)
- PVC 4inch Diameter, 26inch length - ₹70 - ($1.13)
- 2-Wire 3 meter - ₹24 - ($0.39)
- 2-pin Plug - ₹10 - ($0.16)
- Araldite Epoxy - ₹45 - ($0.76)
- Screw & Bolt with 2 washers - ₹4 - ($0.07) Any screw and bolt will work as long as it has necessary length.
The ones used in this has the following measurements Hex head with 4mm diameter and 20mm length of the screw. - Clear Tape - (had them already) or any tape is fine.
- Heat shrink tube - (had them)
- SPST rocker switch - (had them)
Total - ₹213 - ($3.48)
Note: All conversions are from Indian Rupee(₹) to USD$ is an approximation only.
The conversion used is USD$1 = ₹62.049
Tools Required:
- Pencil or marker
- Hot Glue gun
- Soldering set (Soldering iron, solder, flux, helping hand)
- Wire stripper
- Source of heat such as gas stove or torch
- Hacksaw/ Dremel with rotary cutting tool.
- Needle Nose Pliers
- Measuring tape
- A flat piece of wood and a flat surface
- Utility Knife
Disclaimer:
You will be working with high AC voltages, so please be careful and take necessary precautions to avoid getting shock. This is lethal and must be handled with at most care. I am not responsible if you damage any of your equipment following this. It worked for me and you should be aware of what you are doing
Step 2: Planning or Designing
Since it is not a traditional table light and my mom wanted it to light particular area, the measurements need to be taken.
In order to determine the desired position of the light, the led bulb was hung over the table and fixed the point where the light is required.
Using a measuring tape the measurements were made and I used CATIA V5 to roughly design the look of the light.
The design was drawn onto a newspaper and cut to make a template to make it easier for drawing it on the pipe (pic2).
Note that certain design changes were made during the project to make it look and work well and is explained in appropriate steps. For example in the design the light area is flat and round whereas in the original one it will be curved (the curvature of the material is kept as to avoid light reflection, if it was flattened it would be uncomfortable to use it).
If you do come across doubt in any step feel free to ask in the comments.
The measurements were as follows:
Length - 24"
Height - 16.5"
Width - 1.5" for the Vertical Column and 1.14" for Horizontal Column.
3" at the Bottom of the Vertical Column and about 3.5" at the place where the light will be.
Note: the measurements are made when viewed in 2D and thus the curvature of the material is not taken into account.
Step 3: Disassembling the LED Light
The decision to use the internals of the bulb instead of the whole unit was to make it small. Initial thought was to cut of the bulb just below the ventilation holes and to glue it onto the light portion of the fixture. Since my mom doesn't like to have the diffuser on it as it reduces the amount of light it was removed from my plan and decided to use only the PCB.
To disassemble the light:
- Hold the sides of the diffuser closer to the base as shown in pic2. and gently push on the sides and pull out, it should come of easily.
- The PCB was held by couple of drops of hot glue on the sides, it came of fairly easily as well.
- In order to remove the PCB the wires has to be freed as well. The wires were held in by a couple of rivet kinda thing that makes contact with the B22 base to power the light.
- Use a needle nose pliers to pull it out and the wires will be free, now the PCB comes out of the enclosure.
Pics. 6-9
As expected the circuit is very simple to replicate, nothing fancy like the LED Driver, but I liked the white solder mask on the PCB... :)
Step 4: Making the Fixture: Cutting
To make the fixture my material of choice was to use PVC pipe due to following reasons.
- Easily workable.
- Readily available.
- Requires only the tools I had on hand.
- Cheap.
- Looks neat and doesn't require painting (but can be painted).
Take the template and stick it onto the PVC using clear tape to make it easier to trace the outline.
Use pencil or marker to mark the outline. (Tip: I used pencil to mark by making continuous strikes see pic3)
Remove the paper and start cutting.
I thought of using my rotary tool with rotary saw attachment for cutting the PCB but the attachment is not properly centered and thus not suitable for this. So a simple hacksaw was used to cut along the marked line on the PVC, it was fairly easy but took some time.
If you are unable to cut along the line, cut it outside the line, it can then be sanded or cut properly later on.
Remove the burrs by running a utility knife along the edges.
Cut all the required pieces. There are total of 4 main pieces, 2 vertical pieces and 2 horizontal pieces. The shorter ones of the vertical and horizontal pieces are to cover the longer ones for aesthetics and make it more stable.
Since the width of the column is small it has tendency to bent under its own weight, esp. the horizontal one as it is slimmer and longer.
I also kept the wastes to use them if required.
Step 5: Making the Fixture: Bending
In order to make the connection between the vertical and horizontal column, the PVC has to be bend at a couple of places and also have to be bend so that it can rest on the table and also grabs the table.
The short and longer vertical and horizontal pieces are taped together to make the marking and bending easier. Use clear tape at few places to keep them aligned.
Before bending we need to mark places for holes, cutouts and bending places. You can do certain markings later but it is easier to do it beforehand.
In the pics 1 & 2, the holes to join the vertical and horizontal column are marked with a dot and a line is drawn in the place where the bend needs to be made so that it turns 90 degrees for easier attachment between vertical and horizontal column.
Also a line is drawn at the bottom of the vertical piece, the bend portion will be resting on the table.
In order to bend the PVC we need to make it softer. Swiftly and continuously move the area of the PVC to be bent above the lighted gas stove. Keeping it exposed the flame for longer time tends to make the PVC to catch fire and makes black spots. Ensure that the tape is not exposed to the fire
Once the PVC goes soft (you can see it bend on its own) place it on a flat heat resistance clean surface and place a piece of flat plywood on it (pic5), apply pressure with one hand and turn the PVC with other hand to the required position such that the bend made is 90 degrees to the rest of the PVC pic6.
In pic 7 you will see a curved PVC piece that is on the bottom of the vertical column, this is to cover the place where the switch is placed. For this I have used the torch to make the top portion of the cover bendable, doing so it caused the PVC to catch fire and blackened it. So I used some sand paper to remove the blackness and hence is can see it white in color.
Step 6: Making the Fixture: Drilling, Making Holes
I don't know how I missed it, but I forgot to take the pictures when drilling and making the hole for the switch. But it is rather an easy step.
Make hole appropriate for the screw size you choose. There are a total of 4 holes to be drilled and one hole for switch to be made.
One hole is for joining the vertical and horizontal column.
Second is for the clamp portion to be attached to the vertical column.
Third hole is for the wire to exit the vertical column.
Fourth hole is for the wire to enter the horizontal column.
Last hole for the switch. Mark the position for the switch ensuring that it does not get in the way of the clamp and then drill and use utility knife to carve away the unwanted material.
Step 7: Making the Fixture: Epoxy Time
This is pretty straight forward. The epoxy is applied at the joints of the shorter and longer pieces of the vertical and horizontal column. This is done, so that it adds strength to the column and doesn't cause it to bend on it own weight and also makes the edges sealed.
I had to apply epoxy one one side and wait for it to cure and then only able to apply on the other side. The epoxy I used cures overnight and hence it took longer. You can overcome this by using 10 minute epoxy if you want to reduce the time. I only had access to this epoxy. The Light showed in pic4 is not connected yet.
I mixed the epoxy in small batches so that it is easier to work with. Read the instructions provided with your epoxy before commencing.
After the epoxies cured the tape was removed and the epoxy was applied to those areas as well.
Step 8: Making the Fixture: Wiring and Soldering
Time to wire up the light to the fixture. As the LED circuit is already ready, we need to extend the wire and connect a switch to one of the AC wires going to the light.
Wiring Horizontal Column:
Take the horizontal column and thread the wire through the hole made near the bend.
Pull a little excess wire when it shows up where the LED would go.
Strip the insulation using wire stripper and tin them.
Put a piece of heat shrink tubing over the two wires.
Solder the circuit to the wires and insulate the exposed connection using heat shrink tubing. A cigarette lighter is used to shrink the heat shrink tubing.
Pull the wire at the end of horizontal column to pull the circuit in place.
Wiring Vertical Column:
Now take the wire coming out of the horizontal column and thread the wire into the hole made in vertical column.
When it exists at the bottom of the vertical column, place the switch in the hole.
Now carefully cut one of the wires and separate a small length of wire on either side
Tin the exposed wires and solder them to the switch.
Make a knot on the wire at the bottom as a strain relief.
Connecting the plug:
Now strip the end of the wires and tin them.
Open the plug and attach the wires.
Step 9: Making the Fixture: Hot Glue Time
Now hot glue a nut which will hold the clamp in place. Careful not to have hot glue in the threads of the nut. Its a pain to remove.
The cover for the switch is hot glued in place.
The clamp is secured with the screw and that's it....
Your LED Table Light is ready... It is adjustable and consumes only 5W and lights up the whole table and more.
Note: You can make the clamp adjustable by elongating the hole in the vertical portion of the clamp.
Any suggestions and comments are welcome.
And kindly vote for it, if you like it
This instructable is entered in Make Energy Contest and Burn it!!! Contest, do vote for this if you liked it. Thanks.
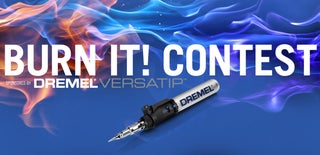
Participated in the
Burn It! Contest
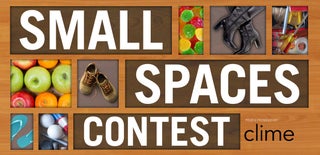
Participated in the
Small Spaces Contest
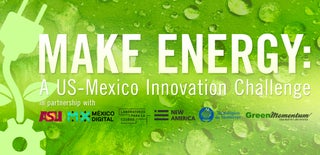
Participated in the
MAKE ENERGY: A US-Mexico Innovation Challenge