Introduction: A Warm Wooly Coat
I usually get the urge to make myself a nice warm coat in January or February, and by the time I have collected my pattern, fabric, lining, and notions, the weather begins to turn warm, and I lose interest.
This year, I decided cold temperatures were bound to return for long enough to need a new piece of warm outerwear, so I went ahead and made myself a coat with this thick textured pink wool. This is the result!
Step 1: Picking a Pattern
I loved this swing coat pattern as soon as I saw it!
My first step is usually to make a muslin. For this particular design, I skipped that step. I happened to have enough of a navy blue mystery fabric that I picked up at a fabric swap. I also had run out of muslin, and I wanted to get started on my project, so the blue fabric came in handy.
Because the garment is not fitted, I felt comfortable jumping right in, especially with a not-so-precious fabric.
Turns out, I was right - I love a swing coat, and this design is no exception.
Of course, the mystery fabric I used for my wearable muslin is a mid-weight textile with a fair amount of drape. That is nothing like my pink wool, but I felt comfortable enough to proceed with a good idea of how this pattern fit my body.
Step 2: Lining First, Instead of Last
Over the years, I have figured out that I like constructing the lining of a coat before the shell. There are times when this is not possible (sometimes I am not sure what lining fabric I will be using, or I am waiting to purchase it, etc.) but if I can, I cut and stitch the lining before the rest of my coat.
If you do this, once the shell is complete, you only have to attach the shell to the lining, hem, and you have a completed coat! On the other hand, if I wait until the pattern instructions mention the lining, I get slightly aggravated after working so diligently on my wool coat that I have to make another coat out of lining material before I can call it finished.
It is a silly trick I play on myself, but it continues to work for me, so I am going to keep constructing jackets and coats in this way!
Step 3: Sewing With Thick Fabric
But first I had to figure out how well my machine was going to handle multiple layers of the thick wool. A couple of scraps convinced me this was going to work . . . and that I would be spending a lot of time at the ironing board!
Really, the only thing that I changed on the machine was to increase my stitch length.
And my clapper got a workout with this wool. This is a piece of hardwood that you apply with pressure after using a steam iron. The wood absorbs the excess moisture and locks the heat directly into the fabric (where you want it!).
After each seam was put through the sewing machine, I lugged the growing coat to the ironing board and put my iron through its paces. The clapper came through like a champ. My iron, on the other hand, had a bit of a fit. It has always spit sporadically, but it is getting rather obnoxious as of late. But I persevered!
Step 4: Steam Heat
I spent way more time at my ironing board for this project than sitting at a sewing machine, which is as it should be. The only real way to tame a thick fabric is with heat and steam. When a fabric is particularly thick, a clapper is an invaluable tool.
The first step is to press your seam flat, just as you put it through the sewing machine. This sets the stitching line.
Next, open the seam, and press again.
The final step is to press down on that freshly pressed seamline with your clapper. This will really make that seamline lay down nice and flat.
You may have to repeat the process again depending on how springy or thick your fabric is.
Step 5: Added Pockets
I managed to avoid closures on this coat, mostly because I just was not willing to fight with such a bulky textile and make bound buttonholes. The pattern has the option of welt pockets, but again, not going to deal with cutting a fussy opening like that in this wool (did I mention it is really, really thick?!).
For my first version, I added side seam pockets - because a coat without pockets is not very useful. But I wanted something a little more interesting this time around.
Patch-pockets for the win!
Of course, there is no pattern piece for a patch-pocket included with this design. In order to easily play with size and placement, I cut a version out of bond paper and pinned them to my in-progress coat shell. This is a cheap and easy solution.
I originally thought I wanted extremely oversized pockets, but once I pinned those on the coat and stepped back, I realized I would prefer something slightly smaller. The paper pockets also allow you to play with directionality of the pockets. I decided to place mine on a slant, rather than following the grain of the front coat pieces.
Once I figured out the size I liked, I cut two pockets out of wool, and two out of my lining fabric. I ended up applying these by hand because of the bulky fabric. I also reinforced that hand stitching by back stitching on the wrong side of the coat front just inside the pockets.
Step 6: Don't Forget to Catch Stitch and Grade Your Seams!
One way to tame seam allowances is with an iron. Another helpful thing to do is catch-stitch those allowances to an underlining (not used in this project) or even opposing seam allowances. This keeps seams allowances from shifting. You don't want to pull those stitches tight or it may pull your garment in strange ways, but a loose catch-stitch allows for a bit of movement, while also controlling the edges. [Because the catch-stitches are rather large, they should not be visible on the final garment as they might easily catch and pull. In this instance, the coat will be lined, and those stitches will be protected.]
A loose catch-stitch can also hold portions of the garment together. For this coat, the neckline seam is stitched together from the inside to keep the outer shell and the lining sandwiched together at this point. This also helps keep the collar and under collar where you want them. The rest of the garment will hang from the shoulders, but with such a heavy wool, without that connection, the outer shell would pull downward and separate from the lining.
And, of course, the heavier your fabric, the more important it is to grade your seam allowances. In other words, two identical seam allowances pressed in the same direction will create a large lump, but two slightly different widths will create less of a lump. Just make sure not to cut into your garment! [Duck-billed scissors can be helpful in some cases. I also like to use pinking sheers when I grade seam allowances as they can help to keep fabrics from unraveling - this is especially useful on the allowance that is getting cut down closest to the seamline.]
Step 7: Reinforcing a Loose Weave
There are the two darts on the coat front pieces that require clipping corners. I used my trusty silk organza scraps and this trick to keep things from raveling. The silk adds very little bulk, and the tight weave acts as a barrier between the clipped portion of the fabric and the remainder of the fabric. This is similar to the idea of stay stitching, but is much more stable (especially for a loose weave fabric).
I also dab a bit of Fray Check at the base of the clip for added security if I am worried about any clipping.
The Fray Check is also helpful when curved seam allowances need to be clipped in order to lay flat. I avoid using the product when I am not lining a garment because it can dry hard and irritate my skin. But if a lining or facing is going to cover those bits, I highly suggest trying it!
Step 8: Interfacing (fail)
I usually go for a sew-in interfacing because I have such bad luck with fusibles. This time around, I thought that this fabric would do much better with a fusible, so I decided to go for it. I dunked my interfacing in a little water and hung it to dry so it would not shrink under the steam of the iron. I fused and let it completely cool before moving my fabric. And yet, it still started to pull away from the fabric during the construction process.
Next time, I will try another brand, but in most cases, I believe I will stick with my tried and true sew-in interfacing!
The good news is, the interfacing in this coat is caught in the seamlines, so although it will probably continue to pull away from the wool, it is going to stay in place within the body of the coat.
Crisis averted!
Step 9: Take a Step Back and Admire How Far You Have Come!
There are times during the construction of any garment where it is a good idea to step back and look at what you have accomplished. That mound of fabric on your sewing table that you have been lugging back and forth from sewing machine to ironing board to cutting table and back again can be exhausting. So take a step back and look how far you have come!
And don't dwell on the mistakes. They become overwhelming when viewed up close, but standing back and looking at the project as a whole can really give you some perspective.
And it's beginning to look like a coat, isn't it!!
Step 10: And Then Get Back to the Ironing Board!
I cannot stress enough how important a role your iron plays in the making of a garment. This coat required a lot of time, and a bit of muscle with my iron and clapper. Keep going back to the ironing board after every step - your finished project will thank you!
If you don't have a clapper, a piece of hardwood will work - just make sure it's clean and splinter free!
Step 11: Before Hemming . . .
I love my rayon seam binding! Most of my hand made garments include this product in one way or another.
In this case, I used it as a hem tape, to cover the raw edge of the hemline. I find that the rayon is far superior to the polyester hem tape that can be purchased at the fabric store. This stuff won't melt under your iron!
Because there was a bit of fraying with this bulky wool weave, I used a small zig zag stitch to attach the seam binding instead of a straight stitch. This will help to anchor the lightweight rayon to the thick wool fabric.
The seam binding will also cover that small portion of raw edge where the facing meets the hem.
Don't be afraid to think outside the box when it comes to sewing notions.
Step 12: Hemming
I like to use catch-stitches for hemming when I will be using a full lining. The stitch allows for a nice controlled hem with the added benefit of being a very elastic stitch. This means the hem can drape nicely.
Step 13: A Helping Hand
In order to keep the facing pieces rolled to the inside of the garment, I used silk thread and very large basting stitches. The heavier the garment, the more challenging it is to wrangle things at the ironing board.
This is especially helpful at the collar edges, but I extended those stitches down the front opening, as well. It is so much easier to let those stitches do the work instead of one hand manipulating the fold while you hold an iron in the other and have to grab the clapper next.
The stitches don't have to be pretty; they just need to keep the edges where you want them!
Step 14: Finishing Touches
One of the final bits of finishing is hand stitching the lining to the hemline. Some people prefer to bag a lining (everything is machine stitched), but I like the control that hand sewing give me.
Step 15: And a Bit More Ironing!
And one final thing:
Before you remove those basting stitches from the opening edges and collar of your coat, give it one last good press! Lean into that clapper, and get those seam allowances nice and flat.
And then those large basting stitches come out, and you have your finished garment!
Step 16: And . . . Finished!!
Now it's time to enjoy my new wool coat - before the Spring weather arrives! Although, I believe this coat will be with me for many years to come, and there will be many more cold days on which it will come in handy.
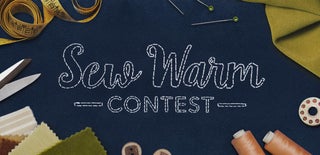
Second Prize in the
Sew Warm Contest 2018