Introduction: Appalachian Stick Dulcimer
I went searching for how to play the outro music for the Squidbillies cartoon on the banjo, and it turns out it isn't a banjo. There is a video of a guy playing the song on a Strumstick, and I had to have one after I saw it. It is like a banjo, only twangier, and easier to play.
I'm not really sure what these are called. I think Strumstick is a brand name for a stick dulcimer, and my buddy said it is called a Woodrow. The tuning pegs aren't really like a Strumstick, it doesn't have enough strings to be a Woodrow, and stick dulcimers look like mostly round bodies. But it sounds good and is fun to play.
What makes it Appalachian? I built it with hand planes my grandfather used to make a living in West Virginia almost 100 years ago. The fretboard is made from a piece of cursed Hickory from my property in North Carolina. It has strong ties to the Appalachian mountains, so I'm calling it Appalachian. Get yourself a jar of white liquor, and keep reading.
There are measured drawings attached in the last step.
I relied heavily on two other Instructables for building this:
Step 1: Tool and Material Selection
The tale of my cursed Hickory log
Fretboards are traditionally Rosewood. But I wanted some real Appalachian hardwood. I started with a +1000 pound log of Hickory from a tree that was taken out when they cleared the lot for my cabin in NC. The log broke my skyline when I was winching it off the mountain onto the trailer, but my welds held up when it rolled down and crashed into my trailer. There are no guard rails up on a private road in the mountains, just loose gravel and steep drop-offs. As I towed the log down the mountain, all eight wheels started sliding. The trailer started catching up to Jeep, just as I was headed for a steep dropoff. To get out of the jackknife, I floored it, and pulled the trailer back straight as I dogged it around the turn. When they loaded the boards on the trailer at the sawmill, the Jeep wouldn't start. It broke down again in the middle of Kansas, 600 miles from home, but I fixed it and drove ten hours with transmission fluid in my hair. I got my 'free' wood back to Colorado to dry in the semi-arid climate, and started using it for projects. I've had wood from this log bang into me, drop on my fingers, and I had to go have my urine tested for blood after a big chunk flew back out of my table saw and left a dinner plate sized bruise on my gut. If you had said a tree could be cursed by evil wood spirits before all this happened, I would have laughed. I'm not laughing now, this log tried to kill me three of four different ways. I think the wood really could be cursed. But now that this instrument is finished, I think it makes a more genuine mountain sound.
Other, less cursed, materials
The neck and body sides are made from a 1-1/4" block of Ash. Ash is
hard enough to make baseball bats, but flexible enough to make shovel handles. This is going to need to be flexed, so even though the grain is a bit ugly for my taste, Ash is the material of choice. Check out the picture showing how far a 3/16" strip will flex.
The metal parts are brass. The round stock is 3/16", the other pieces can be cut from 1/4" x 3/8" flat bar.
The bridge is made from a Purpleheart pen turning blank.
Tools
I guess this could be made using a good rip saw, hand plane, spokeshave, rasps, and a bit and brace. But good luck with that. You really need at least a bandsaw.
Big equipment: bandsaw, jointer, dual-drum sander, table saw, drill press, milling machine, 12" miter saw, oscillating spindle sander, belt sander, 5hp dust collector, and a Husky vacuum.
Hand tools: spoke shave, hand planes, punch, small ball pein hammer, metric yard stick, combination square, marking knives, fret saw, diamond honing plate, round rasp, divider ground to blade edge, compass, tape measure, hobby knife, and a mechanical pencil.
Software: Fret Position Calculator on stewmac.com, search 'tuning a strumstick' for tuning videos, and search 'squidbillies outro' for inspirational music.
Store-bought Materials
Maple sound board at Woodcraft
Step 2: What We Are Making
I've been reading woodworking magazines for decades, and something always bugged me. The articles always show step by step construction, but never showed pictures until the end. How am I supposed to get excited about making something by looking at pictures of a board in saw? The board in saw photos are coming, but first, check out the end goal.
Step 3: Shape the Neck
Mark a little over 1-1/4" from a good flat side and mark for the bend of the headstock as shown in the plans. The goal is enough bend that the top of the tuning peg is below the nut.
Rip the neck on the bandsaw, then flatten the headstock to a consistent width, and get where the fretboard will glue perfectly flat.
Carve the back of the neck with a spokeshave. Hold it like you are playing to get a feel for how you want it shaped.
Step 4: Machine the Headstock for Tuning Pegs
I cut the curves in the headstock before I installed the tuning pegs, and wish I hadn't. Try leaving it square, layout for the pegs, then get funky with the curves. Cut small pilot holes like the other Strumstick instructables suggest (I wish I had). Cut a countersink for the washers with a Forestner bit, then make centered holes for the tuning pegs. Use a round rasp if things don't line up.
Step 5: Split the Neck to for the Sides of the Body
Cut a hole in the neck sized to leave 3/16" of material on either side. I can't overemphasize how important it is that this hole is perfectly centered.Use a magnifying glass, use digital calipers, do whatever you have to do to keep you whole instrument from being lopsided. I used a 7/8" Forestner bit.
Use the marking gauge to transfer a line down the the end, darken with a pencil, then cut it on the bandsaw. These saw cut tails can be cleaned up, but it is hard to get in there with a tool, so take your time on the bandsaw and get it straight.
Step 6: Cut and Clamp the Bottom of the Body
Soak the board in warm water while cutting the bottom of the body. Mill the block of maple that will make the bottom piece down slightly thinner than the sides of the body, then plane the body sides later. It is way easier than trying to mill the block after.
For the curve, splay the body sides out to five-inches. Five inches is the width of the store-bought maple sound boards.
Mark the angles on a piece of paper, then cut the block to match. The measured drawing at the end shows the geometry. The bottom can go straight across, curve in or out. It doesn't change the sound that much, so use some artistic discretion. Just keep in mind you will need to mount a tailpiece later.
Save the angled blocks that you cut from the square blank, and use them to keep a square clamping surface.
With the clamps on, sight down the fretboard and make sure the block is centered. If it isn't, clamp a board on the fretboard, then pull the sides of the body square, and clamp the bottom of the body. It should flex pretty easily.
Step 7: Glue the Fretboard and Soundboards
Mix some hide glue with water, and let it soak for an hour or two.
Clamp the fretboard and soundboards in position, then do what they call 'scarfing in'. Where the two pieces meet, there will likely be a small gap. Saw down into the gap and stop just before hitting the neck wood. Then presto, your joint will perfectly mate when you slide it together.
Hide glue sets up really fast, so pre-heat the wood with a heat gun, then quickly slather on the glue and clamp on the fretboard. Same for the soundboards. Do one side, clamp, wait in hour or so, then do the other side. I tried doing both sides at once, and my glue line is a bit thick in places.
Clean up the overhang on the sander, with a hand plane, a flush trim router bit, or however you like doing that.
Step 8: Make a Fret Saw
The fret wire specifies 0.023" kerf, and my local Woodcraft (Loveland, Colorado) didn't sell anything in that width. The store owner recommended getting a saw a little wider than what I need, and lapping the saw teeth on a diamond hone to get the right width. It worked great, you can see the before and after measurements.
Step 9: Install the Frets
The fretboard is 1/4" thick Hickory. I cut slightly oversized, then made a sled and ran it through my Grizzly dual drum sander until it looked right. If you don't have a big sander like that, a planer would work, or even a long sanding block. It needs to be really flat when you are finished.
Use the Stewmack calculator to get the fret measurements. I laid these out for 24" between the nut and bridge.
I went metric for the fret spacing, and used a meter stick to make little tick marks with a razor knife, then went back with a square and made a heavy cut for every fret. Marking knives work great for this step.
Four blocks of scrap wood are squared up, and used to make a miter box. Use a piece of paper to shim the blocks slightly wider than the saw blade, then clamp and nail the blocks in place.
If, like me, you haven't ever tapped in frets, practice on a piece of scrap. Start at an angle, and tap back and forth. Then put a block of hard wood over the fret and use a c-clamp to get a level seat. Finish the ends with a file or sander.
fret from nut fret to fret
1 2.618mm 2.618mm (nut-1)
2 4.951mm 2.333mm (1-2)
3 6.020mm 1.069mm (2-3)
4 7.982mm 1.962mm (3-4)
5 9.730mm 1.748mm (4-5)
6 10.530mm 0.801mm (5-6)
7 11.286mm 0.756mm (6-7)
8* 12.000mm 0.714mm (7-8)
9 13.309mm 1.309mm (8-9)
10 14.476mm 1.166mm (9-10)
11 15.010mm 0.535mm (10-11)
12 15.991mm 0.981mm (11-12)
13 16.865mm 0.874mm (12-13)
14 17.265mm 0.400mm (13-14)
15 17.643mm 0.378mm (14-15)
16* 18.000mm 0.357mm (15-16)
17 18.655mm 0.655mm (16-17)
18 19.238mm 0.583mm (17-18)
Step 10: Machine the Nut
Cut a little long with a hacksaw, jigsaw, sawzall, or however you like to cut soft metal. Use a belt sander to get to final length. Remember from sixth grade how to find the center of a line using a compass? Do that, then measure one centimeter from each side for the top and bottom strings. Cut light slots for the three strings with a hacksaw.
Step 11: Machine the Trapeze Tailpiece
Cut 3/16" brass rod to 3-1/2", round the ends on the belt sander, then thread one end with a 10-32 die. The length of the threads is about 1/2". Hammer the other end flat, layout two holes on the flat, then drill and countersink. Brass will bend, but if you do it too quick it will break. Put it in the vise, and use little hammer taps to get it at 90-degrees.
For the bar, layout the holes, and drill carefully. Mine is a little crooked.
Step 12: Machine the Trapeze Tailpiece Bar
Rough cut to length, then clean the sides on a belt sander.
Use an industrial Sharpee like machinist layout fluid. Set the dividers to roughly half the width of the bar, then make a little tick mark and adjust the width until it marks the same place from either side. Scribe the length of the bar to establish a center line.
Find the center the same way as the nut, then measure in 3/16" from each end for the 3/16" hole for the angled round bars.
When you center punch, you should be able to feel the scribe lines and get the punch tip in the trough. Use a center finding bit to widen the punch mark, then drill to size.
Step 13: Machine the Bridge
Mill a slot in the center of a pen turning blank, then round the ends of a 3/16" round stock on the belt sander. Cut the slot a little deeper than half of 3/16", then put shims under it to get the strings at just the right height. Shape the wood however you like, but be sure to keep a consistent height.
I really like how this piece came out.
Step 14: Final Tuning
For strings I used:
0.010"
0.014"
0.023" wound
I got enough strings to make four instruments, and a couple of the non-wound strings were off by a thousandth. It would take a really good ear to hear the difference.
Dry fit all of the machined pieces before finishing. Adjust the height of the bridge, the angle of the tailpiece. I countersunk and screwed the nut in place, but you can use epoxy if you get the metal really clean and oil free.
I sanded with 220 grit, using a random orbit sander attached to a vacuum. Two coats of shellac are under three coats of rattle-can acrylic clear. I normally use spray polyurethane but ran out, so I went with acrylic. It looks nice, but 24 hours after spraying, it still reeks. The shellac makes the figure of the wood really pop.
If any frets buzz, or hit the strings when a note is played above them, lightly file them down. Just go slow, and test all the notes. You can't put material back on if you grind it to far down.
For tuning, an electronic tuner works really well.
Now get to picking.
Step 15: Measured Drawings
The fret board is 1/4" thick.
You will notice this is a mix of inches and millimeters. If I start with a piece of 3/16" rod or 5" wide board, I usually use inches to describe the measurements. My drill bits are all inches, so I used those. But 10 mm worked out really well for spacing the strings, and that has major tick marks on my ruler, so I use metric there. There isn't a real system, it is just sometimes easier for me to use one or the other.
I can't predict the future, but as of 2017 I keep up with Instructable messages pretty well. If you are building one of these, feel free to ask questions, or post a picture of your work.
Attachments
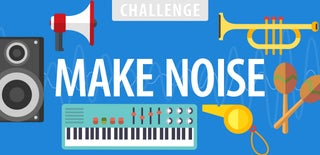
Runner Up in the
Make Noise Challenge
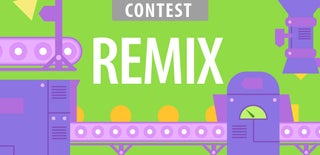
Participated in the
Remix Contest 2016