Introduction: LED Light Fixture Design and Construction
Lights with high color rendering index (CRI) were needed for an art studio setting. Several lighting options were considered including: incandescent and halogen bulbs, light-emitting diode (LED) replacement bulbs, compact fluorescent lights (CFLs) and light fixtures containing built-in LEDs.
Incandescent and halogen bulbs were ruled out because of there relatively short life and lower efficiency. CFL and LED replacement bulbs are both adversely affected by excess heat, making them ill-suited for enclosed light fixtures. The most appealing option is a fixture designed with integral LEDs and proper heat dissipation.
The following will cover generic LED lighting design considerations along with construction details.
Step 1: Materials
(Materials and instructions to build two lights)
Light-emitting diodes (LEDs) (6X Bridgelux bxrc-30h2000-c-23)
- Several aspects need to be considered when selecting LEDs. The first is how much light is needed for the space. Keep in mind that LEDs provide highly directional light, when compared to an incandescent bulb filament, allowing more of the light to be pointed at the work area. Consider how many lumens are currently being used and if more are desired. Also note that perceived brightness is not linear with light output. Two times the lumen output does not correlate to a two times perceived increase in room brightness. (Each of the chosen emitters has a max rated output of ~2000lm and 1189lm at 500mA)
- Color temperature and color rendering index (CRI) are two important parameters. Color temperature determines how blue the light will look having units of kelvin (K). Larger numbers are more blue. A typical incandescent bulb has a color temperature of 2400K, while tungsten-halogen bulbs are at 3200K. (The selected emitters have a nominal value of 3000K but appear less yellow when compared to a tungsten-halogen). Color rendering index determines how accurate the light reproduces the color of illuminated objects. The number is unitless, from 0 to 100, with 100 being ideal (selected emitters are at 97). The number alone can be misleading as the full range of CRI test colors should be examined, R1 to R15.
Constant current driver (6X Harvard cl33-700s2a)
- LEDs have a nonlinear current response to input voltage and also a weak temperature dependence. A constant current driver is needed to maintain consistent power and prevent emitter damage. The current source should have an output voltage that covers the operating voltage range of the emitter. It should also deliver sufficient current to achieve the desired light output while staying under the upper current limit of the emitter. Keep in mind that increasing current decreases light output efficiency.
- Multiple LEDs can be powered from a single driver when wired in series. Each LED experiences the same amount of current. The driver needs to deliver the amount of current needed for a single emitter but supply the sum of all the LED voltage drops.
- Constant current drivers can be purchased with AC or DC inputs with a range of input voltages. LED dimming is also possible with two common input signals. Pulse width modulated (PWM) signals set the brightness as a function of duty cycle, while an analog 0-10V DC signal sets the brightness as function of analog voltage. Drivers may also have adjustable upper current limits that are set during installation. (The selected drivers have a 500mA or 700mA upper current limit with analog 0-10V dimming. They accept 120-277V AC and can deliver 16 to 48V DC to the LED)
Heat dissipation (6X desktop CPU aluminum heat sink)
- Proper heat dissipation is critical for the longevity of the LED and constant current driver. LEDs have an upper operating temperature limit of around 100°C depending on the selected device with an inverse relation between life expectancy and temperature. LED failure is normally defined as a predetermined reduction in lumen output and light quality in the form of CRI and color temperature. Time to reach failure can be quite long, 50,000 to 100,000 hours if the LED is kept cool enough. LED degradation immediately starts when powered, with the operating temperature determining how many hours of operation will pass until noticeable changes in light output occur. It is in one's best interest to keep the LEDs as cool as possible if they were selected for their superior light qualities.
- Constant current drivers have the same inverse relation between temperature and life expectancy, except that at 100°C, life expectancy is drastically less than 50,000 hours. This is a result of electrolytic capacitors degrading at elevated temperatures. A typical 105°C rated electrolytic capacitor operated at 105°C has an endurance value in the range of 2,000 hours. This is unacceptable if one expects to get 50,000 hours of use out of the LED. The solution is to keep everything as cool as possible! (Preferably less than 50°C)
Light diffusion (2X 16.5x16.5x0.118" ACRYLITE Satinice 0D010 DF)
- A good quality diffuser reduces glare from the extremely bright emitter surface and evenly spreads the light over the work area. A diffuser material should provide high light transmission with large amounts of scatter. The selected diffuser accomplishes this with many small embedded spheres with a dissimilar refractive index than the surrounding acrylic substrate.
Structure materials
- 2X mild steel flat bar, 4x0.125x51"
- 2X 3/16" mild steel plate, 5x5"
- 4X mild steel flat bar, 0.5x0.125x51"
- 14X mild steel round bar, 0.25x12"
- 2X aluminum plate ~1/8" 16x16"
- Thin aluminum flashing.
Hardware
- 24X #6-32 1/2" screws
- 12X #6-32 5/8" screws
- Junction box screws
- 12X #6 washers
- 12X #6 clearance 0.5X0.5" standoffs
- 16AWG hook-up wire
- Thermal paste
Step 2: Form the Main Hoops
- Cut two pieces of 4" steel flat bar to 51".
- Bend the loops into shape. A flat bar roller is ideal for this task if you have one. I bent the hoops using an arbor press and parallel 1/2" bar welded to a plate 4" apart.
- Check that the ends of the bar evenly line up after bending.
- Weld and grind the ends to form a smooth seam.
Step 3: Install Bottom Lip
Create a lip on the bottom inside of the hoops using two 0.5X0.125" flat bar to support the diffuser.
- Cut the first bar to fit inside of the hoop.
- Tack weld the bar in place, inside the hoop, along the outer edge using clamps to hold the bar flush with the hoop.
- Cut the next bar to fit on top of the first.
- Tack weld in place using clamps to hold flush with the first bar.
- Weld and grind the entire edge creating a rounded smooth profile.
- Repeat steps for other hoop.
Step 4: Form Steel Chain
- Cut 12X 12" pieces of the 1/4" steel round bar.
- Use a wire bender to form chain loops with 1/2" openings on both ends of the bar.
Closely examine pictures and look at these instructions for building and using the wire bender.
Step 5: Ceiling Plate
- Cut and grind two 5" circles from the 3/16" steel plate. (I only had 4" wide material on hand so pieces were welded together)
- Drill and deburr a 3/8" center hole to pass the wire through.
- Drill two 13/64" mounting holes that line up with the mounting points in the junction box.
- Drill 6 1/4" radially spaced holes (see pictures) to mount the support loops.
- Bend and cut 6 U shaped pieces from 1/4" rod to fit into the support loop holes.
- Weld the loops in place.
Step 6: Drill Main Hoop and Install Chain
- Drill 3 evenly spaced 1/2" holes offset 5/8" from the top edge of the hoop.
- Connect the chain links together, closing the links on the ceiling plate and middle. Leave enough gap in the bottom link to remove from the hoop.
Step 7: Prep and Seal Parts
- Remove the chains from the hoop.
- Grind, sand and clean all steel parts until desired surface quality is achieved.
- Wash all parts to remove any residual oils.
- Apply steel aging chemicals for desired finish.
- Apply a furniture paste finishing wax or other metal sealer.
Step 8: Cut Diffuser and Center Support Plate
- Trace the inside shape of the hoop onto the aluminum sheet and acrylic diffuser. Make sure to mark the orientation as the hoop is not perfectly round.
- Cut the aluminum sheets using a reciprocating saw or metal band saw.
- Drill and tap #6-32 holes in the aluminum plate for mounting the heat sinks and constant current drivers. Also drill holes for the LED wiring.
- Cut three holes in the aluminum plate for the underside of the heat sinks to pass through.
- Cut the acrylic diffuser to shape using a band saw.
Step 9: Prepare the Heat Sinks
- Drill and tap #6-32 holes for mounting the LEDs in the center of the heat sinks.
- Drill #6 clearance holes on the tabs of the heat sink for mounting to the center aluminum plate.
- Sand a flat surface on the heat sinks for mounting the LEDs.
Step 10: Assemble Center Support Plate
- Mount the constant current drivers on the 1/2" standoffs using #6-32 x 5/8" screws into the center plate (the standoffs help isolate the drivers from the warmer aluminum plate).
- Apply a small amount of thermal paste on the heat sinks where they make contact with the aluminum center plate.
- Attach the heat sinks with #6-32 x 1/2" screws and washers to the plate.
- Apply evenly a small amount of thermal paste to the backside of the LEDs.
- Install the LEDS using #6-32 x 1/2" screws to the heat sinks.
- Wire the LEDs to the drivers.
Step 11: Final Assembly
- Install the diffuser into the hoop by applying caulking around the lip, taking care not to leave any on the visible portion of the diffuser.
- Cut strips of aluminum flashing 51x1.375".
- Cut and bend 1/8" tabs along one side of the flashing strip every couple inches.
- Install the flashing on the inside of the hoop so the tabs sit on top of the diffuser.
- Place the center plate onto the flashing ring with the LEDs facing the diffuser.
- Apply caulking where the center plate meets the hoop. Also fill any other voids that would allow dust and insects inside the light.
- Reinstall the chain links to the hoop.
Step 12: Wire and Install the Light
- Wire and install the lights following your local electrical codes.
Bask under the energy efficient, high CRI light source!
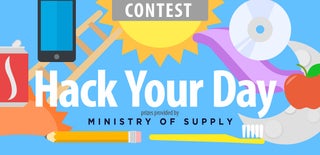
Participated in the
Hack Your Day Contest