Introduction: Autoglockenspiel
Inspirations / props where they are due:
https://www.instructables.com/id/Build-a-Programmab...
http://zebrahall.com/product/gloggomobil/
So here is my version of a programmable music box / glockenspiel. I'm posting this more as proof that such things can be made, and to give ideas of one way to do it. If you are looking for detailed plans, I'm afraid there are none. I used no plans to make this, except those I made as I went along-- Build a piece, figure out what the next piece would need to look like and build it, then figure out what the next piece would look like. If I started over I bet I could make a much better device by improving on this design. But other projects beckon, as always.
News: There is an outfit exploring producing Autoglockenspiel kits based on this design. Click here to show your interest if you think you might like a kit.
Step 1: What I Used
Tools:
- Bandsaw
- Spindle sander
- Band sander
- Disk sander
- Drill press
- Forstner bits. Get some.
- Countersink bit.
Music:
Oak Ridge Boys, "The Oak Ridge Boys Have Arrived"
Other supplies:
- A toy xylophone. Got mine for $14 on Amazon. Hohner makes toys that are actually in tune, which I read is not the case with other brands. http://www.amazon.com/s/ref=nb_sb_noss?url=search... When you deconstruct the glockenspiel save the rubber feet that hold your metal bars, since they really help the sound.
- Scrap wood. Primarily walnut, I think. Some is cherry. Some is hickory.I get a box of scraps from a local furniture factory every so often and just burn through it until I need more.
- Rubber cement to hold on the rubber feet for the notes.
- Spray adhesive to adhere paper plans to wood.
- Wood glue.
- Drywall screws. Black and grippy.
- Dowel rods. Lots of dowel rods.
- Metal washers to fit your various axles
- Howard Feed-n-Wax beeswax with orange oil
Software:
- Sketchup
- Inkscape
- http://woodgears.ca/gear_cutting/template.html
Step 2: Making the Drum
I had one good board of what was probably walnut. This defined the maximum length of the drum. I set the tablesaw to 22.5' and cut 8 staves of equal length, used the disk sander to true them up, and glued together 2 at a time. Since this is a low-stress project I didn't worry about things like tricky joints, just glue. Once I had the octagonal tube, I just rounded it off with the disk sander until it was mostly cylindrical. Exactitude ain't necessary since the drill press will set each pin to the same depth relative to the drum axis.
The octagonal end plates helped true up the gluing.
As for drilling the holes, you can see where I traced (mostly) parallel lines 1cm apart circumferentially, then 4 lines per stave longitudinally. I mounted the drum in its frame so it would rest on the center axis, then used a drill press to drill holes a set distance toward the center of the drum. It was not ideal, and some ended up off center, but again, this was meant to be a low-stress project. If I did it all again I would have made a jig to assure all holes were spaced regularly.
I laid out the gears with http://woodgears.ca/gear_cutting/template.html, then printed them and glued to some cheap plywood and cut on the bandsaw. I always use plywood for gears, since the alternating grain direction provides strength in multiple directions where single-ply wood is strong across but not with the grain.
Step 3: Making the Hammers
Since my xylophone is longer than the wood available to make the drum, my hammer tongs needed to splay out from the drum. If you can avoid this step by using wood the same length as your xylophone, do it!
I've included the Inkscape file I printed out and glued to wood guide cutting the pieces. The arms are 3mm birch ply and the hammer and axle are 1cm cherry scrap.
Attachments
Step 4: Other Pieces
This stuff had no plans, I just made them to fit the drum and hammers. There's a base to support the xylophone, a bar to support the hammers so they only hit the notes once rather than bounce, and a crank for the gear.
The pins were just cut from dowel rods, sanded on the ends, and slotted to make insertion easier. I also sanded little notches with the spindle sander to make them easier to grasp when pulling out.
Step 5: Finished Item
Here you see the amazing effect of rubbing with beeswax, before and after.
My kids love playing with it, though as with all kids their primary interest is in how fast they can turn the crank until it breaks. Fortunately it has withstood their efforts so far.
Incidentally, I also made plans for a laser-cut version, but have no laser cutter to do it on (I know, got that one backwards). If you do, and would be willing to cut me one for free, I will send you the plans. Cheers.
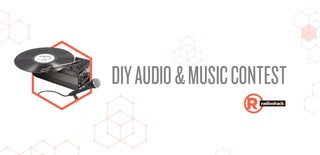
Grand Prize in the
DIY Audio and Music Contest