Introduction: BATTERY RETROFIT FOR CORDLESS TOOLS!
I own a newer 18-volt cordless combo (drill and flashlight). I also have an older 16.8-volt drill with two expired batteries. (We all know the high price of replacement batteries.)
I had to ask myself a couple of questions:
1. Do I really want to do the "non-green thing" and send this good tool to a landfill?
2. Would it not be a great idea if the older cordless drill could join my working cordless combo family?
Step 1: The New Member of My Working Cordless Family
I then searched extensively online for a way to do this, but I never found one. After careful consideration, I FINALLY FOUND MY OWN WAY MAKE THIS HAPPEN!
Step 2: Items Required for the Modification
Cordless device with bad battery – drill, saw, light, etc.
A good battery handle from the working cordless group.
Masking tape and Sharpie marker
Camera – to take pictures for reference
Hacksaw with fine blade and a bench vise
Flat File
Shop rag or old wash cloth
Dremel tool with cutting blade
Solder iron, solder and flux
2” long pieces of 14 gauge wire (1- red & 1- black)
Shrink tubing or electrical tape
A 3” x 6 1/2” piece of 16 gauge galvanized sheet metal
Four - 2” diameter screw-type radiator clamps
Flat screwdriver or nut driver that fits the screws on radiator clamps
Phillips screwdriver to take apart the cordless cases
Safety Glasses and leather gloves
Step 3: Good Battery Handle From the Working Cordless Group
I had another 18 volt battery handle with the flashlight head broken off.
The handle uses that same battery as my cordless combo.
For some reason I had kept the flashlight handle. I am so glad I did!
Step 4: Opening the Plastic Cases
With the batteries removed, use the phillips screwdriver to unscrew and carefully remove one side of each case. Use masking tape to mark the positive lead on the drill battery wire and the broken flashlight handle battery clip.
Step 5: Know How They Go Back Together
Take pictures of the inner parts as they lay in their open cases.
The pictures will be used as a visual reference during re-assembly.
Now, carefully remove the inner parts from both plastic cases.
Step 6: Old Drill Case
Screw the empty drill case pieces back together.
Use masking tape and the Sharpie to draw a horizontal line around the
outer circumference -about 1-3/4” below the trigger opening in the handle.
Step 7: New Battery Holder
Use the Sharpie to mark the outer edges of the flashlight battery handle, just above the internal battery clip holder. Screw the empty battery handle pieces back together. Use the Sharpie to make a complete horizontal line around the outer circumference of the handle.
Step 8: Cutting the Handles
Begin with the old drill case. Wrap a cloth around the case body to protect it from scratches and slipping, then clamp it between the jaws of the bench vise On the line, use the hacksaw to cut the case into two pieces. Repeat the above procedure with the flashlight battery handle. *Use safety glasses to protect the eyes.
Step 9: Cleaning Up the Cuts
Reposition each case in the vise to file smooth newly cut edges. Use the Dremel tool to cut away some of the plastic inside the drill handle so that the new battery clip will recess into that handle when the tool is re-assembled. *Use safety glasses to protect the eyes
Step 10: Preparing the New Battery Holder Clip
I ran into a little problem. The existing wires that went to the old drill battery clip were too short to reach the new battery holder and the wires on the new battery clip were too small to handle higher current. On the new battery clip, use the soldering iron to unsolder the existing small wires. Use flux and solder to install two new 2” long -14 gauge wire pigtails onto the clip. *Use safety glasses to protect the eyes
Step 11: Attaching the New Battery Clip Onto the Drill Wiring
Unsolder the drill wires on the end that went to the old battery clip. Use soldering iron, flux and solder to connect the new battery clip pigtails to the two old drill wires. Be sure to observe the correct polarity (+ to + and - to -). Use shrink tubing or electrical tape to insulate your connections. *Use safety glasses to protect the eyes
Step 12: Re-install the Internal Parts
Using your previously taken photographs as a guide, re-assemble the internal components in one half of the two outer shells. Carefully tuck the wiring in and screw the other side cover back on both pieces.
Step 13: Get the Connecting Pieces Ready
On the piece of sheet metal, use a flat file to round the corners and remove any burrs or sharp edges. Use flat screwdriver or nut driver to fully open up the screw-clamps. *Use safety glasses to protect the eyes and leather gloves to protect hands.
Step 14: Forming the Sheet Metal
Open the bench vise jaws to about 1/8”. Use the top edge of the vise to form or roll the sheet metal into a half circle. (The handle on cordless devices is 6” in circumference; hence the sheet metal is 6-1/2’ long for a good overlap when complete.) *Use leather gloves to protect hands.
Step 15: Applying the Sheet Metal
Close the sheet metal around both handle pieces. Overlap the sheet metal and tighten one screw-clamp around the circumference to hold the metal tightly against the plastic handles. *Use leather gloves to protect hands.
Step 16: Initial Adjustments
Install and tighten the other three clamps. Now you will need to remove the excess banding that extends through each screw-clamp body. Use the Sharpie to mark the excess banding that sticks out past the screw-clamp. Take the clamps off one-at-a-time. Use the Dremel tool to trim off the band at the mark. Use flat file or Dremel tool to round-off and smooth the new edges, then loosely re-install the screw-clamp back onto the handles. Repeat this process on the other three screw-clamp bands. *Wear safety glasses and leather gloves when performing this function to prevent any personal injury.
Step 17: Making the Final Adjustments
Equally space the clamps from the top to the bottom on the sheet metal band. Two should be over the drill handle and two over the battery handle. Install a battery in the new lower handle and set the unit on a flat surface. Have a helper physically push down on the top of the drill body and then tighten all the screw-clamps so the cut handles butt-up tightly inside the wrapped sheet metal.
Step 18: Tightening It All Down
I have big hands and even I cannot get my fingers completely around any cordless tool handle. Individually loosen each band and rotate the screw-clamp heads around the handle and re-tighten to align them in the open space between where the hand palm and fingertips are positioned when gripping the handle.
Step 19: The Finished Product
Insert a battery and test the finished product! Although, the new drill does stand a little taller than the other units, it still serves the purpose. With the screw-clamps tightened securely, the sheet metal wrap makes for a very durable handle If accidentally dropped, the new handle will not break or fall apart. Another advantage to this type of modification is that it can again be disassembled for future drill trigger or motor brush repairs!
Please vote for my entry, if you like it.
(Note: I am so very sorry about the quality of my pictures. I currently cannot
afford a real good camera, so I had to make this Instructable with the only camera I have.)
ONE FINAL THOUGHT: If searching for additional battery handles compatible with your cordless tool group which might be retrofitted this way to orphan tools, consider looking in garage sales, Craigslist or even E-Bay. There are many inexpensive non-operational power tools out there that still have a great battery handle.
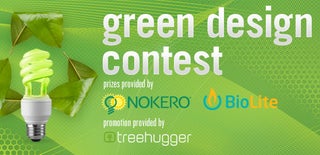
Runner Up in the
Green Design Contest
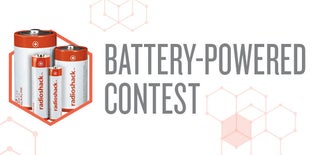
Participated in the
Battery Powered Contest