Introduction: Baransu Self-balancing Scooter
A self-balancing scooter built with 3D printed parts and an Arduino as the micro-controller. Remote control function coming soon!
The self-balancing scooter balances itself using data from a 6-axis IMU and a PID control loop.
NOTE: This is work in progress and the source code is not finalised yet. The files for 3D printing and source code can be downloaded from IXEN Robotics Singapore website at https://ixen-robotics.com.
Step 1: Base Assembly Part 1
Download the 3D printable files from the 3D Print section.
Stick the undercarriage counter-weight to the undercarriage with double-sided tape. This will help to add some weight to the back of the front-heavy scooter and help it balance.
Step 2: Base Assembly Part 2
Press the side details into the side panel.
Step 3: Base Assembly Part 3
Mount the side panel onto the undercarriage by using some M3 10mm flat countersunk cross head screws and M3 locking nuts. Be sure to use a locking nut so that the screw will not come loose due to vibrations.
Step 4: Base Assembly Completed
This is how the base assembly should look like once it is completed.
Step 5: Wheel Assembly Part 1
Attach a motor hub to each of the motor’s shaft. A motor encoder is optional. If you intend to use an encoder, solder a 2.5mm pitch 5-pin female headers to the encoder that is mounted to the motor. If not, solder a 2.5mm pitch 2-pin female headers to the motor.
You will need at least two M3 10mm pan cross head screws to fasten one wheel rim to a motor hub. You will also need at least two M3 5mm pan cross head screws to fasten one wheel rim cover to a wheel rim.
Step 6: Wheel Assembly Part 2
Assemble the wheel assembly as shown in the video.
Step 7: Wheel to Undercarriage Assembly
Assemble the wheel assembly to the carriage as shown in the video. You will need M2.5 10mm pan cross head screws, M2.5 nuts and M2.5 washers.
Step 8: Motor Cover
Assemble the main switch and the motor cover as shown in the video. You will need M3 10mm flat countersunk cross head screws, M3 10mm pan cross head screws and M3 locking nuts.
Step 9: Mainboard Circuit Schematics
Wire up the mainboard as per indicated in the schematic. You may want to use 2.5mm pitch headers when connecting wires in your circuit so that it can easily be connected or disconnected if necessary.
Step 10: PCB Mount
Connect the wires to the mainboard as shown in the video. You may want to refer to the schematics in the previous step. Mount the PCB to the undercarriage using , M3 5mm pan cross head screws.
Step 11: Tail-light
Mount the tail-light to the undercarriage as shown in the video. You will need M2 10mm pan cross head screws.
Step 12: Front Panel Cover & Horn
Mount the piezo speaker to the front panel and cover it with the front panel cover. You will need M2 5mm pan cross head screws and M2 washers in case the screws are too long or you can use a shorter M2 screws.
Step 13: Head Frame & Front Axle
Connect the LED lights as shown in the schematics in the previous step. You may need to cut the LED strips so that it is small enough to fit into the handle bars. Stick the translucent signal filter and the handlebar to the head frame using superglue. Then mount the head frame to the front axle as shown in the video.
Step 14: Mount Front Axle to Front Panel
Then mount the front axle to the front panel as shown in the video. You will need M2 5mm pan cross head screws.
Step 15: Wire Connections & Battery
Connect the wires and battery accordingly. You may want to refer to the schematics in the previous step.
Step 16: Final Assembly
Finally, yes finally!!! Mount the front panel to the undercarriage as shown in the video and you are ready to roll. You will need some M3 5mm flat countersunk cross head screws.
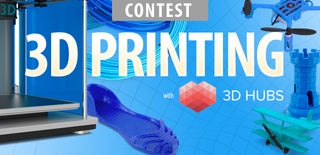
Runner Up in the
3D Printing Contest 2016
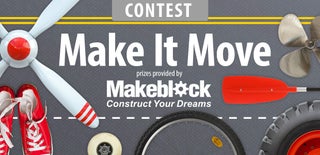
Participated in the
Make it Move Contest 2016
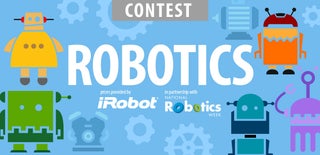
Participated in the
Robotics Contest 2016