Introduction: Barrel Nuts for Your Makerspace
In this instructable, I will be taking the GI-pipe barrel nuts I introduced in this instructable to the next level by explaining how they can be made in bulk in your local makerspace, or in any public workshop around you.
This attempt comes with a number of improvements over the old barrel nuts, namely:
- The nuts now come pre-made with all the features in place. Only installation is required which makes building rigid wooden structures a very rapid process
- The nuts now have a Nylon insert which acts as a thread lock (this is an optional feature which can be omitted to accelerate the build. In my case I thought it would be nice to have)
- The nuts now have two side holes. These two holes are receptive of a 3mm pin which prevents the barrel nut from rotating when embedded in the wooden post (this is also an optional feature which can be omitted to accelerate the build. In my case I thought it would be nice to have)
The content of this instructable has taken a bit of time to prepare. I wish that you will enjoy going through it as much as I enjoyed making it, and that it would inspire you to improve these barrel nuts and/or develop instructables around using them.
My motivation behind this instructable is to help anyone create stable wooden structures really cheaply. It is also my belief that aside from the time invested in making these barrel nuts, the supplies needed to make them are very cheap.
Bellow is a list of the materials, tools, machines, etc., needed both for making and for installing the barrel nuts.
MATERIALS/SUPPLIES:
- A schedule-40, 1/2'' GI pipe
- Countersink M12 bolts (90mm in length or more)
- OPTIONAL: A 3/8 Nylon hose for the thread-locking feature
- OPTIONAL: 3mm stainless steel pins (around 30-60mm in length) for the anti-rotation feature.
MACHINERY/ACCESSORIES:
- One of the following:
- A chop saw
- A metal band saw (preferred)
- A metal bench grinder
- A mill with a digital display, a tapping function, and the following attachments:
- A vertical rotary table/vise
- A rotary chuck that fits on the rotary table/vise, for holding the workpiece
- A drill chuck for holding drill bits
- A spring-collet chuck for holding the power tap
- OPTIONAL: A tumbler, either bought or DIY
TOOLS/HOLDERS/BITS:
- A center drill bit
- A steel-cutting countersink bit
- An M12 power tap
- One of the following (for holding the power tap on the mill):
- An 8-9mm spring collet
- A 1/2'' rigid-tapping collet (preferred)
- A deburring tool.
- A steel-cutting 10-10.5mm drill bit
- A 12mm wood drill bit (for installing)
- A 3mm wood drill bit (for installing)
- A 22mm auger drill bit (for installing)
A WORD OF ADVICE:
Before starting this build, ensure that your local makerspace is okay with you reserving the mill for a number of days for the purpose of fabricating these nuts. Also make sure that all the vises, tools, tool holders, taps and drill bits are available before starting the build in order not to have to reserve the mill for an extended duration of time unnecessarily. In my case, the mill was reserved for nearly a month because we didn't have an 8-9mm spring collet in the shop (we only had 7-8 and 9-10), which was not ideal.
Hence, please be considerate to your local maker community and plan your build ahead of time. Even better, talk to your local makerspace and explain to them the value of these nuts. Make them believe in the cause of your build and try to leverage that to go through it with as little uneasiness as possible. I wish you the best of luck!
Step 1: CUT INTO LENGTH
[THIS STEP IS REQUIRED]
Starting from a schedule-40, 1/2'' GI pipe, choose a reasonable length for your barrel nuts and cut the pipe into equal segments of that chosen length. In our case, we chose a length of 75mm for the barrel nuts.
For cutting, I recommend using a metal band saw as the resulting cut would be cleaner than that on a chop saw with a grinding disc. However, since our band saw was out of service during the time of this build, I had to cut the pipe using the chop saw, grind on a bench grinder, then use a deburring tool for an okay result.
Step 2: SETUP MILL
[THIS STEP IS REQUIRED]
Setting up the mill is by far the most critical and the most demanding step in terms of the mental effort and the concentration required. Namely, this step can be broken down into the following mini steps:
- Assemble the vertical rotary vise for a head support of the barrel nut segments
- Switch on your mill's digital display
- Find the zero point along the X axis
- Find the zero point along the Y axis
- Go to the (0,0) point and lock the bed's movement along the X and the Y axes
- Change the angle of the rotary vise so that the primary chuck is facing upward
- Lock the rotation of the rotary vise
Create the clamp-set arrangement required for a tail support of the barrel nut segments
The images attached to this step try to elaborate more on the details of accomplishing each one of these mini steps, in the same order mentioned above. Please read the notes that appear on these pictures.
Also bear in mind that everything you do from this point on is crucially dependent on the correctness of your mill setup. Any room for vibrations will undermine the quality of your work, furthermore, take the time you need to find the exact zero along the X and the Y axes and make sure to lock the movement of the bed along the X and Y axes otherwise your zero point will shift due to vibrations, leading into inconsistencies and subpar results. Also make sure to use a calculator and to double check the correctness of the center. One of the biggest mistakes I have made during this build is that I computed the center along the Y axis in my head which resulted in an incorrect center (you will notice that in the video, my mental division by two was incorrect). This has lead to an imprefection in all of the barrel nuts that I made in this instructable, which might be unnoticeable but annoyed me. Hence, my advice to you is to take your time and to enjoy setting up the mill as much as you'd enjoy machining.
Step 3: CENTER DRILL
[THIS STEP IS REQUIRED]
This step is not complicated. Just understand the importance of marking, and the importance of using a center drill bit for this step.
A word on marking: In order to be able to carry each machining step with the barrel nut being in the same position, there is a need to mark the head side of the nut vs. the tail side of nut as well as the rotation. Both objectives can be achieved simply by marking the area where the main chuck jaw holds into the workpiece (i.e. the barrel nut), with the workpiece being flushed towards the rotary chuck. This marking needs to survive throughout the entire machining cycle, hence it is highly recommended that you use a permanent marker or a marker that is designed for machining.
In my case, I used a white board marker and I regretted it.
Step 4: DRILL
[THIS STEP IS REQUIRED]
For a better yield and a higher efficiency, I recommend getting the shortest and the highest-quality 10-10.5mm drill bit you could find. When machining 50-100 barrel nuts, good drill bits tend to make a big difference and require less lubrication/cutting oil. Using too much oil makes the job messier and less enjoyable.
NOTE: one of the things that would make a big difference in drilling is whether the center along the Y axis was set correctly. In my case, I rushed the calculation in my head and ended up with an incorrect center along the Y axis. This along with using a cheap drill bit didn't help me accomplish this step nicely.
Step 5: CHAMFER
[THIS STEP IS RECOMMENDED BUT NOT REQUIRED]
Luckily, I used a good quality countersink drilling bit for this step which made it more enjoyable than the previous step.I suggest you do the same and not compromise on cutting tools when machining in bulk.
NOTE: You will see me wearing gloves in this video, it is very dangerous to wear gloves when using machinery in which there is a rotating spindle with a sharp tool mounted in it as the gloves might get caught in the spindle. Please be aware of this and do not use gloves.
Step 6: TAP
[THIS STEP IS REQUIRED]
Power tapping is not a trivial step, and a one that requires attention to detail.
For one, you will need to use a collet chuck rather than a drill chuck to mount the tap, otherwise it will slip or rotate in place as you attempt to thread a hole.
For two, you will need a collet that has a square back end (called a rigid-tapping collet) or a collet that matches closely the shank diameter of the power tapping tool used, otherwise again, the tap would slip or rotate in place.
Good power tapping tools are pricey but they will pay off with the ease of threading and the quality of the threads they produce, I highly recommend getting a high-quality tap.
After the tapping is finished, make sure to check every nut and apply strict quality control. I show this in the second video which is attached to this step.
Step 7: SIDE DRILL
[THIS STEP IS OPTIONAL]
Now that the center drilling, the drilling, the chamfering and the tapping are all done, we are pretty much done with all the machining operations that need to be performed in the (0,0) position. Now it is the time to rotate the vise to a 90 degree angle, move the bed along the X axis by a certain amount and machine the side holes.
A bit about the side holes. These holes are receptive of a steel pin which prevents the nut from rotating spontaneously when embedded inside of a wooden post. It is an optional feature, you do not really have to machine it or to use it in the final assembly, I just thought it would be nice to have and to incorporate into the machining.
Step 8: TUMBLE
[THIS STEP IS OPTIONAL]
Despite the machining going well and the desired functionality being met, there is something about the appearance of GI water pipes that makes you desire better aesthetics. I have looked into this matter extensively, and what I found is that tumbling in a vibratory bucket with construction aggregate (sand and rocks) seems to be the way to go.
For one, it can be done with improvised tools in the makerspace, really cheaply, and without stripping the zinc layer which prevents the nuts from rusting.
For two, it uses cheap media, it is quite fast (2-3 hours), and the resulting nuts look amazing. As for the main-jaw markings, expect them to disappear after this step, but that's okay since they aren't crucially needed anymore (from this point, only drilling of the insert is needed).
To identify the head side of the nut after the marking is gone (as opposed to the tail side), use the pin side holes as a guide (they are towards the tail side of the nuts).
Step 9: INSERT
[THIS STEP IS OPTIONAL]
Inserting a 5/8'' Nylon hose into the nut and drilling it was an idea that I came up with to add a thread locking function to the barrel nuts. It is an interesting idea but not really required, and can hence be skipped if you are trying to finish this build faster.
However, if you like the idea of adding a thread locking feature, then it would be a nice thing to have.
Starting from an uncut length of 5/8'' (16mm) air hose, use a cable cutter to cut the hose into short segments (just enough to cover the threaded hole in the barrel nut. Once inserted, it is time to drill them in the next step.
Step 10: DRILL INSERT
[THIS STEP IS OPTIONAL]
Now that the Nylon inserts are in place, it is the time to create a 10-10.5mm hole which will push against the bolt, providing thread locking functionality.
To drill this hole, we can use a wood drill bit and support the hose on the inside with chalk, which is a weird choice I admit but seemed to work. You have to go really slow as you drill, it is actually more difficult that it sounds.
If you were careful, you will end up with okay holes, which can be beautified further by applying a heat treatment (in the next step).
Step 11: SMOOTH INSERT
[THIS STEP IS OPTIONAL]
Using a hot-air soldering station with a nozzle, it is possible to melt the shredded Nylon around the drilled hole to give it a better finish. In the video above I demonstrate this technique.
Last but not least, I drill the side holes to ensure they are free of any obstructions.
Step 12: CASE STUDY
Before ending this instructable, I'd like to show case what I believe to be a good application of the product of this instructable.
Namely, in this example I take a 4 feet by 8 feet solid-wood door material and I turn it into a working table, only using 4x4 wooden posts and 4 barrel nuts.
This is a demonstration of the idea of repurposing a wooden door into a workbench, using a build technique that takes less than an hour, is very rigid and is very cost effective.
Any comments? Please do not forget to write them below. I am eager to hear your thoughts and feedback.
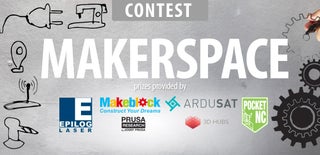
Participated in the
Makerspace Contest